In the realm of sheet metal processing, the press brake machine stands as a crucial apparatus, with its operational precision directly impacting the bending accuracy of workpieces. During the bending process, the concentrated stress on the two ends of the ram often induces concave deformation on the lower surface of the ram. This deformation is most pronounced in the middle portion of the ram, resulting in varying angles along the length of the final bent workpieces.
The Role of Crowning Systems in Press Brake Machine Precision
To counteract the detrimental effects of ram deformation, it becomes imperative to compensate for the deflection deformation of the ram. This is where Crowning Systems come into play.
These systems, such as hydraulic and mechanical Crowning, are designed to induce upward elastic deformation in the middle section of the workbench. This offsetting deformation effectively counterbalances the ram deformation of the bending machine, ensuring machining joint surface precision and enhancing workpiece accuracy.
Currently, many leading foreign press brake manufacturers have embraced mechanical crowning devices. However, domestic manufacturers opt for Crowning methods based on their specific operational contexts and requirements.
Two Types of Press Brake Machine Crowning Systems
Hydraulic Crowning
The hydraulic automatic deflection Crowning mechanism of the workbench is composed of a group of oil cylinders installed in the lower workbench. The position and size of each Crowning oil cylinder are designed according to the deflection ram of the ram and the workbench finite element analysis. The hydraulic Crowning realizes the bulge Crowning of the neutral version through the relative displacement between the front, middle and back three vertical plates. The principle is that the bulge is realized through the elastic deformation of the steel plate itself, so the Crowning amount can be adjusted within the elastic range of the workbench.
Mechanical Crowning
Mechanical Crowning is composed of a group of convex wedge blocks with inclined plane, and each convex wedge block is designed according to the deflection curve of finite element analysis of ram and workbench.
The CNC Controller calculates the required deflection amount according to the load force when the workpiece is bent (this force will cause deflection deformation of the ram and the workbench vertical plate), and automatically controls the relative movement amount of the convex wedge, thus effectively compensating the deflection deformation caused by the ram and the workbench vertical plate.
The ideal mechanical deflection Crowning of the bent workpiece can be achieved by controlling the position to realize "pre-bulging". A set of wedges form a curve consistent with the actual deflection in the length direction of the workbench, so that the gap between the upper and lower dies is consistent during bending.
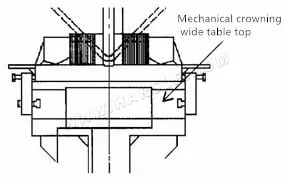
Principle of Hydraulic Crowning
The working principle of hydraulic crowning involves the use of hydraulic actuators to adjust the curvature of the bed or lower beam of the press brake machine. Here's a breakdown of how it operates:
- Hydraulic Actuators: Hydraulic cylinders or pistons are strategically positioned along the length of the bed or lower beam of the press brake machine. These actuators are connected to a hydraulic system that controls their extension and retraction.
- Measurement and Control: Sensors or measurement devices are installed to detect the deflection of the bed or lower beam during operation. These sensors continuously monitor the curvature of the bed.
- Feedback Loop: The measurements obtained from the sensors are fed into a control system. Based on the desired bending parameters and the detected deflection, the control system calculates the necessary adjustments required to achieve the desired bend angle and uniformity across the workpiece.
- Hydraulic Adjustment: The control system sends commands to the hydraulic actuators to extend or retract as needed. By selectively pressurizing or depressurizing the hydraulic cylinders, the curvature of the bed or lower beam is adjusted accordingly.
- Real-time Correction: Throughout the bending process, the control system continuously monitors the curvature of the bed and makes real-time adjustments to maintain the desired bend angle and uniformity.
- Precision Bending: As the hydraulic crowning system dynamically adjusts the curvature of the bed or lower beam, it compensates for any deflection caused by the bending forces. This ensures that the workpiece receives uniform pressure during bending, resulting in precise and consistent bending across its length.
Principle of Mechanical Cowning
The principle of mechanical crowning involves the use of mechanical components to adjust the curvature of the bed or lower beam of the press brake machine. Here's how it typically works:
- Adjustment Mechanism: Mechanical crowning systems consist of a series of adjustable wedges or shims that are strategically positioned along the length of the bed or lower beam of the press brake.
- Manual or Automated Adjustment: Depending on the design, the wedges or shims can be manually adjusted by the operator or controlled automatically through a mechanical or pneumatic system.
- Measurement and Calibration: Before the bending operation, the machine is calibrated to determine the initial curvature of the bed or lower beam. This may involve measuring the flatness of the bed using precision instruments.
- Desired Bend Parameters: Based on the desired bending parameters and the characteristics of the material being processed, the operator or control system determines the adjustments needed to achieve the desired bend angle and uniformity across the workpiece.
- Selective Adjustment: The wedges or shims are adjusted selectively along the length of the bed or lower beam to introduce the required curvature. This adjustment compensates for any anticipated deflection that may occur during the bending process.
- Uniform Pressure Distribution: By adjusting the curvature of the bed or lower beam, mechanical crowning systems ensure that the workpiece receives uniform pressure during bending, resulting in consistent bending across its length.
- Stability and Durability: Mechanical crowning systems are often praised for their stability and durability, as they rely on mechanical components that are less prone to wear and tear compared to hydraulic systems.
Hydraulic Crowning and Mechanical Crwoning: Difference Explained
- Principle of Operation:
- Hydraulic Crowning: Operates by using hydraulic actuators to adjust the curvature of the bed or lower beam of the press brake machine. It relies on a hydraulic system to control the extension and retraction of hydraulic cylinders, compensating for deflection during the bending process.
- Mechanical Crowning: Operates using mechanical components such as adjustable wedges or shims positioned along the length of the bed or lower beam. These components are manually or automatically adjusted to introduce the required curvature, compensating for deflection during bending.
- Adjustment Precision:
- Hydraulic Crowning: Offers high precision adjustments due to the fine control provided by hydraulic systems. This enables precise and real-time adjustments to compensate for deflection, resulting in accurate bending.
- Mechanical Crowning: Provides precise adjustments but may have limitations in fine-tuning compared to hydraulic systems. However, it still offers sufficient precision for many bending applications.
- Complexity and Maintenance:
- Hydraulic Crowning: Generally more complex due to the hydraulic system components such as pumps, valves, and cylinders. Regular maintenance of hydraulic components is required to ensure proper functioning.
- Mechanical Crowning: Typically simpler in design and requires less maintenance compared to hydraulic systems. Mechanical components such as wedges or shims are durable and less prone to wear and tear.
- Cost:
- Hydraulic Crowning: Typically more expensive due to the complexity of hydraulic systems and associated components.
- Mechanical Crowning: Generally more cost-effective compared to hydraulic systems, as it involves simpler mechanical components.
- Response Time:
- Hydraulic Crowning: Offers fast response times as adjustments are made through hydraulic actuators, enabling real-time compensation for deflection.
- Mechanical Crowning: Response time may be slightly slower compared to hydraulic systems, especially if adjustments are made manually.
- Flexibility:
- Hydraulic Crowning: Provides greater flexibility in adjustment capabilities due to the fine control offered by hydraulic systems.
- Mechanical Crowning: While still offering flexibility, adjustments may be limited compared to hydraulic systems, particularly in fine-tuning.
Conclusion
Ultimately, the choice between hydraulic crowning and mechanical crowning depends on factors such as precision requirements, budget constraints, maintenance considerations, and the specific needs of the application.