Interested in mastering press brake operation? Look no further! This article offers invaluable insights into the intricate workings of press brake operation, catering to both novices and seasoned operators alike.
Press brakes stand as linchpins in metal fabrication and bending endeavors. Mastery of their operation is paramount for achieving precision and accuracy. Here, we dissect the essential components of a press brake, elucidating their roles. From the control panel to the hydraulic system, you'll gain a thorough grasp of how each facet contributes to the machine's overall functionality. Whether you're a veteran in the field or just starting out, this article arms you with the knowledge essential for success in press brake operation.
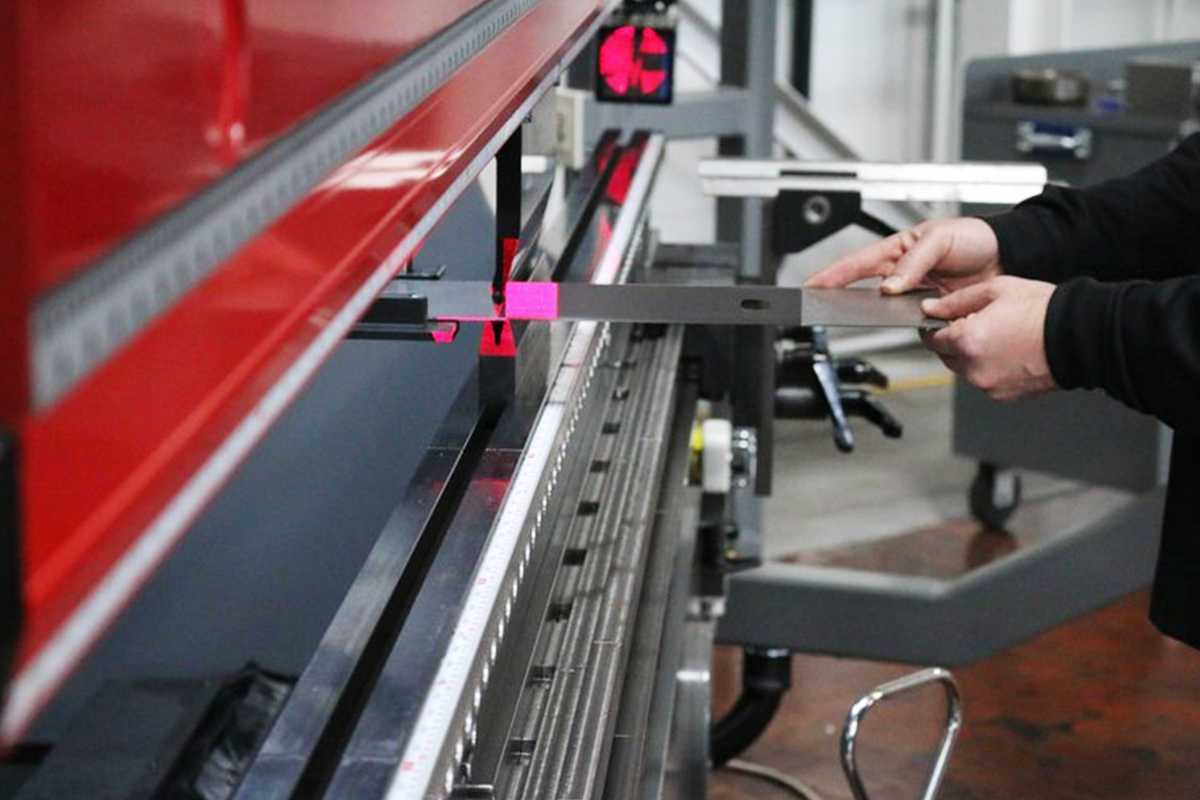
What Is A Press Brake?
A press brake is a vital machine used in metal fabrication processes to bend and shape sheet metal. It is a versatile tool that allows for precise and accurate bending of various materials, such as steel, aluminum, and stainless steel.
The press brake consists of several key components, including the frame, the ram, the bed, and the back gauge. The frame provides stability and support for the machine, while the ram is responsible for applying the force needed to bend the metal. The bed acts as a surface on which the material is placed, and the back gauge ensures consistent and accurate positioning of the metal.
Press brakes come in different types, such as mechanical, hydraulic, and servo-electric. Each type has its own advantages and is suitable for different applications. Mechanical press brakes use a flywheel and a clutch to generate force, hydraulic press brakes rely on hydraulic cylinders, and servo-electric press brakes use a combination of electric motors and ball screws.
The operation of a press brake involves a series of steps. First, the operator sets the material on the bed and positions it using the back gauge. Then, the operator selects the appropriate tooling, such as punches and dies, based on the desired bend radius and angle. Next, the operator adjusts the machine settings, including the tonnage and the bend length. Finally, the operator activates the machine, and the ram descends to bend the material to the desired angle.
Understanding the function and operation of a press brake is crucial for achieving precise and accurate bends in metal fabrication. By mastering the key components and steps involved, operators can produce high-quality products efficiently and effectively.
Different Types Of Press Brakes
When it comes to press brake operation, it’s important to understand that there are different types of press brakes available in the market. Each type offers unique features and advantages to suit specific manufacturing needs. Here are some common types of press brakes:
- Mechanical Press Brakes: These press brakes use a mechanical flywheel to generate power and apply force to bend the material. They are known for their high-speed operation and are suitable for small to medium-sized jobs. Mechanical press brakes are often preferred for their cost-effectiveness and durability.
- Hydraulic Press Brakes: Hydraulic press brakes use hydraulic cylinders to apply force and bend the material. They offer excellent control over the bending process, allowing for precise and accurate results. Hydraulic press brakes are ideal for heavy-duty applications and can handle a wide range of materials and thicknesses.
- Servo-Electric Press Brakes: Servo-electric press brakes use electric motors and ball screws to control the bending process. They offer superior precision and control, making them ideal for complex bending operations. Servo-electric press brakes are known for their energy efficiency, quiet operation, and low maintenance requirements.
- Pneumatic Press Brakes: Pneumatic press brakes use compressed air to apply force and bend the material. They are compact and lightweight, making them suitable for small-scale operations and mobile applications. Pneumatic press brakes are often used for bending thin and delicate materials.
Each type of press brake has its own advantages and considerations, so it’s important to choose the right one based on your specific requirements. Whether you need speed, precision, versatility, or portability, there is a press brake that can meet your needs.
Understanding The Basic Components Of A Press Brake
When it comes to operating a press brake, it is crucial to have a clear understanding of its basic components. These components work together to ensure accurate and precise bending operations. Let’s take a closer look at each one:
- Frame: The frame is the foundation of the press brake and provides support and stability during operation. It is typically made of welded steel plates to withstand the high force and pressure exerted during bending.
- Ram: The ram is the moving part of the press brake that applies force to the workpiece to bend it. It is connected to the hydraulic or mechanical system and moves up and down to perform the bending operation.
- Bed: The bed is the flat surface on which the workpiece rests during bending. It provides support to prevent any deformation or movement of the workpiece during the bending process.
- Die: The die is a specialized tool that determines the shape and angle of the bend. It is mounted on the bed and works in conjunction with the punch to form the desired bend in the workpiece.
- Punch: The punch is another specialized tool that applies force to the workpiece in conjunction with the die. It is mounted on the ram and creates the desired bend by pressing against the workpiece.
- Backgauge: The backgauge is a device that positions the workpiece accurately for each bend. It ensures consistent and precise bending by controlling the depth and location of the bend.
Understanding these basic components of a press brake is essential for efficient and accurate bending operations. By familiarizing yourself with their functions and how they work together, you can optimize your workflow and achieve high-quality results.
Safety Measures For Press Brake Operation
When it comes to operating a press brake, safety should always be a top priority. Here are some important safety measures to keep in mind:
- Proper Training: Before operating a press brake, it is crucial to receive proper training. This includes understanding the machine’s controls, safety features, and operational procedures. Training should also cover the use of personal protective equipment (PPE), such as safety glasses, gloves, and hearing protection.
- Machine Maintenance: Regular maintenance of the press brake is essential to ensure safe operation. This includes inspecting and replacing worn-out parts, lubricating moving components, and keeping the machine clean. By maintaining the machine in good working condition, you can reduce the risk of accidents and improve overall productivity.
- Safe Work Environment: Creating a safe work environment is crucial for press brake operation. This includes keeping the area around the machine clean and free of clutter, ensuring proper lighting, and marking off hazardous areas. Additionally, it is important to have clear safety protocols in place, such as emergency stop procedures and lockout/tagout practices.
- Safe Handling of Materials: When working with materials on the press brake, it is important to follow safe handling practices. This includes using proper lifting techniques, wearing appropriate PPE, and securing materials properly. Avoid overloading the machine and ensure that the materials are positioned correctly on the bed and aligned with the backgauge.
- Awareness and Focus: Maintaining awareness and focus during press brake operation is crucial for safety. Avoid distractions and stay focused on the task at hand. Be aware of your surroundings and the movements of the machine, and be prepared to react quickly if something goes wrong.
By following these safety measures, you can minimize the risk of accidents and ensure a safe working environment for press brake operation. Remember, safety should always come first.
Operating The Press Brake
Operating a press brake requires a combination of technical skill, precision, and attention to detail. In this section, I will guide you through the steps involved in operating a press brake effectively.
Step 1: Safety First
Before operating the press brake, it is crucial to prioritize safety. Ensure that you have received proper training on press brake operation and are familiar with the machine’s safety features. Always wear appropriate personal protective equipment (PPE) such as safety glasses and gloves. Keep the work area clean and organized to prevent accidents.
Step 2: Machine Inspection
Before starting any work, inspect the press brake to ensure it is in good working condition. Check for any loose or damaged parts, and verify that all safety guards are in place. It’s also important to ensure the machine is properly lubricated for smooth operation.
Step 3: Selecting Tooling
Choose the appropriate tooling for the specific bending task. Consider factors such as material type, thickness, and desired bend angle. Proper tooling selection is crucial for achieving accurate and precise results.
Step 4: Adjusting the Backgauge
The backgauge is a key component of the press brake that helps position the workpiece accurately. Adjust the backgauge according to the desired bend length, ensuring it is securely locked in place. Take measurements and make any necessary adjustments to achieve the desired results.
Step 5: Setting Bending Parameters
Set the bending parameters on the press brake control panel. This includes selecting the bend angle, bend length, and tonnage required for the specific material and thickness. Refer to the machine’s manual or consult with an expert if you are unsure about the appropriate settings.
Step 6: Securing the Workpiece
Position the workpiece securely on the bed of the press brake, ensuring it is aligned with the backgauge. Use clamps or other appropriate methods to secure the workpiece in place. This will prevent any movement during the bending process and ensure accurate results.
Remember, operating a press brake requires practice and experience. Always maintain focus and concentration while working to minimize the risk of accidents. By following these steps, you can operate a press brake safely and efficiently, achieving precise bends with ease.
Common Issues In Press Brake Operation And How To Troubleshoot Them
When operating a press brake, it’s important to be aware of common issues that may arise and know how to troubleshoot them effectively. Here are some of the most common issues and their solutions:
- Uneven Bending: If you notice that your bends are not uniform or have inconsistencies, it could be due to several factors. One possible cause is an improperly adjusted or worn-out die. In this case, you should check and adjust the die to ensure proper alignment. Another possible cause is uneven material thickness, which can be resolved by using shims or adjusting the material position. Finally, make sure that the punch and die are clean and free from debris, as this can also affect the quality of the bend.
- Material Slippage: Material slippage can occur when the material moves or shifts during the bending process, resulting in inaccurate bends. To troubleshoot this issue, start by checking the condition of the backgauge fingers. They should be clean, properly adjusted, and securely holding the material in place. Additionally, make sure that the clamping system is functioning correctly and that there is enough pressure applied to prevent slippage. If the issue persists, consider using anti-slip coatings or tapes on the backgauge fingers for better grip.
- Springback: Springback refers to the tendency of the material to return to its original shape after bending, leading to a bend angle that is less than desired. To minimize springback, you can make adjustments such as increasing the bending angle, using a smaller bend radius, or using a higher tonnage. Additionally, pre-bending the material or using a bottoming tool can help reduce springback. It’s important to note that the level of springback can vary depending on the material type and thickness, so experimentation and experience are key in finding the optimal solution.
- Tooling Wear: Over time, the punch and die may wear out, resulting in poor quality bends and inconsistencies. Regularly inspect the tooling for signs of wear, such as chipping or rounding of the edges. If any issues are detected, it’s important to replace or regrind the tools promptly to maintain accurate bending results.
By being aware of these common issues and knowing how to troubleshoot them effectively, operators can ensure smooth and precise press brake operation. Remember to always prioritize safety and consult the machine’s manual or seek professional assistance
Conclusion
Press brake operation is a critical skill that requires a deep understanding of the machine’s components and safety measures. This article has provided valuable insights for both beginners and experienced operators, highlighting the importance of knowing the key components of a press brake and their functions in achieving accurate results. It has also emphasized the significance of safety measures, such as proper training, machine maintenance, and creating a safe work environment.
By following the step-by-step guide on setting up and preparing the press brake, operators can ensure a smooth and efficient bending process. However, it is important to note that practice and experience play a crucial role in mastering press brake operation. Maintaining focus and concentration are essential for achieving precise bends with ease.
Remember, safety should always be the top priority when operating a press brake. By adhering to the safety measures outlined in this article, operators can minimize the risk of accidents and create a safe working environment.
Press brake operation requires a combination of knowledge, skill, and safety consciousness. With the right techniques and precautions, operators can achieve accurate and precise results while ensuring their own well-being and the safety of those around them.