Looking to become a press brake operator? You've come to the right place! In this article, we'll give you a detailed breakdown of the press brake operator job description. Whether you're just starting out or already have some experience, knowing the key responsibilities and qualifications for this role is essential for your career growth. Let's take a closer look at what it takes to succeed as a press brake operator.
What is a Press Brake Operator?
A press brake operator is a highly skilled technician who operates machines designed to bend, punch, and shape metal sheets and plates, primarily in the manufacturing sector. This role demands a blend of technical knowledge, mathematical skills, and mechanical aptitude.
Responsibilities of a Press Brake Operator
A press brake operator’s duties include setting up and running press brake machinery based on specific job instructions and blueprints. They meticulously measure and align metal sheets and plates to ensure accurate bends and angles. Additionally, they utilize various tools to punch holes, cut shapes, and produce intricate forms.
Quality Control and Safety
An essential part of the press brake operator's job is to inspect the finished products for quality and precision. They must pay close attention to detail, spotting any flaws or deviations from specifications. When necessary, they adjust the machinery to resolve issues and ensure the final product meets the required standards.
Skills and Qualifications
To excel as a press brake operator, strong mathematical and mechanical abilities are crucial. Operators must accurately read and interpret blueprints, perform calculations, and take precise measurements. A thorough understanding of safety protocols is also vital to minimize the risk of accidents and injuries.
Career Outlook
A career as a press brake operator offers great potential in the manufacturing industry. With continued growth in demand for metal products, the need for skilled operators remains high. Press brake operators can further their careers by pursuing advanced training and taking on more complex roles within the industry.
In summary, a press brake operator is a skilled professional in the metal fabrication process. Their attention to detail, technical skills, and focus on quality make them a valuable asset to the manufacturing industry.
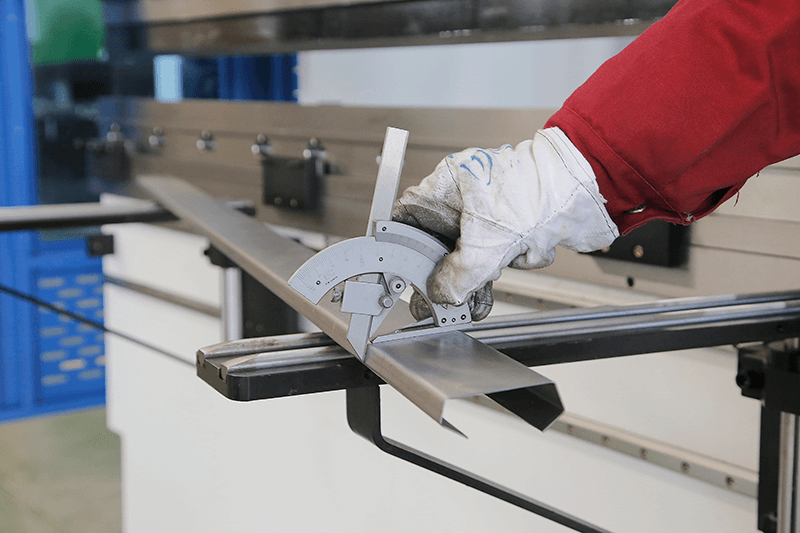
Responsibilities of a Press Brake Operator
A press brake operator plays a crucial role in the metal fabrication process, with key responsibilities that include:
Machine Setup and Operation:
Setting up the press brake machine according to specific job instructions, blueprints, and technical specifications. This involves configuring the machine’s tools, dies, and other components for precise bending operations.
Material Preparation:
Measuring, cutting, and aligning metal sheets or plates to ensure they meet the required dimensions and angles for the job. This includes verifying material thickness and type to match the machine settings.
Bending and Shaping:
Operating the press brake to bend, punch, or shape metal into desired forms, ensuring each part conforms to specifications. This requires adjusting the machine for different bends and angles based on the design.
Quality Control:
Inspecting the finished parts to ensure accuracy and quality, checking for defects or deviations from the blueprint. If necessary, adjusting the machine or reworking parts to correct errors.
Tool Maintenance:
Performing regular checks on the press brake’s tools, dies, and components to ensure they are in proper working condition. This also includes cleaning and maintaining the machine to avoid breakdowns.
Safety Compliance:
Adhering to safety standards and protocols, including the use of protective equipment, to prevent accidents and injuries. Operators must be vigilant about keeping the work area organized and hazard-free.
Troubleshooting:
Identifying and resolving technical issues that may arise during operation. This involves diagnosing mechanical or material problems and making adjustments to ensure smooth production.
Collaboration:
Working closely with engineers, supervisors, and other team members to meet production goals, adjust plans when needed, and ensure timely delivery of finished products.
Skills and Qualifications Required for a Press Brake Operator
As a press brake operator, there are several skills and qualifications that are essential for success in this role. Here are some key requirements:
- Mechanical aptitude: A press brake operator must have a strong understanding of mechanical systems and be able to troubleshoot and perform routine maintenance on the machinery. This includes knowledge of hydraulic and pneumatic systems.
- Mathematical skills: Precision is crucial in operating a press brake. Operators need to be able to read and interpret blueprints and engineering drawings, make accurate measurements, and calculate bending angles and dimensions.
- Attention to detail: Press brakes require precise positioning and alignment to produce high-quality products. Operators must pay close attention to detail to ensure that the bending, punching, and shaping processes are executed accurately.
- Physical stamina: Operating a press brake involves standing for long periods and often requires lifting and moving heavy metal sheets and plates. Physical stamina and strength are necessary to perform these tasks safely and efficiently.
- Problem-solving abilities: Press brake operators encounter various challenges during their work, such as equipment malfunctions or material defects. They must be able to identify problems, troubleshoot, and make adjustments to ensure the quality and efficiency of the production process.
- Safety consciousness: Working with heavy machinery can be hazardous. Press brake operators must follow safety protocols and guidelines to prevent accidents and injuries. They should have a strong understanding of workplace safety practices and be committed to maintaining a safe working environment.
- Communication skills: Press brake operators often work as part of a team and need to effectively communicate with coworkers, supervisors, and other departments. Clear and concise communication is essential for coordinating tasks and ensuring smooth operations.
By possessing these skills and qualifications, a press brake operator can excel in th
Safety Guidelines for Operating a Press Brake
When operating a press brake, safety should always come first. Here are some essential guidelines to ensure a safe work environment:
- Wear Appropriate Personal Protective Equipment (PPE): Always wear proper PPE, such as safety glasses, gloves, and steel-toed boots, to protect yourself from hazards like flying debris and accidental contact with the machine.
- Inspect the Machine and Tools: Before starting any task, thoroughly inspect the press brake and its tools for signs of damage or wear. Check components such as the hydraulic system, electrical connections, and tooling. If any issues are found, report them immediately and avoid using the machine until repairs are made.
- Follow Lockout/Tagout Procedures: When performing maintenance or repairs, always follow lockout/tagout protocols to prevent accidental machine startup. This involves disconnecting the power source, locking out the power switch, and tagging the machine to indicate it's undergoing maintenance.
- Use Proper Lifting Techniques: To avoid injuries when lifting heavy materials or tools, bend your knees, keep your back straight, and lift with your legs. If the load is too heavy, seek help or use equipment like cranes or forklifts.
- Maintain a Clean and Organized Work Area: A clutter-free workspace reduces accidents. Clear away scraps, tools, and other obstructions around the press brake. Ensure the floor is free from oil or slippery substances to prevent falls.
By adhering to these safety measures, press brake operators can significantly reduce the risk of accidents. Remember, safety is a shared responsibility, and taking the proper precautions is key to maintaining a secure and efficient workplace.
Common Challenges and Troubleshooting Tips for Press Brake Operators
Operating a press brake machine can come with various challenges. Below are some common issues operators may face, along with troubleshooting tips to resolve them:
- Uneven Bending: If the bends in your metal sheets are inconsistent, it may be due to several factors. Worn or misaligned tooling is often the culprit—check and adjust the tooling as needed. Another potential cause could be incorrect material thickness settings or insufficient clamping force. Double-check these settings and make adjustments to ensure accurate bends.
- Material Slippage: Material slipping during the bending process can result in inaccurate bends. To prevent this, ensure the material is correctly positioned and securely clamped before starting the bend. Additionally, using anti-slip materials or adhesive tapes can provide extra grip and stability during operation.
- Cracked or Deformed Parts: Cracks or deformations in finished parts often indicate excessive stress or improper bending techniques. To avoid this, make sure the material is adequately supported and that the bending force is evenly applied. Using the right tooling and following proper bending procedures can prevent these issues.
- Tooling Wear: Over time, press brake tooling can wear out, affecting bend quality. Regularly inspect your tooling for signs of wear and replace it when necessary. Proper maintenance, including lubrication, will also help extend the life of your tools.
Troubleshooting these common challenges requires experience, knowledge, and attention to detail. By addressing these issues with the tips provided, press brake operators can enhance the efficiency and accuracy of their operations.
Case: 90° Bending of Stainless Steel Sheet
Workpiece Parameters
- Material: 304 stainless steel
- Thickness: 4mm
- Bending angle: 90°
- Bending length: 1000mm
Operation Key Points
Die Selection
- Choose a V-shaped die with a V-opening width of 8 times the sheet thickness, which is 32mm. This ensures bending quality while avoiding excessive impact force.
- The die length should be the bending length + 3 times the sheet thickness, which is 1012mm, to prevent edge deformation.
Bending Force Calculation
- The tensile strength of 304 stainless steel is 600MPa, and the bending width is 1000mm. The bending force F = 0.4 × tensile strength × thickness^2 × bending width ÷ V-opening width
- Substituting the data, F = 0.4 × 600 × 4^2 × 1000 ÷ 32 = 300kN
- Choose a press brake with a capacity above 350kN to have some margin
Bending Compensation
- The springback rate of 304 stainless steel is about 15%, so it is necessary to overbend by 15%, which is 103.5°
- Set the bending angle to 103.5° on the press brake to compensate for spring back
Bending Speed Control
- 304 stainless steel is a difficult-to-process material, and the bending speed should not be too fast, generally controlled at 5-8mm/s
- Excessive bending speed will aggravate die wear and affect bending accuracy
Die Lubrication
- Stainless steel tends to stick to the die, affecting the bending quality, so a layer of lubricating oil needs to be applied to the die surface.
- Choose low-viscosity mineral oil or synthetic oil, and avoid using vegetable oil because it is prone to oxidative deterioration
Post-Bending Treatment
- After bending stainless steel, the bending area will undergo some hardening, and the toughness will decrease.
- If there are high plasticity requirements for the bending area, annealing treatment can be performed to restore the material's ductility.
By following the above operation key points, the 90° bending quality of a 4mm thick 304 stainless steel sheet can be ensured. Of course, in actual operation, it is also necessary to make fine adjustments according to equipment conditions and production requirements, which requires the operator to control flexibly based on experience.
How to Become A Press Brake Operator
Firstly, if you want to be an excellent press brake operator, you need to have some basic knowledge such as mathematics, machinery, computers, and other related areas. You should also understand different metal materials and their characteristics, and learn how to read and understand CAD drawings.
It's also important to understand the structure and working principle of the press brake. Once you have acquired this knowledge, the company will train the operators on the operation of the machine.
Press brake operators must also learn how to make complex workpieces through machine programming. In short, it's important to constantly learn new technologies and take additional training courses to improve your competitiveness in the industry.
Career Path
Preliminary Operator: familiar with the basic operation of press brake and can independently accomplish the simple workpiece bending. Know the common material bending properties and master the basic tooling selection principle. Able to measure the size and quality identify according to the drawing.
Intermediate Operator: able to handle some complex bending workpieces, such as multiple bending and special-shaped bending; master bending process setting and optimization, improving production efficiency and quality; master some troubleshooting, diagnosis, and maintenance ability, which can handle common machine problems.
Senior Operator: proficient in the bending process of various materials and able to handle difficult bending tasks. Has design and innovation capabilities for bending processes and continuously optimizes the production process. Able to guide and train junior and intermediate operators to improve the team's overall skill level.
Bending engineer: engage in R&D and research on bending processes and solve key technical problems. Optimize the layout and process of the bending production line to improve production efficiency and flexibility. Participate in the process design and trial production of new products to shorten the product development cycle.
Production management personnel: responsible for the daily management of the bending workshop and reasonable allocation of personnel and equipment resources. Develop production plans and quality goals, and supervise and evaluate the process. Promote the standardization and leanness of bending processes and continuously improve production performance.
Future of Press Brake Operators
If press brake operators want to develop in the industry for a long time, they need to keep up-to-date with the latest industry developments at all times.
This way, they can improve their understanding of the industry, enhance their technology skills, and increase their industry knowledge. Automation is increasingly being used in the sheet metal industry.
Enterprises will purchase automated equipment to improve production efficiency. Press brake operators should be able to use automation systems, including machine programming and other functions.
Press brake operators should have enough skilled experience and obtain certification from authoritative institutions. This will give them more competitive advantages in the job hunting process.
New requirements for automation and intelligence
With industrial 4.0 and development for intelligence, press brake automation and intelligence degrees have been improved. This arouses new requirements for press brake operators:
Digital ability: Familiar with digitally designed software like CAD/CAM, able to perform digital modeling and simulation of bending processes. Understand digital manufacturing systems, such as MES, ERP, etc., and be able to collect and analyze production data.
Automation control ability: master the press brake automation line operation and programming, know the PLC, sensor, which can handle simple production data collection and analysis.
Intelligent optimization capabilities: use big data and artificial intelligence technology to optimize bending process parameters intelligently. Develop an intelligent bending process APP to realize the sharing and promotion of process knowledge.
Flexible production capabilities: Adapt to the flexible production needs of multiple varieties, small batches, and short delivery times and quickly complete process switching. Collaborate with product design, process planning, and other departments to achieve product life cycle management.