Introduction
In the world of sheet metal fabrication, two terms often cause confusion: Press Brake vs Brake Press. Understanding the difference between Press Brake and Brake Press is vital for anyone involved in this industry. This article aims to clarify these terms and shed light on their significance in sheet metal fabrication. Additionally, we'll touch upon the importance and trends shaping this sector.
Unlocking the Diffrences: Press Brake vs Brake Press
Let's start by defining these terms. A Press Brake is a machine used to bend sheet metal into various shapes, commonly used in industries like automotive and construction. On the other hand, a Brake Press is primarily designed for shearing or bending metal sheets, offering versatility in cutting and shaping tasks.
Comparing Working Principles and Operational Modes
Expanding on the key difference in working principles between Press Brake and Brake Press machines, it's essential to delve deeper into how these principles shape their respective functionalities and operational capabilities.
A Press Brake, as mentioned, utilizes a downward force to bend metal against a die. This method enables precise bending of sheet metal into various shapes and angles. The die, which acts as a mold, helps ensure consistent and accurate bends across the metal surface. Press Brakes are particularly suitable for applications that demand high precision and repeatability, such as forming complex geometries or achieving tight tolerances.
On the other hand, a Brake Press employs a top-down approach for cutting or bending metal. While it can also be used for bending, Brake Presses are more commonly associated with shearing tasks, where they excel in swiftly and cleanly cutting through metal sheets. The top-down motion allows for efficient shearing, making Brake Presses ideal for high-volume production environments where speed and simplicity are paramount.
In terms of operation, Press Brakes often feature advanced control systems and automation technologies. These systems enable operators to precisely control parameters such as bending angle, force, and speed, leading to consistent and high-quality results. Automation further enhances productivity by reducing setup times and minimizing human error.
Conversely, Brake Presses are favored for their simplicity and ease of use, particularly in shearing tasks. Their straightforward operation and intuitive controls make them accessible to operators of varying skill levels. While they may lack the advanced features of Press Brakes, Brake Presses offer reliability and efficiency in repetitive cutting operations.
Overall, the choice between a Press Brake and a Brake Press depends on the specific requirements of the application. Press Brakes excel in precision bending tasks, offering versatility and control, while Brake Presses are preferred for their efficiency and simplicity in shearing operations. By understanding the nuances of their working principles and operational capabilities, manufacturers can make informed decisions to optimize their sheet metal fabrication processes.
Contrasting Structural and Design Features
Press Brakes are engineered with sturdy frames specifically optimized for bending applications. These frames are designed to withstand the significant forces exerted during the bending process, ensuring stability and accuracy. Reinforced components and heavy-duty construction contribute to the overall durability of Press Brakes, making them well-suited for demanding bending tasks across various metal thicknesses.
In contrast, Brake Presses prioritize robustness to accommodate the forces involved in shearing tasks. The frames of Brake Presses are engineered to withstand the pressures exerted during cutting operations, providing stability and precision. While they may not be as heavy-duty as Press Brake frames, Brake Press frames are still designed to endure the repetitive stresses encountered in high-volume shearing environments.
Design-wise, Press Brakes often incorporate sophisticated hydraulic systems to facilitate precise control over bending angles and forces. These hydraulic systems allow operators to adjust parameters such as pressure and speed with accuracy, ensuring consistent bending results across different materials and thicknesses. Additionally, advanced features such as CNC (Computer Numerical Control) integration enable automated bending sequences, further enhancing efficiency and repeatability.
On the other hand, Brake Presses focus on efficient shearing mechanisms to optimize cutting performance. The design of Brake Presses emphasizes simplicity and reliability, with emphasis placed on the blade geometry and cutting mechanism. This streamlined approach ensures smooth and precise shearing motions, enabling Brake Presses to deliver clean cuts with minimal deformation or burring.
Comparing Application Fields and Processing Capacities
Press Brakes are ideal for industries requiring precise bending of complex shapes, such as aerospace and electronics. They offer high accuracy and flexibility in handling various metal thicknesses. On the other hand, Brake Presses excel in high-volume shearing tasks, delivering clean and straight cuts efficiently, making them indispensable in sectors like metal fabrication and manufacturing.
Offering Usage Recommendations and Market Insights
When choosing between Press Brakes and Brake Presses, consider the specific needs of your project. If precision bending is paramount, opt for a Press Brake with advanced control features. For heavy-duty shearing tasks, a Brake Press would be the preferred choice. As the sheet metal fabrication industry evolves, we anticipate advancements in technology driving efficiency and versatility in both equipment categories.
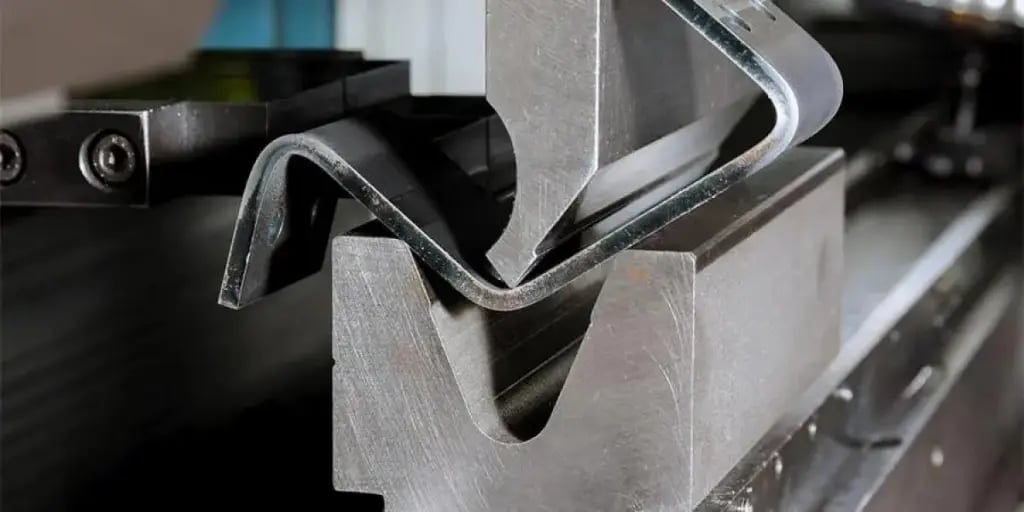
Conclusion:
In conclusion, understanding the distinction between Press Brake and Brake Press is crucial for optimizing sheet metal fabrication processes. Each machine has its unique strengths and applications, and selecting the right equipment is essential for achieving desired outcomes efficiently. By staying informed about industry trends and technological advancements, manufacturers can stay ahead and meet the evolving demands of sheet metal fabrication with confidence.