À medida que as indústrias modernas avançam, a prevalência de máquinas de dobrar na produção industrial se tornou comum. No entanto, com o aumento da demanda, o mercado testemunhou o surgimento de máquinas de dobra de qualidades variadas. A qualidade dessas máquinas desempenha um papel crucial na determinação da suavidade ou frustração de futuros processos de produção. Então, como selecionar adequadamente uma máquina de dobra de alta qualidade? A melhor abordagem é considerar cuidadosamente o uso final da máquina, as variáveis de deflexão potenciais e o raio de curvatura da peça. Os tomadores de decisão também devem se aprofundar em detalhes sobre o desempenho da máquina, faixa de processamento, precisão e outros recursos.
Guia de seleção de máquina de dobra
Peça de trabalho - Tipo de especificação
A primeira consideração crucial é o tipo de peças pretendidas para produção. Uma estimativa abrangente do tamanho padrão, formato estrutural e outros fatores das peças deve ser feita. O objetivo é comprar uma máquina que possa concluir eficientemente tarefas de processamento com a menor mesa e menor tonelagem, alcançando propósitos práticos e econômicos.
Material - Força de flexão
O material da placa de processamento é um fator-chave que influencia a força de flexão. O aço inoxidável, por exemplo, normalmente requer cerca de 50% a mais de carga em comparação ao aço macio, enquanto a maioria dos materiais precisa de aproximadamente 50% a menos de carga do que o alumínio macio. Parâmetros de pressão de flexão relevantes podem ser obtidos do fabricante.
Raio de curvatura - Especificações de tonelagem
O raio de curvatura do canto da peça de trabalho é um fator crítico durante o processo de curvatura. Para curvatura livre, o raio de curvatura é 0,156 vezes o tamanho da abertura da ranhura em V. A seleção da especificação de tonelagem mais baixa é melhor alcançada planejando um raio de curvatura maior do que a espessura da chapa, usando curvatura livre sempre que possível.
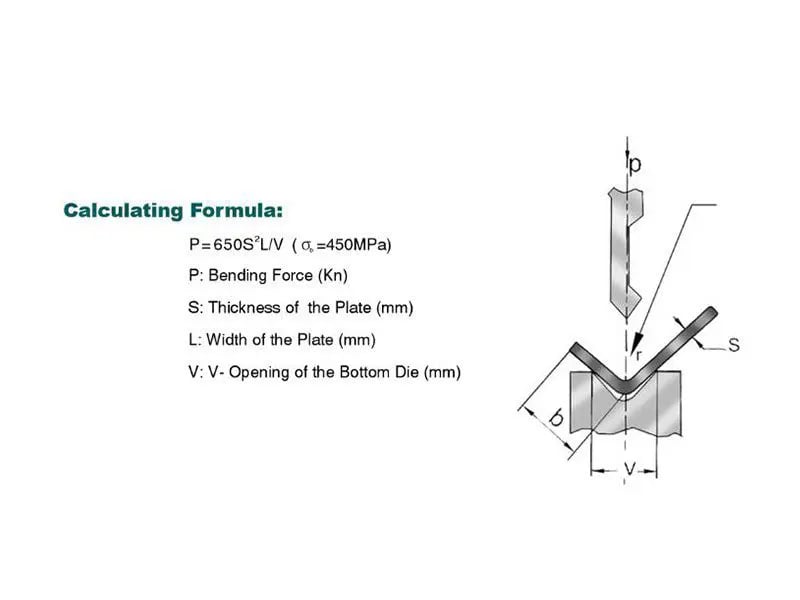
Precisão - CNC Inteligente
A precisão da dobra é um fator que precisa de consideração cuidadosa, determinando se deve investir em uma máquina de dobra CNC ou em uma convencional. As máquinas de dobra CNC oferecem alta precisão, com repetibilidade do cursor garantida em ± 0,01 mm, tornando-as adequadas para aplicações que exigem precisão de ± 0,5°.
Ferramenta - Desgaste
Matrizes de dobra impactam diretamente na precisão da dobra. Medições frequentes de desgaste, avaliando o comprimento da frente da matriz superior até o ombro da mesa e o comprimento entre a matriz inferior e o ombro da mesa, são necessárias. Matrizes de retificação fina são recomendadas para Máquinas de dobrar CNC, enquanto matrizes convencionais podem ser suficientes para máquinas de dobra comuns.
Deflexão - Sistema de coroamento
Isso significa que máquinas mais curtas exigem menos ajustes de calço para produzir peças de qualidade, e menos ajustes de calço reduzem o tempo de entrega. No entanto, a maioria das máquinas de dobra hidráulica CNC atuais foi projetada para produção com a adição de uma função de compensação de deflexão hidráulica, reduzindo a necessidade de os operadores de produção ajustarem a máquina enquanto melhoram a precisão e a produtividade da dobra. A função de compensação de deflexão hidráulica é controlada pelo sistema CNC, óleo hidráulico através da válvula de serviço magnética no cilindro de compensação, para levar a mesa para cima, enquanto a força de compensação de deflexão aumenta com o aumento da força de dobra, desempenhando assim um papel na compensação de deflexão.
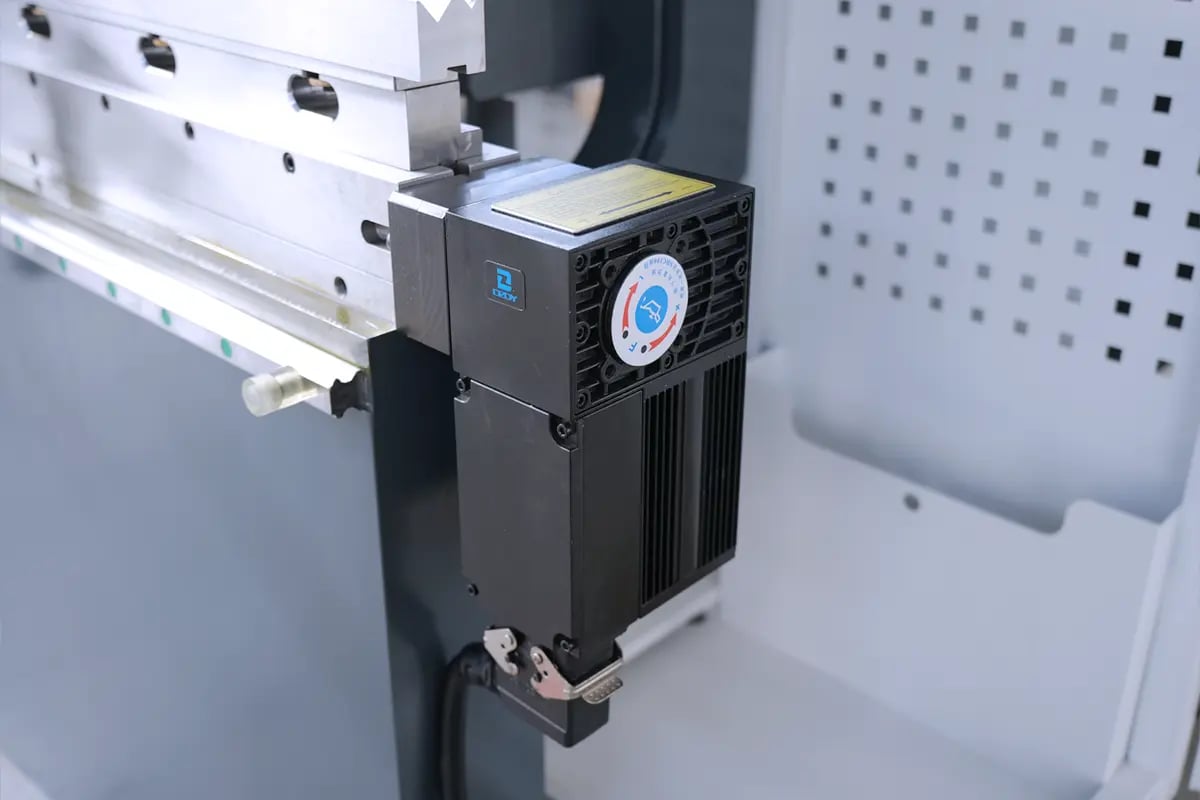
Resumo
Concluindo, ao comprar uma máquina de dobrar, os usuários ou fabricantes devem se concentrar em adquirir uma máquina economicamente prática. É essencial considerar múltiplos fatores simultaneamente com base na situação real. Os pontos mencionados acima fornecem uma breve visão geral de algumas considerações importantes. No entanto, a melhor abordagem é escolher um fabricante profissional de máquinas de dobrar. Eles podem fornecer vários planos alternativos adaptados à sua situação específica, garantindo uma resolução mais razoável e eficaz.