Índice
Cortadores a laser são uma classe capaz e versátil de máquinas-ferramentas controladas numericamente. Elas são usadas em praticamente todas as indústrias para alto rendimento, corte de precisão, gravação e marcação — desde o uso doméstico cortando cartão/papel até a construção naval e engenharia pesada. Elas aplicam radiação laser bem colimada e firmemente focada para perfurar ou gravar materiais, com precisão controlada por CNC e alta produtividade. Existem vários tipos de lasers comumente usados em corte a laser, cada um com suas características e aplicações específicas, tornando-o adequado para nichos de mercado selecionados.
Quatro tipos principais de laser são usados em equipamentos de corte a laser, com uma enorme variedade de potências, de alguns mW a mais de 100 kW. Uma variedade de comprimentos de onda de emissão os tornam adequados para tipos específicos de materiais. Há também fatores operacionais que tornam alguns tipos de lasers particularmente bem adaptados a setores de mercado limitados, sem que nenhuma solução seja universal.
4 tipos comuns de cortadores a laser
Cortador a laser de fibra
Cortadores a laser de fibra são usados principalmente para cortar e gravar peças metálicas. Eles oferecem várias vantagens sobre outros tipos de lasers, tornando-os uma escolha lógica em aplicações industriais.
Os lasers de fibra recebem esse nome devido à fibra óptica quimicamente dopada usada para induzir o laser e entregar a energia ao ponto de corte. A fonte do laser começa com um laser primer, geralmente um tipo de diodo, que injeta um feixe de baixa potência na fibra. Esse feixe é então amplificado dentro da fibra óptica, que é dopada com elementos de terras raras, como itérbio (Yb) ou érbio (Er). O processo de dopagem induz a fibra a agir como um meio de ganho, amplificando o feixe de laser por excitações/emissões em cascata.
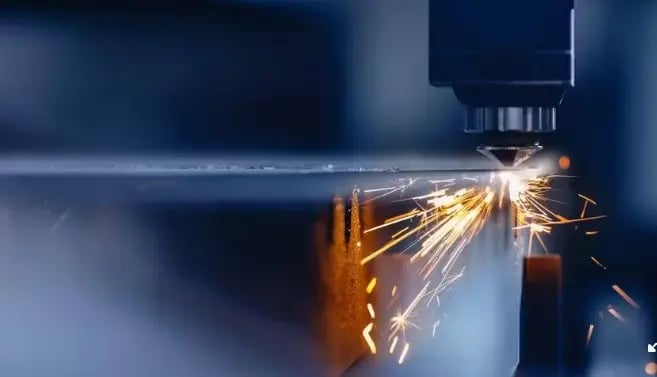
Os lasers de fibra emitem um comprimento de onda no espectro infravermelho próximo, em torno de 1,06 μm. Esse comprimento de onda é completamente absorvido por metais, tornando os lasers de fibra particularmente adequados para cortar e gravar essa classe de materiais, até mesmo os metais reflexivos "problemáticos".
Uma das vantagens particulares dos lasers de fibra é sua qualidade excepcional de feixe. Essa qualidade de feixe determina a capacidade do laser de produzir uma aplicação altamente focada de radiação e, portanto, um caminho de corte menor e mais preciso e maior energia específica (energia por unidade de área). Isso também implica menor divergência de feixe, permitindo cortes que abrem menos com o aumento da espessura do alvo.
Os lasers de fibra são conhecidos por oferecer maiores velocidades de corte e produtividade. Isso também contribui para menor consumo de energia, em comparação a outros tipos de lasers. Os lasers de fibra são geralmente otimizados para cortar metais, incluindo: aço inoxidável, aço carbono, alumínio, cobre, latão e várias ligas. Eles não são tão eficazes para cortar materiais não metálicos como madeira, acrílico ou plásticos, que são cortados de forma mais eficaz com lasers de CO2. Os lasers de fibra com níveis de potência mais altos também podem processar metais mais espessos de forma eficaz.
Os lasers de fibra possuem uma construção elegante, simples e robusta e uma característica de estado quase sólido. Isso resulta em requisitos de manutenção suprimidos, em relação a outras classificações de laser. A ausência de espelhos e alguns dos componentes focais mais delicados minimizam problemas de alinhamento, melhoram a qualidade do feixe e elevam a vida útil. Alguns modelos são capazes de fornecer dezenas de milhares de horas de uso, antes de exigir manutenção significativa.
Os lasers de fibra são, em muitos aspectos, a escolha ideal para tarefas de corte/ablação e gravação de metal. Os fatores essenciais que consolidam sua viabilidade comercial incluem: fornecer alto rendimento, precisão excepcional, operacional e eficiência energética e baixa manutenção. Suas capacidades os tornam uma ferramenta preferida em diversas indústrias, incluindo: automotiva, aeroespacial, eletrônica e manufatura, nas quais o processamento preciso e eficiente de metais é crucial.
Lasers de CO2
Apesar de serem os primeiros dispositivos explorados comercialmente, os lasers de CO2 continuam sendo muito amplamente utilizados no setor. Eles se beneficiam de menor CAPEX (embora maior OPEX) e um alto grau de versatilidade/aplicabilidade do material. Eles são particularmente adequados para processar materiais não metálicos com precisão e eficiência moderadas. Eles também são considerados viáveis em muitas aplicações de corte de metal. Para processamento de metal, o espectro de absorção é adverso, mas várias soluções alternativas amplamente utilizadas podem facilitar uma melhor funcionalidade.
Os lasers de CO2 são dispositivos de excitação de gás que usam uma mistura de dióxido de carbono (CO2), nitrogênio (N2) e hélio (He) para produzir o feixe de laser em uma sequência de cascata de energia. A fonte de laser normalmente consiste em um tubo de flash de xenônio ou similar, que é excitado por uma descarga elétrica para iniciar o processo de emissão estimulada. Este processo é caracterizado por três transições de energia distintas, apenas a última das quais envolve uma emissão de fótons. As moléculas de N2 são elevadas a um estado de energia mais alto que então transmitem para as moléculas de CO2, que emitem fótons à medida que perdem sua energia de excisão ao impactar átomos de He.
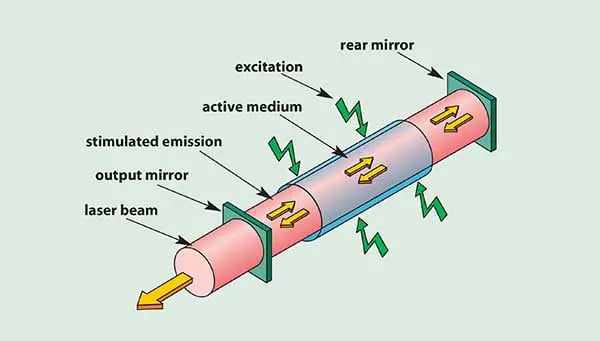
Esta classe emite em torno de 10,6 μm, no espectro infravermelho distante. Este comprimento de onda é fortemente absorvido por materiais orgânicos como madeira, plásticos, couro, vários tecidos, papel e alguns compostos não metálicos, resultando em corte altamente eficiente, limpo e preciso.
Eles têm uma qualidade de feixe inferior em comparação aos lasers de fibra, o que significa que o feixe de laser é menos focado. Isso é um subproduto da complexidade óptica relativa dos dispositivos e também é intrínseco ao sistema de emissão de gás. No entanto, os avanços na tecnologia de laser de CO2 melhoraram a qualidade do feixe ao longo da longa vida útil da tecnologia. O feixe normalmente gera um tamanho de ponto maior e maior divergência do que outros sistemas, o que pode afetar significativamente a precisão dos cortes.
Os lasers de CO2 são amplamente aceitos devido à sua versatilidade, custo de compra relativamente baixo e maior uso de energia por watt de corte. Eles podem ser consideravelmente mais lentos no corte de materiais metálicos espessos do que os lasers de fibra. Para materiais não metálicos, eles podem oferecer excelente velocidade de corte, tornando-os adequados para designs complexos e uma ampla gama de aplicações. Os lasers de CO2 exigem mais manutenção do que os lasers de fibra, devido à presença de espelhos e outros componentes ópticos em seu design. Além disso, a fonte primária do laser se degrada com o tempo de uso. Eles precisam de limpeza regular do sistema óptico e realinhamento delicado para manter o desempenho.
Para mais informações, consulte nosso guia sobre cortadores a laser de CO2.
Lasers Nd: YAG / Nd: YVO
Os lasers Nd:YAG (neodymium-doped yttrium aluminium granate) e Nd:YVO (neodymium-doped yttrium vanadate) são dispositivos de estado sólido fundamentalmente semelhantes. Ambos emitem no espectro infravermelho próximo, diferenciado pelo meio dentro do qual a emissão estimulada ocorre. Eles são mais aplicáveis ao corte e marcação de metais e uma gama limitada de não metais.
Os lasers Nd:YAG e Nd:YVO são dispositivos laser de estado sólido intimamente relacionados dopados com íons de neodímio. Nos lasers Nd:YAG, o meio laser são cristais de granada de ítrio e alumínio dopados com íons de neodímio. Nos lasers Nd:YVO, o meio laser são cristais de vanadato de ítrio dopados de forma semelhante com íons de neodímio. Quando bombeados opticamente (por um laser ou fonte de descarga), os íons de neodímio ficam excitados. Isso leva à emissão de luz laser, pois eles perdem a energia de excitação.
Esses lasers emitem em um comprimento de onda de 1,064 μm, enquanto os lasers Nd:YVO emitem em 1,064 μm ou 1,34 μm, diferenciados pela orientação do cristal. Esses comprimentos de onda estão na faixa do infravermelho próximo e são bem absorvidos por muitos metais, tornando esses lasers adequados para aplicações de corte, gravação e marcação de metais. Os lasers de neodímio geralmente possuem alta qualidade de feixe, baixa divergência e um pequeno tamanho de ponto, resultando em alta energia específica.
Os lasers Nd:YAG e Nd:YVO são eficazes para cortar e processar metais, especialmente chapas finas e materiais de alta precisão e calibre inferior. Eles são mais bem usados para metais, incluindo os materiais mais "reflexivos": aço inoxidável, aço carbono, alumínio, latão e cobre. Eles também são adequados para cortar cerâmicas, plásticos e certos compostos — mas são mal adaptados para cortar outros materiais não metálicos. Esses tipos de laser são muito apreciados por sua durabilidade e requisitos de manutenção relativamente baixos, melhorando o tempo de atividade e o desempenho comercial. Eles podem fornecer milhares de horas de uso antes de exigir grande manutenção.
Lasers de diodo direto
Os lasers de diodo direto (ou simplesmente diodo) são um tipo de tecnologia de laser que utiliza junções semicondutoras simples para gerar luz laser. Eles estão aumentando a penetração de mercado em aplicações industriais, incluindo: corte, soldagem e tratamento de superfície. Um laser direto laser de diodo é baseado em junções semicondutoras, tipicamente feitas de arsenieto de gálio (GaAs). Quando uma corrente de polarização direta é aplicada ao diodo, ele emite luz por eletroluminescência, sem exigir uma fonte de luz para iniciação. A luz emitida é então guiada e focada em um feixe de laser por elementos ópticos que fazem uma cavidade ressonante de emissão estimulada com um meio espelho em uma extremidade, através do qual a energia do laser é emitida.
Os lasers de diodo estão disponíveis em uma variedade de comprimentos de onda, variados pela seleção do material semicondutor, dopantes e design da cavidade ressonante. Os comprimentos de onda mais comuns para lasers de diodo direto usados em aplicações de corte estão no espectro infravermelho próximo, em torno de 900 a 1.100 nm (0,9 a 1,1 μm). Sistemas de diodo alternativos podem emitir nas faixas de comprimento de onda azul e verde. A qualidade do feixe de lasers de diodo direto pode variar consideravelmente, embora em geral a qualidade do feixe de diodo esteja melhorando a cada geração de dispositivo. A qualidade do feixe geralmente não corresponde à dos lasers de fibra ou lasers de CO2.
Os lasers de diodo oferecem excelente eficiência energética pela conversão de baixa perda de energia elétrica em luz laser, reduzindo um pouco os custos operacionais. No entanto, suas velocidades de corte são geralmente menores do que para dispositivos baseados em laser de fibra ou CO2, quando as espessuras do material são maiores. Os lasers de diodo direto são adequados para cortar uma variedade de materiais, incluindo: metais, plásticos, compostos e certos materiais não metálicos. Eles são considerados eficazes para corte ou soldagem de alta velocidade de chapas finas de metal, tornando-os adequados para indústrias como: automotiva, eletrônica e fabricação de chapas metálicas. Esta família de dispositivos é mais simples e mais robusta em construção do que a maioria dos outros tipos de laser, resultando em uma vida útil operacional mais longa e menores requisitos de manutenção. Eles também são de tamanho físico menor e requerem menos dispositivos auxiliares, melhorando ainda mais a manutenção e a adequação para aplicações móveis.
Conclusão
Esses são apenas alguns exemplos, e a escolha do cortador a laser depende de fatores como os materiais a serem cortados, a precisão desejada e as aplicações pretendidas. Cada tipo de cortador a laser tem seus pontos fortes e limitações, então é importante selecionar aquele que melhor se adapta às necessidades específicas da tarefa de corte em questão.