Índice
Introdução
Hydraulic press brake machines are indispensable tools in the sheet metal fabrication industry, offering precision, versatility, and efficiency in bending operations. In this comprehensive guide, we will explore the principles, advantages, applications, and best practices associated with hydraulic press brake technology.
Definition of Hydraulic Press Brake Machines
Hydraulic press brake machines are advanced sheet metal fabrication tools designed to bend and shape metal components with precision and efficiency. These machines utilize hydraulic systems to apply controlled force to a workpiece, allowing for accurate bending at various angles and shapes. Hydraulic press brake machines consist of several key components, including a hydraulic system, a ram, a bed, and a back gauge. The hydraulic system generates hydraulic pressure, which is transmitted to the ram to exert force on the workpiece, causing it to bend against the stationary bed. The back gauge assists in positioning the workpiece accurately for precise bending operations. Hydraulic press brake machines are widely used in industries such as automotive, aerospace, construction, and electronics for manufacturing a diverse range of components and structures. They offer high precision, versatility, and efficiency, making them essential equipment in modern sheet metal fabrication processes.
Hydraulic press brake technology plays a pivotal role in sheet metal fabrication, offering numerous advantages and contributing significantly to the efficiency, precision, and versatility of the manufacturing process. Here are several key reasons why hydraulic press brake technology is indispensable in sheet metal fabrication:
Importance of Hydraulic Press Brake Technology in Sheet Metal Fabrication
Precision Bending: Hydraulic press brake machines provide precise control over bending operations, allowing manufacturers to achieve tight tolerances and accurate bend angles. This precision is essential for ensuring the dimensional accuracy and consistency of fabricated parts, meeting the stringent requirements of various industries.
Versatility: Hydraulic press brake machines are capable of bending a wide range of materials, including steel, aluminum, stainless steel, and other alloys. They can handle varying material thicknesses, from thin sheets to heavy plates, making them suitable for a diverse range of applications across industries.
Flexibility in Bending Capacities: Hydraulic press brake machines offer flexibility in bending capacities, allowing manufacturers to produce components of different sizes and shapes. With adjustable ram stroke lengths and customizable tooling options, hydraulic press brakes can accommodate a variety of bending requirements, from simple bends to complex geometries.
Efficiency and Productivity: Hydraulic press brake technology enables efficient and productive sheet metal fabrication processes. These machines feature fast cycle times, rapid setup capabilities, and automated bending sequences, minimizing downtime and maximizing throughput. This efficiency contributes to reduced lead times and increased production output, enhancing overall productivity.
Hydraulic press brake machines consist of several key components, each playing a vital role in the bending process and overall functionality of the machine. Understanding these components is essential for operating and maintaining hydraulic press brakes effectively. Here are the key components of hydraulic press brake machines:
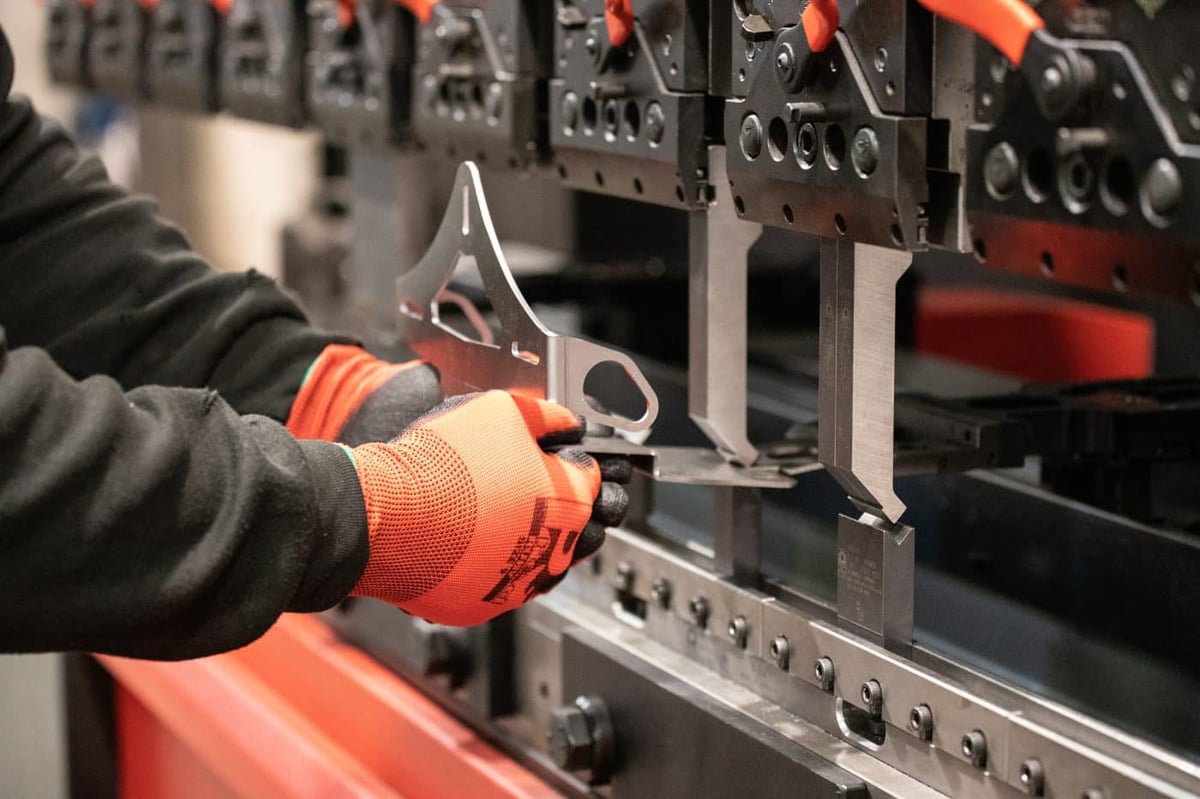
Key Components of Hydraulic Press Brake Machines
Sistema Hidráulico
The hydraulic system is the heart of a hydraulic press brake machine, responsible for generating and transmitting hydraulic pressure to the bending mechanism.
It typically comprises hydraulic pumps, cylinders, valves, hoses, and reservoirs.
The hydraulic system converts mechanical energy into hydraulic energy, providing the force necessary for bending operations.
Bater
The ram is the moving component of the hydraulic press brake machine, which exerts force on the workpiece to perform bending operations.
It moves vertically downward to apply pressure on the sheet metal, causing it to bend against the stationary bed or tooling.
The ram may be equipped with punch and die tooling to shape the workpiece according to desired specifications.
Cama
The bed, also known as the lower beam or bed beam, provides a flat and stable surface for supporting the workpiece during bending operations.
It is typically made of heavy-duty steel and is securely anchored to the machine frame to withstand the bending forces exerted by the ram.
The bed ensures proper alignment and stability of the workpiece, facilitating accurate and consistent bending results.
Medidor traseiro
The back gauge is a positioning device located at the rear of the hydraulic press brake machine, opposite the ram.
It consists of adjustable fingers or stops that help position the workpiece accurately relative to the bending tooling.
The back gauge ensures consistent bend angles and dimensions across multiple workpieces by precisely controlling the positioning of the workpiece.
Painel de controle
The control panel serves as the interface between the operator and the hydraulic press brake machine, allowing for the adjustment of bending parameters and monitoring of the bending process.
It may feature a touchscreen display or a combination of buttons, switches, and knobs for inputting bending parameters such as bend angle, bend length, and material thickness.
Advanced hydraulic press brake machines may be equipped with computer numerical control (CNC) systems, enabling programmable bending sequences and automation of bending operations.
Ferramentas
Tooling refers to the various punches and dies used in hydraulic press brake machines to shape the workpiece during bending operations.
Punches are mounted on the ram, while dies are mounted on the bed or in the tool clamping system.
Different types of tooling are available to accommodate various bending requirements, such as V-dies for air bending, acute angle dies for bottom bending, and special tooling for specific applications.
Basic Working Principle
The basic working principle of a hydraulic press brake involves the use of hydraulic pressure to bend sheet metal to a desired angle or shape. Here's a step-by-step overview of the working principle:
Initial Setup
The operator selects the appropriate tooling, including the punch and die, based on the desired bend angle and material thickness.
The workpiece, typically a flat sheet of metal, is positioned on the bed of the press brake machine between the punch and die.
Ativação do sistema hidráulico:
The operator activates the hydraulic system, which consists of hydraulic pumps, cylinders, valves, hoses, and reservoirs.
Hydraulic fluid is pumped from the reservoir into the hydraulic cylinders, creating pressure within the system.
Movimento de Carneiro
As hydraulic pressure builds up, the hydraulic cylinders extend, causing the ram to move downward towards the workpiece.
The ram exerts force on the workpiece, pressing it against the stationary die.
Bending Operation
The force applied by the ram causes the sheet metal to bend along the predetermined bend line, defined by the position of the die.
The operator controls the bending process by adjusting parameters such as ram speed, pressure, and stroke length using the control panel.
Bend Angle Adjustment
The operator monitors the bending process and adjusts the position of the back gauge, if necessary, to ensure accurate positioning of the workpiece for subsequent bends.
Additional bends may be performed by repeating the above steps, repositioning the workpiece as needed.
Liberação e remoção
Once the bending operation is complete, the hydraulic pressure is released, and the ram retracts to its original position.
The operator removes the bent workpiece from the press brake machine for further processing or assembly.
The hydraulic press brake's ability to precisely control the application of force allows for accurate and repeatable bending operations, making it a versatile and indispensable tool in sheet metal fabrication. By adjusting parameters such as pressure, speed, and stroke length, operators can achieve a wide range of bend angles and geometries to meet the requirements of various applications.
Hydraulic press brakes offer several advantages over other types of bending machines, making them a popular choice for sheet metal fabrication. Here are some key advantages of hydraulic press brakes:
Vantagens da prensa dobradeira hidráulica
Precisão e exatidão
Hydraulic press brakes provide precise control over bending operations, allowing for accurate and repeatable results.
Operators can adjust parameters such as ram speed, pressure, and stroke length to achieve tight tolerances and precise bend angles.
Versatilidade
Hydraulic press brakes are capable of bending a wide range of materials, including steel, aluminum, stainless steel, and alloys.
They can handle varying material thicknesses, from thin sheets to heavy plates, making them suitable for a diverse range of applications across industries.
Flexibility in Bending Capacities
Hydraulic press brakes offer flexibility in bending capacities, allowing manufacturers to produce components of different sizes and shapes.
With adjustable ram stroke lengths and customizable tooling options, hydraulic press brakes can accommodate a variety of bending requirements, from simple bends to complex geometries.
Eficiência e Produtividade
Hydraulic press brakes feature fast cycle times and rapid setup capabilities, minimizing downtime and maximizing throughput.
Automated bending sequences and programmable features further enhance efficiency, allowing for high-volume production with minimal manual intervention.
Facilidade de operação
Hydraulic press brakes are user-friendly and easy to operate, making them accessible to operators of varying skill levels.
Intuitive control interfaces and ergonomic designs streamline the bending process, reducing operator fatigue and increasing productivity.
Segurança
Hydraulic press brakes are equipped with safety features to protect operators and prevent accidents.
These features may include safety guards, light curtains, emergency stop buttons, and interlocking systems to ensure safe operation during bending operations.
Custo-eficácia
Despite their advanced capabilities, hydraulic press brakes offer a cost-effective solution for sheet metal fabrication.
They provide high-quality results with minimal material waste, reducing production costs and maximizing the return on investment for manufacturers.
Conclusão
The hydraulic press brake, with its ability to deliver precision, versatility, and enhanced safety, has revolutionized numerous industries. It’s vital, however, to understand its workings, maintenance needs, and operational costs to fully harness its potential.
Whether used in the automotive, aerospace, or the wider manufacturing sector, these machines are invaluable tools, and an understanding of their features, costs, and proper maintenance can ensure their effective and efficient use for many years to come.