Hydraulic press brakes are essential machines in sheet metal processing, known for their ability to bend metal sheets with high precision and efficiency. This comprehensive guide delves into the various types of freios de prensa hidráulica, the crucial molds that determine the shape and angle of the workpieces, and the advanced safety systems that ensure operator and equipment safety. Additionally, we explore optional features that enhance the functionality of hydraulic press brakes, making them adaptable to diverse production needs. Whether you're in large-scale manufacturing or require high-precision bending, understanding these aspects will help you select and utilize the right hydraulic press brake for your operations.
Índice
What is a Hydraulic Press Brake?
O prensa dobradeira hidráulica is a machine that uses a hydraulic transmission system to bend metal sheets into various shapes. It is widely used in the sheet metal processing industry. The main components of a hydraulic press brake include the frame, workbench, ram, hydraulic system, electrical control system, and tooling. By controlling the up and down movement of the ram, the machine bends metal sheets to the desired shape and angle.
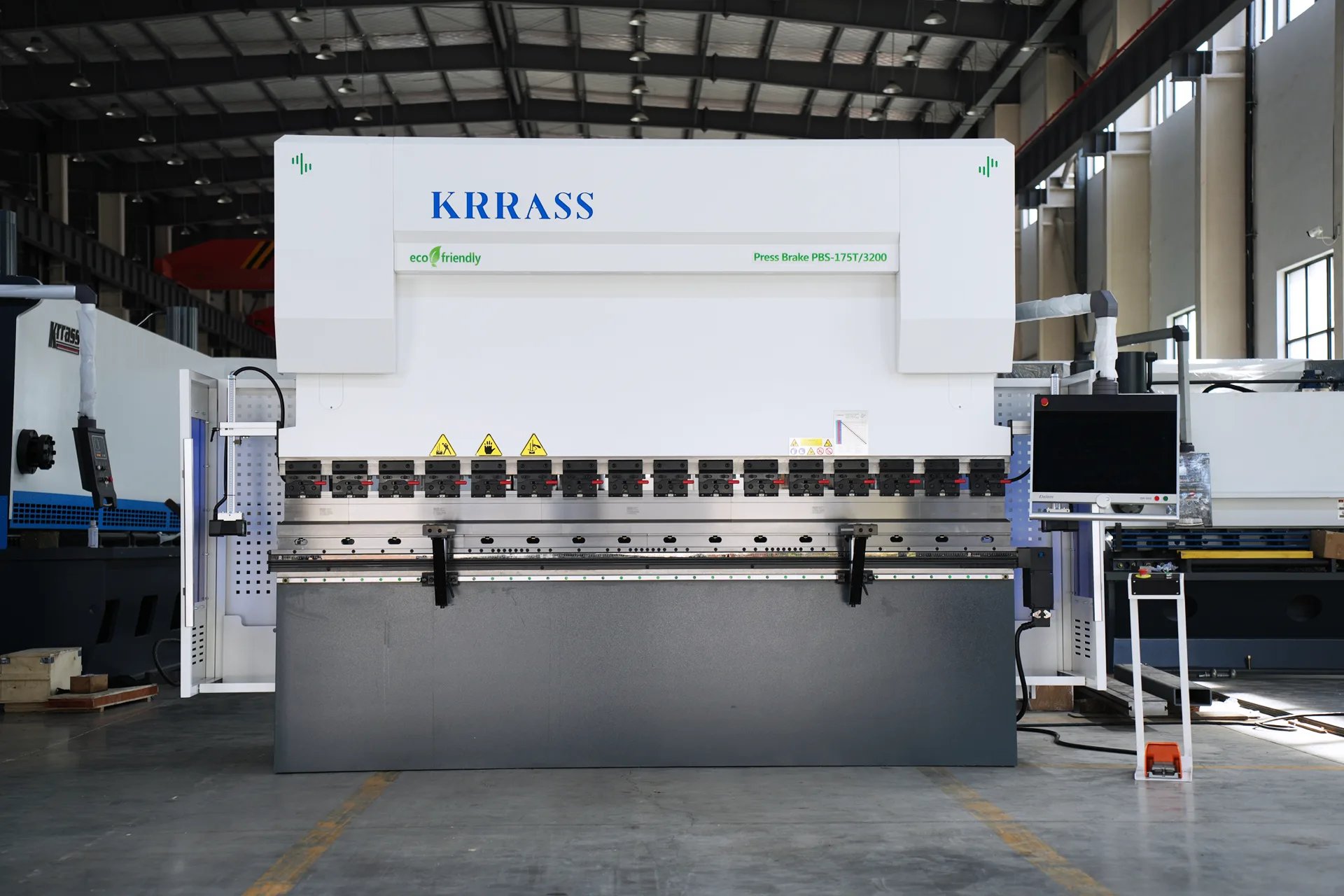
Tipos de dobradeiras de pressão
Hydraulic press brakes are primarily classified into two types based on their control systems and structural characteristics: Torsion Bar Press Brakes and Electro-Hydraulic Press Brakes.
Torsion Bar Press Brakes
The torsion-bar bending machine uses torsion-bar to link left and right swing rods to form torsion-bar forcing synchronization mechanism to move up and down the oil cylinders on both sides. Therefore, torsion-bar bending machine is a mechanical forced synchronization mode, and the parallelism of slide blocks cannot be automatically checked and adjusted. Usually, torsion axis bending machine is also called Prensa dobradeira NC.
Vantagens:
- Simple Structure: Torsion bar press brakes have a relatively simple structure, making them easy to maintain.
- Lower Cost: They are more cost-effective to manufacture and maintain compared to electro-hydraulic press brakes, making them suitable for small and medium-sized enterprises.
- Facilidade de operação: These machines are straightforward to operate, ideal for large-volume, low-precision sheet metal processing.
Desvantagens:
- Lower Precision: Due to mechanical torsion synchronization, achieving high-precision synchronization control is challenging.
- Limited Flexibility: They cannot automate complex curves and multi-step bending processes.
- Functional Limitations: Not suitable for complex sheet metal processing needs.
Electro-Hydraulic Press Brakes
The electro-hydraulic press brake is to install a grating ruler on the slider or the bed, and the numerical control system can analyze the synchronization on both sides of the slider through the information fed back by the grating ruler at any time.If there is an error, the numerical control system will adjust through the proportional hydraulic servo valve to synchronize the stroke on both sides of the slider. Numerical control system, hydraulic control valve set and grating ruler form the feedback closed-loop control of electro-hydraulic press brake. Usually, electro-hydraulic bending machine is also called Prensa dobradeira CNC.
Vantagens:
- Alta precisão: Electro-hydraulic servo control systems provide high-precision synchronization control.
- Greater Flexibility: Capable of handling complex curves and multi-step bending processes, suitable for high-precision, high-complexity sheet metal processing.
- High Automation: Can achieve full automation, reducing manual intervention and increasing production efficiency.
Desvantagens:
- Higher Cost: Higher manufacturing and maintenance costs, suitable for large enterprises or high-end market demands.
- Complex Operation: Requires professional technicians for operation and maintenance.
Controllers for Press Brakes
The controller is a crucial component of a press brake, responsible for controlling its movement and operation. Based on the control method, press brake controllers can be classified into the following types:
Mechanical Controllers: Mechanical controllers are traditional press brake controllers known for their simple structure and low cost but limited in control precision and functionality. They typically consist of gears, cams, and linkages, controlling the press brake's movement through mechanical transmission. The main advantage of mechanical controllers is their simplicity and ease of maintenance, but their primary drawbacks are low control precision, low efficiency, and inability to handle complex bending processes.
Numerical Control (NC) Controllers: NC controllers are commonly used in modern press brakes, utilizing electronic components and computer technology to control the machine's movement. They offer high control precision, comprehensive functions, and easy operation. NC controllers include components like central processors, memory, and input/output devices, allowing for pre-set programs to control the press brake's movements and enabling various complex bending processes.
Controladores CNC: CNC controllers are an advanced version of NC controllers, offering even higher control precision and more powerful functionalities. Typically comprising industrial computers, servo drives, and human-machine interfaces, CNC controllers enable more complex bending processes and higher production efficiency.
How to Choose a Press Brake Controller?
When selecting a press brake controller, consider the following factors:
- Control Precision: The higher the control precision, the more accurate the dimensions of the bent parts.
- Funcionalidade: The controller should be able to control the press brake's movement, adjust bending speed and pressure, and set bending programs. More comprehensive functions mean the press brake can better meet user needs.
- Facilidade de operação: The controller should be easy to operate so that even general workers can quickly learn to use it.
- Preço: Controllers vary significantly in price, and users should choose based on their budget.
Common Press Brake Controller Brands
- Estun
- Delem
Estun Controllers Overview
Estun is a well-known manufacturer of numerical control controllers, offering a range of controllers for press brakes. Here is a brief introduction to two popular models, E21 and E310P:
E21 Controller
The E21 is a basic NC controller suitable for users who need a simple and economical solution. It features:
- 2-axis control (X and Y)
- Back gauge control
- Programming functions (single-step, automatic, etc.)
- Fault diagnosis
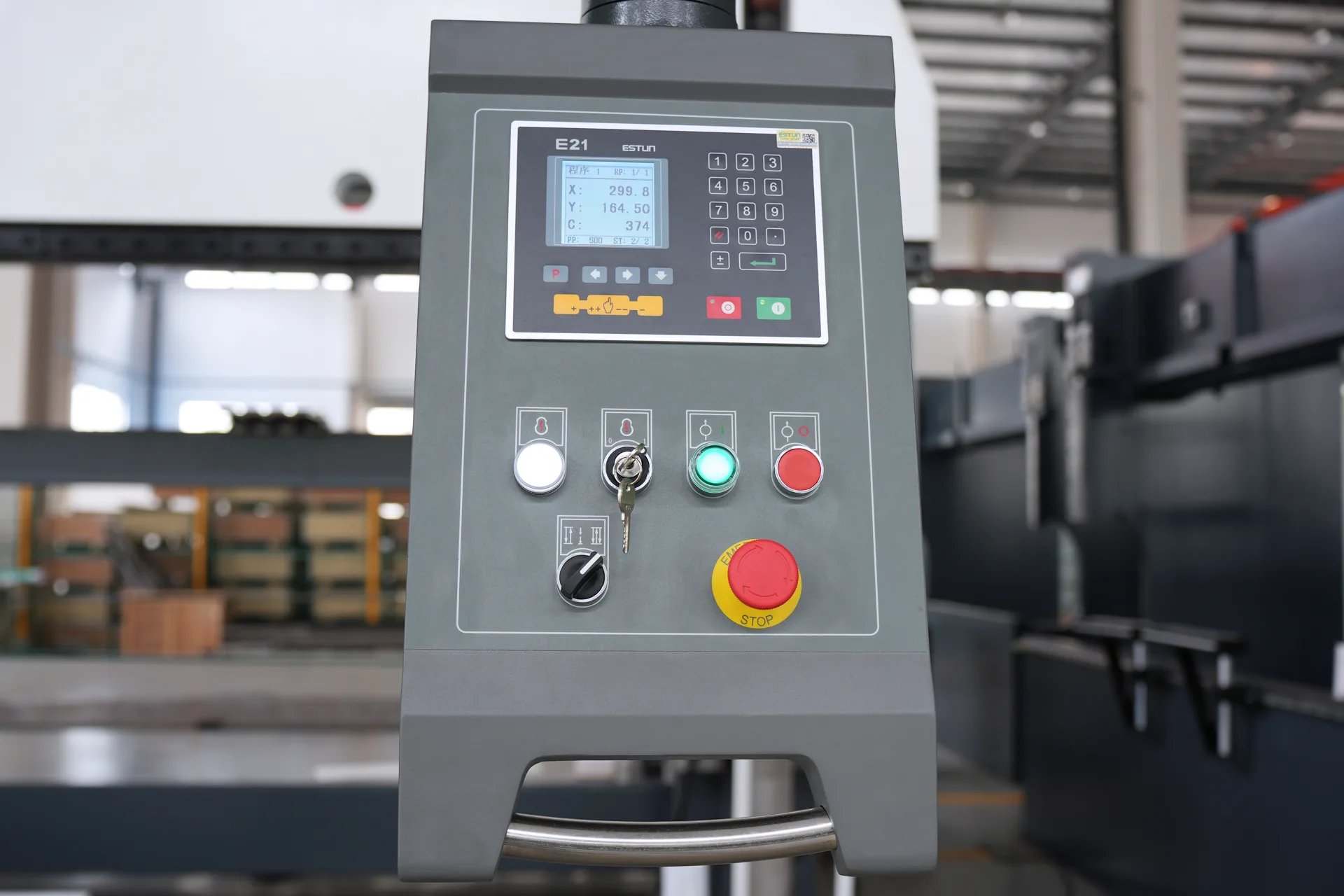
E310P Controller
The E310P is a more advanced NC controller with greater functionality and flexibility, suitable for users needing more control and versatility. It features:
- 3-axis control (X, Y, and R)
- Back gauge control
- Programming functions (single-step, automatic, etc.)
- Sequence programming
- Tool library
- Fault diagnosis
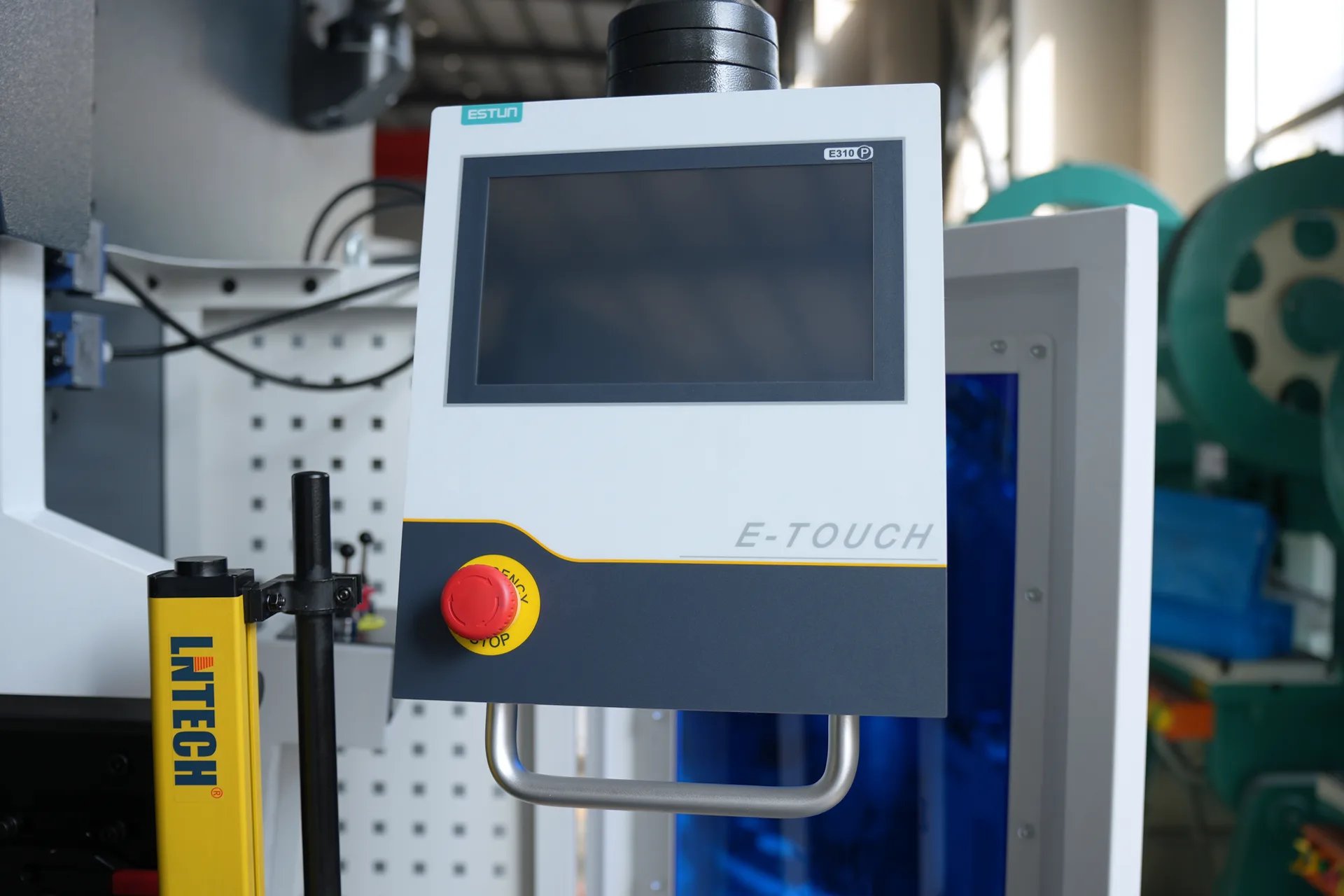
Delem Controllers Overview
Delem is a globally recognized manufacturer of numerical control systems, providing control solutions for various types of metal processing machines, including press brakes. Delem controllers are known for their high precision, reliability, and ease of use, widely used in industries such as aerospace, automotive, shipbuilding, and home appliances.
Here are the mainstream Delem press brake controllers:
DA-41T
The DA-41T control provides a user-friendly and versatile touch control solution for conventional press brake applications with support for multiple axes. It features:
- Panel-based housing
- Tela LCD brilhante
- Beam stop control (Y)
- Back gauge control (X)
- Retract functionality
- Movimento manual de todos os eixos
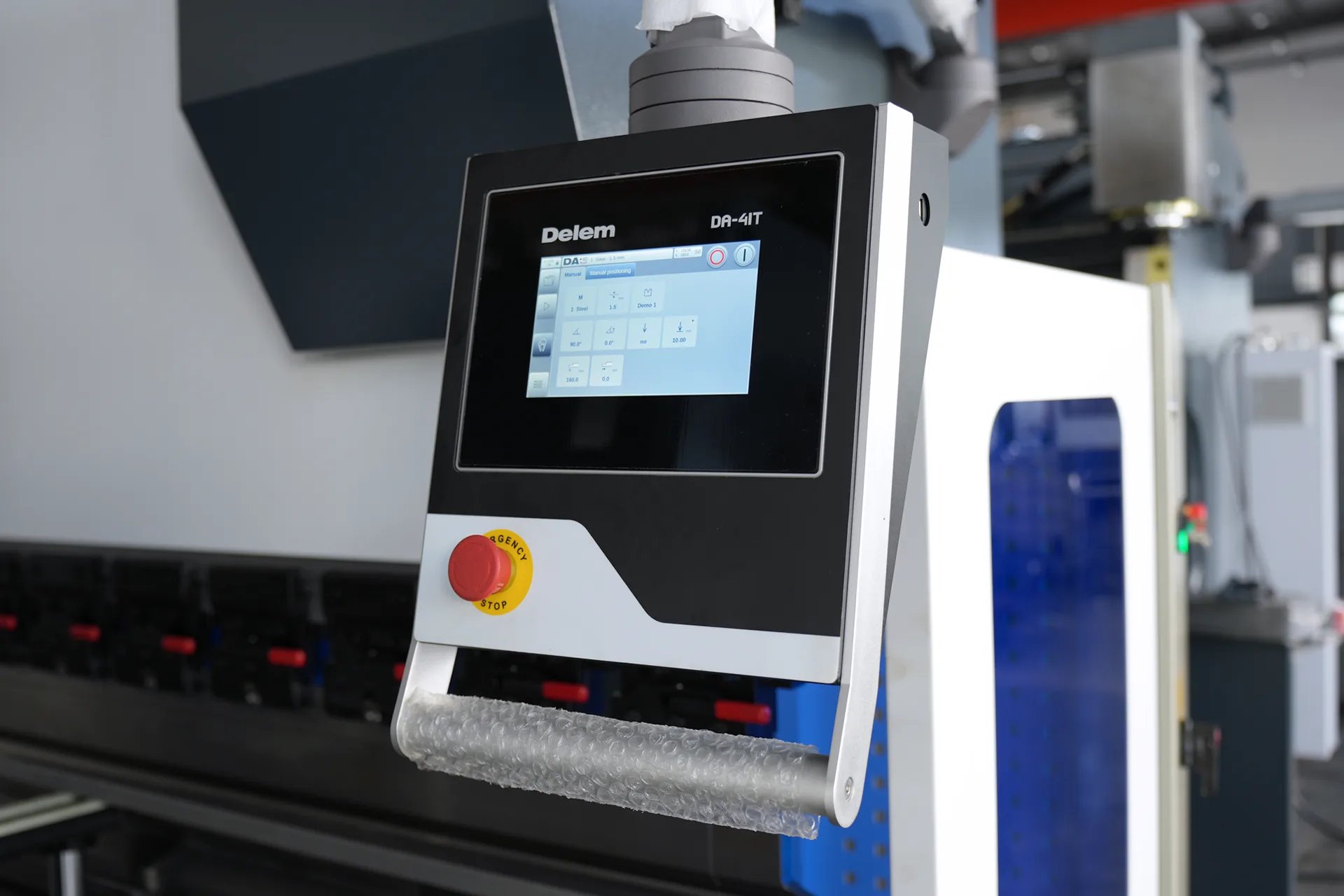
DA-53T
The compact DA-53T adds a state-of-the-art complete touch control solution for synchronized press brakes, offering the easiest CNC programming based on the Delem graphical touch screen user interface. It features:
- Navegação por toque “Hot-key”
- 10.1" high-resolution color TFT
- Up to 4 axes (Y1, Y2 + 2 auxiliary axes)
- Controle de coroação
- Tool/material/product library
- Controle de servo e inversor de frequência
- Advanced Y-axis control algorithms for closed-loop as well as open-loop valves
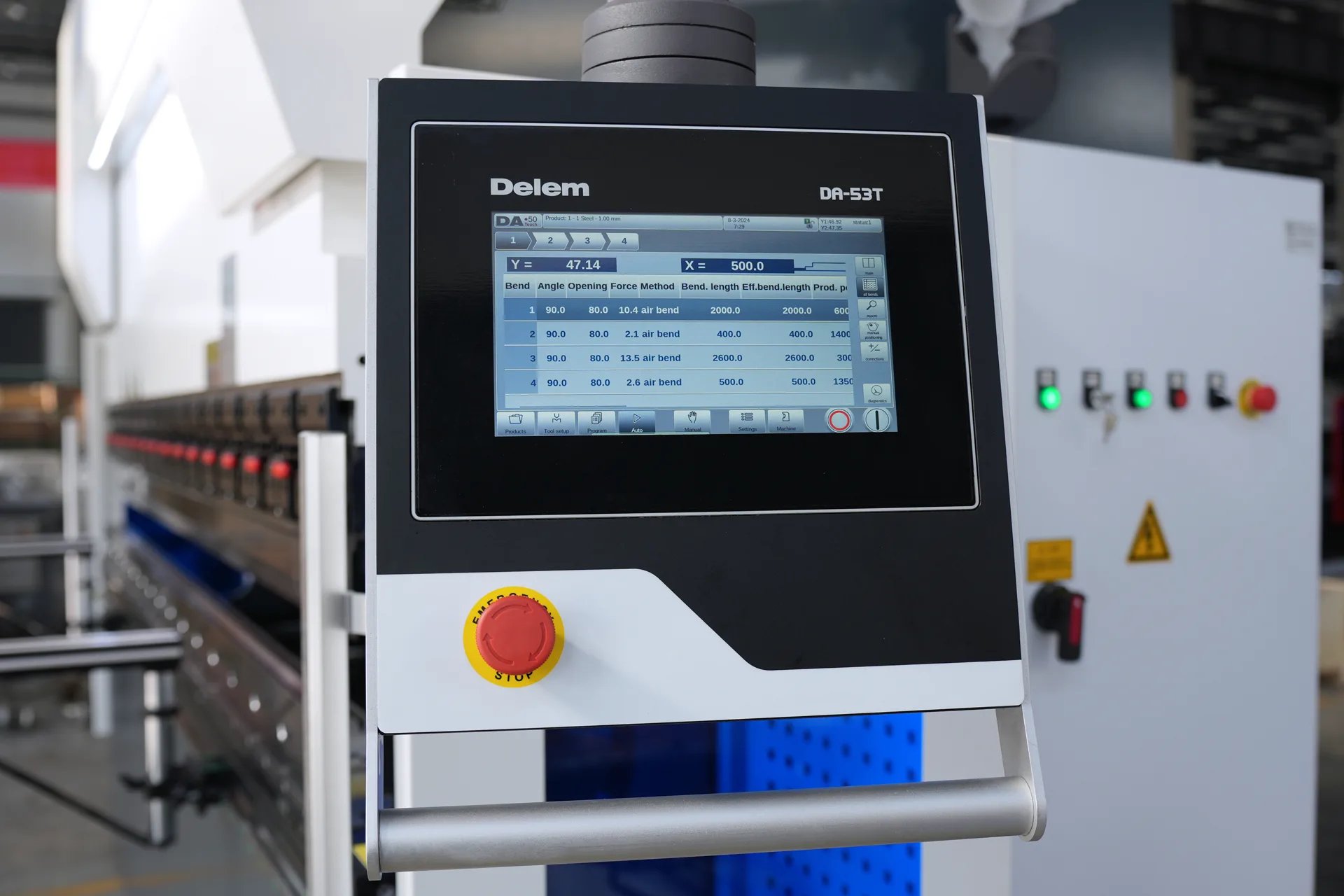
DA-58T
The DA-58T is a state-of-the-art complete 2D graphical control solution for synchronized press brakes, featuring automatic bend sequence calculation and collision detection. It includes:
- Programação gráfica de tela sensível ao toque 2D
- 15" high-resolution color TFT
- Cálculo da sequência de dobra
- Controle de coroação
- Controle de servo e inversor de frequência
- Advanced Y-axis control algorithms for closed-loop as well as open-loop valves
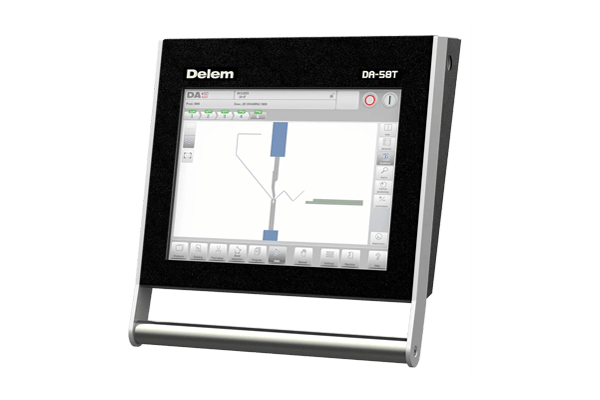
DA-66T
The DA-66T offers 2D programming that includes automatic bend sequence calculation and collision detection, with full 3D machine setup providing true feedback on product feasibility and handling. It includes:
- Modo de programação de tela de toque gráfica 2D
- 17" high-resolution color TFT
- Full Windows application suite
- Compatibilidade com Delem Modusys (escalabilidade e adaptabilidade do módulo)
- USB, interface periférica
- User-specific application support within the control's multitasking environment
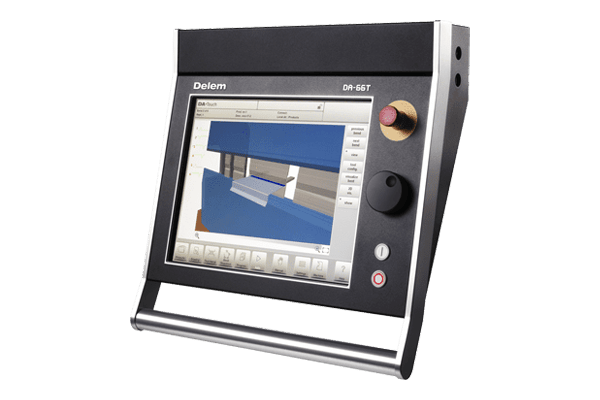
DA-69T
The DA-69T offers both 2D and 3D programming that includes automatic bend sequence calculation and collision detection. It provides full 3D machine setup with multiple tool stations. It features:
- Modo de programação de tela de toque gráfica 3D e 2D
- 3D visualization in simulation and production
- 17" high-resolution color TFT
- Full Windows application suite
- Compatibilidade com Delem Modusys (escalabilidade e adaptabilidade do módulo)
- USB, interface periférica
- User-specific application support within the control's multitasking environment
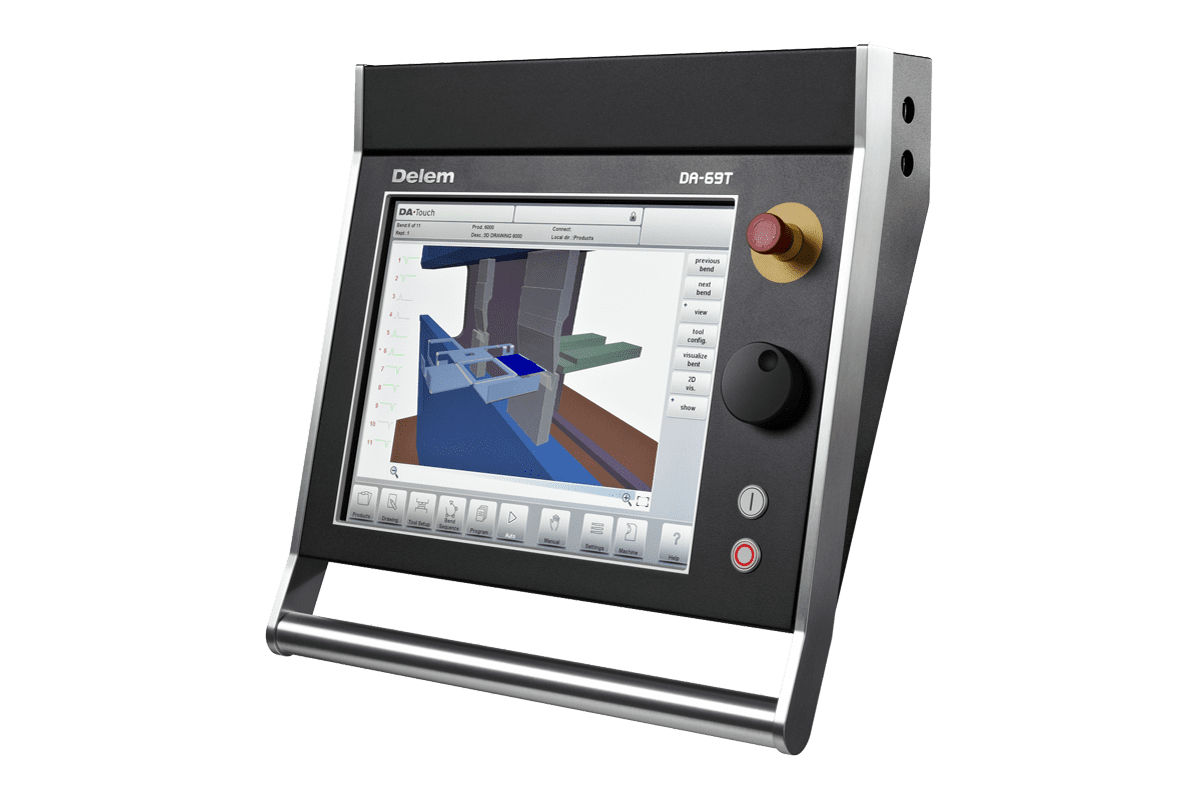
DA-66S
The DA-66S combines fundamental press brake control functionality with the latest enhancements to increase productivity. It includes:
- Modo de programação de tela de toque gráfica 2D
- 3D machine representation in simulation and production
- 24" high-resolution color TFT
- Compatibilidade com Delem Modusys (escalabilidade e adaptabilidade do módulo)
- USB, interface periférica
- User-specific application support within the control's multitasking environment
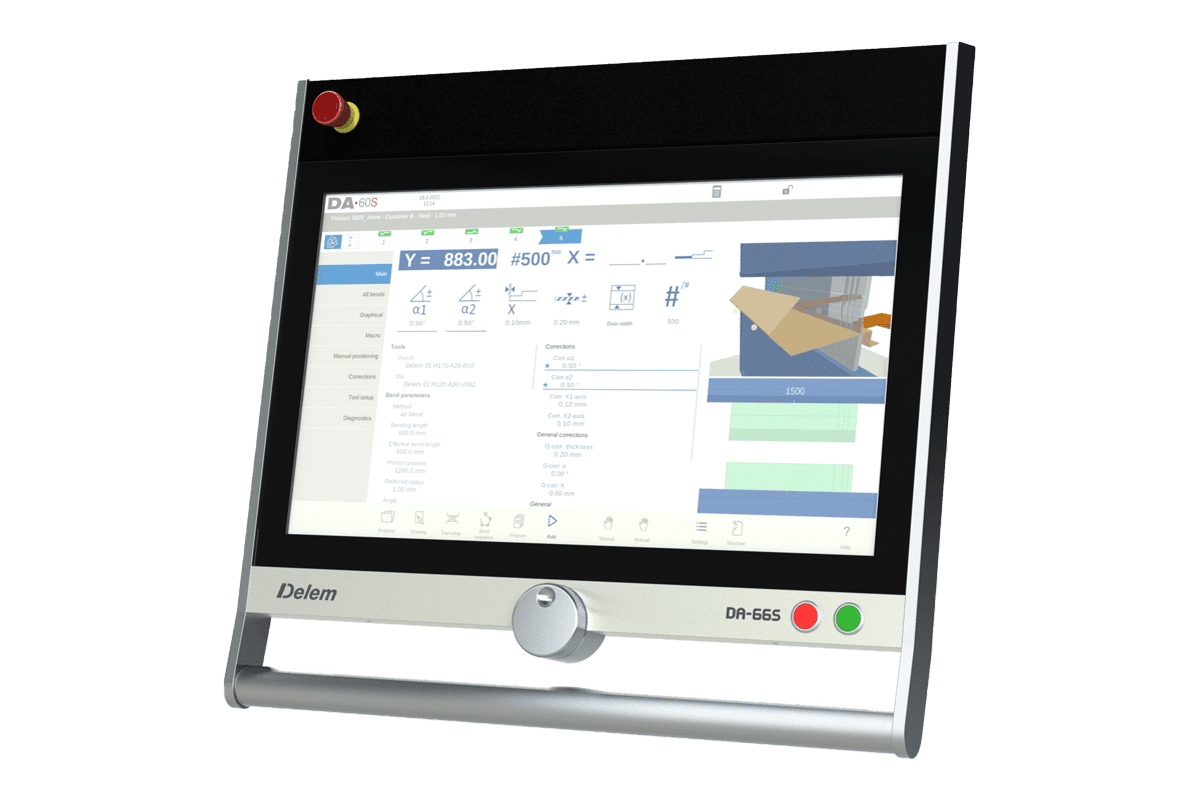
DA-69S
The DA-69S flagship control combines fundamental press brake control functionality with the latest enhancements to increase productivity. It includes:
- Modo de programação de tela de toque gráfica 3D e 2D
- 3D visualization, including 3D machine representation in simulation and production
- 24" high-resolution color TFT
- Compatibilidade com Delem Modusys (escalabilidade e adaptabilidade do módulo)
- USB, interface periférica
- User-specific application support within the control's multitasking environment
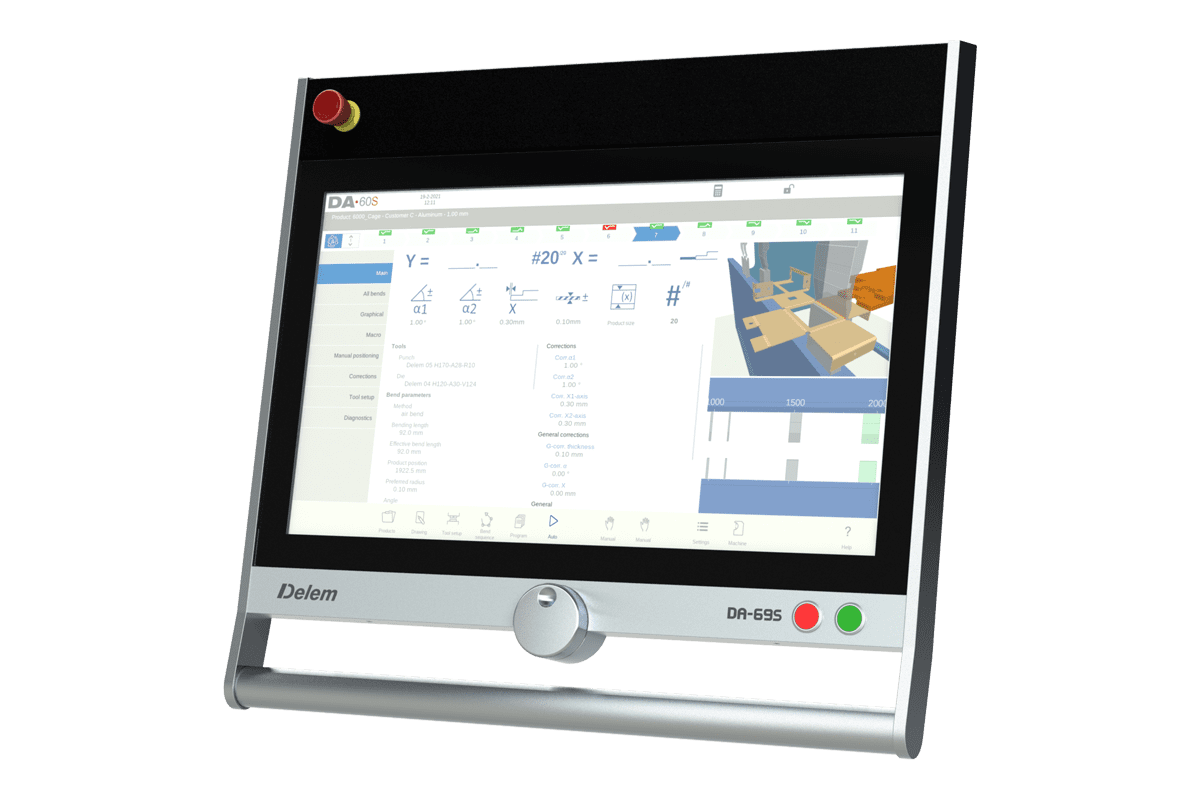
When choosing a Delem press brake controller, consider the following factors:
- The type and size of your press brake
- Your budget
- The functionalities you need
Delem offers a range of controllers to meet your requirements. For more information, please visit the Delem website: Delem.
The Main Motor of Hydraulic Press Brake
The main motor of a prensa dobradeira hidráulica is a crucial component of the hydraulic system, providing power to the hydraulic pump. There are two primary types of main motors used in hydraulic press brakes: conventional motors and servo motors.
Conventional Motors
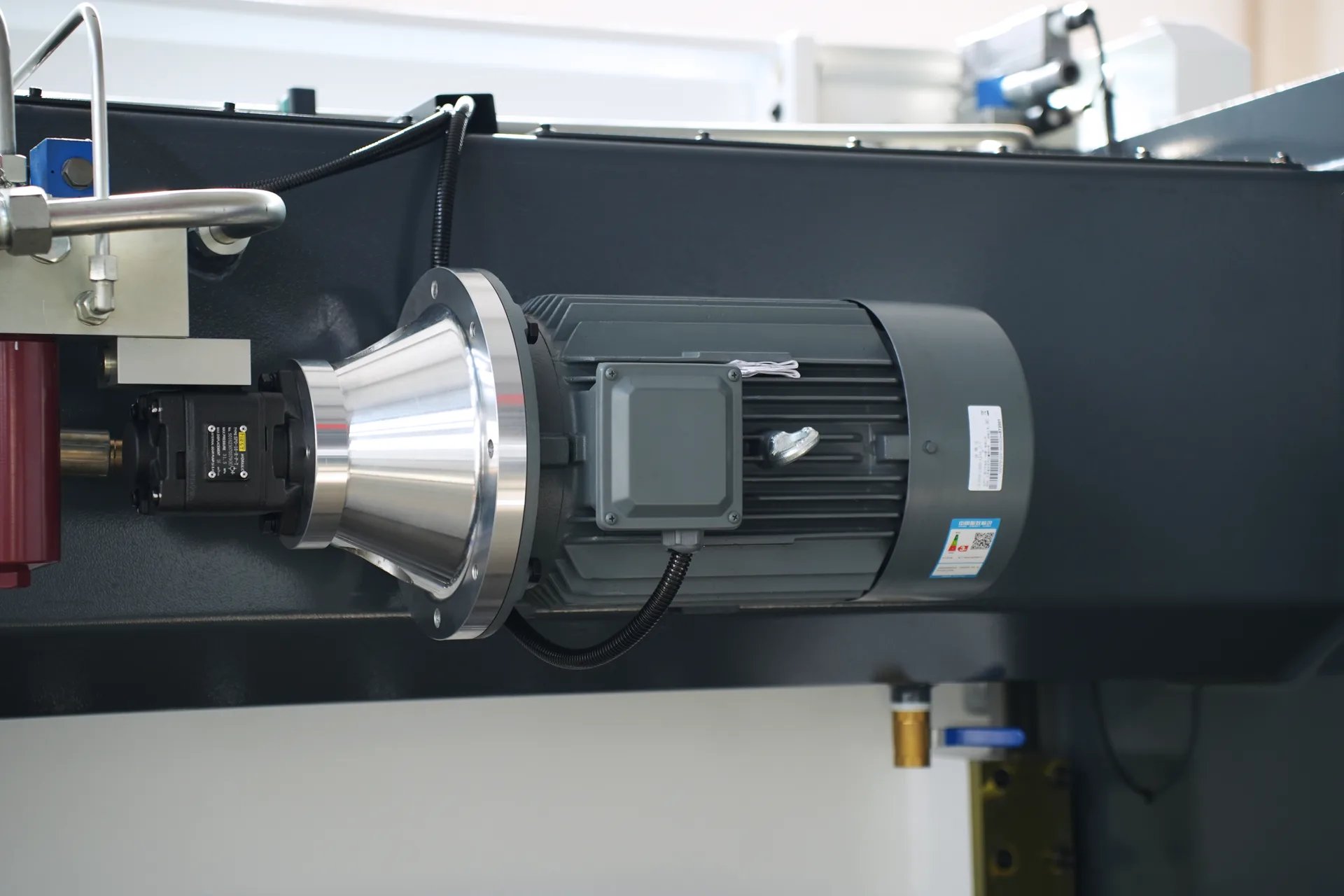
Vantagens:
- Low Cost: Conventional motors have a lower manufacturing cost, making them suitable for budget-conscious users.
- Simple Maintenance: With a simple structure, these motors are relatively easy to maintain and repair.
- Alta confiabilidade: Proven technology with a low failure rate, suitable for long-term stable operation.
Desvantagens:
- Low Efficiency: Compared to servo motors, conventional motors have lower energy efficiency, leading to higher operating costs.
- Low Control Precision: These motors offer lower precision in speed and position control, making them unsuitable for high-precision processing.
- High Starting Impact: They draw a large current at startup, causing significant impact on the power grid.
Servomotores
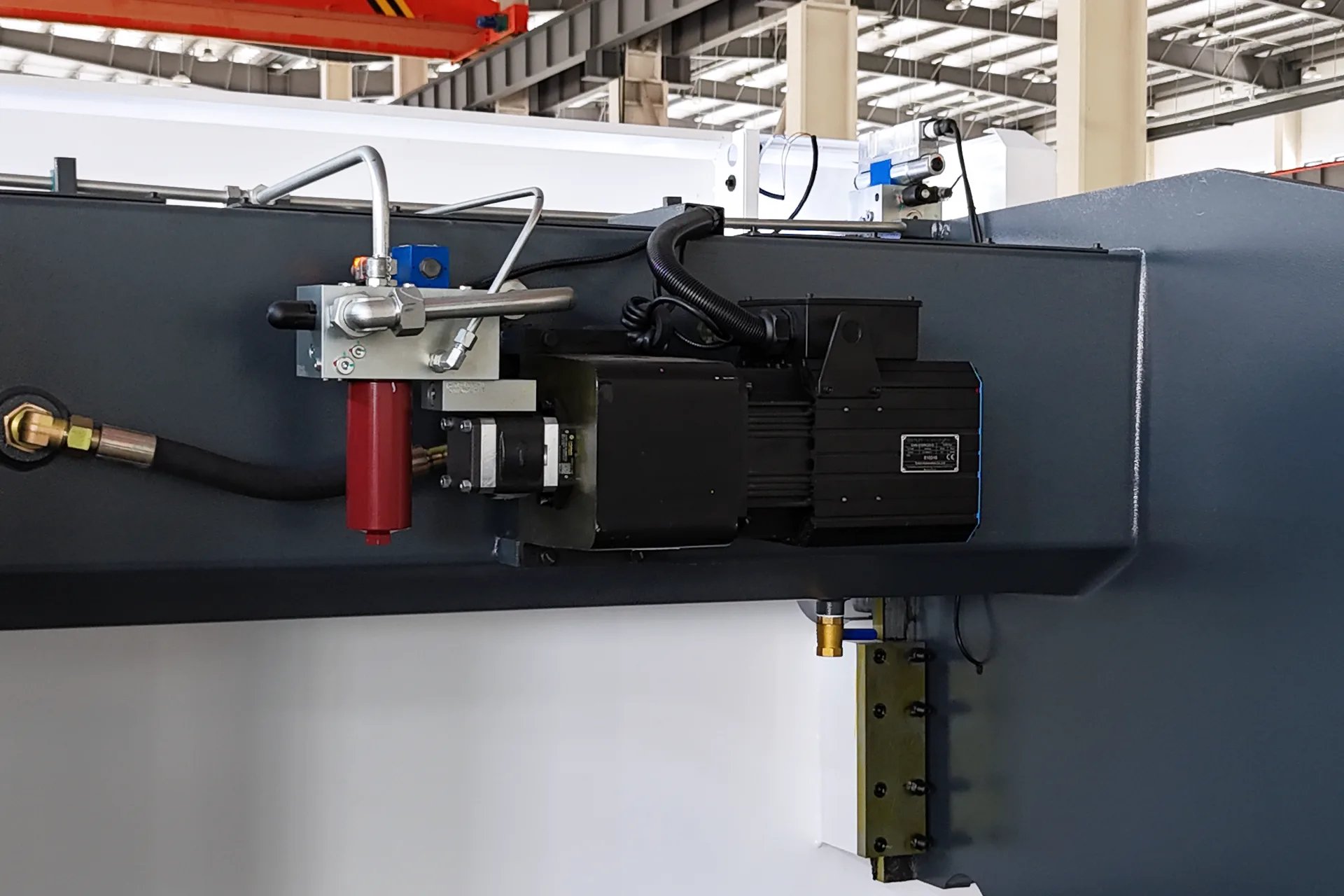
Vantagens:
- Alta eficiência: Servo motors offer higher energy efficiency, reducing operating costs.
- High Precision Control: Capable of achieving high-precision speed and position control, suitable for high-precision processing.
- Quick Response: They have a fast dynamic response capability, meeting the needs of complex processes.
- Good Flexibility: Can adjust speed and position flexibly according to processing requirements, enhancing production efficiency.
Desvantagens:
- High Cost: The manufacturing and maintenance costs of servo motors are higher, requiring a larger initial investment.
- Complex Maintenance: Their complex structure demands higher technical and maintenance skills.
- Environment Sensitivity: Servo motors require stringent environmental conditions, such as temperature and humidity, necessitating a good working environment.
In summary, conventional motors are suitable for applications with limited budgets and low precision requirements, while servo motors are ideal for high-end applications requiring high precision, efficiency, and flexible control. The choice of motor should be balanced based on specific processing needs and budget constraints.
Mechanical Crowning Compensation in Hydraulic Press Brake
Mechanical crowning compensation is a method used in hydraulic press brakes to correct deformation and errors caused by uneven forces during the bending process. It ensures that the workpieces have consistent angles and shapes by adjusting the mechanical structure.
Princípio de funcionamento
Mechanical crowning compensation systems usually consist of a set of adjustable wedge blocks or wedge mechanisms. These wedges move relative to each other to adjust the shape of the worktable, compensating for machine deformation caused by bending forces. By adjusting the position of the wedges, a counter-deformation force is applied during bending to offset the errors generated during actual operations.
Mechanical crowning compensation is typically divided into manual and automatic types, each with its own advantages and disadvantages, suitable for different applications.
Manual Mechanical Crowning Compensation
Princípio de funcionamento: Manual mechanical crowning compensation adjusts the shape of the worktable by manually adjusting wedges or other mechanical components to compensate for deformation during the bending process. Operators manually rotate adjustment mechanisms based on processing needs and experience, moving the wedges to the appropriate positions for compensation.
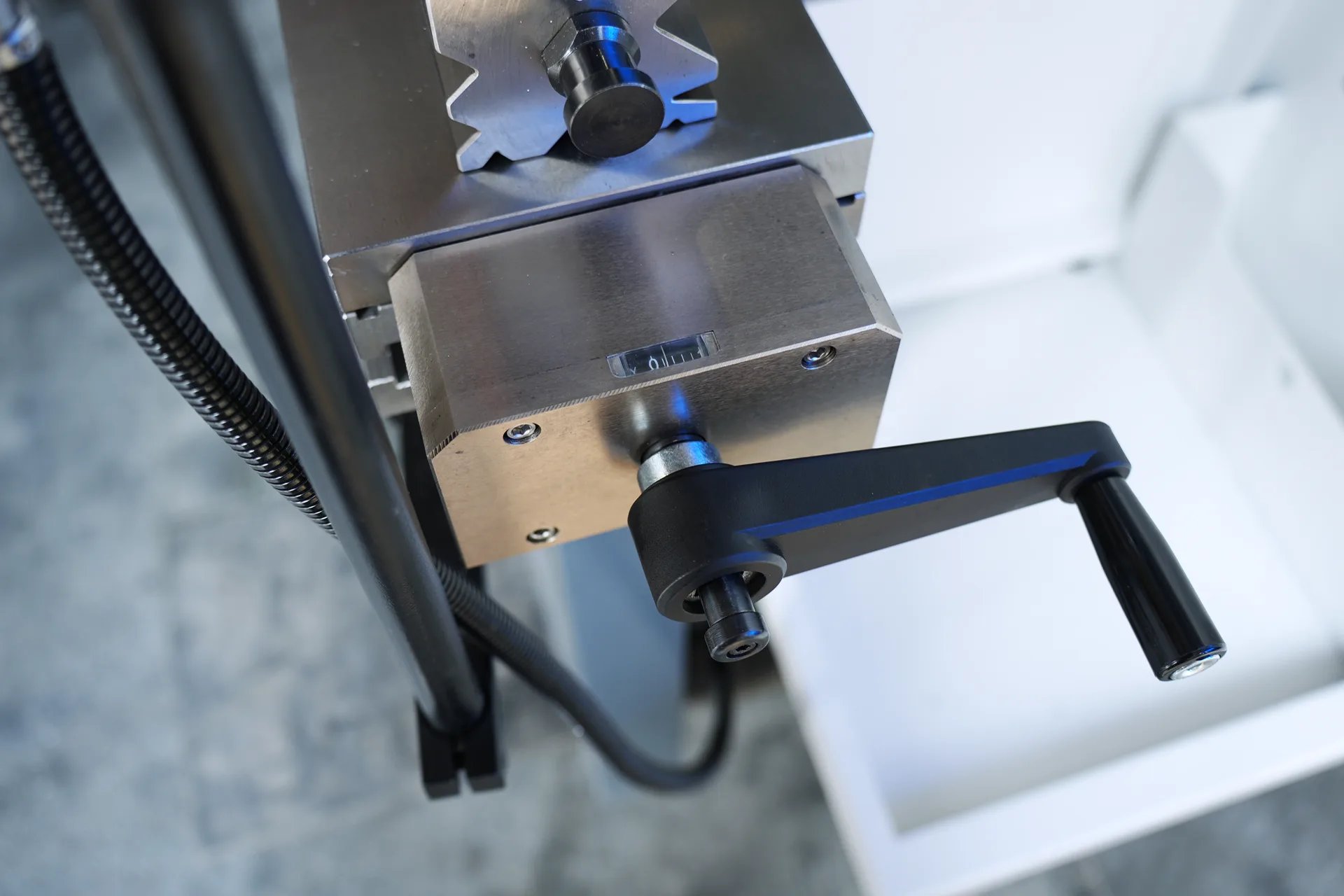
Vantagens:
- Low Cost: Manual adjustment devices are simple, with lower manufacturing and maintenance costs.
- Fácil operação: The structure is relatively simple, easy to understand and operate, suitable for beginners and small businesses.
Desvantagens:
- Low Adjustment Precision: Manual adjustment relies on the operator's experience and skills, resulting in lower precision, which is challenging for high-precision requirements.
- Low Efficiency: The manual adjustment process is time-consuming, affecting production efficiency, especially when frequent adjustments are needed.
- Poor Adaptability: Unsuitable for scenarios requiring quick workpiece changes and process parameter adjustments.
Suitable Scenarios:
- Small Batch Production: Suitable for small-scale production without frequent adjustments.
- Low Precision Requirements: Ideal for bending tasks with low precision demands.
- Limited Budget: Suitable for small businesses with budget constraints.
Automatic Mechanical Crowning Compensation
Princípio de funcionamento: Automatic mechanical crowning compensation uses CNC systems or other automatic control devices to monitor and adjust the position of wedges in real-time. After inputting the required compensation parameters, the system automatically controls the adjustment mechanism to ensure bending precision.
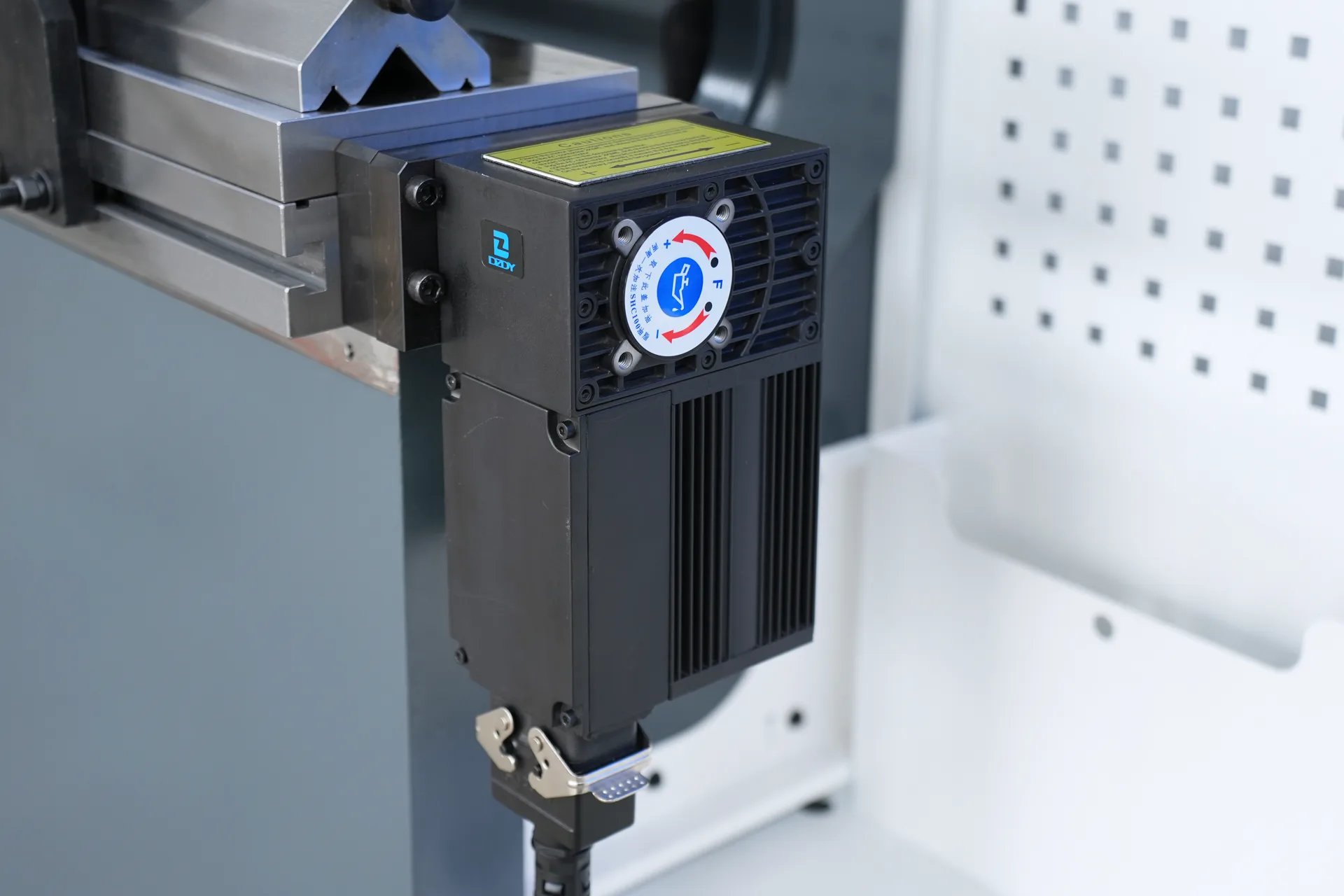
Vantagens:
- Alta precisão: The automatic control system can achieve high-precision compensation, meeting high-precision processing needs.
- Alta eficiência: The automatic adjustment process is fast and stable, enhancing production efficiency, suitable for mass production.
- Good Consistency: The automatic system provides stable and consistent compensation effects, reducing human error.
Desvantagens:
- High Cost: The automatic compensation system is complex, with higher manufacturing and maintenance costs.
- High Technical Requirements: Requires professional operators and maintenance personnel, increasing training and management costs.
Suitable Scenarios:
- Mass Production: Suitable for large-scale production requiring frequent adjustments.
- Requisitos de alta precisão: Ideal for bending tasks with high precision demands.
- High Automation Needs: Suitable for highly automated and efficient production environments.
Recommendations for Selecting Mechanical Crowning Compensation
When choosing between manual or automatic mechanical crowning compensation, consider the specific production needs, budget, and technical conditions comprehensively. For small-batch, low-precision production tasks, manual mechanical crowning compensation is an economical and practical choice. For mass production, high precision, and high efficiency demands, automatic mechanical crowning compensation offers better performance and production outcomes.
Multi-Axis Backgauge System in Press Brakes
A multi-axis backgauge system is an advanced component in electro-hydraulic press brakes used for precise positioning and supporting workpieces. Compared to single or dual-axis backgauge systems in torsion bar press brakes, multi-axis backgauge systems offer greater flexibility and precision, meeting the demands of complex and diversified processing.
Princípio de funcionamento
A multi-axis backgauge system typically consists of multiple independently controlled axes driven by CNC systems through servo motors or stepper motors, achieving high-precision movement and positioning. Each axis can independently adjust its position based on preset programs to accommodate different shapes, sizes of workpieces, and complex bending processes.
Componentes principais
- Servo Motor or Stepper Motor: Drives the movement of each axis, providing high-precision positioning control.
- Linear Guides and Ball Screws: Ensure smooth movement and high repeat positioning accuracy.
- CNC System: Coordinates the entire system, executing preset bending programs and position adjustments.
- Sensors and Feedback System: Monitor the position of each axis in real-time, providing feedback to correct deviations, ensuring precision.
Características
- Alta precisão: Multi-axis control achieves high-precision positioning and adjustment, suitable for complex bending processes.
- Strong Flexibility: Each axis can be independently controlled, quickly adapting to different workpieces and multi-step bending needs.
- High Degree of Automation: Linked with CNC systems, enabling highly automated operations, reducing human intervention.
- Alta eficiência: Automatic adjustment and fast positioning significantly improve production efficiency, suitable for mass production.
- Good Consistency: Precise control and feedback systems ensure consistent and high-quality processing results.
Classificação
Multi-axis backgauge systems can be classified into the following categories based on their design and functionality, each suitable for different application scenarios and processing needs:
- X-axis (Front-Back): Controls the front-back movement of the backgauge plate, determining the depth position of the workpiece.
- Características: Basic function, widely used.
- Suitable Scenarios: All types of press brakes.
- R-axis (Up-Down): Controls the up-down movement of the backgauge plate, suitable for multi-step bending or different height positioning.
- Características: Height adjustment, adaptable to different thicknesses and shapes of workpieces.
- Suitable Scenarios: Complex processes and multi-step bending.
- Z1/Z2 Axes (Left-Right Independent): Controls the independent left-right movement of the backgauge plates, allowing for more complex positioning and support.
- Características: Independent control, suitable for asymmetrical workpieces and special bending needs.
- Suitable Scenarios: Complex positioning and special bending requirements.
- X1/X2 Axes (Front-Back Independent): Controls the independent front-back movement of the left and right backgauge plates, used for high-precision and complex bending processes.
- Características: Independent front-back movement, providing higher processing precision and flexibility.
- Suitable Scenarios: High-precision processing and complex bending processes.
- R1/R2 Axes (Up-Down Independent): Controls the independent up-down movement of the left and right backgauge plates, suitable for different height positioning and complex bending processes.
- Características: Independent up-down movement, suitable for complex processes and multi-step bending.
- Suitable Scenarios: Multi-step bending and complex processes.
- Crowning Compensation Axis (W Axis): Most press brakes may be equipped with other axes, such as the crowning compensation axis, for higher precision and processing needs.
- Características: Customizable, suitable for special process requirements.
- Suitable Scenarios: High-end manufacturing and complex process scenarios.
Comparison of Types
Axis Type | Função | Características | Suitable Scenarios |
---|---|---|---|
X-axis (Front-Back) | Controls front-back position | Basic function, widely used | All types of press brakes |
R-axis (Up-Down) | Controls height position | Height adjustment, adaptable | Complex processes, multi-step bending |
Z1/Z2 Axes (Left-Right Independent) | Independent left-right position | Independent control, adaptable | Complex positioning, special bending |
X1/X2 Axes (Front-Back Independent) | Independent front-back position | High precision, independent movement | High-precision, complex bending |
R1/R2 Axes (Up-Down Independent) | Independent up-down position | High precision, independent movement | Multi-step bending, complex processes |
Crowning Compensation Axis (W Axis) | Higher precision needs | Customizable, advanced applications | High-end manufacturing, complex processes |
Selection Recommendations
Based on the above combinations and the main Y1 and Y2 axes of the press brake, multi-axis backgauge systems usually have the following combination types:
- 3+1 Axis (Y1+Y2+X+W)
- 4+1 Axis (Y1+Y2+X+R+W)
- 5+1 Axis (Y1+Y2+X1+X2+R+W)
- 6+1 Axis (Y1+Y2+X+Z1+Z2+R+W)
- 8+1 Axis (Y1+Y2+X1+X2+Z1+Z2+R1+R2+W)
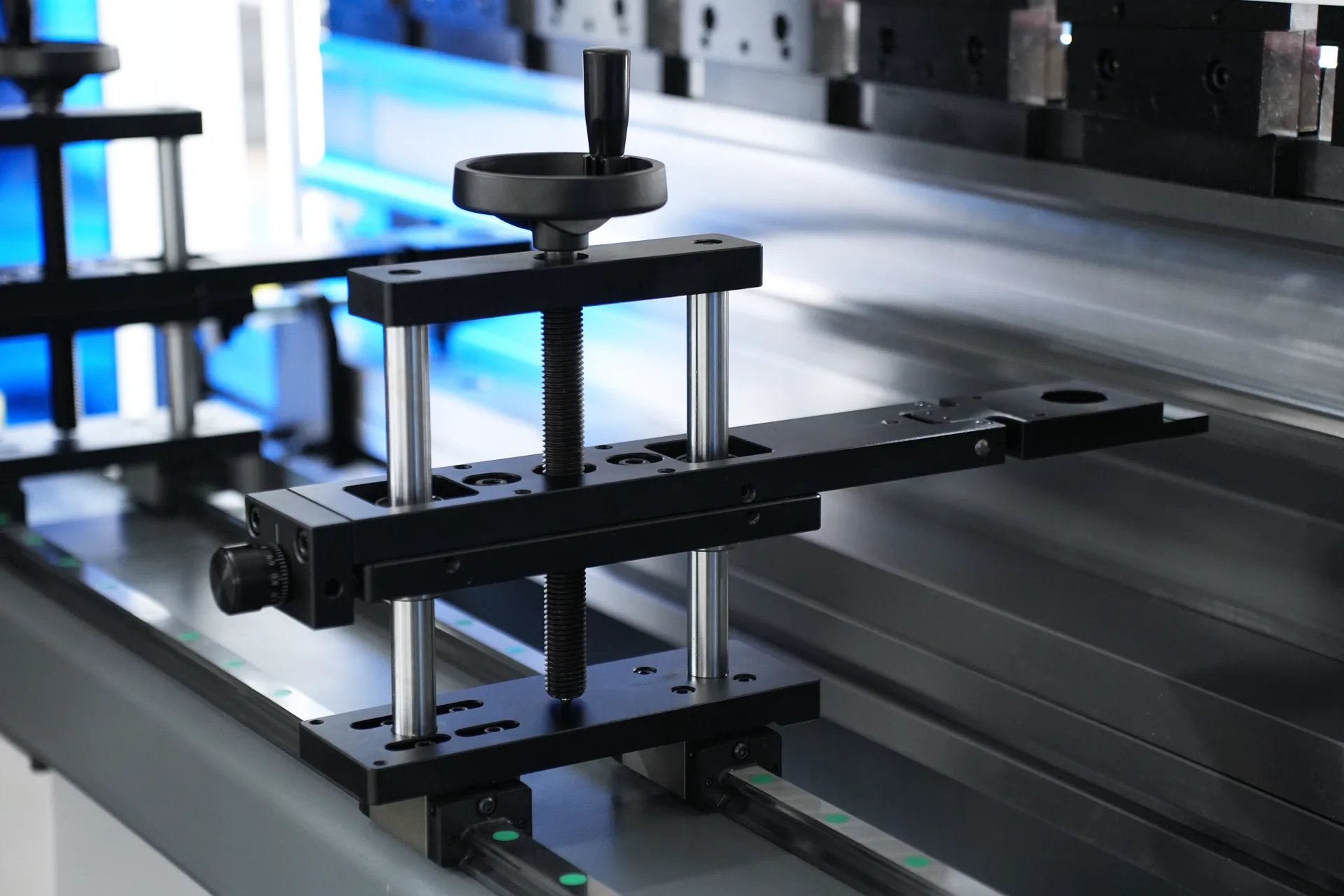
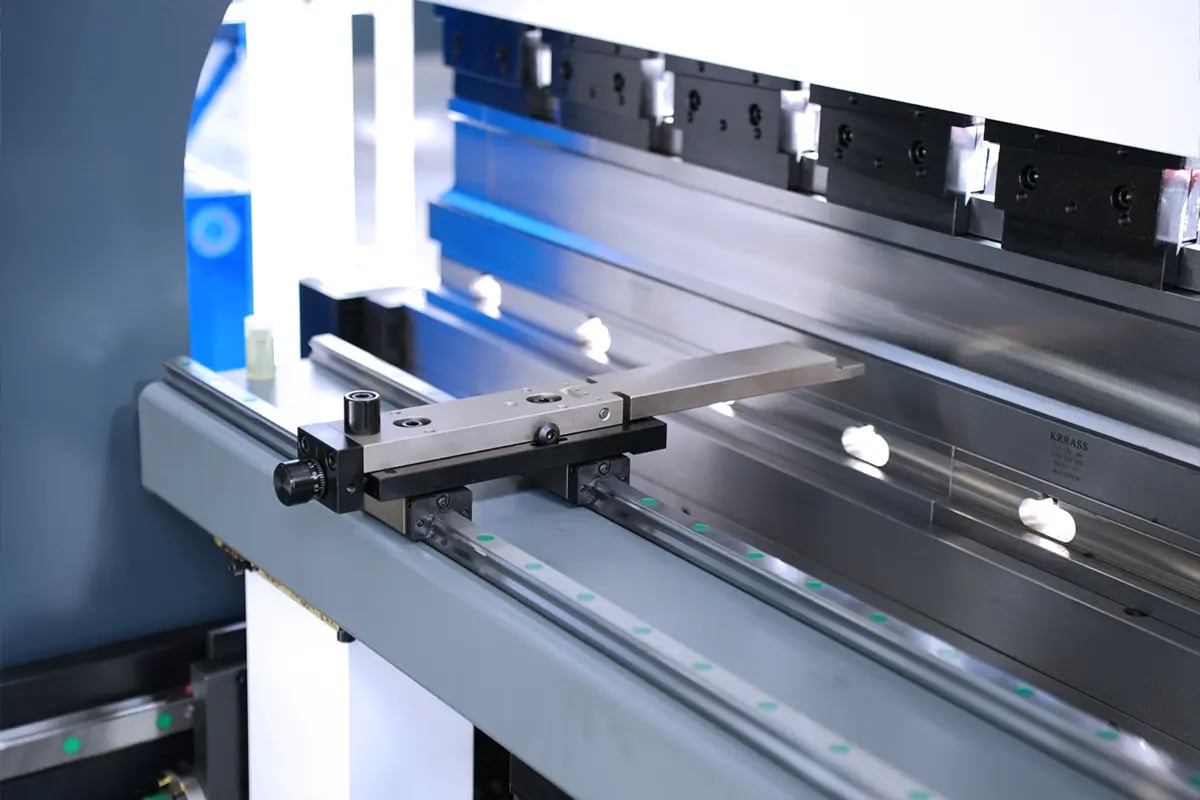
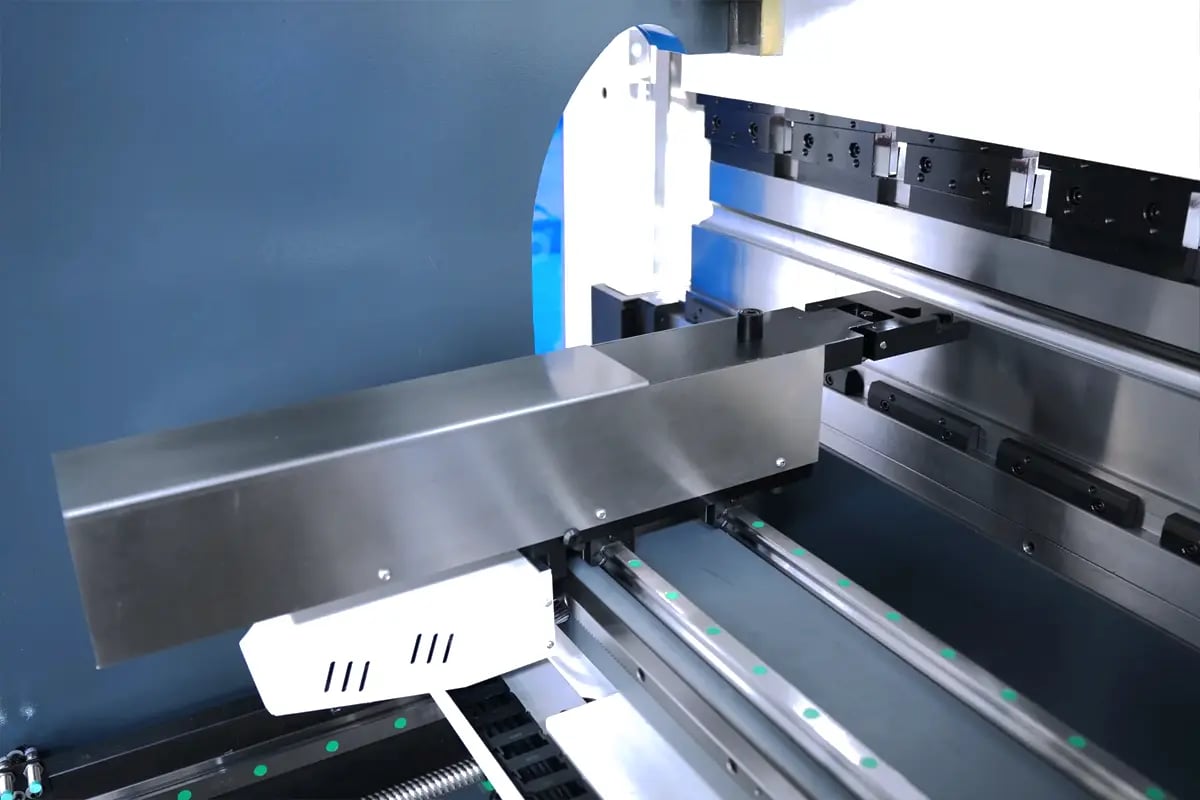
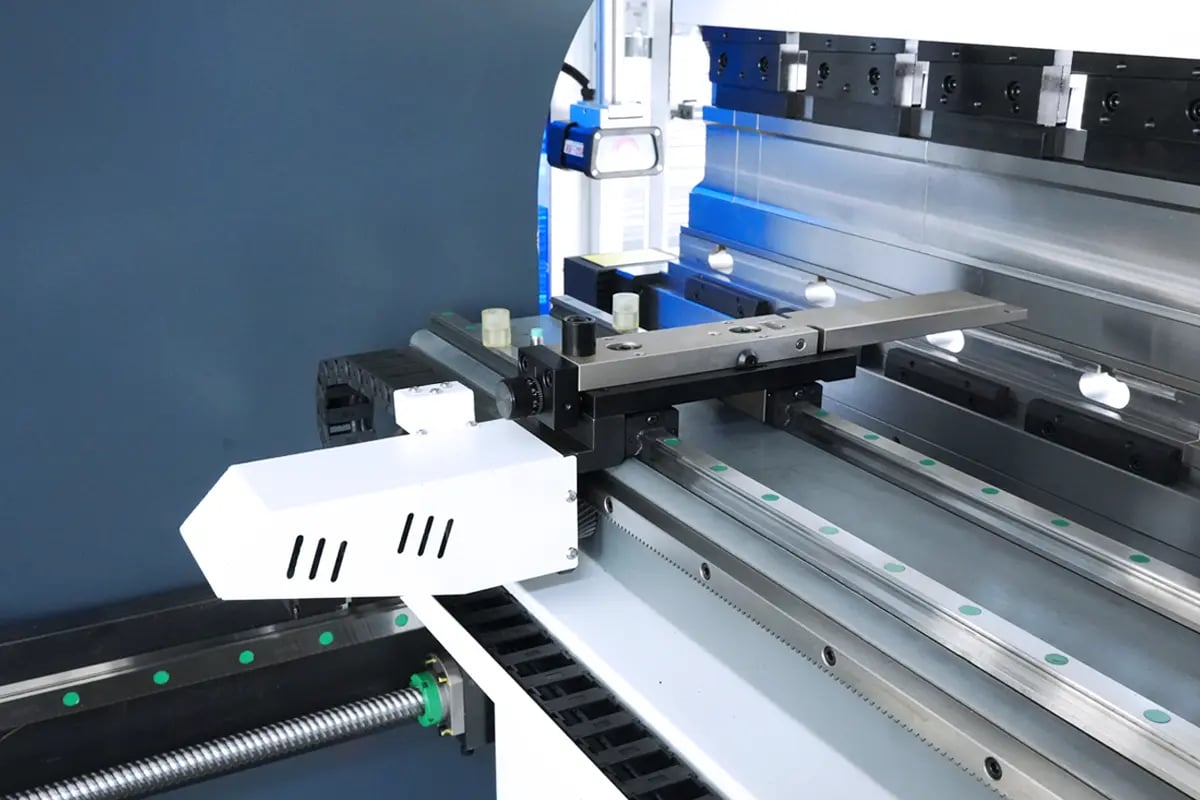
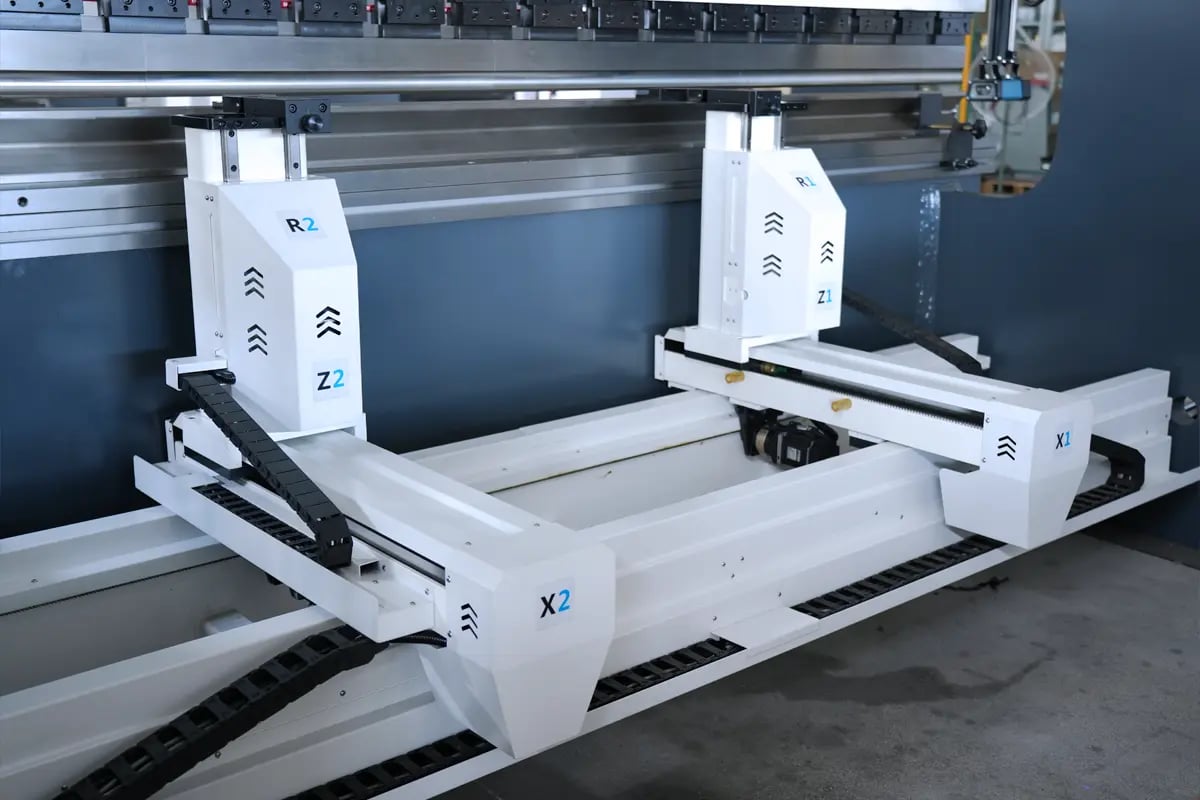
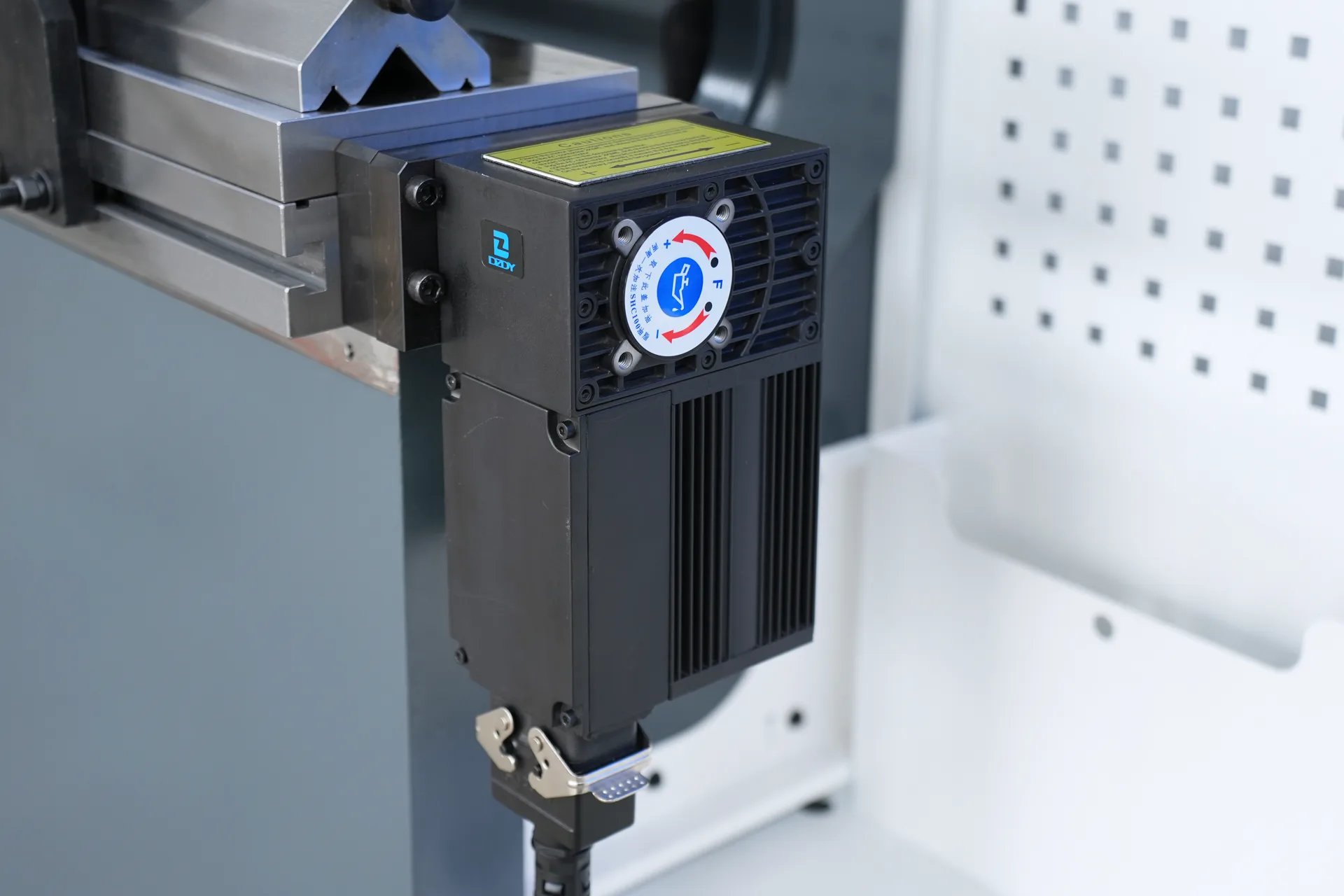
When selecting a multi-axis backgauge system, consider the specific production needs and processing techniques:
- Basic Needs: For regular processing, the X-axis and R-axis are sufficient.
- Requisitos de alta precisão: For high-precision and complex processing, the X1/X2 axes, Z1/Z2 axes, and R1/R2 axes provide more flexibility and precision.
- Special Processes: For special process needs, consider adding other special axes to meet specific positioning and support requirements.
By reasonably selecting and configuring the multi-axis backgauge system, the processing capability and production efficiency of the press brake can be significantly improved, meeting the high standards of modern manufacturing in terms of precision, efficiency, and flexibility.
Hydraulic Press Brake Molds
The molds of a press brake are crucial components for determining the shape and angle of the workpieces being bent. They typically consist of an upper die and a lower die, with the upper die fixed to the top of the press brake and the lower die fixed to the workbench. During the bending process, the upper die exerts pressure on the lower die, causing the workpiece to undergo plastic deformation between the molds, thus completing the bending operation.
Types of Molds
A complete set of press brake molds includes both the upper and lower dies, each available in various types based on their shapes and purposes:
- Standard Upper Die:
- Usage: Suitable for general bending needs, with a simple shape and high versatility.
- Knife-shaped Upper Die:
- Usage: Used for sharp-angle bending, capable of achieving acute bending angles.
- Gooseneck Upper Die:
- Usage: Features a curved edge, suitable for bending deeper workpieces.
- Matriz V Única:
- Usage: Has a single V-shaped groove, suitable for general V-shaped bending needs.
- Double V Concentric Die:
- Usage: Features two concentric V-shaped grooves, suitable for workpieces requiring two different bending angles.
- Four V Concentric Die:
- Usage: Features four concentric V-shaped grooves, suitable for multi-angle bending needs.
- Multi V Die:
- Usage: Has multiple V-shaped grooves, allowing flexible selection based on the shape and size of the workpiece.
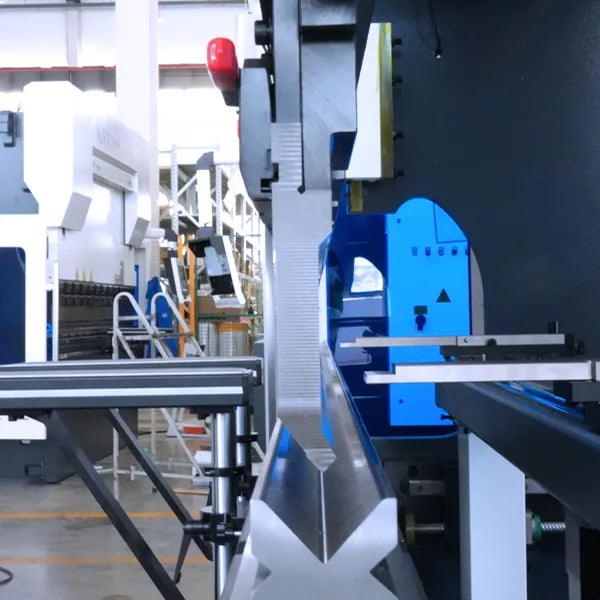
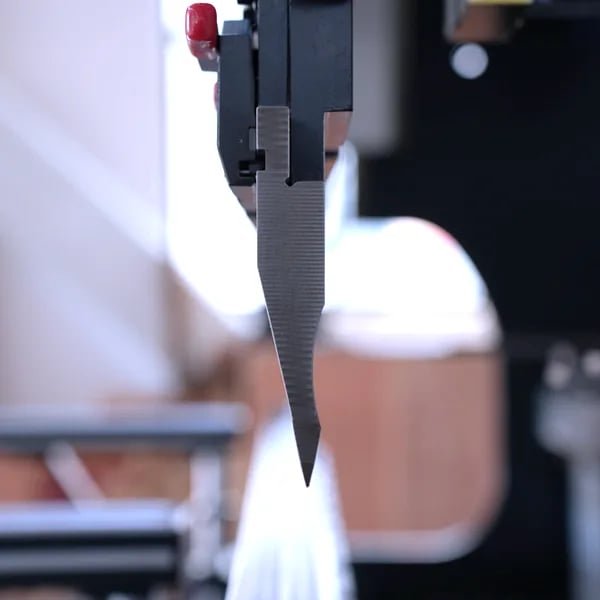
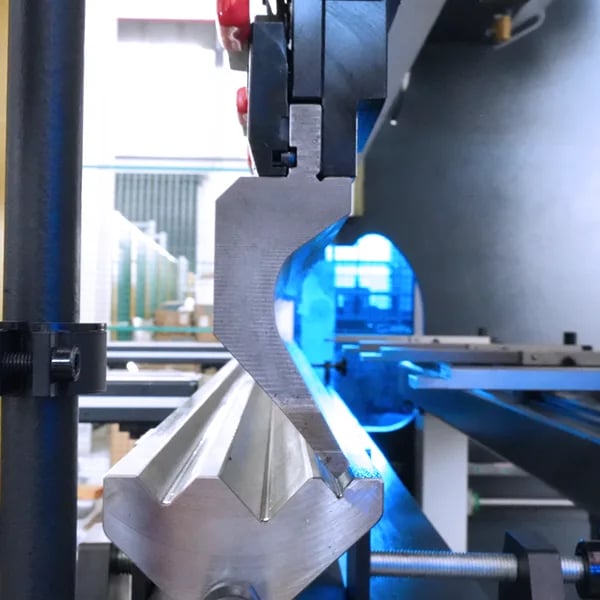
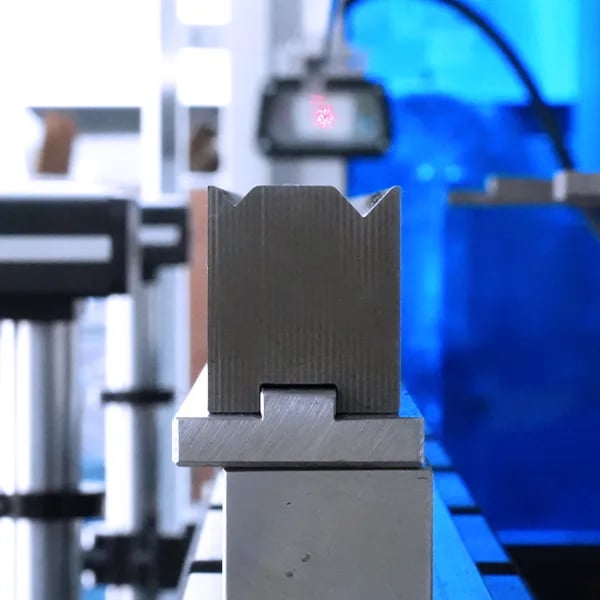
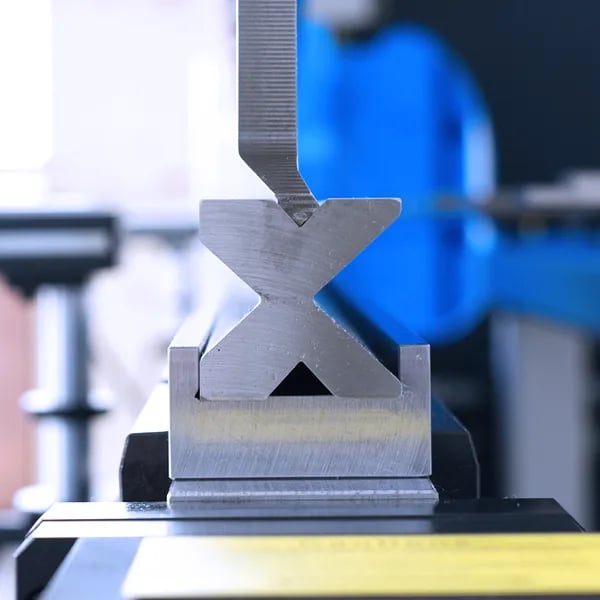
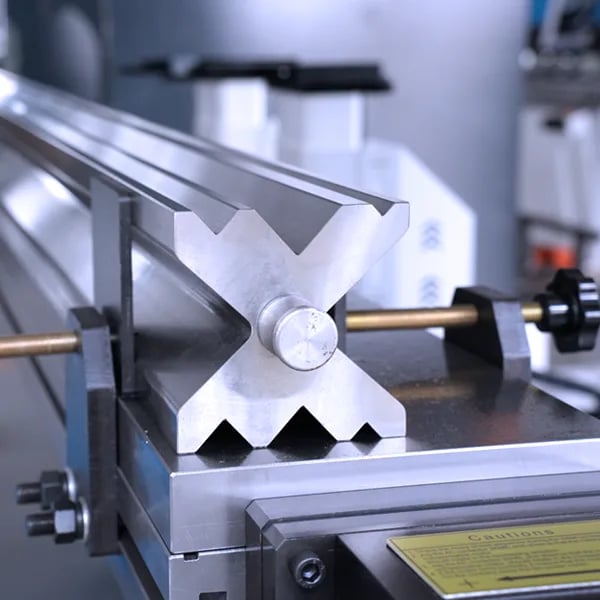
Mold Selection
When selecting press brake molds, the following factors should be considered comprehensively:
- Material of the Workpiece: Different materials have varying requirements for the mold's material and hardness.
- Thickness of the Workpiece: The thickness determines the V-groove width of the mold and the curvature radius of the R-type mold.
- Ângulo de curvatura e raio: The bending angle and radius determine the shape and size of the mold.
- Requisitos de precisão: The higher the precision requirement, the higher the accuracy needed for the mold.
- Orçamento: The price of molds depends on factors such as material, precision, and complexity.
Press brake molds are essential for achieving desired bending operations. Proper selection and use of molds can improve processing efficiency and product quality, meeting various processing needs.
Safety Protection Systems of the Press Brake
As a large metal processing machine, the hydraulic press brake poses significant operational risks. Therefore, it is equipped with multiple safety protection systems to ensure the safety of operators and equipment. Common safety protection systems in hydraulic press brakes include:
- Light Curtain: Consists of a pair of transmitters and receivers installed around the work area. When an operator enters the work area, the light beam is interrupted, and the machine automatically stops running to prevent accidental contact with dangerous areas.
- Two-Hand Control: Requires the operator to press buttons with both hands simultaneously to start the press brake. This system prevents accidental injuries caused by misoperation or single-hand operation.
- Safety Door Switch: Installed on the press brake's door. When the door is opened, the system automatically stops running to prevent operators from entering the dangerous area during operation.
- Botão de parada de emergência: Usually located on the control panel. In an emergency, the operator can press the button to immediately stop the machine, preventing accidents.
- Guards and Barriers: Installed at key parts of the machine, such as the tool area and hydraulic system, to prevent accidental contact with dangerous components.
- Overload Protection System: Monitors the pressure and load of the hydraulic system. If it detects pressure or load exceeding the set range, the system automatically stops running to prevent damage from overloading.
- Laser Protection System (e.g., DSP and MSD): Uses laser beams to monitor the operational area. When an operator enters the danger zone, it immediately stops the machine to ensure safety.
- Safety Signs and Labels: Installed around the press brake and on the control panel, providing warnings and operational guidelines to remind operators of safety precautions.
These safety protection systems collectively form a comprehensive safety framework for hydraulic press brakes, effectively reducing operational risks and protecting the safety of operators and the integrity of the equipment. Operators should strictly follow relevant safety regulations and procedures, using the safety protection systems correctly to ensure safe production.
Enhanced Functions of Hydraulic Press Brakes
In addition to standard configurations, hydraulic press brakes often offer various optional features to meet the specific needs of different customers. Common optional features and their characteristics include:
- Automatic Tool Adjustment: Allows the machine to automatically adjust the gap between the upper and lower dies to accommodate different material thicknesses, improving production efficiency and operational convenience.
- Sistema de armazenamento de ferramentas WILA: An efficient tool management solution, especially suitable for hydraulic press brakes. This optional feature allows operators to effectively organize, store, and manage the tools used by the press brake, enhancing production efficiency and workflow smoothness.
- Angle Sensor: Installed on the upper die of the machine, used for precise measurement of the bending angle to ensure the accuracy and consistency of each bend.
- Automatic Feeding Device: Can automatically feed workpieces into the machine for bending, improving production efficiency and reducing manual operations.
- CNC Front Support for Back Gauge: Another important optional feature for hydraulic press brakes, typically used to support and stabilize the front end of the workpiece, ensuring accuracy and stability during the bending process.
- Tandem Press Brake System: Connects two hydraulic press brakes together for synchronized control, enabling simultaneous bending of workpieces, thus improving production efficiency. This system is typically used for processing large workpieces and can perform symmetrical or asymmetrical bending operations.
- Flexible Bending Unit: A modular design that allows the addition of extra working units or devices on the hydraulic press brake for specific shapes, complex curves, or special workpieces. This unit can be customized according to actual needs, enhancing the machine's flexibility and applicability.
These optional features can be selected and customized based on the specific needs of customers, enhancing the processing efficiency, quality, and operational convenience of freios de prensa hidráulica.
Conclusão
Hydraulic press brakes are essential equipment in sheet metal processing, with diverse types and functions. Choosing the right model depends on specific processing needs and production conditions. Hydraulic torsion bar press brakes are suitable for high-volume, low-precision production, while hydraulic electro-hydraulic press brakes are ideal for high-precision, complex processing. The controller, drive method, bending compensation, and tooling all significantly impact the performance and application range of hydraulic press brakes. Therefore, when purchasing a hydraulic press brake, these factors should be comprehensively considered to ensure the selection of the most suitable equipment, thereby improving production efficiency and processing quality.