Uma chapa metálica freio de caixa e panela tem muitos pseudônimos, alguns dos quais você já deve conhecer. São termos usados por muitos ainda hoje na indústria, mas podem ser novos para alguns de nós. Vamos analisar alguns desses termos de box pan folder, bem como o que uma caixa de chapa metálica e uma pan folder realmente são e por que sua empresa pode se beneficiar ao investir em uma.
Também destacamos algumas áreas comuns que devem ser observadas quando se trata de convidar convidados em uma caixa e uma pasta de chapa metálica.
O que é uma caixa de chapa metálica e freio de panela?
Uma chapa metálica freio de caixa e panela, também conhecido mais frequentemente como box and pan brake, box pan folder ou sheet metal finger brake, é uma máquina-ferramenta usada para dobrar chapas metálicas. Ela é projetada para permitir que chapas metálicas sejam dobradas em caixas e panelas, assim como outras formas complexas.
Essas máquinas de dobrar bandejas de caixa normalmente consistem em uma superfície plana, chamada de cama, e uma barra de fixação que é articulada em uma extremidade. A barra de fixação segura a chapa metálica no lugar enquanto ela está sendo dobrada, enquanto uma série de dedos, ou matrizes, são usados para moldar o metal.
Muitas inovações em dobra e encurvamento significam que novos sistemas de dobradeira de bandeja de caixa estão sendo lançados constantemente, o que melhora a eficiência e a qualidade dessas dobras. É por esse motivo que aconselhamos manter-se atualizado sobre as últimas notícias dos principais fabricantes do setor. Eles podem simplesmente apresentar uma solução que resolva um problema específico para você!
Algumas dobradeiras de caixa e panela também têm um batente que pode ser ajustado para ajudar a garantir dobras precisas e consistentes. Essas máquinas são comumente usadas na fabricação de gabinetes de chapa metálica, gabinetes e outros componentes.
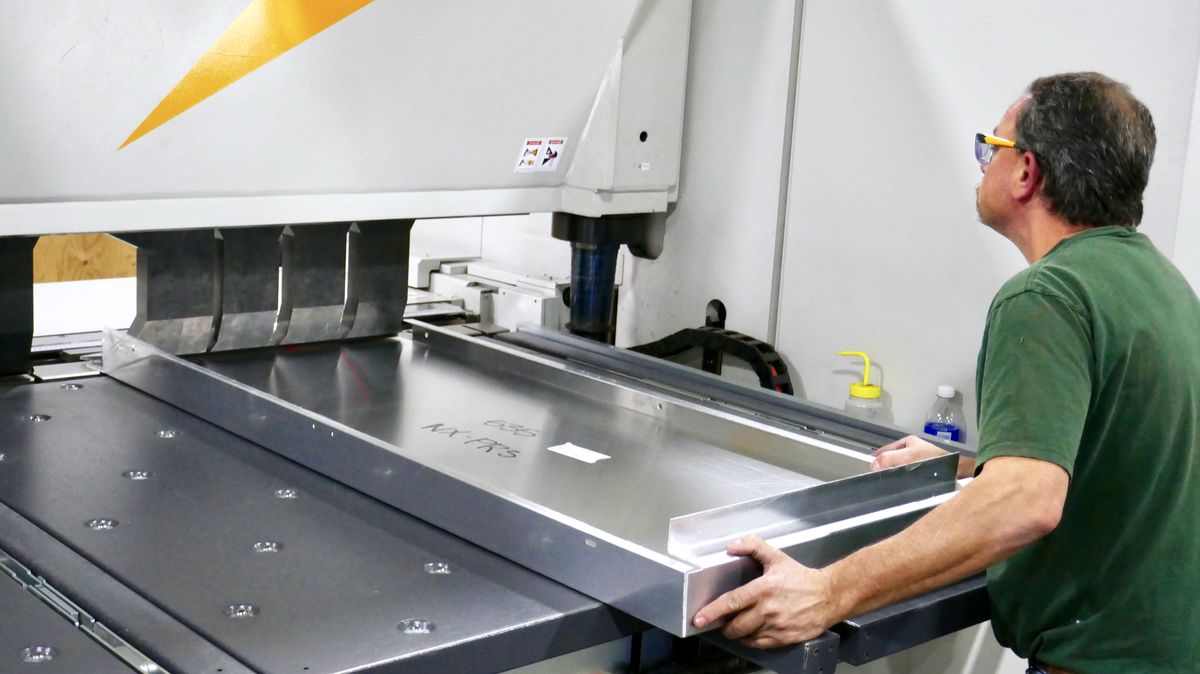
Por que um freio de caixa e bandeja é conhecido por outros nomes?
O nome que você dá à sua máquina de dobrar chapas metálicas pode depender do tipo que você possui, de quem o treinou e de como você a usa. Muitas das diferenças surgiram ao longo do tempo. Por exemplo, caixa e panela eram frequentemente a descrição usada ao falar sobre os modelos anteriores do tipo de dobradeira de chapas metálicas do Sistema RAS.
Nós dividimos abaixo os motivos comuns por trás de alguns dos nomes mais populares. Em geral, eles são bem literais. Você está usando o nome certo?
Freio de caixa e bandeja
É chamado de box and pan brake porque é usado para dobrar chapas de metal em caixas e panelas, assim como outros formatos. Essa lógica segue para muitos dos nomes, às vezes adicionando o material usado no começo ou no fim.
Freio de dedo de chapa metálica (ou freio de dedo)
Este nome surgiu porque as máquinas de dobrar chapas metálicas têm uma série de dedos, ou matrizes, que são usados para moldar o metal. Esses dedos são normalmente montados na barra de fixação e podem ser ajustados para criar diferentes dobras e formatos na chapa metálica. Vale a pena saber que o termo “freio de dedo de chapa metálica” é frequentemente usado para descrever uma versão menor e portátil desta máquina que é usada para fazer dobras e dobras menores em chapas metálicas. Pode ser que pesquisar isso não traga os resultados certos para você.
A que se refere a parte “Caixa e Panela”?
Vamos dar um passo adiante e analisar os tipos específicos de formatos aos quais nos referimos quando nos referimos a uma caixa e uma pasta de chapa metálica.
O termo “caixa” se refere a um invólucro tridimensional com uma parte superior, inferior e laterais que é feito de chapa metálica. Uma “panela” é um tipo similar de invólucro, mas tem uma profundidade mais rasa e é frequentemente usada para coisas como bandejas.
É realmente tão óbvio quanto parece, mas devido à variedade de termos usados na indústria, pode deixar algumas pessoas inseguras. A parte importante é garantir que, não importa como você chame, você invista em uma máquina que seja capaz para o seu negócio. Como você faz isso?
Por que você deve investir em uma caixa de chapa metálica e uma dobradeira para panelas?
Há vários motivos pelos quais você pode querer investir em uma caixa de chapa metálica e uma dobradeira para panelas:
- Aumento da produtividade: Uma caixa de chapa metálica e uma dobradeira de panela podem ajudar a aumentar a produtividade, permitindo que você dobre chapas metálicas de forma rápida e precisa em formas complexas. Isso pode economizar tempo e esforço em comparação ao uso de outros métodos, como dobra manual ou corte e soldagem.
- Precisão melhorada: Uma caixa de chapa metálica e uma dobradeira de panela podem ajudar a melhorar a precisão das suas dobras de chapa metálica. Isso ocorre porque a máquina permite que você faça dobras precisas e repetíveis usando uma série de dedos ou matrizes ajustáveis.
- Maior versatilidade: Uma caixa de chapa metálica e uma dobradeira de panela são ferramentas versáteis que podem ser usadas para dobrar chapas metálicas em uma ampla variedade de formas e tamanhos. Isso pode permitir que você crie uma variedade maior de produtos e componentes.
- Economia de custos: Investir em uma caixa de chapa metálica e em uma dobradeira pode economizar dinheiro, reduzindo a quantidade de tempo e esforço necessários para dobrar chapas metálicas, além de reduzir a quantidade de sucata gerada.
No geral, uma caixa de chapa metálica e uma dobradeira podem ser um investimento valioso para qualquer empresa que trabalhe com chapas metálicas e precise criar formas e compartimentos complexos.
Qual é a diferença entre freio panorâmico e freio de prensa?
O que considerar ao comprar uma caixa de chapa metálica e freio de panela
É importante que você tome uma decisão bem pensada antes de escolher sua nova caixa e pasta de panelas. Destacamos algumas áreas-chave a serem consideradas abaixo:
- Custo: Caixas de chapa metálica e dobradeiras de panela podem ser caras, especialmente para modelos de ponta com recursos avançados. Certifique-se de que você está fazendo o melhor negócio e pagando apenas pelos recursos que sua empresa precisa. Você também pode procurar máquinas pré-usadas e ex-demonstração para economizar mais. Oferecemos uma grande variedade de freios de chapa metálica de caixa e panela para atender a todos os orçamentos.
- Capacidade: Algumas caixas de chapas metálicas e dobradeiras de panelas têm capacidade limitada e podem não ser capazes de dobrar chapas maiores de metal ou manusear calibres mais grossos. Certifique-se de que a máquina em que você investe atende às suas necessidades. Também ajuda pensar sobre como suas capacidades futuras podem parecer para garantir que você não tenha que recusar empregos em potencial.
- Complexidade: Essas máquinas podem ser complexas e exigem treinamento e experiência para uso eficaz. Certifique-se de estar confiante na caixa e na dobradeira de chapas de metal que você possui, como ela funciona e o que fazer se der errado. A Press and Shear permanece à disposição para ajudar desde a instalação até a sua primeira dobra.
- Manutenção: Como qualquer máquina, uma caixa de chapa metálica e uma dobradeira de panela exigirão manutenção regular e podem precisar ser reparadas ou substituídas ao longo do tempo. A manutenção regular aumentará a produtividade e o ciclo de vida da sua máquina, essencialmente pagando por si mesma. A Press and Shear está à disposição para ajudar com todos os serviços e peças de reposição.
Você está usando o nome correto para freio de caixa e freio de bandeja?
Não importa se você está na fase de pesquisa, pronto para adquirir uma nova máquina de dobrar ou treinando sua equipe sobre como usar uma máquina, é fundamental escolher o nome certo para sua dobradeira de chapas metálicas tipo caixa e panela e conhecer as diferenças.
Isso ajudará você a fazer o investimento certo em uma máquina capaz e garantir que sua equipe seja capaz de explicar claramente aos clientes as capacidades do seu negócio.
Como testar uma pasta de caixa e panela
Estamos aqui para ajudar você, seja para obter alguns materiais de leitura ou para colocar a mão na massa com uma dobradeira de chapas de metal para caixas e panelas. Você pode baixar nosso folheto mais recente, que contém uma gama completa de máquinas de dobra de caixas e panelas agora mesmo. Você também pode navegar por eles on-line, onde encontrará muitos vídeos dessas máquinas em ação.
Às vezes, a coisa mais fácil de fazer é colocar a mão na massa, e é aí que entra nosso showroom. Você pode agendar uma visita para ver um freio de caixa de chapa metálica em ação e até mesmo trazer suas próprias peças de chapa metálica para testar. Achamos que essa é a melhor maneira de saber que você está fazendo o investimento certo e aproveitar ao máximo sua viagem para nos visitar.
Qual é a diferença entre Pan Brake e Press Brake?
Na fabricação de metal, dobrar chapas de metal em vários formatos e estruturas é essencial. Esse processo normalmente envolve o uso de máquinas como prensas dobradeiras e freios de panela. Cada máquina tem vantagens distintas, tornando crucial para os fabricantes entenderem suas diferenças para fazer escolhas informadas com base em requisitos específicos. As prensas dobradeiras, também conhecidas como prensas de freio, são o tipo mais comum usado na indústria de metal. Elas são capazes de lidar com metais mais espessos e componentes mais complexos do que outros freios de chapa metálica. Com conjuntos mecânicos e hidráulicos, as prensas dobradeiras são ferramentas versáteis adequadas para uma ampla gama de projetos de fabricação de metal.
Por outro lado, um freio de panela, também chamado de freio de caixa e panela ou freio de dedo, é projetado para criar curvas ao longo da borda de uma chapa de metal. É particularmente útil para formar caixas, bandejas e panelas planas, oferecendo curvatura precisa para aplicações específicas. Este artigo tem como objetivo comparar as características e aplicações de freios de prensa e freios de panela, ajudando os leitores a entender melhor suas funções e vantagens na indústria de fabricação de metal. Por meio dessa comparação, os leitores aprenderão quando escolher freios de prensa, quando optar por freios de panela e como cada máquina atende a várias necessidades industriais.
Compreendendo as prensas dobradeiras
Definição e mecânica básica de prensas dobradeiras
Uma prensa dobradeira é uma máquina usada para dobrar ou formar chapas de metal nos ângulos e formas necessárias usando um punção e uma matriz. O processo envolve colocar a chapa de metal entre o punção e a matriz, onde o punção da prensa dobradeira aplica força para obter a dobra desejada. As prensas dobradeiras podem ser operadas manualmente, hidraulicamente ou por outras fontes de energia, com sua operação determinada precisamente pelo tipo de prensa dobradeira usada.
Tipos de dobradeiras de pressão
As prensas dobradeiras são categorizadas com base em seus mecanismos de acionamento:
- Prensa Dobradeira Hidráulica: Este tipo usa um cilindro hidráulico para controlar o movimento do carneiro, oferecendo potência forte, velocidade controlável e boa estabilidade. Seus principais componentes incluem um cilindro hidráulico, carneiro, grampo, matriz e punção.
- Prensa dobradeira mecânica: Este tipo emprega um volante mecânico para gerar força para dobrar chapas de metal, conhecido por sua alta velocidade e adequação para produção em massa. Seus principais componentes incluem um volante, um aríete, uma braçadeira, uma matriz e um punção.
- Servoprensa dobradeira: Acionado por um servo motor, esse tipo fornece controle mais preciso e menor consumo de energia. Suas partes primárias são o motor, o aríete, a braçadeira, a matriz e o punção.
Usos comuns e principais características
As prensas dobradeiras apresentam um calibre traseiro ajustável para posicionamento preciso, controles programáveis para sequências de dobra automáticas e funções de segurança para proteger os operadores durante o processo de dobra. Elas são caracterizadas por controle de alta precisão, forte adaptabilidade a várias espessuras e tipos de chapas metálicas e capacidades avançadas de automação.
Vantagens na Metalurgia
As prensas dobradeiras oferecem inúmeras vantagens na metalurgia:
- Alta precisão: Eles utilizam sistemas de controle avançados para gerenciar com precisão o processo de dobra, garantindo resultados precisos e repetíveis.
- Forte Adaptabilidade:Eles podem lidar com diferentes tipos e espessuras de materiais metálicos.
- Alta Eficiência:Eles aumentam significativamente a eficiência da produção, especialmente em ambientes de produção em massa.
- Personalização: As prensas dobradeiras podem criar curvas e formas personalizadas por meio de controles programáveis e opções de ferramentas para atender a requisitos específicos de design.
Explorando freios de panela
Definição e funções primárias
Freios de panela, também conhecidos como freios de caixa e panela ou freios de dedo, são máquinas-ferramentas usadas na fabricação de metal e na fabricação de chapas metálicas. Eles são empregados principalmente para dobrar e moldar chapas metálicas finas em ângulos e formas necessárias, como caixas, bandejas e outros componentes tridimensionais. Amplamente usados em indústrias como HVAC, fabricação de metal e trabalho geral de chapas metálicas, os freios de panela apresentam peças principais como a braçadeira, dedos segmentados, matrizes e punção. Embora mais simples do que as prensas dobradeiras, as prensas dobradeiras se destacam na criação de ângulos estreitos e bordas curtas, mas não têm a precisão e o controle das prensas dobradeiras CNC ou NC.
Variações (como freios de dedo)
Um freio de dedo é um tipo de freio de panela que inclui dedos ou barras segmentadas, que podem ser ajustadas para criar diferentes tipos de curvas e formas na chapa de metal. Essa variação oferece maior versatilidade e precisão ao formar componentes de chapa de metal intrincados e personalizados.
Características únicas e aplicações típicas
Os freios de panela são equipados com grampos para prender a chapa de metal, uma borda reta para alinhamento e uma folha de dobra para aplicar pressão e criar dobras. Eles são comumente usados para produzir caixas, panelas planas e bandejas em tamanhos e formatos específicos. Os freios de panela são particularmente úteis para criar componentes com dobras e dobras complexas, como gabinetes elétricos, sistemas de tubulação e invólucros de metal especializados, tornando-os ideais para produção personalizada em pequena escala.
Benefícios em Projetos Específicos
Em certos projetos, os freios de panela oferecem as seguintes vantagens:
- Dobra personalizável:Eles são adequados para produzir formatos ou tamanhos exclusivos de peças metálicas.
- Operação simples: Os freios de panela são mais fáceis de operar e configurar do que os freios de prensa, especialmente para aplicações que não exigem alta precisão.
- Custo-eficácia: Os freios de panela são altamente econômicos para projetos personalizados e de pequena escala, reduzindo os custos de terceirização e os prazos de entrega ao permitir a produção interna de peças metálicas personalizadas.
- Tamanho compacto: Ao contrário das grandes prensas dobradeiras, as prensas dobradeiras são menores e adequadas para áreas de trabalho com espaço limitado.
- Versatilidade: Os dedos ajustáveis dos freios de dedo proporcionam flexibilidade para criar vários formatos e tamanhos, permitindo a produção de diversos produtos de metal.
Principais diferenças entre prensas dobradeiras e prensas dobradeiras
1. Funcionalidade e Design
- Freios de prensa: As prensas dobradeiras são projetadas para dobrar e moldar chapas de metal usando um sistema de punção e matriz. Elas podem lidar com metais mais espessos e produzir componentes complexos, tornando-as adequadas para uma ampla gama de projetos de fabricação de metal. Elas normalmente apresentam sistemas mecânicos, hidráulicos ou servoacionados para controle preciso e operação em alta velocidade.
- Freios Pan: Freios de panela, também conhecidos como freios de caixa e panela ou freios de dedo, são projetados para dobrar chapas finas de metal em formatos específicos, como caixas, bandejas e componentes tridimensionais. Eles usam um mecanismo de fixação e dedos segmentados para criar dobras, tornando-os ideais para aplicações que exigem ângulos estreitos e bordas curtas.
2. Precisão e Controle
- Freios de prensa: As prensas dobradeiras oferecem alta precisão e controle, especialmente quando equipadas com sistemas CNC (Controle Numérico Computadorizado) ou NC (Controle Numérico). Essas máquinas podem atingir resultados precisos e repetíveis, tornando-as adequadas para tarefas de produção complexas e de alto volume.
- Freios Pan: Os freios de panela são geralmente menos precisos do que os freios de prensa e são mais adequados para tarefas simples de dobra. Embora forneçam algum nível de versatilidade, eles não têm os sistemas de controle avançados encontrados em freios de prensa CNC ou NC.
3. Aplicações e usos
- Freios de prensa: Devido à sua capacidade de lidar com várias espessuras e complexidades de metal, as prensas dobradeiras são usadas em diversas indústrias, incluindo automotiva, aeroespacial e construção. Elas são ideais para produzir componentes com formas complexas e séries de produção em larga escala.
- Freios Pan: Freios de panela são comumente usados em HVAC, fabricação geral de chapas metálicas e outras indústrias onde a produção de caixas, bandejas e componentes de pequena escala é necessária. Eles são particularmente benéficos para projetos de produção personalizados e de baixo volume.
4. Operação e configuração
- Freios de prensa: As prensas dobradeiras exigem configuração e operação mais complexas, geralmente envolvendo programação e mudanças de ferramentas. No entanto, elas oferecem maior automação e eficiência, particularmente em ambientes de fabricação de alto volume.
- Freios Pan: Os freios de panela são mais simples de operar e configurar, tornando-os acessíveis para oficinas menores ou situações em que mudanças frequentes de configuração são necessárias. Eles são bem adequados para projetos com requisitos de precisão mais baixos.
5. Requisitos de custo e espaço
- Freios de prensa: Normalmente maiores e mais caras, as prensas dobradeiras exigem investimento e espaço significativos. Elas são mais adequadas para operações com necessidade de alta capacidade e precisão.
- Freios Pan: Geralmente mais econômicos e compactos, os freios de pan são ideais para oficinas menores com espaço limitado. Eles fornecem uma solução acessível para tarefas específicas de dobra sem a necessidade de equipamentos de grande porte.
Escolhendo o freio certo para seu projeto
Fatores a considerar
Complexidade do projeto e exigência de precisão: para projetos que exigem alta precisão e dobras complexas, a prensa dobradeira é uma escolha inteligente.
Tipos de materiais e espessuras: a prensa dobradeira é adequada para materiais mais espessos e sólidos, enquanto a prensa dobradeira é adequada para chapas metálicas mais finas, abaixo de 6 mm.
Volume de produção: As prensas dobradeiras são adequadas para produção em massa porque oferecem maior velocidade de produção e maior repetibilidade.
Restrições de espaço e orçamento: em caso de espaço e orçamento restritos, o freio de mão será a escolha ideal para você.
Fator | Freio Pan | Pressione o freio |
---|---|---|
Espessura do material | Aço macio ou alumínio mais fino com menos de 6 mm | Calibres mais grossos acima de 6 mm |
Alterar frequência/raios de curvatura | Mudanças frequentes ou raios estreitos | Curvas simples sem raios apertados |
Espaço no chão | Limitado | Não é uma restrição (pode substituir vários freios de panela) |
Volume de produção | Não especificado | Volumes mais altos |