A qualidade de corte a laser alcançado por máquinas de corte a laser está sujeito a uma infinidade de fatores, tornando-o uma interação complexa. No cerne do processo de corte a laser está a interação entre o feixe de laser e os materiais sendo cortados, categorizados em dois fenômenos principais: microscópico e macroscópico.
Fenômenos microscópicos aprofundam-se nos intrincados processos de reação quântica que ocorrem durante a interação laser-material. Enquanto isso, fenômenos macroscópicos abrangem absorção de material, reflexão, refração, bem como a conversão de energia e transmissão de feixes de laser.
Além das características intrínsecas do material que está sendo processado, fatores relacionados ao hardware também exercem influência na qualidade do corte. Vamos explorar esses fatores juntos.
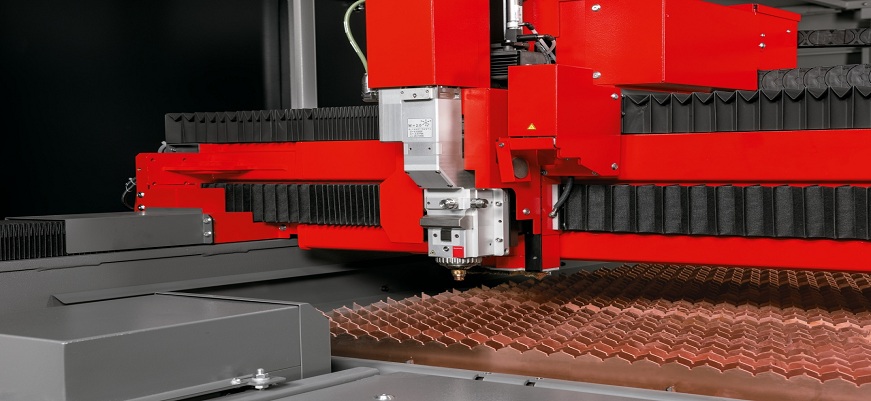
Importância do Controle de Qualidade
O controle de qualidade tem um papel insubstituível nos negócios. Por meio de amostragem e controle de processo, as organizações podem melhorar seu desempenho. O mesmo é válido para o processo de corte a laser. No entanto, surge a questão de como medir a qualidade do corte de metal a laser?
Nos textos anteriores, enfatizamos a importância de otimizar os parâmetros de corte a laser, ou seja, a implementação de manutenção preventiva do cortador a laser. Quando se trata de cortadores a laser bons e de alta qualidade, a possibilidade de anomalias no processo de corte é reduzida ao mínimo. No entanto, deve-se prestar atenção a outros indicadores-chave de desempenho (KPI) importantes que fornecem feedback sobre o nível de qualidade do corte a laser.
Normas de corte a laser
Como uma grande parte dos negócios e processos nas organizações de hoje é padronizada e normatizada, padrões que prescrevem parâmetros de corte a laser de qualidade foram desenvolvidos. O padrão ISO DIN EN ISO 9013: 2002 define os requisitos para corte a laser e outros tipos de corte térmico. O padrão prescreve o controle dos seguintes parâmetros de corte:
- metal fundido
- a incisão do corte
- a perfuração do corte
- linhas de corte
- rugosidade
Parâmetros de controle de qualidade
- Formação do metal fundido – o controle deste parâmetro é geralmente feito por inspeção visual do metal que está sendo fatiado. As informações obtidas pela verificação referem-se ao foco do feixe de laser ou da óptica do cortador a laser.
- A incisão do corte – um parâmetro que depende do material que está sendo cortado e é determinado pela tolerância para cada metal de forma diferente. As informações obtidas pela inspeção da incisão nos dizem sobre o tamanho da penetração do feixe de laser no metal.
- A perfuração–A perfuração do metal é criada devido à ação corrosiva e pode alterar muito a qualidade do corte. Este parâmetro é geralmente inspecionado visualmente e descrito qualitativamente.
- Linhas de corte – as linhas de corte durante o corte a laser são determinadas pela velocidade em que cada posição é cortada. Este parâmetro também é inspecionado visualmente, e as informações fornecidas pela inspeção falam sobre a necessidade de ajustar os parâmetros de corte em termos de potência e velocidade.
- Rugosidade – um parâmetro que influencia a necessidade de manuseio adicional de material após o corte a laser. A rugosidade é definida dependendo da espessura do material que está sendo cortado.
A melhoria da qualidade dos cortes a laser pode ser alcançada por meio da manutenção consistente do cortador a laser e do ajuste fino dos parâmetros de corte. Embora o controle de qualidade e a otimização dos parâmetros desempenhem papéis cruciais, eles servem como etapas iniciais para atingir resultados de corte ideais. A eficácia do controle de qualidade depende da execução de uma série de cortes.
Quando múltiplos cortes idênticos são realizados, o controle meticuloso dos parâmetros se torna imperativo para evitar a repetição de erros ao longo da série. Assim, o monitoramento e o ajuste contínuos dos parâmetros garantem operações de corte consistentes e sem erros.
Fatores que afetam a qualidade do corte a laser das máquinas de corte a laser
Características do feixe:
Há uma relação significativa entre a largura da incisão do corte a laser e o diâmetro do ponto focalizado. Devido ao fato de que a densidade de potência e a densidade de energia da irradiação a laser estão relacionadas ao diâmetro do ponto do laser, para obter uma maior densidade de potência e escala de energia, no processamento de corte a laser, o diâmetro do ponto deve ser o menor possível.
Potência do laser:
A magnitude da potência do laser afeta diretamente a espessura da chapa de aço que pode ser cortada. Quanto maior a potência, mais espesso o material que pode ser cortado. Além disso, também afeta a precisão dimensional da peça de trabalho, a largura da costura de corte, a rugosidade da superfície de corte e a largura da zona afetada pelo calor.
A potência do laser tem um impacto significativo na velocidade de corte, largura da costura, espessura do corte e qualidade do corte. O nível de potência é determinado pelas características do material e pelo mecanismo de corte. Materiais com altos pontos de fusão (como ligas) e alta refletividade de superfície (como cobre e alumínio) exigem maior potência do laser.
Por exemplo, uma Máquina de Corte a Laser de Fibra de Chapa de Metal de 1500 W não consegue atingir o trabalho de uma máquina de corte a laser de 6000 W. Muitas vezes, se você achar que o efeito de corte não é o ideal, é bem provável que você tenha escolhido o modelo de laser errado.
No processamento de corte a laser, há uma potência de laser que atinge a melhor qualidade de corte. Sob essa potência de laser, pode haver fenômenos de corte incompleto ou suspensão de escória. Acima dessa potência, ele superaquecerá.
Velocidade de corte a laser:
A velocidade de corte tem um impacto significativo na qualidade do corte. A velocidade de corte ideal resultará em uma linha relativamente suave na superfície de corte, seção transversal lisa do material e sem rebarbas. Quando a pressão do gás auxiliar e a potência do laser são constantes, há uma relação inversa não linear entre a velocidade de corte e a largura da costura de corte. Se a velocidade de corte for muito lenta, é fácil causar a superfusão do material, a costura de corte se torna mais larga, a zona afetada pelo calor aumenta e até mesmo a superfusão da peça de trabalho. Cortar muito rápido pode fazer com que o material não corte, causando respingos de faíscas, produzindo escória na metade inferior e até mesmo queimando a lente.
Bicos:
A abertura do bico e a distância entre a saída do bico e a superfície do material podem afetar o efeito de corte.
Posição do foco:
A posição do foco afeta diretamente a largura da incisão, a rugosidade da seção transversal e a adesão de resíduos de resíduos. As diferentes posições focais resultam em diferentes diâmetros de feixe e profundidades focais na superfície do material processado, levando a mudanças no formato da costura de corte e afetando o fluxo de gás processado e metal fundido dentro da seção transversal.
A posição do foco é a distância do foco do laser até a superfície da peça de trabalho, o que afeta diretamente a rugosidade da superfície de corte, a inclinação e a largura da costura de corte e o status de adesão do resíduo fundido. Se a posição do foco for muito avançada, aumentará o calor absorvido pela extremidade inferior da peça de trabalho que está sendo cortada.
Em uma certa velocidade de corte e pressão de ar auxiliar, isso fará com que o material que está sendo cortado e o material derretido perto da costura de corte fluam em um estado líquido na superfície inferior. Após o resfriamento, o material derretido irá aderir à superfície inferior da peça de trabalho em uma forma esférica. Se a posição ficar para trás, o calor absorvido pela face da extremidade inferior do material que está sendo cortado diminuirá, de modo que o material na costura de corte não pode derreter completamente, e alguns resíduos afiados e curtos irão aderir à superfície inferior da placa.
Normalmente, a posição do foco deve ser na superfície da peça de trabalho ou um pouco mais baixa, mas materiais diferentes exigem requisitos diferentes. Ao cortar aço carbono, a qualidade do corte é melhor quando o foco está na superfície da placa. Ao cortar aço inoxidável, o foco deve estar em torno de 1/2 da espessura da placa para melhores resultados.
Gás auxiliar:
O corte de material requer o uso de gás auxiliar, principalmente a pressão do gás e o tipo de gás, os quais podem afetar a rugosidade da seção de corte e a geração de escória.
No processamento de corte a laser, a pressão de ar auxiliar desempenha um papel na remoção de escória, no resfriamento de materiais e na assistência à combustão. Os gases auxiliares incluem oxigênio, ar comprimido, nitrogênio e gases inertes.
O oxigênio pode participar da combustão do metal e melhorar a eficiência do corte, tornando-o adequado para cortar a maioria dos metais; Gases inertes e ar são adequados para cortar certos materiais metálicos (como ligas de alumínio) e materiais não metálicos, o que pode evitar a combustão do material.
Se a pressão do gás auxiliar for muito alta, correntes parasitas aparecerão na superfície do material, enfraquecendo a capacidade de remover materiais fundidos, levando ao alargamento da costura de corte e à superfície de corte áspera; Se a pressão do ar for muito baixa, o material fundido não pode ser completamente soprado para longe, e a escória irá aderir à superfície inferior do material. Portanto, a pressão do gás auxiliar deve ser ajustada durante o corte para obter a melhor qualidade de corte.
Soluções de qualidade de corte a laser para máquinas de corte a laser de fibra
- Configurações de energia ideais: Ajustar as configurações de potência do laser de acordo com o tipo e a espessura do material é crucial para obter cortes limpos e precisos. O ajuste fino dos parâmetros de potência garante um processamento eficiente do material sem causar zonas excessivamente afetadas pelo calor ou bordas ásperas.
- Ajuste de foco: O foco adequado do feixe de laser é essencial para manter a qualidade do corte. A calibração e o ajuste regulares da posição do foco garantem a qualidade ideal do feixe e o desempenho do corte.
- Seleção de gás e controle de pressão: Escolher o gás de assistência apropriado (como oxigênio, nitrogênio ou ar) e controlar sua pressão remove efetivamente o material fundido do corte e previne a oxidação durante o corte. A seleção adequada do gás e o ajuste da pressão contribuem para melhorar a qualidade da borda e reduzir a formação de escória.
- Manutenção de bicos e lentes: A limpeza e inspeção regulares dos bicos de corte e lentes de foco são essenciais para evitar o acúmulo de detritos e manter a qualidade do feixe. Substitua componentes desgastados ou danificados imediatamente para garantir um desempenho de corte consistente.
- Tecnologia avançada de cabeça de corte: A atualização para cabeçotes de corte equipados com recursos avançados, como ajuste automático de distância focal, proteção contra colisões e monitoramento em tempo real, pode aumentar a precisão e a produtividade do corte.
- Controle de feixe dinâmico: A implementação de tecnologias de controle dinâmico de feixe, como modelagem e oscilação de feixe, permite um controle mais preciso sobre a distribuição de intensidade do feixe de laser e melhora a qualidade do corte, especialmente em geometrias complexas e cantos apertados.
- Manuseio e fixação de materiais: Técnicas adequadas de manuseio e fixação de materiais ajudam a minimizar a vibração e a distorção do material durante o corte, resultando em cortes mais suaves e maior precisão dimensional.
- Parâmetros de corte otimizados: O ajuste fino de parâmetros de corte, como velocidade de corte, aceleração e alinhamento do feixe com base nas propriedades do material e nos requisitos de corte, pode melhorar significativamente a qualidade e a eficiência do corte.
- Sistemas de Garantia de Qualidade: A implementação de sistemas de garantia de qualidade, como monitoramento em tempo real, detecção automática de defeitos e mecanismos de feedback, garante qualidade de corte consistente e confiável durante todo o processo de produção.
Ao implementar essas soluções, os operadores podem otimizar o desempenho de máquinas de corte a laser de fibra e alcançar qualidade de corte superior em uma ampla gama de materiais e aplicações.