O que é a ferramenta Grooving
UM ferramenta de ranhura, também conhecida como fresa de ranhura ou inserto de ranhura, é uma ferramenta de corte usada em operações de usinagem para criar ranhuras ou canais em uma peça de trabalho. Essas ranhuras podem servir a vários propósitos, dependendo da aplicação e da indústria. Aqui está uma visão geral das ferramentas de ranhura e seus usos comuns:
10 considerações importantes para utilizar uma ferramenta de ranhura.
Entenda o tipo de ranhura
É fundamental compreender os três principais tipos de ferramentas de ranhura, que são: ranhura externa, ranhura de furo interno e ranhura de face final.
Ranhuras externas são as mais simples de processar, pois a força da gravidade e o uso de refrigerante podem auxiliar na remoção de cavacos. O operador pode observar diretamente a usinagem de ranhuras externas, tornando relativamente fácil monitorar a qualidade do processo de usinagem. No entanto, é essencial evitar potenciais problemas de design ou fixação com a peça de trabalho. Para obter resultados de corte ideais, é melhor manter a ponta da ferramenta de ranhura ligeiramente abaixo da linha central.
A ranhura interna do furo se assemelha à ranhura do diâmetro externo, exceto que a aplicação do refrigerante e a remoção de cavacos podem ser mais desafiadoras. Os melhores resultados podem ser obtidos quando a posição da ponta está ligeiramente acima da linha central para ranhura interna.
Para ranhuramento de face final, a ferramenta deve ter a capacidade de se mover na direção axial, e o raio do flanco da ferramenta deve corresponder ao raio da superfície usinada. A posição da aresta de corte da ferramenta de ranhuramento deve estar ligeiramente acima da linha central.
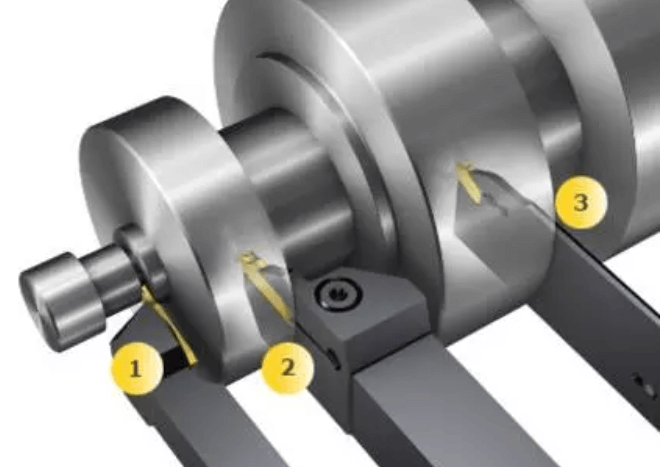
Máquinas-ferramentas de processamento e aplicações
No processo de ranhuramento, o tipo de design e as especificações técnicas da ferramenta de ranhura também são fatores críticos a serem considerados. Alguns dos principais requisitos de desempenho para máquinas-ferramentas incluem:
Ter potência suficiente para garantir que a ferramenta opere dentro da faixa de velocidade correta sem parar ou vibrar;
Possui alta rigidez para completar o corte necessário sem vibração;
Ter pressão e fluxo de refrigerante altos o suficiente para facilitar a remoção de cavacos;
Ter um alto nível de precisão.
Além disso, para produzir o formato e o tamanho de ranhura desejados, é crucial ajustar e calibrar adequadamente a máquina-ferramenta.
Entenda as características do material da peça de trabalho
Estar familiarizado com as propriedades do material da peça de trabalho, como sua resistência à tração, características de endurecimento por trabalho e tenacidade, é vital para compreender o impacto da peça de trabalho na ferramenta. Ao usinar diferentes materiais de peça de trabalho, combinações variadas de velocidade de corte, taxa de avanço e características da ferramenta são necessárias. Diferentes materiais de peça de trabalho também podem necessitar de geometrias de ferramenta específicas para gerenciar lascas ou exigir o uso de revestimentos específicos para aumentar a longevidade da ferramenta.
Escolha a ferramenta de ranhura certa
A seleção e utilização adequadas de ferramentas de ranhuramento determinarão a relação custo-benefício da usinagem.
A ferramenta de ranhura pode usinar a geometria da peça de duas maneiras:
A primeira é processar todo o formato da ranhura fazendo um único corte;
A segunda é desbastar o tamanho final da ranhura cortando em várias etapas.
Depois que a geometria da ferramenta for escolhida, pode ser benéfico considerar um revestimento de ferramenta que melhore o desempenho de remoção de cavacos.
Ferramentas de formulário
Ao usinar grandes quantidades, pode ser vantajoso considerar o uso de ferramentas de conformação.
A ferramenta de conformação pode cortar todos ou a maioria dos formatos de ranhuras em uma única operação, liberando a posição da ferramenta e reduzindo o tempo do ciclo de processamento.
Uma desvantagem das ferramentas sem lâmina é que se um dos dentes quebrar ou se desgastar mais rápido que os outros dentes, a ferramenta inteira deverá ser substituída.
É importante controlar os cavacos gerados pela ferramenta e a potência da máquina necessária para o corte de conformação. Isso deve ser levado em consideração.
Escolha a ferramenta multifuncional de ponto único
O uso de ferramentas multifuncionais pode gerar trajetórias de ferramentas nas direções axial e radial.
Com esse tipo de ferramenta, não apenas a ranhura pode ser usinada, mas o diâmetro também pode ser torneado, o raio e o ângulo podem ser interpolados e o torneamento multidirecional pode ser executado.
Quando a lâmina começa a cortar, ela se move axialmente de uma extremidade à outra da peça de trabalho, mantendo contato com a peça.
Ao usar uma ferramenta multifuncional, é possível gastar mais tempo cortando a peça de trabalho em vez de trocar ferramentas ou fazer movimentos de curso vazios.
Ferramentas multifuncionais também ajudam a otimizar o processo de usinagem de toda a peça de trabalho.
Use a sequência de processamento correta
O planejamento racional da sequência de usinagem ideal envolve levar em consideração vários fatores, como a mudança na resistência da peça antes e depois da usinagem da ranhura, pois a resistência da peça diminui depois que a ranhura é usinada primeiro.
Isso pode fazer com que o operador use uma taxa de avanço e velocidade de corte menores do que o ideal para evitar trepidação. No entanto, diminuir os parâmetros de corte pode levar a tempos de usinagem mais longos, vida útil da ferramenta mais curta e desempenho de corte instável.
Outro fator a ser considerado é se o processo subsequente empurrará as rebarbas para dentro das ranhuras usinadas anteriormente.
Como orientação geral, é aconselhável começar pelo ponto mais distante do porta-ferramentas após a conclusão do torneamento do diâmetro externo (DE) e do diâmetro interno (ID), seguido pela usinagem das ranhuras e outras características estruturais.
O papel da taxa de alimentação e da velocidade de corte
A taxa de avanço e a velocidade de corte são fatores cruciais na usinagem de ranhuras. Velocidades de avanço e corte inadequadas podem resultar em trepidação, vida útil reduzida da ferramenta e tempos de ciclo de usinagem estendidos.
Vários fatores, incluindo o material da peça de trabalho, a geometria da ferramenta, o tipo e a concentração do líquido de arrefecimento, o revestimento do inserto e o desempenho da máquina, podem afetar o avanço e a velocidade de corte.
Para resolver problemas causados por velocidades de avanço e corte incorretas, geralmente é necessária usinagem secundária.
Embora haja uma grande quantidade de informações disponíveis sobre as velocidades de avanço e corte “ótimas” para várias ferramentas, as informações mais relevantes e práticas são normalmente fornecidas pelo fabricante da ferramenta.
Seleção do revestimento da lâmina
O revestimento de uma lâmina de carboneto pode aumentar significativamente sua vida útil.
Ao fornecer uma camada lubrificante entre a ferramenta e o cavaco, o revestimento também reduz o tempo de usinagem e melhora o acabamento superficial da peça de trabalho.
Alguns dos revestimentos comumente usados hoje incluem TiAlN, TiN e TiCN. Para desempenho ideal, é essencial combinar o revestimento com o material que está sendo usinado.
Fluido de corte
A aplicação adequada do fluido de corte envolve o fornecimento de fluido suficiente no ponto de corte onde o inserto ranhurado entra em contato com a peça de trabalho.
O fluido de corte tem duas funções: resfriar a área de corte e auxiliar na remoção de cavacos.
Aumentar a pressão do fluido de corte no ponto de corte é altamente eficaz para melhorar a evacuação de cavacos ao usinar ranhuras de diâmetro interno de furo cego.
Para ranhurar materiais desafiadores, como aqueles com alta tenacidade ou viscosidade, o resfriamento de alta pressão oferece benefícios significativos.
A concentração de líquido de arrefecimento à base de óleo solúvel em água também é crucial para a abertura de valas em materiais difíceis.
Embora a faixa típica de concentração do líquido de arrefecimento esteja entre 3% e 5%, você também pode testar o aumento da concentração (até 30%) para aumentar a lubricidade do líquido de arrefecimento e fornecer uma camada protetora para a ponta da lâmina.