Erros que resultam na falha de Precisão da prensa dobradeira pode surgir de vários fatores, incluindo problemas mecânicos com a máquina de dobrar chapas metálicas, bem como fatores externos como ferramentas de dobra, espessura do material e erros operacionais humanos. Neste artigo, examinaremos os vários fatores que impactam a dobra precisa e forneceremos soluções para alguns dos cenários comuns encontrados.
Introdução aos princípios básicos da prensa dobradeira
Freios de prensa são indispensáveis na indústria de fabricação de metais, servindo como a pedra fundamental para transformar chapas planas em peças com geometrias complexas. O domínio das operações de prensa dobradeira é uma mistura de arte e ciência, exigindo um profundo entendimento da mecânica da máquina, do comportamento do material e das complexidades do design a ser executado.
O papel das prensas dobradeiras na dobra de metais
- Funcionalidade: A essência de uma prensa dobradeira está em sua capacidade de transformar chapas de metal em formatos desejados com controle meticuloso sobre o ângulo e o raio de curvatura. A força exercida pela prensa dobradeira é poderosa e precisa, permitindo uma ampla gama de operações de curvatura, de ângulos agudos a dobras complexas e multiangulares.
- Tipos: A diversidade de prensas dobradeiras, desde as tradicionais mecânico modelos para avançados hidráulico e elétrico versões, oferece aos fabricantes a flexibilidade de escolher uma máquina que se alinhe com suas necessidades específicas de produção. Cada tipo traz vantagens distintas, como a velocidade das prensas mecânicas, a potência dos sistemas hidráulicos e a eficiência energética dos modelos elétricos.
- Ferramentas: Selecionando o direito morre e socos é crítico não apenas para atingir a curvatura desejada, mas também para minimizar o desgaste da máquina. As ferramentas devem ser escolhidas com base na espessura do material, ângulo de curvatura e raio de curvatura necessário para garantir resultados ideais.
Processos controlados para precisão
- Programação: A integração de Controles CNC revolucionou as operações de prensas dobradeiras, permitindo que os operadores programem sequências de dobra complexas e as armazenem para uso futuro. Essa precisão digital garante que cada dobra seja executada com força e ângulo consistentes, contribuindo para a precisão geral do produto finalizado.
- Precisão:Atingir precisão na dobra é uma sinfonia de controle velocidade, pressão, e posicionamento do medidor traseiro. A capacidade de ajustar esses parâmetros permite ajustes minuciosos que podem impactar significativamente a qualidade da curvatura.
- Repetibilidade: A verdadeira medida da capacidade de uma prensa dobradeira é sua consistência. A capacidade de replicar dobras com precisão inabalável é o que diferencia a fabricação de alta qualidade do resto. Essa repetibilidade é crucial para manter a uniformidade em todas as execuções de produção, especialmente para fabricação em larga escala.
Obtendo Precisão na Dobra
A dobra de precisão é um processo holístico que se estende além da própria prensa dobradeira. Ela abrange o experiência do operador, o seleção de materiais, e o manutenção de máquinas. Cada elemento desempenha um papel fundamental no resultado final, e uma falha em qualquer área pode comprometer a integridade da curva.
Seleção e preparação de materiais
- Propriedades do material: A seleção do material não é uma decisão a ser tomada de ânimo leve. Fatores como resistência à tracção, ductilidade, e grossura ditam o processo de dobra e a força necessária. Materiais com maior resistência à tração exigem mais força para dobrar, enquanto aqueles com maior ductilidade permitem raios de dobra mais apertados sem rachar.
- Preparação:A condição da superfície do metal pode influenciar muito o processo de dobra. Tratamento de superfície como primer ou revestimento, juntamente com uma limpeza completa limpeza, garante que impurezas não afetem o comportamento do metal durante a dobra. Esta preparação é essencial para obter uma dobra limpa e afiada.
Técnicas e considerações avançadas
- Dobra de ar:A técnica de dobra a ar se destaca pelo contato mínimo entre a ferramenta e a peça, o que se traduz em menor desgaste das ferramentas e maior flexibilidade no manuseio de diferentes espessuras de material.
- Medição de ângulo: O uso de sistemas de medição de ângulo a laser fornece feedback em tempo real, permitindo ajustes instantâneos para garantir que o ângulo de curvatura seja preciso. Esta tecnologia é inestimável para manter altos padrões de precisão.
- Manutenção de ferramentas: Normal inspeção e manutenção das ferramentas não são negociáveis para preservar a qualidade das dobras. Ferramentas cegas ou danificadas podem levar a defeitos na peça de trabalho e reduzir a vida útil da prensa dobradeira.
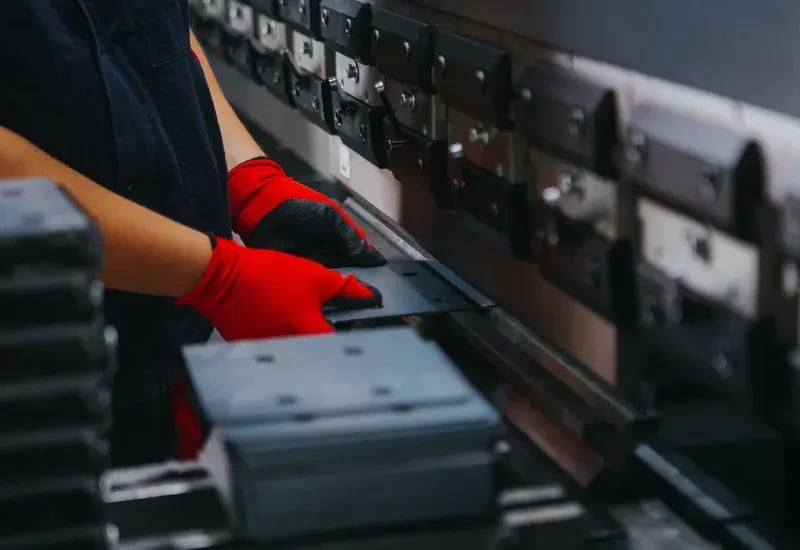
Compreendendo a precisão da dobra da prensa dobradeira
Definindo a precisão da flexão
A precisão da dobra da prensa dobradeira é a pedra angular da metalurgia de precisão. É o grau em que a máquina pode corresponder às especificações de dobra pretendidas, o que inclui o ângulo, o raio e a posição da dobra na chapa metálica. Essa precisão é primordial, pois determina o ajuste e a função do produto final montado. Mesmo um pequeno desvio pode levar a problemas de montagem, defeitos funcionais ou discrepâncias estéticas.
Principais fatores que influenciam a precisão
- Espessura do material: A espessura do material que está sendo dobrado desempenha um papel fundamental no processo de dobra. Materiais mais espessos exigem mais força e podem retornar mais do que os mais finos, necessitando de calibração cuidadosa da prensa dobradeira para compensar esses fatores.
- Configuração da máquina: Uma configuração de máquina bem calibrada é essencial para obter dobras precisas. Isso envolve selecionar as ferramentas corretas, como o punção e a matriz, e garantir que a prensa dobradeira esteja programada com precisão para o trabalho em questão. A configuração deve levar em conta o tipo de material, a espessura e o ângulo de dobra desejado.
Garantindo precisão consistente
Importância da Consistência
- Uniformidade: A consistência na dobra garante que cada peça produzida pela prensa dobradeira esteja de acordo com as especificações do projeto. Essa uniformidade é crucial em indústrias onde componentes de metal devem se encaixar perfeitamente, como na fabricação aeroespacial ou automotiva.
- Controle de qualidade: Um processo de dobra consistente é um aspecto essencial do controle de qualidade. Ele minimiza o risco de produzir peças não conformes, o que pode levar a desperdício, aumento de custos de produção e potenciais problemas de segurança.
Mantendo alta precisão
Manutenção de máquinas
- Inspeções regulares: Inspeções de rotina são necessárias para identificar quaisquer sinais de desgaste ou problemas potenciais que possam afetar o desempenho da prensa dobradeira. Componentes como sistemas hidráulicos, peças elétricas e ferramentas devem ser verificados regularmente para garantir que estejam em boas condições de funcionamento.
- Ajustes: Com o tempo, os componentes do freio de prensa podem exigir ajustes para manter o desempenho ideal. Isso pode incluir realinhar o medidor traseiro, calibrar o êmbolo ou ajustar as configurações de pressão para corresponder às propriedades do material.
Experiência do operador
- Treinamento: Os operadores devem receber treinamento abrangente sobre a configuração, operação e manutenção da prensa dobradeira. Esse treinamento deve cobrir as nuances do trabalho com diferentes materiais e a importância da precisão no processo de dobra.
- Medição e Inspeção: Os operadores devem usar ferramentas de medição de precisão, como transferidores, localizadores de ângulo ou sistemas baseados em laser, para verificar a precisão de cada dobra. A inspeção regular das peças durante a produção ajuda a detectar quaisquer desvios precocemente e permite a correção imediata.
Ao focar nesses aspectos detalhados da precisão de dobra de prensa dobradeira, os fabricantes podem garantir que seus produtos atendam aos mais altos padrões de precisão e qualidade. A combinação de uma máquina bem conservada, operação qualificada e processos rigorosos de controle de qualidade é a chave para atingir e manter a precisão de dobra na fabricação de metal.
Compreendendo a precisão da dobra da prensa dobradeira
Definindo a precisão da flexão
A precisão da dobra da prensa dobradeira é a pedra angular da metalurgia de precisão. É o grau em que a máquina pode corresponder às especificações de dobra pretendidas, o que inclui o ângulo, o raio e a posição da dobra na chapa metálica. Essa precisão é primordial, pois determina o ajuste e a função do produto final montado. Mesmo um pequeno desvio pode levar a problemas de montagem, defeitos funcionais ou discrepâncias estéticas.
Principais fatores que influenciam a precisão
- Espessura do material: A espessura do material que está sendo dobrado desempenha um papel fundamental no processo de dobra. Materiais mais espessos exigem mais força e podem retornar mais do que os mais finos, necessitando de calibração cuidadosa da prensa dobradeira para compensar esses fatores.
- Configuração da máquina: Uma configuração de máquina bem calibrada é essencial para obter dobras precisas. Isso envolve selecionar as ferramentas corretas, como o punção e a matriz, e garantir que a prensa dobradeira esteja programada com precisão para o trabalho em questão. A configuração deve levar em conta o tipo de material, a espessura e o ângulo de dobra desejado.
Garantindo precisão consistente
Importância da Consistência
- Uniformidade: A consistência na dobra garante que cada peça produzida pela prensa dobradeira esteja de acordo com as especificações do projeto. Essa uniformidade é crucial em indústrias onde componentes de metal devem se encaixar perfeitamente, como na fabricação aeroespacial ou automotiva.
- Controle de qualidade: Um processo de dobra consistente é um aspecto essencial do controle de qualidade. Ele minimiza o risco de produzir peças não conformes, o que pode levar a desperdício, aumento de custos de produção e potenciais problemas de segurança.
Mantendo alta precisão
Manutenção de máquinas
- Inspeções regulares: Inspeções de rotina são necessárias para identificar quaisquer sinais de desgaste ou problemas potenciais que possam afetar o desempenho da prensa dobradeira. Componentes como sistemas hidráulicos, peças elétricas e ferramentas devem ser verificados regularmente para garantir que estejam em boas condições de funcionamento.
- Ajustes: Com o tempo, os componentes do freio de prensa podem exigir ajustes para manter o desempenho ideal. Isso pode incluir realinhar o medidor traseiro, calibrar o êmbolo ou ajustar as configurações de pressão para corresponder às propriedades do material.
Experiência do operador
- Treinamento: Os operadores devem receber treinamento abrangente sobre a configuração, operação e manutenção da prensa dobradeira. Esse treinamento deve cobrir as nuances do trabalho com diferentes materiais e a importância da precisão no processo de dobra.
- Medição e Inspeção: Os operadores devem usar ferramentas de medição de precisão, como transferidores, localizadores de ângulo ou sistemas baseados em laser, para verificar a precisão de cada dobra. A inspeção regular das peças durante a produção ajuda a detectar quaisquer desvios precocemente e permite a correção imediata.
Ao focar nesses aspectos detalhados da precisão de dobra de prensa dobradeira, os fabricantes podem garantir que seus produtos atendam aos mais altos padrões de precisão e qualidade. A combinação de uma máquina bem conservada, operação qualificada e processos rigorosos de controle de qualidade é a chave para atingir e manter a precisão de dobra na fabricação de metal.
Fatores que influenciam a precisão da prensa dobradeira
Fatores da Máquina
Existem vários fatores que afetam a precisão de dobra de uma máquina de dobra de prensa dobradeira. Estes incluem:
- Retidão da abertura do carneiro: A abertura de fixação do carneiro é reta nas direções Y e X. Precisão de reposicionamento e precisão de posicionamento arbitrário do carneiro esquerdo e direito. A precisão da abertura do carneiro nas direções Y e X é crucial para a precisão da dobra. Se a abertura do carneiro não for reta, isso levará a desvios no ângulo e na posição da dobra.
- Folga entre o carneiro e os trilhos-guia do quadro: A folga entre o êmbolo da prensa dobradeira e a guia linear do quadro deve ser razoável. A folga adequada entre o êmbolo e os trilhos-guia do quadro garante a estabilidade do êmbolo durante o movimento, melhorando assim a precisão de dobra das prensas dobradeiras.
- Perpendicularidade e Inclinação do Quadro: Perpendicularidade e inclinação do quadro. A perpendicularidade e a inclinação do quadro afetam a distribuição da força de flexão durante o processo de flexão, o que por sua vez garante a precisão da flexão.
- Conexão entre o cilindro e o carneiro:A conexão entre o cilindro e o cilindro deve ser consistente para garantir uma distribuição uniforme da força de flexão durante a flexão em prensas dobradeiras.
Há também outros fatores que afetam a precisão da dobra da prensa dobradeira, como a resistência e a precisão da estrutura e do cilindro, a precisão do reposicionamento do sistema de batente traseiro nas direções X e R, o ajuste adequado do sistema de computador, o ajuste do sistema hidráulico e a correspondência entre o sistema hidráulico e o ajuste do computador.
Fatores de ferramentas
1. Precisão das matrizes superior e inferior:
A precisão das matrizes superior e inferior é crítica. Deformação, danos, desgaste e outros problemas com as matrizes podem impactar todos os aspectos da dobra de metal. Se descoberto, deve ser prontamente relatado e corrigido. Portanto, inspeção e manutenção regulares são necessárias.
2. Alinhamento da matriz:
O desalinhamento entre as matrizes superior e inferior pode resultar em desvio no tamanho da dobra. Certifique-se de que as ferramentas estejam alinhadas corretamente durante a configuração da ferramenta.
Após as posições esquerda e direita do back gauge se moverem, a distância entre a matriz inferior e o back gauge muda. Isso pode ser medido usando um paquímetro e ajustado usando o parafuso do back gauge.
A precisão e compatibilidade do dispositivo de compensação da matriz inferior devem ser verificadas, combinando com o design do quadro. O dispositivo de fixação da matriz superior deve ser altamente preciso.
3. Tamanho da abertura da matriz em V:
O tamanho da abertura da matriz em forma de V e a pressão de dobra são inversamente proporcionais. Quando o comprimento e a espessura da placa são fixos, quanto maior a abertura, menor a pressão necessária. Portanto, ao trabalhar com espessuras diferentes, o tamanho de abertura da matriz em forma de V apropriado deve ser usado.
Ao processar com uma carga unilateral, como em uma extremidade da prensa dobradeira, a pressão de flexão pode ser impactada, danificando a máquina. Isso é estritamente proibido. A parte do meio da máquina deve sempre ser tensionada ao montar a ferramenta.
Fatores de Chapa Metálica
A retidão do plano de referência da chapa metálica deve ser verificada. Certifique-se de que a tensão na chapa metálica seja uniforme. Verifique se a espessura da chapa metálica é consistente.
O paralelismo inadequado entre a peça de trabalho e a matriz inferior durante a dobra pode fazer com que a peça de trabalho retorne após a matriz superior ser pressionada, afetando o tamanho da dobra.
Springback se refere ao fenômeno em que o material tenta retornar à sua forma original após a dobra. A resistência à tração, espessura, ferramental e tipo de prensa dobradeira influenciam o springback. Prever e avaliar o springback de forma eficaz é crucial para lidar com dobras apertadas e materiais espessos e de alta resistência.
As propriedades e a espessura do material podem afetar o ângulo de curvatura, portanto, uma inspeção adequada e uma verificação pontual devem ser realizadas em cada peça de trabalho antes da dobra.
A seguir estão as propriedades do material em detalhes:
- Limite de escoamento: A resistência ao escoamento é o estresse máximo que um material pode suportar antes de começar a se deformar permanentemente. Entender a resistência ao escoamento ajuda a determinar a força máxima que pode ser aplicada durante a flexão para evitar danos ao material.
- Módulo de elasticidade: O módulo elástico indica a rigidez de um material e determina a quantidade de deformação sob uma dada tensão. Saber o módulo elástico ajuda a prever a quantidade de retorno elástico após a flexão.
- Espessura do material: A espessura do material afeta significativamente o processo de dobra. Materiais mais espessos exigem mais força para dobrar, e um raio de dobra maior é necessário para evitar rachaduras ou deformações.
- Ductilidade: Ductilidade se refere à capacidade de um material de sofrer deformação plástica sem quebrar. Materiais com alta ductilidade são mais fáceis de dobrar e menos propensos a rachar ou rasgar durante o processo.
Fatores de operação de flexão
1. Consistência das ações do operador:
Verifique se as forças esquerda e direita são consistentes quando os operadores de prensa dobradeira empurram o material para dobrar. Força de dobra inconsistente pode levar a desvios nas dimensões de dobra.
2. Ajuste de dados do sistema:
Certifique-se de que o erro de dados do sistema esteja ajustado corretamente ao usar o sistema. Um ângulo de dobra primário insuficiente pode afetar a dimensão de dobra secundária. Erros acumulados na dobra aumentarão o erro na dimensão do contorno da peça de trabalho.
A pressão necessária para dobrar varia com o comprimento e a espessura da peça de trabalho, e o comprimento e a espessura da placa são proporcionais à pressão necessária.
É importante ajustar a capacidade de flexão adequadamente quando o comprimento e a espessura da peça de trabalho mudam.
Impacto na precisão do trabalho
Influência da planura da mesa de trabalho da máquina de dobrar (longitudinal) na retidão das peças dobradas
1. Efeito da precisão do ângulo da peça de trabalho
Quando há um erro de planicidade longitudinal na bancada de trabalho, isso afetará a profundidade da matriz superior no entalhe da matriz inferior.
2. Efeito da precisão da retidão da peça de trabalho
Quando há um erro de planicidade na superfície de trabalho, a retidão da parte dobrada é igual ao erro de planicidade.
3. A influência da planura da mesa da prensa dobradeira (lateral) no ângulo e na retidão das peças dobradas
O mecanismo de influência da planura (direção transversal) da mesa da prensa dobradeira na precisão do ângulo e da retidão das peças dobradas é o mesmo do mecanismo de "influência longitudinal".
Inspeção de precisão de trabalho
Condições de inspeção
Requisitos da peça de teste
Requisitos de comprimento (desvio de comprimento é de ±3 mm)
Comprimento da bancada (mm) | Comprimento da amostra (mm) |
---|---|
≤2000 | eu |
>2000~3200 | 2000 |
>3200~5000 | 3000 |
>5000 | 4000 |
Requisito de largura: A largura da peça de teste não deve ser inferior a 100 mm. (*O desvio da largura é de ±0,2 mm.)
Requisitos de espessura
Força nominal (kN) | Espessura da amostra (t) |
---|---|
≤1000 | 2 |
>1000~2500 | 3 |
>2500~6300 | 4 |
>6300 | 6 |
Requisitos de material: O material da peça de teste é uma chapa de aço Q235A e a resistência à tração do material é σb≤450MPa.
Número de peças: O número de peças de teste não deve ser inferior a 3.
Requisitos do molde: O tamanho da abertura do molde inferior para a peça de teste é de 8 a 10 vezes a espessura do material.
Requisitos de posição: A peça de teste deve ser colocada no meio da bancada de trabalho.
Requisitos de ângulo de curvatura: O ângulo de curvatura da amostra é de 90°.
Posição de medição: Comece a medir a 100 mm da extremidade da peça de teste.
Requisitos da ferramenta de inspeção
Régua plana qualificada, régua angular universal e régua de folga.
Requisitos gerais
Antes de realizar o teste de precisão, o equipamento precisa ser nivelado e as direções horizontal e vertical não devem exceder 0,2/1000.
A prensa dobradeira é um dos principais equipamentos para formar produtos de chapa metálica e garantir a precisão do processamento de produtos de chapa metálica. A precisão do equipamento de dobra afetará diretamente a precisão do processamento de produtos de chapa metálica. O impacto de equipamentos de dobra insuficientemente precisos em desvios do produto é de longo prazo e objetivo. Se o status de precisão de um equipamento de dobra puder ser detectado, é muito necessário fornecer dados de precisão do equipamento para que a empresa aceite e repare o equipamento de dobra.
A norma nacional GB/T14349-2011 "Precisão de prensas dobradeiras" estipula inspeção de precisão, tolerância de inspeção e métodos de detecção para a precisão de prensas dobradeiras. Os itens de inspeção do equipamento de dobra incluem a inspeção da precisão geométrica e velocidade de trabalho da prensa dobradeira, que são explicados a seguir.
Teste de taxa de desconto de peça de teste
Cobrança ou diferença
0,05 mm em 1000 mm de comprimento.
Método de detecção
Coloque a superfície de detecção da régua plana de 1000 mm contra a borda do espécime dobrado (veja a imagem abaixo) e use um calibrador de folga para medir a folga δ entre os dois. O valor do erro é calculado com base no valor máximo da folga dentro de 1000 mm.
Peça de teste de flexão secundária
Se a tensão do material da peça de teste for grande, a peça de teste pode ser dobrada duas vezes (veja a figura abaixo). Teste a precisão de trabalho da máquina de dobra.
Calibração de prensa dobradeira: Aumente a precisão e a produtividade
Etapas de calibração da prensa dobradeira
O quão bem a prensa dobradeira é calibrada pode fazer ou quebrar todo o seu processo de dobra. Uma máquina mal calibrada pode produzir produtos irregulares que podem matar um tempo valioso por meio de retrabalho.
Não se intimide aqui. Basta seguir os seguintes passos e você estará pronto para prosseguir.
- Reúna a ferramenta necessária
Primeiro, você deve preparar algumas ferramentas. Ferramentas como ferramentas de prensa dobradeira, paquímetros ou micrômetros, localizadores de ângulo de precisão e materiais para testar dobra são alguns exemplos.
- Verifique a especificação
Obtenha informações sobre as especificações das prensas dobradeiras, como tonelagem, comprimento de dobra e velocidade de punção, no menu de fabricação ou nos arquivos. Verifique se esses requisitos podem atender às suas necessidades para determinadas tarefas.
- Limpe a máquina
A calibração não será tão precisa se a máquina estiver suja. Então, mantenha-a limpa e garanta que não haja sujeira, poeira ou detritos.
Examine cuidadosamente a cama, o aríete e o batente traseiro da prensa dobradeira. Isso porque essas são as peças mais propensas a tocar em chapas de metal. Além disso, certifique-se de que todos os equipamentos de segurança estejam onde deveriam estar e funcionem corretamente.
- Verificando
Há três tipos de processos de verificação que você terá que conduzir nesta etapa da calibração.
- Verificando a máquina: Verifique se há danos, deterioração ou desgaste no dispositivo, pois isso pode afetar a precisão da prensa dobradeira. Substitua todas as peças quebradas antes da calibração contínua. Além disso, certifique-se de que o sistema hidráulico, a conexão elétrica e o controlador estejam funcionando corretamente.
- Verifique o punção e a matriz: Observe o punção e a matriz para quaisquer problemas estranhos (por exemplo, ruído). Se houver algum problema com qualquer um dos componentes, substitua-os para que a dobra seja feita corretamente.
- Verifique o nível do óleo: Avalie o nível de óleo no sistema hidráulico. Níveis baixos de óleo farão a máquina funcionar mal. Os resultados de dobra serão ruins nesse caso. Portanto, certifique-se de que o óleo seja suficiente para operar a máquina antes de cada uso.
- Testando
Este é o último passo antes da calibração real. Use a amostra dobrando em material de resíduos para testar o freio de prensa.
- Verificação de flexão: Para encontrar o ângulo de curvatura final feito ao dobrar uma chapa de metal, use um transferidor ou medidor de ângulo confiável. As ferramentas de curvatura devem ser ajustadas para o ângulo certo se o resultado estiver errado.
- Verificação de distorção: Depois de dobrar algo, verifique se a prensa dobradeira se move. A deflexão anormal afetará a precisão da dobra. Se necessário, siga as instruções do fabricante para manter a deflexão no mínimo.
- Calibração
É hora de configurar a máquina para calibração. Isso inclui configurar os grampos, o back gauge e a ferramenta de dobra.
- Calibração do medidor traseiro
Para dobrar metal corretamente, você deve ajustar as configurações do medidor traseiro nos bastidores. Aqui está o que fazer:
- Comece desligando a máquina e colocando seus equipamentos de segurança, como luvas e óculos.
- Puxe a extremidade traseira do medidor totalmente para fora para que seja fácil levar o metal e as ferramentas até o local desejado.
- Escolha um ponto específico naquele back gauge para medir. Pode ser o ponto onde ele recua mais ou algum ponto fixo do ponto de flexão.
- Use ferramentas de medição exatas (pense em réguas extremamente precisas) para descobrir e anotar a distância desse ponto.
- Olhe para o número que a máquina joga para você para aquele ponto. Se esse número for diferente do que você mediu, você vai para o bit de controle do computador e mexe nele para combinar.
- Quando você achar que acertou, meça novamente naquele ponto especial, e ambos os números — o que você mediu e o que a máquina lhe disser — deverão ser gêmeos.
- Enrole-o verificando as distâncias em todo o território de puxar e empurrar. Você precisa verificar novamente se o número que apareceu é o que você tem na sua ferramenta de medição para cada instância.
- Ajuste a braçadeira e a ferramenta de dobra
O grampo segura a chapa de metal no lugar corretamente. Certifique-se de que ela esteja no local correto. Verifique se a ferramenta de dobra está no ângulo certo para fazer a dobra que você precisa.
- Verifique o paralelismo da RAM
Paralelismo de ram significa que o ram está reto em frente à superfície de dobra, que pode ser a base da prensa dobradeira ou uma bancada de trabalho. Meça corretamente e faça alterações com o medidor de paralelismo.
- Coroação
Coroamento é a linha curva na cama que endireita a pressão da chapa de metal que faz com que ela se dobre. Simplesmente mova o cilindro de óleo de cama até que ele forme a linha curva correta para ajustar o coroamento.
- Operar a execução de teste completa
Execute todo o programa de testes na prensa dobradeira usando diferentes espessuras de material e ângulos de curvatura. Verifique a precisão e a repetibilidade comparando o resultado medido com o que era esperado.
- Manter registros de calibração
Mantenha registros completos do processo de calibração, incluindo quaisquer alterações que você fizer e as configurações finais que você tiver. O arquivo é muito útil para solução de problemas e referência futura.
- Manutenção Regular
A prensa dobradeira funcionará melhor se receber manutenção regular. Verificar e calibrar a máquina rotineiramente é para mantê-la funcionando corretamente e com segurança.
Importância da calibração da prensa dobradeira
A calibração do freio de prensa é muito importante porque tem um efeito direto na segurança, precisão e qualidade da dobra do metal. Veja como:
- Consistência
A calibração do freio de prensa pode garantir que a máquina possa dobrar a chapa de metal em um ângulo preciso e estável. Fazer peças uniformes é possível com dobra precisa. Como resultado, haverá menos peças desperdiçadas e menos alterações no produto final.
- Economia de custos
Uma prensa dobradeira calibrada pode reduzir o desperdício de material porque ela só faz algumas peças quebradas. Além disso, a dobra precisa pode reduzir a necessidade de retrabalho, o que economiza tempo e dinheiro.
- Segurança
Uma prensa dobradeira bem calibrada diminui a probabilidade de acidentes em grande medida. No entanto, uma prensa dobradeira não calibrada ou mal calibrada pode fazer com que as ferramentas se movam inesperadamente durante o processo de medição. Isso pode acabar sendo ameaçador para o operador.
Conclusão
Da análise de um conjunto de dados de teste de referência fornecidos pelo fabricante da ferramenta de prensa dobradeira, o impacto do erro longitudinal da mesa de prensa dobradeira na precisão de dobra é cerca de três vezes maior que o erro transversal. O valor de impacto do desvio do ângulo de dobra é cerca de 3 vezes o erro de planura da bancada.
O desvio do ângulo de curvatura tem pouco efeito na verticalidade da superfície de trabalho devido ao curso do controle deslizante e pode ser ignorado. A retidão da superfície de trabalho refletirá diretamente o desvio de retidão da peça de trabalho, e os dois são quase iguais. O desvio de retidão de curvatura é menos afetado pelo curso do controle deslizante e pelo erro de verticalidade da superfície de trabalho. A mesa de trabalho mencionada neste artigo inclui dois, um é a mesa da máquina e o outro é a precisão geométrica da superfície de suporte horizontal da superfície de encaixe do molde superior. por exemplo:
O comprimento da mesa de trabalho de uma certa prensa dobradeira é de 3200 mm. Após medir a precisão de trabalho desta prensa dobradeira, os seguintes dados foram obtidos: o desvio de retidão da peça de trabalho é de 0,06 mm, e o desvio do ângulo de curvatura é de 0,1720. Pode-se inferir disso que a planura da superfície de trabalho desta prensa dobradeira é de cerca de 0,06 mm.
De acordo com o padrão nacional GB/T14349-2011 "Precisão de prensas dobradeiras", a margem de planicidade de uma prensa dobradeira com comprimento de mesa de 3200 mm é de 0,08 mm. A partir disso, pode-se determinar que a precisão de planicidade da prensa dobradeira é qualificada. Na verdade, como usuário de uma ferramenta de prensa dobradeira, você só precisa prestar atenção à precisão de trabalho da máquina-ferramenta.
Porque o Precisão da prensa dobradeira após o uso a longo prazo não ser afetado apenas pelos fatores mencionados neste artigo, a folga de transmissão e o desgaste mecânico da máquina-ferramenta que afetam a precisão da peça de trabalho também devem ser levados em consideração, e a máquina-ferramenta deve ser avaliada e considerada de forma abrangente. Ou seja, por meio da inspeção da precisão de trabalho das peças de dobra da máquina-ferramenta, combinada com os padrões nacionais para a precisão da prensa dobradeira, as capacidades abrangentes de processamento de precisão de uma prensa dobradeira podem ser inspecionadas e julgadas.