O que é uma prensa hidráulica
Prensa hidráulica, também conhecida como prensa hidráulica a óleo, é um tipo de maquinário que usa pressão estática líquida para processar metal, plástico, borracha, madeira, pó e outros produtos. É comumente usada em processos de prensagem e processos de conformação por prensa, como: forjamento, estampagem, extrusão a frio, endireitamento, dobra, flangeamento, trefilação de chapa fina, metalurgia do pó, encaixe por prensa e assim por diante.
Seu princípio é o uso da lei de Pascal feita pelo uso de maquinário de transmissão de pressão líquida, muitos tipos. Claro, o uso também é de acordo com a necessidade de uma variedade de coisas.
Por exemplo, há duas categorias de prensas hidráulicas e prensas hidráulicas de acordo com o tipo de líquido usado para transmitir pressão. A pressão total gerada por prensas hidráulicas é maior e é frequentemente usada para forjamento e estampagem.
As prensas hidráulicas de forjamento são divididas em dois tipos: prensas hidráulicas de forjamento de matriz e prensas hidráulicas de forjamento livre. As prensas de forjamento de matriz usam moldes, enquanto as de forjamento livre não usam moldes. A primeira prensa hidráulica de 10.000 toneladas feita na China é uma prensa hidráulica de forjamento livre.
Faixa de aplicação
O processo de conformação hidráulica tem uma ampla gama de aplicações nas indústrias automotiva, de aviação, aeroespacial e de dutos, principalmente para: peças estruturais ocas de seção transversal circular, retangular ou moldada que variam ao longo do eixo do componente, como conexões de tubos moldados para sistemas de escapamento de automóveis; estruturas ocas de seção transversal não circular, como compartimentos de motor, suportes de painel de instrumentos, estruturas de carroceria (representando cerca de 11%-15% da massa de automóveis); peças semelhantes a eixos ocos e conexões de tubos complexas, etc.
Os materiais aplicáveis para o processo de conformação hidráulica incluem aço carbono, aço inoxidável, liga de alumínio, liga de cobre e liga de níquel, etc. Em princípio, todos os materiais aplicáveis à conformação a frio são aplicáveis ao processo de conformação hidráulica. Principalmente para fábrica de autopeças, fábrica de eletrônicos, fábrica de eletricidade, fábrica de tratamento térmico, fábrica de peças de veículos, fábrica de engrenagens, fábrica de peças de ar condicionado.
Operação segura
- Pessoas que não entendam o desempenho estrutural ou os procedimentos operacionais da máquina não devem ligá-la sem permissão.
- A máquina não deve ser revisada e o molde ajustado durante o processo de trabalho.
- Quando for constatado que a máquina apresenta vazamento grave de óleo ou outras anormalidades (como ação não confiável, ruído alto, vibração, etc.), ela deve ser parada para analisar as causas e tentar eliminá-las, e não deve ser colocada em produção com problemas de saúde.
- não deve sobrecarregar ou exceder a distância excêntrica máxima utilizada.
- É estritamente proibido exceder o curso máximo do cursor, a altura mínima de fechamento do molde não deve ser inferior a 600 mm.
- O aterramento dos equipamentos elétricos deve ser sólido e confiável.
- No final de cada dia de trabalho, coloco o controle deslizante na posição mais baixa.
Sistema de Manutenção
- Como óleo de trabalho, recomenda-se usar óleo hidráulico antidesgaste nº 32, nº 46, e a temperatura do óleo deve estar entre 15 e 60 graus Celsius.
- O óleo é rigorosamente filtrado antes de ser adicionado ao tanque de óleo.
- O fluido de trabalho deve ser substituído uma vez por ano, sendo que a primeira substituição não deve exceder três meses.
- O controle deslizante deve ser lubrificado com frequência, a superfície exposta da coluna deve ser mantida limpa com frequência e óleo deve ser pulverizado antes de cada trabalho.
- A excentricidade máxima permitida da carga concentrada é de 40 mm sob pressão nominal de 500T. A excentricidade é muito grande para causar deformação na coluna ou outros fenômenos indesejáveis.
- A cada seis meses, calibre e verifique o manômetro.
- Quando a máquina ficar fora de uso por um longo período, a superfície de cada peça deve ser esfregada e coberta com óleo antiferrugem.
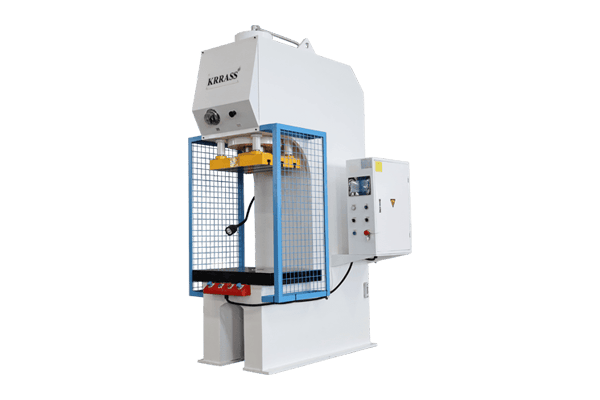
Manutenção Secundária
- Máquinas-ferramentas funcionam 5000 horas para manutenção secundária. Trabalhadores de manutenção como os principais, trabalhadores operacionais para participar. Além da implementação do primeiro nível de conteúdo de manutenção deve fazer o seguinte trabalho, e mapeamento de peças de desgaste, peças de reposição.
- Primeiro desligue a energia para manutenção.
- Guia de coluna de viga transversal: verifique e ajuste o plano de viga transversal de suspensão de linha, guia de coluna, bucha de guia, deslizador, platen, para que possa obter movimento suave e atender aos requisitos do processo. Repare ou substitua peças defeituosas.
- Lubrificação hidráulica: desmonte e limpe, revisando a válvula solenóide, válvula de moagem, carretel. Em seguida, limpe e verifique o êmbolo do cilindro da bomba de óleo, repare a rebarba leve, substitua o retentor de óleo. Em seguida, calibre o manômetro. De acordo com a situação real para reparar ou substituir peças de desgaste sério. Finalmente, dirija para verificar o cilindro de óleo, o êmbolo funcionando suavemente, sem rastejar. A válvula de suporte pode fazer a viga móvel parar em qualquer posição com precisão e a pressão atende aos requisitos do processo.
- Eletricidade: primeiro limpe o motor, verifique os rolamentos e atualize a graxa. Depois repare ou substitua os componentes danificados. Certifique-se de que a parte elétrica atenda aos requisitos do padrão de integridade do equipamento.
- Precisão: Calibre o nível da máquina e verifique e ajuste a precisão do reparo. Certifique-se de que a precisão atenda aos requisitos dos padrões de integridade do equipamento.
Manutenção e manutenção de máquinas hidráulicas ou necessidade de dedicação, profissionalismo e tempo integral para manutenção, para que você possa usá-la por mais tempo!
Falhas comuns
Extrusão de metal prensa hidráulica operação, às vezes haverá parafusos caindo e caindo no cilindro hidráulico para a parede do êmbolo causando arranhões sérios. Depois que o problema ocorre, o método tradicional simplesmente não consegue reparo no local, só pode ser desmontado e transportado para o fabricante para processamento de soldagem de remendo ou substituição de sucata.
Como não há peças de reposição para substituir, o tempo para reproduzir peças ou retornar à fábrica para reparo não pode ser controlado, e o longo tempo de inatividade causa sérias perdas econômicas para a empresa e também paga altos custos de processamento ou reparo. Para atender aos requisitos de produção contínua, é necessário encontrar métodos de manutenção convenientes, simples e eficazes para resolver o problema do equipamento, minimizar o tempo de inatividade e reduzir os custos de reparo e manutenção. O método de compósito de polímero pode ser usado para reparo no local.
Etapas da operação
- Assar peças arranhadas com chama de oxiacetileno (controlar a temperatura para evitar o recozimento da superfície), o vazamento perene de óleo da superfície do metal é cozido, cozido sem faíscas ao redor.
- Tratamento de superfície da parte arranhada com esmerilhadeira angular, profundidade de esmerilhamento de mais de 1 mm, e ao longo da parede externa da ranhura de esmerilhamento do cilindro, preferencialmente ranhura de cauda de andorinha. Perfure mais fundo em ambas as extremidades do arranhão para alterar a força.
- Limpe a superfície com algodão desengordurante embebido em acetona ou etanol anidro.
- Aplique o material de reparo misturado na superfície arranhada; a primeira camada deve ser fina, uniforme e cobrindo toda a superfície arranhada para garantir a melhor ligação entre o material e a superfície metálica; em seguida, aplique o material em toda a área de reparo e pressione-o repetidamente para garantir que o material seja preenchido e atinja a espessura necessária, deixando-o ligeiramente mais alto que a superfície da parede externa do cilindro.
- Leva 24 horas para o material atingir todas as propriedades a 24℃. Para economizar tempo, você pode aumentar a temperatura com uma lâmpada halógena de tungstênio. Para cada aumento de 11℃ na temperatura, o tempo de cura será reduzido pela metade. A melhor temperatura de cura é 70℃.
- Após a cura do material, use uma pedra abrasiva fina ou raspador para reparar o material mais alto que a superfície da parede externa do cilindro, a construção estará concluída.