Índice
Desenvolvimento do Corte a Laser
O desenvolvimento da tecnologia de corte a laser tem sido um avanço significativo nos processos de fabricação e fabricação. Aqui está uma breve visão geral dos principais estágios no desenvolvimento de corte a laser:
Invenção do Laser (década de 1960): O conceito de laser (Amplificação de Luz por Emissão Estimulada de Radiação) foi proposto pela primeira vez por cientistas na década de 1950, e o primeiro laser funcional foi desenvolvido em 1960. Esta invenção inovadora abriu caminho para inúmeras aplicações, incluindo o corte a laser.
Primeiros experimentos (décadas de 1960-1970): Nos primeiros anos da tecnologia laser, pesquisadores conduziram experimentos para explorar suas potenciais aplicações. Os primeiros experimentos de corte a laser envolveram o uso de lasers de CO2 para cortar materiais como metais, plásticos e tecidos.
Adoção Industrial (década de 1980): Na década de 1980, os avanços na tecnologia laser levaram à comercialização de sistemas de corte a laser para aplicações industriais. Os lasers de CO2 surgiram como a escolha preferida para corte a laser industrial devido à sua capacidade de cortar uma ampla gama de materiais com alta precisão e eficiência.
Avanços na tecnologia laser (décadas de 1990-2000): Ao longo das décadas de 1990 e 2000, avanços significativos foram feitos na tecnologia laser, levando a melhorias na velocidade de corte, precisão e versatilidade. Lasers de fibra, que usam fibras ópticas para gerar feixes de laser, surgiram como uma alternativa aos lasers de CO2, oferecendo vantagens como maiores velocidades de corte e menores custos operacionais.
Integração da Tecnologia CNC: A integração da tecnologia de controle numérico computadorizado (CNC) com sistemas de corte a laser revolucionou a indústria. Os controladores CNC permitiram controle preciso sobre o processo de corte, permitindo que formas e designs complexos fossem cortados com facilidade.
Diversificação de Aplicações: À medida que a tecnologia de corte a laser amadureceu, suas aplicações se diversificaram em várias indústrias, incluindo automotiva, aeroespacial, eletrônica, dispositivos médicos e design arquitetônico. O corte a laser se tornou o método preferido para cortar padrões, contornos e protótipos intrincados nessas indústrias.
Avanços em Automação e Robótica: Nos últimos anos, tem havido uma tendência em direção à automação e integração de robótica em sistemas de corte a laser. O manuseio automatizado de materiais, a classificação de peças e o carregamento e descarregamento robóticos aumentaram ainda mais a produtividade e a eficiência em operações de corte a laser.
Tendências emergentes: Olhando para o futuro, os esforços contínuos de pesquisa e desenvolvimento continuam a impulsionar a inovação na tecnologia de corte a laser. As tendências emergentes incluem o desenvolvimento de sistemas de corte a laser híbridos, manufatura aditiva usando deposição a laser e avanços em fontes de laser e óptica para melhor desempenho de corte.
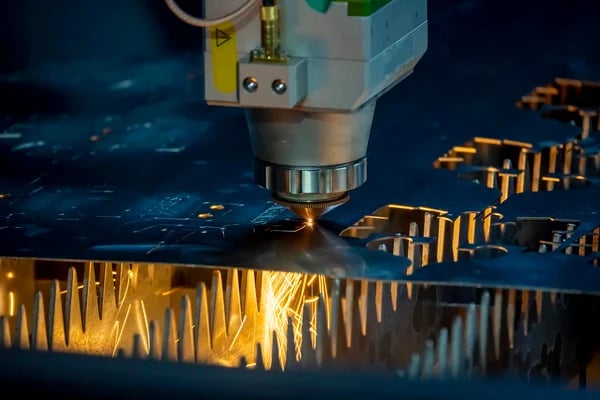
O que é corte a laser e como funciona
Corte a laser usa um laser de alta potência que é direcionado por meio de óptica e controle numérico computadorizado (CNC) para direcionar o feixe ou material. Normalmente, o processo usa um sistema de controle de movimento para seguir um CNC ou código G do padrão que deve ser cortado no material. O feixe de laser focado queima, derrete, vaporiza ou é soprado para longe por um jato de gás para deixar uma borda de acabamento de superfície de alta qualidade.
O feixe de laser é criado pela estimulação de materiais de laser por meio de descargas elétricas ou lâmpadas dentro de um recipiente fechado. O material de laser é amplificado ao ser refletido internamente por meio de um espelho parcial até que sua energia seja suficiente para escapar como um fluxo de luz monocromática coerente. Essa luz é focada na área de trabalho por espelhos ou fibras ópticas que direcionam o feixe por uma lente que o intensifica.
Em seu ponto mais estreito, um feixe de laser normalmente tem menos de 0,0125 polegadas (0,32 mm) de diâmetro, mas larguras de corte tão pequenas quanto 0,004 polegadas (0,10 mm) são possíveis dependendo da espessura do material.
Quando o processo de corte a laser precisa começar em qualquer lugar que não seja a borda do material, é usado um processo de perfuração, em que um laser pulsado de alta potência faz um furo no material, levando de 5 a 15 segundos para queimar uma chapa de aço inoxidável de 13 mm de espessura, por exemplo.
O corte a laser usa um laser de alta potência que é direcionado por meio de óptica e controle numérico computadorizado (CNC) para direcionar o feixe ou material. Normalmente, o processo usa um sistema de controle de movimento para seguir um CNC ou código G do padrão que deve ser cortado no material. O feixe de laser focado queima, derrete, vaporiza ou é soprado para longe por um jato de gás para deixar uma borda de acabamento de superfície de alta qualidade.
O feixe de laser é criado pela estimulação de materiais de laser por meio de descargas elétricas ou lâmpadas dentro de um recipiente fechado. O material de laser é amplificado ao ser refletido internamente por meio de um espelho parcial até que sua energia seja suficiente para escapar como um fluxo de luz monocromática coerente. Essa luz é focada na área de trabalho por espelhos ou fibras ópticas que direcionam o feixe por uma lente que o intensifica.
Em seu ponto mais estreito, um feixe de laser normalmente tem menos de 0,0125 polegadas (0,32 mm) de diâmetro, mas larguras de corte tão pequenas quanto 0,004 polegadas (0,10 mm) são possíveis dependendo da espessura do material.
Quando o processo de corte a laser precisa começar em qualquer lugar que não seja a borda do material, é usado um processo de perfuração, em que um laser pulsado de alta potência faz um furo no material, levando de 5 a 15 segundos para queimar uma chapa de aço inoxidável de 13 mm de espessura, por exemplo.
Tipo de corte a laser
Esse processo pode ser dividido em três técnicas principais: laser de CO2 (para corte, perfuração e gravação) e neodímio (Nd) e neodímio ítrio-alumínio-granada (Nd:YAG), que são idênticos em estilo, com Nd sendo usado para perfuração de alta energia e baixa repetição e Nd:YAG usado para perfuração e gravação de altíssima potência.
Todos os tipos de lasers podem ser usados para soldagem.
Os lasers de CO2 envolvem a passagem de uma corrente através de uma mistura de gás (DC-excitado) ou, mais popularmente hoje em dia, usando a técnica mais nova de energia de radiofrequência (RF-excitado). O método RF tem eletrodos externos e, portanto, evita problemas relacionados à erosão do eletrodo e ao revestimento do material do eletrodo em vidrarias e ópticas que podem ocorrer com DC, que usa um eletrodo dentro da cavidade.
Outro fator que pode afetar o desempenho do laser é o tipo de fluxo de gás. Variantes comuns do laser de CO2 incluem fluxo axial rápido, fluxo axial lento, fluxo transversal e slab. O fluxo axial rápido usa uma mistura de dióxido de carbono, hélio e nitrogênio circulados em alta velocidade por uma turbina ou soprador. Os lasers de fluxo transversal usam um soprador simples para circular a mistura de gás em uma velocidade menor, enquanto os ressonadores de slab ou difusão usam um campo de gás estático que não requer pressurização ou vidraria.
Diferentes técnicas também são usadas para resfriar o gerador de laser e a óptica externa, dependendo do tamanho e da configuração do sistema. O calor residual pode ser transferido diretamente para o ar, mas um refrigerante é comumente usado. A água é um refrigerante frequentemente usado, geralmente circulado por um sistema de transferência de calor ou resfriador.
Um exemplo de processamento a laser resfriado a água é um sistema de microjato a laser, que acopla um feixe de laser pulsado com um jato de água de baixa pressão para guiar o feixe da mesma maneira que uma fibra óptica. A água também oferece a vantagem de remover detritos e resfriar o material, enquanto outras vantagens sobre o corte a laser "seco" incluem altas velocidades de corte, corte paralelo e corte omnidirecional.
Os lasers de fibra também estão ganhando popularidade na indústria de corte de metais. Essa tecnologia usa um meio de ganho sólido em vez de um líquido ou gás. O laser é amplificado em uma fibra de vidro para produzir um tamanho de ponto muito menor do que o obtido com técnicas de CO2, tornando-o ideal para cortar metais refletivos.
As vantagens do corte a laser incluem:
Precisão: O corte a laser oferece altos níveis de precisão e repetibilidade, tornando-o ideal para produzir formas complexas e intrincadas com tolerâncias rigorosas.
Versatilidade: O corte a laser pode ser usado em uma grande variedade de materiais, incluindo metais, plásticos, madeira e muito mais.
Velocidade: O corte a laser é um processo rápido e eficiente, permitindo a produção rápida de peças e componentes.
Desperdício mínimo de material: o corte a laser produz cortes estreitos, resultando em desperdício mínimo de material e maior utilização do material.
Bordas limpas: o corte a laser produz bordas limpas e suaves sem a necessidade de processos de acabamento secundários.
Corte sem contato: como o feixe de laser não toca fisicamente o material, há risco mínimo de danos ou deformação na peça de trabalho.
Automação: Os sistemas de corte a laser podem ser facilmente integrados à automação e à robótica para maior produtividade e eficiência.