A importância das posições focais em corte a laser operações não podem ser exageradas, pois elas impactam diretamente a qualidade, eficiência e precisão do processo de corte. A posição focal se refere ao ponto exato em que o feixe de laser converge para seu menor diâmetro, conhecido como ponto focal. Este ponto é onde o feixe de laser fornece densidade máxima de energia, permitindo um desempenho de corte ideal. Aqui estão várias razões principais que destacam a importância das posições focais em operações de corte a laser:
Focalização do corte a laser
Focalizando feixes de laser
Cada fabricante pode ter sua opinião sobre qual é o elemento mais importante em corte a laser. Você acha que é manter o menor tamanho de ponto e uma orientação de lente perpendicular ao eixo do feixe de laser? Se você respondeu sim, você está parcialmente correto, mas muitos outros fatores precisam ser considerados com relação às propriedades do feixe de laser e aplicações de corte. Manter posições de foco dentro do material é crucial para a repetibilidade dos parâmetros de corte a laser e para produzir qualidade de borda consistente.
Por exemplo, ao lidar com materiais espessos, na verdade é necessário criar um padrão de queima maior para criar um canal mais largo, que é necessário para suportar um volume maior de material fundido que deve ser expelido durante o processo de corte. Para criar esse padrão de queima ampliado, você foca o feixe acima ou abaixo da superfície do material, dependendo do gás auxiliar. Consequentemente, focar um pequeno ponto na superfície normalmente é uma abordagem menos bem-sucedida para materiais mais espessos.
No entanto, para materiais mais finos, um pequeno ponto focado na superfície do material é muito mais eficaz do que um maior, porque envolve menos material e, consequentemente, não é necessário um canal mais largo.
Um fator muito importante a ser considerado com o corte a laser é o uso de um gás auxiliar, como oxigênio, nitrogênio ou ar comprimido. Cada gás tem propriedades específicas relacionadas à aceleração do processo de queima, evacuação do material fundido ou ambos.
No corte a laser, gases auxiliares suportam duas reações específicas: exotérmica ou endotérmica. As regras de foco variam com o tipo de reação e gás usado.

Focalização para reações exotérmicas
Reações exotérmicas são criadas usando um gás que oferece propriedades aceleradoras, como oxigênio. Durante esse tipo de reação, a energia intensa do feixe de laser vaporiza — ou literalmente ferve — o material cortado, pois o oxigênio reage vigorosamente com o material fundido em seu estado líquido. Durante o corte de alta pressão assistido por oxigênio, o material base é levado a uma temperatura tão intensamente alta que a conversão do material em vapor térmico é quase completa.
As regras de foco para dar suporte a reações exotérmicas exigem que as posições de foco estejam acima da superfície para materiais espessos ou logo acima da superfície para materiais mais finos.
Quando o foco está acima do material, você normalmente está usando uma baixa pressão e baixo volume para ajudar a liquefazer e então expelir o material fundido (aproximadamente 6 a 8 libras por polegada quadrada a 40 pés cúbicos por hora). Na verdade, muito pouco do material é vaporizado porque o pequeno volume de oxigênio é incapaz de suportar a vaporização completa. Quando o foco é posicionado apenas na superfície do material, você normalmente está usando uma alta pressão e alto volume (aproximadamente 60 PSI a 80 CFH). Isso é o suficiente para suportar a vaporização vigorosa do material.
É por isso que quando você inspeciona a maioria das mesas de corte onde materiais mais finos são cortados predominantemente, você vê muito pouco material acumulado nos suportes da mesa. Em contraste, mesas de corte usadas para processar materiais mais grossos terão um volume muito maior de material acumulado em seus suportes.
Focalização para reações endotérmicas
Reações endotérmicas, por outro lado, são criadas quando você usa um gás que tem propriedades inertes, ou não reativas. Nitrogênio e argônio entram nessa categoria.
Durante esse tipo de reação, o gás está apoiando apenas a evacuação do material fundido através do canal de corte. O processo endotérmico depende muito da energia bruta do feixe de laser focado para levar o metal base rapidamente a um estado fundido e criar o canal de corte adequado. Isso permite que o gás inerte expulse o material liquefeito através do canal de corte, deixando uma superfície de corte limpo sem aderência de escória.
As regras de foco para dar suporte a reações endotérmicas exigem que as posições de foco estejam na, ou logo abaixo, parte inferior do material. Manter o foco abaixo do material cria um leve formato de V dentro do canal de corte, permitindo que o gás de alta pressão comprima o material fundido através do canal de corte em alta velocidade e o expulse pela base do canal.
Reações endotérmicas requerem alto volume e alta pressão para suportar a rápida evacuação do material fundido. Volumes típicos podem começar em 350 CFH para materiais finos e atingir mais de 3.000 CFH para materiais mais espessos. As pressões podem começar em 140 PSI para materiais finos e aumentar para mais de 300 PSI para os mais espessos.
Usar ar comprimido como gás auxiliar na verdade produz reações endotérmicas e exotérmicas ao mesmo tempo. No entanto, como o volume de ar é composto principalmente de nitrogênio (aproximadamente 78 por cento), é principalmente uma reação endotérmica, com o pequeno volume de oxigênio (cerca de 20 por cento) criando uma reação exotérmica simultânea, mas menor. Isso resulta em fusão mais rápida do material base devido às propriedades reativas do oxigênio. O equilíbrio do ar é principalmente inerte em composição e adiciona apenas à reação endotérmica produzida pelo nitrogênio.
O corte com ar comprimido tem melhores resultados quando a posição do foco é mantida no centro da espessura do material.
Efeitos de feixe bruto
Assim como a intensidade do sol afeta a capacidade da lupa de focar e criar um tamanho de ponto efetivo, o feixe de laser bruto influencia o quão bem você pode focar sua energia e o tamanho do ponto focado resultante. Aqui está a regra geral: quanto maior o diâmetro do feixe bruto, maior o diâmetro da cintura focal resultante e mais longe o ponto focal é projetado da lente.
Outra maneira de alterar o tamanho do ponto efetivamente é usando uma lente com uma distância focal efetiva (EFL) diferente. Isso cria não apenas um tamanho de ponto diferente, mas também uma profundidade de foco (DOF) diferente, conforme ilustrado na Figura 3. Tenha em mente que DOF não é apenas onde o feixe é menor (cintura focal), mas também inclui um intervalo logo antes e depois do menor tamanho de ponto.
Como exemplo de alteração do tamanho do ponto e da DOF, considere um feixe de laser de CO2 com comprimento de onda de 10.600 nm, diâmetro bruto do feixe de 20 mm e M2 de 2. Se passarmos esse feixe por uma lente de 3,75 polegadas (95,25 mm), o diâmetro na cintura focal seria de aproximadamente 128 mícrons (0,128 mm). Agora, se substituirmos uma lente de 5 pol. (127 mm), usando o mesmo feixe bruto de 20 mm, o diâmetro na cintura focal seria de 170 mícrons (0,170 mm). Ao mesmo tempo, ocorreria uma alteração na profundidade de foco entre as duas lentes. A lente de 3,75 pol. teria uma DOF de aproximadamente 1,2 mm, em comparação com uma DOF de 2,16 mm para a lente de 5 pol.
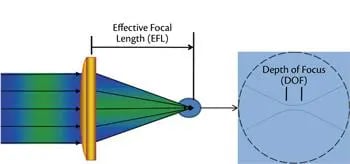
Outra consideração que pode alterar a projeção do ponto focal do feixe é uma mudança na frente de onda do feixe antes que ele atinja a lente. A frente de onda do feixe bruto pode ser descrita como convergente, paralela ou divergente. No caso de uma frente de onda convergente, o feixe está essencialmente ficando menor à medida que viaja. À medida que essa frente de onda convergente atinge a lente, a projeção de foco resultante é mais curta do que a de uma frente de onda paralela devido à projeção de diâmetro de feixe menor no topo da lente. Por outro lado, focar uma frente de onda divergente resulta em uma projeção de ponto focal mais longa do que a de uma frente de onda paralela devido ao diâmetro de feixe maior projetado na superfície superior da lente.
Aplicações do mundo real
É importante controlar todos os aspectos relacionados à manutenção das projeções de ponto de foco adequadas. Você deve garantir que o feixe bruto no ressonador óptico esteja em boas condições e que o feixe esteja sendo entregue corretamente à lente. Usar a lente de distância focal adequada pode alterar a taxa na qual o material é derretido e a espessura que pode ser processada. Uma lente de distância focal curta, como uma EFL de 3,75 pol., é mais eficaz até uma espessura máxima de calibre 12 ou 0,104 pol. Uma lente de 5 pol. é mais eficaz até uma espessura máxima de 0,250 pol. Para materiais mais espessos, use uma lente de 7,5 pol. até um máximo de 1,25 pol. e uma lente de 10 pol. até um máximo de 1,312 pol. para obter o corte mais eficaz.
Uma prática genuína de economia de tempo é usar uma EFL que permite cobrir a maior parte da sua produção diária sem ter que mudar para uma lente diferente. O uso de uma lente de 7,5 pol. permitirá, na maior parte, que você alcance todos os objetivos relacionados à manutenção do foco adequado, de espessuras de 16 ga. a 1 pol., ao longo do curso de um dia de produção.
Como mencionado antes, escolher o gás de assistência tem muito a ver com como sua posição focal será determinada dentro do material. O corte a laser assistido por oxigênio (exotérmico) exigirá que as posições de foco estejam apenas na superfície ou acima da superfície do material. Muito poucas mudanças focais são necessárias, a menos que você esteja mudando de corte de alta pressão para corte de baixa pressão porque o foco está sempre na superfície do material ou próximo a ela e, consequentemente, não é afetado por mudanças na espessura do material. Por outro lado, o corte a laser assistido por nitrogênio (endotérmico) é muito dependente do foco com base na espessura do material a ser processado porque o foco está na parte inferior do material ou próximo a ela.
Em ambos os casos, todos os pontos focais básicos podem ser satisfeitos utilizando um dispositivo CNC de foco automático, como um espelho adaptável.
Um espelho adaptativo funciona alterando o formato da superfície do espelho por meio da aplicação de pressão na parte de trás do espelho. Em seu estado normal, sem pressão aplicada, a superfície do espelho adaptativo é côncava. Conforme a pressão é aplicada ao espelho, a superfície muda de côncava para plana e, então, para convexa. Alterar o formato do espelho altera a frente de onda do feixe e, consequentemente, altera o tamanho do feixe na lente e onde a posição focal é projetada dentro do material.
Outro grande benefício do foco automático é a capacidade de alterar a posição focal dinamicamente durante o processo de perfuração, o que permite a entrada máxima de energia dentro da espessura do material e reduz o tempo geral de perfuração.
Avanços em tecnologias de corte a laser que servem para melhorar o rendimento e a produtividade continuam até hoje. O que continua muito crítico, no entanto, é a entrega do feixe bruto para a lente e a manutenção das posições focais adequadas, com base na aplicação.
Se a posição focal adequada e as formas de projeção forem mantidas dentro do material a ser processado, o restante dos requisitos necessários para produzir um corte consistente e de alta qualidade serão minimizados. Isso economiza tempo de configuração, mantendo produtividade e rendimento consistentes.