Índice
Introdução
No domínio da engenharia mecânica e de chapas metálicas, a pressione o freio é uma ferramenta essencial para transformar chapas metálicas em formas e designs complexos.
Esta máquina potente pode realizar dobras e dobras precisas, mudar completamente a indústria e criar produtos em massa que vão desde raquetes simples até componentes mecânicos complexos.
No entanto, ele também tem restrições. Sua série de vantagens e desvantagens específicas deve ser levada em consideração quando os fabricantes equilibram seu uso.
Nossa passagem tem como objetivo mergulhar no mundo das máquinas de dobra para explorar seus prós e contras, fazendo com que você entenda a máquina de forma abrangente na indústria de chapas metálicas.
Compreensão da prensa dobradeira
Definição
UM pressione o freio é uma máquina especialmente projetada para dobrar chapas metálicas, também um dos dispositivos indispensáveis para a indústria de chapas metálicas.
Principais componentes e funções
A estrutura e a base são os fundamentos da máquina de dobra. Elas são feitas de aço pesado e suportam a força produzida no processo de dobra. A base é uma superfície horizontal na qual a peça de trabalho é colocada. E a estrutura suporta o carneiro e a matriz.
O carneiro e a matriz são peças essenciais de uma máquina de dobrar
. O carneiro é uma peça que se move verticalmente, que deixa pressão na peça de trabalho e a faz dobrar ao redor da matriz. A matriz é uma ferramenta trocável projetada para garantir o ângulo e os parâmetros da prensa dobradeira.
O calibre traseiro também é uma parte importante da prensa dobradeira, que garante a localização precisa da peça de trabalho a ser dobrada. Ele é composto de muitos dedos de parada alinhados com linhas curvas e guia a peça de trabalho para o local correto. O calibre traseiro pode ser ajustado manualmente ou automaticamente para acomodar diferentes tamanhos de dobra.
A principal função do controlador inclui parâmetros de dobra, monitoramento de pressão e garantia de que a máquina opere dentro de suas especificações.
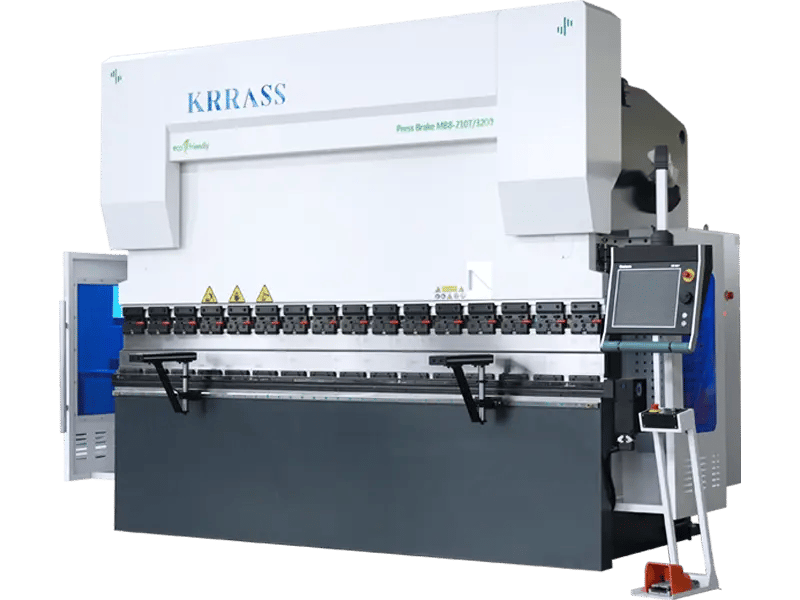
Tipos principais
Máquina de dobrar mecânica
Este é o tipo mais comum de prensa dobradeira. O mecanismo é operado pelos motores elétricos dentro delas.
O motor oferece energia ao volante e gira o volante grande em alta velocidade. O operador controla o volante por meio da embreagem.
A prensa dobradeira mecânica é simples de operar, especialmente em equipamentos eletrônicos. Ela torna a manutenção e a operação mais fáceis.
Uma vez que o carneiro esteja conectado, ele deve passar por todo o processo. Se o curso do portão for muito grande, o freio de prensa pode ser travado, o que é um risco potencial.
Prós: baixo custo, fácil operação
Contras: restrições de precisão, potência e controle
Máquina de dobrar hidráulica
A máquina de dobra hidráulica usa um mecanismo hidráulico para empurrar o cilindro de óleo para baixo em vez de uma configuração mecânica.
Ele pode ser equipado com vários cilindros, o que proporciona muita conveniência para os operadores controlarem o cotovelo, alcançando assim uma dobra altamente personalizada e precisa.
Comparada com a prensa dobradeira mecânica, a prensa dobradeira hidráulica oferece dobra mais precisa e melhor controle.
Pode ser facilmente ajustado para se adaptar a várias espessuras de metal e obter curvatura intrincada em movimento constante. Geralmente é mais caro, mas é popular devido ao seu maior desempenho e versatilidade.
Prós: maior precisão, controle e força, e se adapta a vários materiais
Contras: alto custo, operação mais complexa e não pode exceder sua tonelagem nominal
Prensa dobradeira CNC
A máquina CNC é altamente personalizada e precisa e é controlada por tecnologia de computador para melhorar a eficiência e a precisão do controle.
Os operadores qualificados podem inserir dados como ângulo de curvatura, espessura da folha e largura no controlador para controlar a máquina.
Prós: alta precisão e exatidão, fácil operação e manuseio de vários formatos e ângulos
Contras: alto custo, limitações com materiais altamente refletivos ou quebradiços
Vantagens e desvantagens da prensa dobradeira
Vantagens
A máquina de dobrar apresenta muitas vantagens, tornando-a indispensável para a indústria de chapas metálicas. E desempenha um papel fundamental na indústria de chapas metálicas.
Fácil operação: a prensa dobradeira é um dos dispositivos mais simples. Comparado com outras máquinas, não requer operadores altamente qualificados.
Alta precisão: precisão é a chave para o manuseio de metais. A prensa dobradeira pode oferecer maior precisão em comparação com outras máquinas de dobra de metal porque usa um punção e matrizes para formar o metal, alcançando a dobra do metal em um ângulo preciso.
Mais flexível: comparada com outras máquinas, a máquina de dobrar pode dobrar pequenos componentes e grandes massas de metais. Ela apresenta grande flexibilidade em várias aplicações devido à sua compatibilidade com vários tamanhos de chapas metálicas.
Melhore a produtividade: a prensa dobradeira é mais eficiente do que outros métodos de dobrar metais. Ela pode dobrar muitos metais de uma só vez, melhorando assim a produtividade.
Reduza o desperdício de material: comparado a outros dispositivos, a prensa dobradeira oferece alta precisão e exatidão. Isso significa menos desperdício de material, tornando-a mais eficiente e econômica.
Baixo custo: o custo da matriz usada pela prensa dobradeira é relativamente baixo, mas tem uma longa vida útil, o que aumenta a acessibilidade econômica no processo de conformação e dobra de chapas metálicas.
Segurança melhorada: a prensa dobradeira é mais segura do que outros métodos de dobra de metal. Porque não há necessidade de aquecer o metal antes de dobrar, diminuindo assim o risco de ferimentos. A prensa dobradeira moderna é equipada com muitas medidas de proteção, como sensores a laser. Quando o operador se machuca, os sensores interrompem o processo de operação do metal.
Versatilidade: a prensa dobradeira moderna pode lidar com muitos formatos de cotovelos. Além disso, ela pode dobrar diferentes espessuras de chapas de metal.
Usado para prototipagem: Uma vantagem fundamental das prensas dobradeiras é a facilidade de configuração e troca de ferramentas, permitindo trocas rápidas e testes de diferentes designs e formatos durante a prototipagem.
Tecnologia inteligente: a prensa dobradeira CNC oferece soluções avançadas de resolução automática para dobra de metais, o que torna a prensa dobradeira moderna uma tecnologia muito inteligente.
Coroamento: ao dobrar uma peça longa, pode haver um desvio perceptível entre os ângulos de formação no meio e nas laterais, causando ângulos de dobra desiguais. No entanto, a prensa dobradeira apresenta uma função de coroamento para ajustar cada local do ângulo, garantindo a dobra da linha e diminuindo a necessidade de ajuste e manutenção manuais.
Desvantagens
Alto custo inicial: a prensa dobradeira precisa de investimento inicial em massa devido à compra e manutenção. Além disso, a máquina requer equipamento especializado e treinamento, o que pode aumentar o custo inicial de configuração da operação da máquina. Ela precisa de mais energia e pode melhorar o custo da operação aparentemente. A prensa dobradeira com automático é cara, o que pode reduzir a pequena empresa a pedir modelos de ponta.
Requer alta pressão: a máquina de dobrar precisa de alta pressão para operar. Isso significa que a prensa dobradeira pode não ser adequada para materiais finos, pois a alta pressão pode causar deformação do material. Além disso, a alta pressão é perigosa. A prensa dobradeira deve ser operada por operadores qualificados para uso, portanto, os riscos potenciais podem ser reduzidos.
Restrito a geometrias simples: As prensas dobradeiras também são limitadas nas geometrias que podem criar. Embora possam criar dobras simples, não podem criar formas mais complexas, como curvas ou espirais. Assim, se formas geométricas complexas precisam ser criadas, métodos diferentes podem ser necessários, como estampagem ou hidroformação.
Precisa de treinamento profissional: a máquina pode ser operada com segurança e eficácia por treinamento profissional. O operador deve receber treinamento adequado para saber o princípio de funcionamento da máquina e como ajustar o material corretamente. Além disso, os operadores devem saber os riscos relacionados a operações de alta pressão e como escapar de ferimentos.
Necessidade de espaço: a máquina tem tamanhos grandes, portanto, mais área de oficina deve ser reservada para a colocação da máquina.
Barulho: pode haver alguns ruídos produzidos quando a prensa dobradeira é operada. Assim, o operador precisa de um dispositivo de proteção auricular. Além disso, pode causar vibração no local de trabalho.
Manutenção: a máquina precisa de manutenção regular e deve ser limpa com frequência para garantir a qualidade dos produtos.
Risco de quebra durante a dobra: durante o processo de dobra, as bordas e cantos do material desenvolverão rebarbas ou camadas de óxido, o que pode fazer com que o material rache ou quebre durante o processo de dobra.
Conclusão
Em poucas palavras, uma máquina de dobrar é uma excelente ferramenta para fabricação de precisão, exatidão e baixo custo de mão de obra.
Considere as vantagens e desvantagens da prensa dobradeira antes de usar esta máquina para atender às suas necessidades de fabricação. Assim, você pode fazer uma escolha inteligente para satisfazer as necessidades do seu negócio.