O que é Press Brake U Bend
Pressione o freio A dobra em U se refere a um processo no qual a chapa de metal será dobrada constantemente na prensa dobradeira duas ou mais vezes para ser moldada no formato de “U”.
Esse processo é obtido por meio do controle preciso dos graus de fechamento das matrizes superiores e inferiores e dos cursos para atender ao tamanho e ângulo precisos dos requisitos do projeto.
A curva em U é uma das técnicas de conformação mais comuns nas indústrias de fabricação de metais.
A curva em U é essencial em vários setores, como fabricação de metais e engenharia mecânica.
É amplamente utilizado na produção de peças arquitetônicas e estruturais, peças automotivas, carcaças de eletrodomésticos e fabricação de projetos que exigem espaço interno, como sistemas de tubulação e gabinetes elétricos.
A curva em U não só pode economizar custos de material e melhorar a eficiência da produção, mas também garantir boas propriedades mecânicas e qualidade de aparência dos produtos.
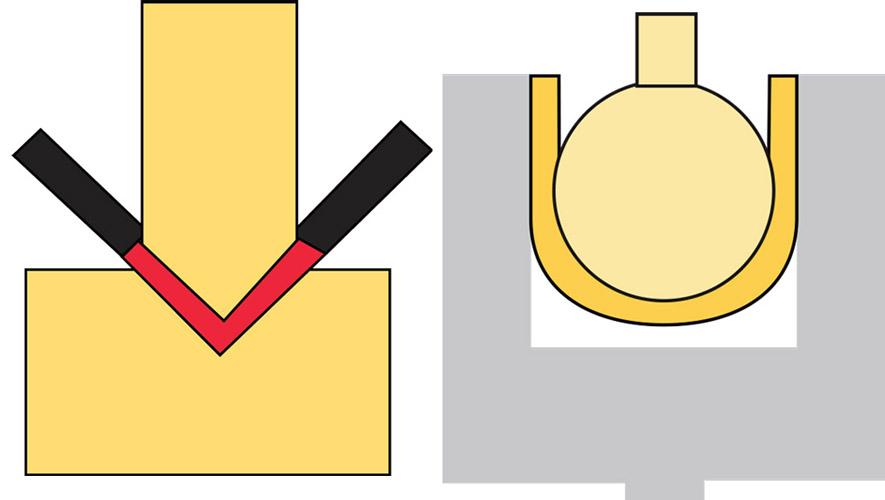
História e evolução da tecnologia de prensa dobradeira
O pressione o freio é considerado um equipamento essencial para conformação de chapas metálicas, e sua história pode ser datada do início da industrialização.
A prensa dobradeira manual inicial depende da força de trabalho, o que apresenta operação complexa e baixa eficiência.
Com o avanço da tecnologia, a tecnologia hidráulica e CNC melhoram significativamente o desenvolvimento da prensa dobradeira, tornando a máquina capaz de realizar dobras precisas e complexas, incluindo dobras em U.
A tecnologia de dobra em U é constantemente atualizada com a evolução da tecnologia de prensa dobradeira, que varia da simples dobra em linha reta à dobra tridimensional.
Não apenas alcançando ângulo de curvatura e precisão aparentemente melhorados, mas também realizando dobra automática constante em sequência de várias etapas.
As modernas prensas dobradeiras CNC podem até ser integradas com software CAD/CAM, imitando e controlando com precisão a curva em U geral, alcançando projetos de alta precisão e produção em massa.
Além disso, a técnica de matriz e as ferramentas auxiliares, como o medidor traseiro e o dispositivo de suporte frontal, também enriquecem e melhoram ainda mais a possibilidade e a adaptabilidade da curva em U.
Aspectos técnicos
Tipos de dobradeiras para dobra em U
Prensa dobradeira mecânica:
Prós: estrutura simples, desempenho de alto custo, manutenção conveniente, operação intuitiva, adequado para pequena escala ou ocasiões que exigem menos precisão.
Contras: provavelmente não consegue realizar um controle preciso sob alta tonelagem devido às restrições de suas vias de movimento. Além disso, tem menor eficiência de trabalho do que os tipos hidráulicos e não é adequado para produção em massa e constante.
Prensa dobradeira hidráulica:
Prós: o sistema hidráulico oferece pressão estável e intensa, que pode ser adaptada para dobra precisa com múltiplas espessuras de materiais. Ele também pode ser ajustado sem níveis em uma faixa mais extensa, adequado para produção em massa e indústrias que exigem alta precisão.
Contras: o equipamento é complexo e requer manutenção regular para operação regular. Seus custos de manutenção inicial e posterior são relativamente altos.
Materiais adequados para curvas em U
Conhecer as propriedades físicas e mecânicas dos diferentes tipos de materiais metálicos é essencial para o projeto e a implementação precisos do processo de dobra em U, o que é benéfico para evitar problemas de qualidade do produto devido ao uso inadequado de materiais.
Aço de baixo carbono: apresenta boa plasticidade de intensidade moderada, é fácil de dobrar e é um dos materiais mais comuns para produção de curvas em U.
Aço inoxidável: é bom, resistente à corrosão e decorativo. Requer cálculo preciso e controle dos parâmetros de deformação durante a flexão devido à alta intensidade e propriedades de retorno elástico.
Alumínio: tem baixa densidade e boa condutividade elétrica e térmica, tornando-o adequado para peças leves. Quando dobrado, você deve levar em consideração as propriedades de forte ductilidade e pequeno módulo elástico para evitar o rebote excessivo e influenciar a qualidade do produto.
Liga de cobre: apresenta boa condutividade elétrica e resistência à corrosão. Devido à sua alta solidez, deve ser processada com matrizes e condições de processo adequadas.
Considerações de projeto para curvas em U
Raio de curvatura: geralmente é maior que um certo múltiplo da espessura do material para evitar a geração de trincas ou tensões internas excessivas durante a dobra, garantindo a integridade da estrutura da peça.
Ângulo de curvatura: determina o formato final da peça. É calculado de acordo com os requisitos de design do produto e o efeito spring-back, compensando e chegando ao tamanho geométrico antecipado.
Força de flexão: é determinada por muitos fatores, como espessura do material, raio de flexão e comprimento. Pressão muito grande ou muito pequena pode levar a problemas de qualidade. Assim, ferramentas de cálculo profissionais e fórmulas empíricas são necessárias para garantir o valor de pressão adequado.
III. Guia Prático
Guia passo a passo para executar uma flexão em U
Escolha a prensa dobradeira e matrizes adequadas: escolha a prensa dobradeira mecânica ou hidráulica com base no tipo e espessura do material. Escolha a matriz superior e inferior apropriadas de acordo com o tamanho e o formato do u-bend necessários.
Preparação do material: meça e corte a chapa de metal no tamanho necessário.
Defina os parâmetros da máquina: defina a força de dobra, a velocidade e os parâmetros de ângulo razoáveis de acordo com a espessura do material e o raio de curvatura.
Operar a dobra: coloque a chapa metálica na prensa dobradeira, certifique-se de que ela esteja no meio da matriz e dobre-a de acordo com os parâmetros definidos.
Verifique e ajuste: monitore a deformação do material, verifique a precisão do tamanho e ângulo e ajuste a tempo a pressão e o ângulo para compensar o efeito de retorno elástico. Após a dobra inicial de um ou dois lados, realize a outra parte da dobra de acordo com os mesmos procedimentos.
Técnica: use ferramentas de medição precisas para verificar a posição da matriz e o ajuste do ângulo várias vezes.
Quanto a peças complexas em formato de U, o método de formação passo a passo pode ser aceito. Dobre uma pequena seção de cada vez e mantenha a seção constante e consistente.
Desenvolva procedimentos operacionais padronizados, proceda rigorosamente e melhore a proficiência operacional por meio da prática repetida.
Erros comuns e como evitá-los
A escolha inadequada de matrizes e a configuração imprecisa da folga das matrizes causarão um efeito de dobra ruim ou danos à peça de trabalho.
Se a força de flexão for muito grande ou muito pequena, isso resultará na quebra do material. O retorno elástico é muito grande, o que afetará a precisão do produto.
O posicionamento e a fixação inadequados do material causarão deslocamento durante o processo de dobra.
Existem algumas abordagens de precauções baseadas nas perguntas acima:
Obedeça rigorosamente o manual de operação, escolha a matriz integrada com a experiência prática, verifique regularmente e ajuste a folga da matriz.
Calcule a força de flexão de acordo com as propriedades e espessura do material, e também leve em consideração a mola de retorno, aumentando adequadamente o volume de compensação.
Melhore o treinamento do operador e melhore a precisão de fixação e posicionamento do material.
Manutenção e cuidados com máquinas de dobradeira
Manutenção diária
Limpe regularmente os detritos internos e externos da prensa dobradeira, certifique-se de que o sistema de lubrificação esteja suave e complemente ou substitua o óleo de lubrificação em tempo hábil.
Verifique as propriedades de vedação do sistema hidráulico para evitar vazamento de óleo, garantindo que os componentes hidráulicos funcionem corretamente.
Manter e verificar o sistema de controle elétrico, garantindo que os componentes funcionem de forma estável e segura.
Verifique a situação de abrasividade da matriz, retificando, reparando ou substituindo as novas matrizes quando necessário.
Estratégias de manutenção de longo prazo
Desenvolva um plano detalhado de manutenção do equipamento, verifique e repare regularmente para evitar possíveis maus funcionamentos.
Estabeleça o registro de uso e acompanhe a condição de operação do equipamento para oferecer evidências para manutenção posterior.
Aumente a conscientização dos funcionários sobre a importância da manutenção do equipamento e desenvolva um bom hábito de operação para prolongar a vida útil da prensa dobradeira e a eficiência de trabalho.
Aplicações industriais
Curvas em U em várias indústrias
Indústria automobilística
Na fabricação de automóveis, a curva em U é amplamente usada na produção de dutos de sistema de exaustão, componentes de suspensão e peças estruturais da carroceria. Ela é rigorosa quanto ao material escolhido, à precisão do processo de curvatura e à durabilidade dos produtos porque esses componentes geralmente precisam suportar alta temperatura, alta pressão e vibração.
Indústria aeroespacial
A indústria aeroespacial tem requisitos extremamente altos para leveza e alta resistência. O processo de curvatura em U é geralmente usado em sistemas de fornecimento de combustível de aeronaves, estruturas de estrutura de fuselagem e outros layouts de tubulação interna, garantindo que cada parte possa atender a padrões fortes e atingir metas de perda de peso.
Indústria da arquitetura
No setor de construção, tubos ou aço em formato de U são amplamente utilizados em suporte de estruturas, sistemas de exaustão, tubulações de HVAC, etc. Especialmente na arquitetura de estruturas de aço, vigas em formato de U pré-dobradas podem melhorar a eficiência de trabalho e a estabilidade da estrutura, o que é conveniente para montagem pontual.