UM V sulco, também conhecida como máquina de ranhura em V ou Cortador de ranhura em V, é uma ferramenta especializada usada em trabalhos de chapa metálica para criar ranhuras ou entalhes precisos em forma de V ao longo da superfície de uma chapa metálica. Essas ranhuras são comumente usadas para vários propósitos, como dobrar, dobrar, soldar ou propósitos decorativos.
A fabricação de chapas metálicas é um aspecto essencial do processamento mecânico, particularmente em indústrias como aviação, eletrodomésticos, automóveis, elevadores e outras. Peças de chapas metálicas são amplamente utilizadas nessas indústrias.
A dobra é um dos processos mais cruciais na fabricação de chapas metálicas e é considerado um único processo de conformação.
Técnica de ranhura em V
A qualidade do processo de dobra afeta significativamente o tamanho e a aparência do produto final.
Portanto, garantir as dimensões e os ângulos de conformação da peça durante o processo de dobra é uma área crucial de pesquisa em tecnologia de dobra.
À medida que a economia se desenvolve e os padrões de vida das pessoas melhoram, suas atividades sensoriais se tornam mais elevadas.
Quanto mais complexo for o formato das decorações em chapa metálica, mais ele refletirá o nível de habilidade e o estilo moderno do designer, atraindo assim a atenção da maioria dos clientes.
Além disso, a peça de trabalho deve atender a requisitos técnicos, como ter um raio de arco circular mínimo na borda de dobra, nenhuma marca de dobra na superfície e nenhuma reentrância na superfície decorativa.
A máquina dobradeira tradicional não conseguiu atender a requisitos técnicos específicos, levando ao surgimento da tecnologia de dobra por ranhuras em chapas metálicas.
Este artigo se concentra nas características da técnica de ranhuramento, métodos para ranhurar chapas metálicas e maneiras de garantir precisão em tamanho e ângulo durante o processo de dobra.
Métodos tradicionais de dobra e suas limitações
O método tradicional de dobra na fabricação de chapas metálicas envolve o uso de pressão das matrizes superior e inferior de uma máquina de dobradeira.
A chapa metálica é dobrada através da abertura da matriz inferior e da borda superior da matriz superior.
A placa metálica sofre uma transformação de deformação elástica para deformação plástica.
O ângulo de curvatura é determinado pela profundidade da matriz superior na matriz inferior, e o raio de curvatura (R) deve ser maior ou igual à espessura da placa (t), conforme mostrado na Figura 1.
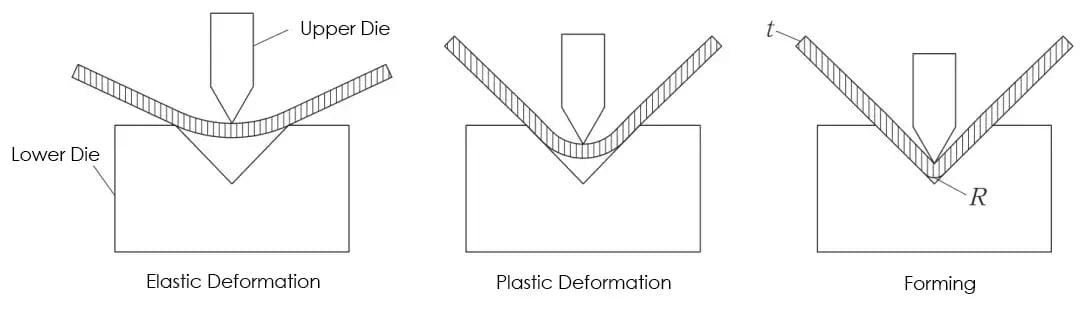
No entanto, as demandas atuais por formas de peças de trabalho estão se tornando cada vez mais altas. Para algumas peças com formas complexas (como mostrado na Figura 2), as técnicas tradicionais de dobra são insuficientes, e o método tradicional não consegue controlar o raio de dobra, tornando desafiador atender aos requisitos técnicos para dobra sem indentação.
Como resultado, surgiu uma nova técnica de dobra chamada dobra de ranhura.
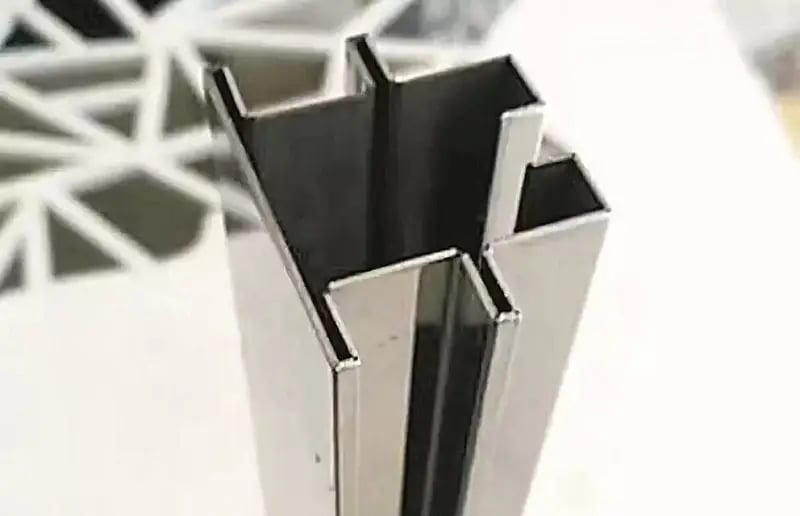
Características da dobra de ranhuras
Vamos começar definindo o que é dobra de ranhura.
A dobra de ranhuras é uma técnica que usa uma máquina de ranhuras para criar uma linha de ranhuras em V na chapa metálica que precisa ser dobrada e, em seguida, dobrá-la em uma prensa dobradeira para atender a requisitos específicos.
As principais características do processo de dobra de ranhuras são as seguintes:
Pequeno raio de arco e sem marcas de curvatura na peça de trabalho
O raio máximo do arco da borda da peça de trabalho é diretamente proporcional à espessura da chapa após a dobra. Quanto mais espessa a chapa, maior o raio do arco.
No entanto, após ranhurar a chapa metálica em V, a espessura restante se torna metade da original, ou até menor. Isso reduz significativamente o raio do arco após a dobra.
Além disso, a espessura reduzida no ponto de dobra após a ranhura reduz a força de deformação durante a dobra, o que não afeta a área não dobrada. Isso resulta em nenhuma marca de dobra na superfície da peça de trabalho após a dobra.
Essa técnica pode atender aos requisitos técnicos de ter um pequeno raio de arco, sem marcas de curvatura e sem entalhes em superfícies decorativas em ambientes de alto padrão, como hotéis, bancos, centros comerciais e aeroportos.
Reduzindo a tonelagem necessária para dobrar chapas em uma prensa dobradeira
No processo de dobra, a força necessária para dobrar a chapa metálica é proporcional à sua espessura. Quanto mais espessa a chapa metálica, maior a força de dobra necessária e maior a tonelagem necessária na prensa dobradeira.
No entanto, ao ranhurar a parte de dobra da chapa metálica antes da dobra, a espessura restante é significativamente reduzida. Essa redução na espessura reduz correspondentemente a força de dobra necessária, permitindo que a chapa seja dobrada em uma máquina de dobra com uma tonelagem menor.
Isso não só reduz o custo do equipamento como também economiza energia e espaço.
Dobrando peças de trabalho com formas complexas e controlando a resiliência
A peça mostrada na Figura 2 não pode ser dobrada e moldada em uma máquina de dobra padrão, mas isso pode ser feito manualmente após ranhurar um formato em V no ponto de dobra.
Além disso, o controle da espessura restante da folha pode ser usado para gerenciar a força de retorno da mola e o ângulo.
Se a espessura restante da placa após a ranhura for mantida em torno de 0,3 mm, o ângulo de retorno elástico pode ser reduzido significativamente, e o retorno elástico pode ser essencialmente ignorado.
Método de ranhura em V
Na produção de chapas metálicas, a plaina de pórtico e a máquina de ranhurar chapas metálicas são comumente usadas para criar ranhuras em forma de V na chapa metálica.
Máquina de ranhurar V CNC horizontal RGHK-1500x4000
Posicione a placa dobrada na máquina de ranhurar para alinhamento e insira a espessura da placa para ranhuramento automático.
Durante o processo de ranhuramento, deve-se prestar atenção aos dois aspectos a seguir.
Profundidade da ranhura e espessura restante
Em uma determinada espessura de chapa, a profundidade da ranhura e a espessura restante têm uma relação correspondente.
De acordo com os requisitos da técnica de dobra, um valor de espessura residual é definido, que normalmente é definido em 0,8 mm por padrão e não deve ser inferior a 0,3 mm no mínimo.
Em seguida, o número de ranhuras e a profundidade das ranhuras são definidos com base na espessura da placa.
Para controlar rebarbas no metal e proteger as facas, o avanço das facas não deve ser excessivo.
Normalmente, a profundidade da primeira ranhura não pode exceder 0,8 mm e o processo de ranhura deve ser realizado em pelo menos dois cortes. Um corte não é apropriado.
Por exemplo, ao ranhurar uma chapa de aço inoxidável de 1,2 mm de espessura, a espessura restante após a ranhura é de 0,5 mm.
Se o primeiro avanço de ranhura for definido em 0,5 mm e o segundo avanço de ranhura em 0,2 mm, a espessura restante da chapa será de 0,5 mm com rebarba metálica mínima, conforme mostrado na Figura 3.
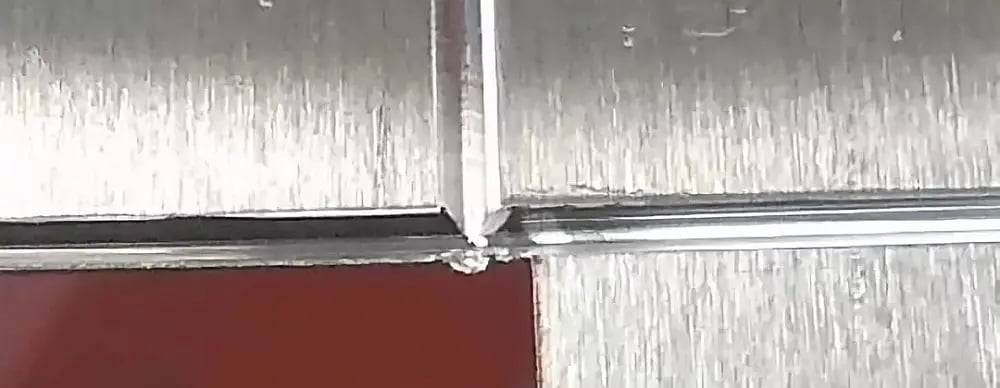
A configuração do ângulo de ranhura
Sabe-se pelo processo de dobra que a chapa metálica sofre vários graus de deformação elástica durante a dobra, levando a desvios no ângulo de dobra.
O processo de ranhura em V pode ser realizado corretamente garantindo que o ângulo de ranhura corresponda ao ângulo de curvatura necessário da peça de trabalho.
Normalmente, o ângulo de ranhura em V é 1-2° maior que o ângulo de curvatura.
Por exemplo, ao dobrar uma peça de trabalho em um ângulo de 90°, o ângulo de ranhura em V pode ser definido como 92° (veja a Figura 4).
Dessa forma, o erro de ângulo causado pelo retorno elástico durante a flexão pode ser efetivamente resolvido (veja Figura 5).
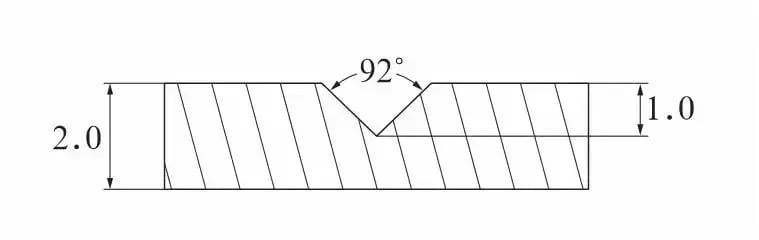
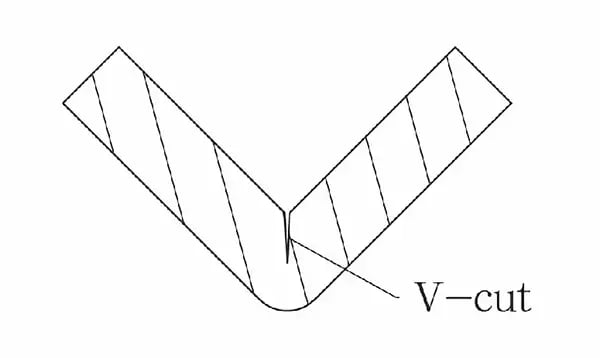
Seleção de facas de ranhura e configuração de quantidade
Tipos e seleção de facas de ranhurar
Os tipos de facas de ranhura são classificados principalmente em facas de ranhura de ângulo superior rômbico, facas de ranhura quadradas, facas de ranhura triangulares e facas de ranhura circulares, entre outras (ver Figura 6).
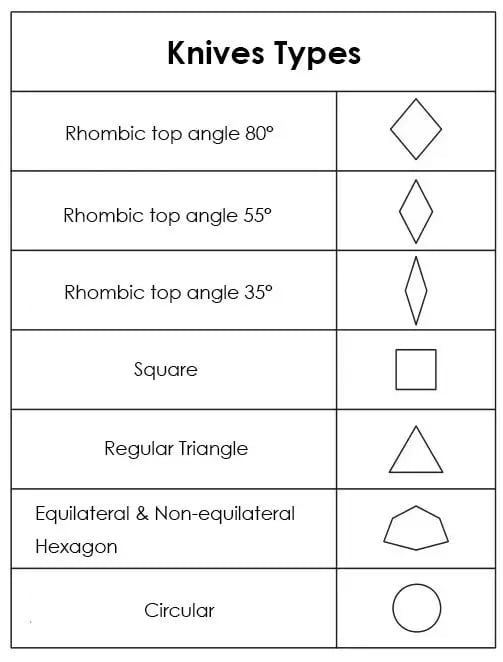
Facas apropriadas podem ser selecionadas com base no formato e no ângulo da ranhura em V.
Ao formar uma ranhura em V padrão, o ângulo das facas deve ser menor que o ângulo da ranhura em V.
Por exemplo, se o ângulo da ranhura em V estiver entre 45° e 60°, devem ser usadas facas rômbicas com ângulo superior de 35°.
Para ranhuras em V entre 60° e 80°, facas de ranhura triangulares são a opção preferida.
Ao fazer ranhuras em V entre 80° e 90°, devem ser utilizadas facas rômbicas com ângulo superior de 80°.
Se o ângulo de ranhura em V for maior que 90°, facas quadradas são a escolha recomendada.
Além disso, facas circulares devem ser usadas para ranhurar formas redondas.
A configuração da quantidade de facas
Ao ranhurar folhas longas de metal com uma profundidade grande, usar continuamente apenas uma faca pode levar a danos por calor excessivo. Isso também pode resultar em baixa qualidade de ranhura, aumento de rebarbas de metal e outros problemas.
Por exemplo, ao ranhurar uma placa de aço inoxidável de 2 m de comprimento com 2 mm de profundidade, definir a quantidade inicial de avanço da faca para 0,5 mm e ranhurar continuamente fará com que a faca gere muito calor e fique macia, resultando em diminuição da qualidade da ranhura após 1,5 m e maior tamanho de rebarba.
Se a quantidade de avanço da faca for definida como 0,2 mm, serão necessários 10 ciclos de ranhura para concluir a chapa de metal de 2 mm, o que afeta muito a eficiência da fabricação.
Portanto, ao ranhurar chapas mais longas, é importante considerar não apenas a quantidade de avanço da faca, mas também o número de facas trabalhando simultaneamente.
Normalmente, 3 a 4 facas são usadas ao mesmo tempo (veja Figura 7).
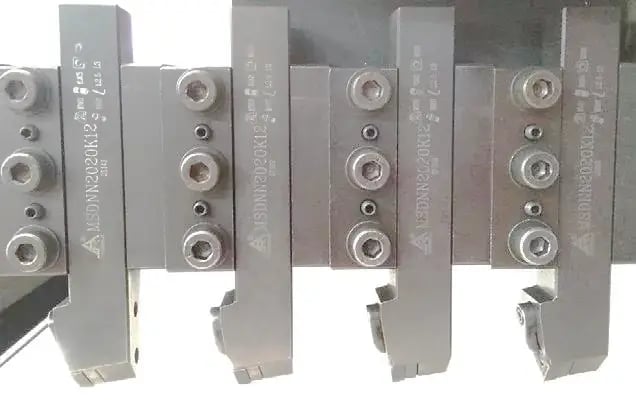
Cada faca tem uma quantidade de avanço ligeiramente diferente, por exemplo, se o primeiro avanço for de 5 mm, o segundo, terceiro e quarto avanços serão de 7 mm, 9 mm e 11 mm, respectivamente.
Isso não só garante a qualidade da ranhura, mas também melhora a eficiência do trabalho.
Como evitar desvios de ângulo e tamanho de curvatura
No processo de dobra, a qualidade da dobra depende em grande parte de dois parâmetros críticos: o ângulo de dobra e o tamanho.
Para garantir o tamanho e o ângulo de curvatura precisos, as seguintes considerações devem ser levadas em conta:
(1) Se o punção superior e a matriz inferior não estiverem alinhados, isso resultará em erros no tamanho da dobra. Para evitar isso, as matrizes superior e inferior devem ser centralizadas antes da dobra.
(2) A posição relativa da placa e da matriz inferior pode mudar após o batente traseiro se mover para a esquerda ou direita, afetando o tamanho da dobra. Para resolver isso, a distância da posição do batente traseiro deve ser medida novamente antes da dobra.
(3) A falta de paralelismo entre a peça de trabalho e a matriz inferior causará retorno elástico durante a dobra e impactará o ângulo de dobra. O paralelismo deve ser medido e ajustado antes da dobra.
(4) Se o ângulo da primeira dobra for insuficiente, isso afetará a dobra subsequente. O acúmulo de erros de dobra resultará em um aumento no erro do tamanho e ângulo de formação da peça de trabalho. Portanto, é crucial garantir a precisão de cada dobra.
(5) Na dobra, o tamanho da abertura em V na matriz inferior é inversamente proporcional à força de dobra. Ao processar chapas metálicas de diferentes espessuras, a abertura em V apropriada da matriz inferior deve ser selecionada com base nas regulamentações. Normalmente, 6 a 8 vezes a espessura da chapa é a melhor escolha.
(6) Ao dobrar a peça de trabalho em uma prensa dobradeira após a ranhura em V, é necessário garantir que a borda ambígua superior, a borda inferior em forma de V da peça de trabalho e a borda inferior em forma de V da matriz inferior estejam todas na mesma superfície vertical.
⑺ Ao dobrar a peça de trabalho após a ranhura, o ângulo da matriz superior deve ser controlado em torno de 84° para evitar fixação.
Cálculo do comprimento de desdobramento da chapa metálica
Presumo que a maioria de vocês já esteja familiarizada com o cálculo do comprimento de desdobramento antes da ranhura.
Mas você sabe como calcular o comprimento de desdobramento após a ranhura?
Deixe-me demonstrar isso com um exemplo.
A figura abaixo descreve as dimensões de cada aresta da peça de trabalho. A chapa metálica tem espessura de 3 mm.
Cálculo do comprimento de desdobramento da chapa metálica após ranhura
Dobramento após ranhura:
Se o cliente solicitar um raio menor e a espessura restante da chapa for de 0,5 mm, o comprimento de desdobramento L = (40-0,5) + (30-2×0,5) + (30-2×0,5) + (10-0,5) = 107 mm.
Dobramento direto sem ranhura:
Se a dobra for feita sem ranhura e um fator K de 0,25 for selecionado, o comprimento de desdobramento L = (40-3+0,25) + (30-6+2×0,25) + (30-6+2×0,25) + (10-3+0,25) = 93,5 mm.
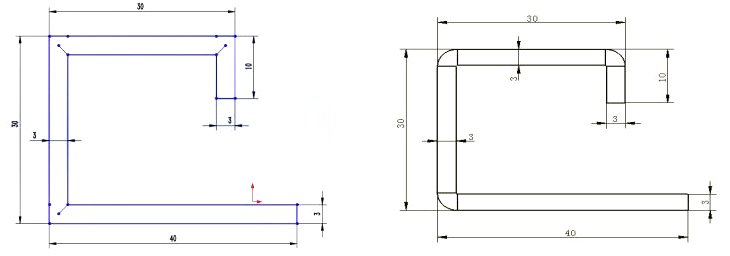
Conclusão
Ranhuramento é um novo tipo de técnica de dobra que foi selecionada pelo mercado.
Para produzir produtos de alta qualidade, é essencial ter domínio sobre diversas técnicas de processamento.
Explorar e adotar continuamente novas técnicas é crucial para produzir produtos ainda melhores.