Dobramento de chapas metálicas é um campo versátil que permite que designs que variam de complexos a simples sejam criados de forma econômica e eficiente. Como em todos os processos de fabricação e aplicações de design, regras práticas específicas devem ser usadas para garantir que recursos apropriados sejam criados para facilitar a fabricação. Este artigo discutirá termos gerais de chapas metálicas e sua respectiva importância de design, bem como regras gerais.
Diferenças em materiais
Ao fazer trabalho em chapa metálica, é importante notar que as diferenças nos materiais afetarão os parâmetros gerais de design permitidos. Uma suposição geral é que, à medida que os materiais ficam mais duros, seu raio mínimo de curvatura fica maior. Essas diferenças nos materiais são importantes para se ter em mente durante o processo de design, pois podem, em última análise, causar problemas durante a produção.
Termos gerais de raio de curvatura e seus significados
Raio de curvatura
O raio de curvatura da chapa metálica se refere ao raio mínimo que pode ser aplicado a um componente de chapa metálica de onde seu flange se origina. Os raios de curvatura são geralmente ditados pelas ferramentas disponíveis e, para um trabalho de design rápido e eficaz, é recomendável falar com os fabricantes para que o design possa ser feito em torno de seus procedimentos operacionais padrão, bem como das ferramentas disponíveis.
Há um raio de curvatura mínimo que deve ser sempre mantido em práticas de projeto de chapas metálicas, e esse BR mínimo é exibido como um múltiplo da espessura específica da matéria-prima. Esse valor também muda com base no tipo de material que está sendo dobrado. Veja abaixo para obter detalhes: Altura de Dobramento
Altura de Dobramento de Chapa Metálica refere-se ao "comprimento" do flange após uma dobra ser feita a partir do corpo principal. Essa altura pode ser tão grande quanto desejado, mas há um limite inferior que não deve ser excedido como regra geral. Essa regra geral é que a Altura de Dobramento deve ser maior ou igual ao BR somado com duas vezes a espessura do material, ou H ≥ 2t + R.
Uma curvatura pode ser caracterizada por vários parâmetros diferentes, mostrados na imagem.
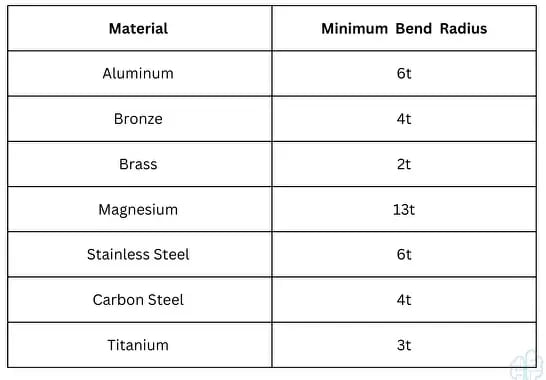
Direção de flexão
A chapa metálica exibe comportamento anisotrópico ao ser dobrada, e a direção importa para evitar defeitos gerais de fabricação, como rachaduras e rasgos durante o processo de dobra. Se a chapa metálica for dobrada em linha com a direção das fibras metálicas, a probabilidade de ocorrer uma rachadura ou rasgo na dobra é muito maior. Junto com esse risco de falha, a dobra em si será mais fraca do que uma dobra feita perpendicularmente às fibras metálicas.
Como regra geral, as dobras devem ser sempre perpendiculares à direção da fibra metálica para aumentar a resistência da dobra, bem como reduzir o risco geral de defeitos de fabricação durante o processo de produção.
a posição de achatamento deslocada estava muito próxima da base da chapa metálica, causando falha no processo de dobra porque não era possível pressioná-la.
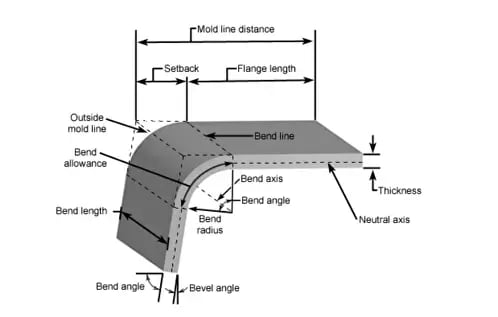
Interferência de ferramenta de flexão
Ao projetar componentes para operações de dobra de chapas metálicas, deve-se considerar a folga e a acessibilidade da dobra desejada pela própria ferramenta. Se os recursos estiverem se estendendo sobre a área de dobra desejada, é possível evitar que a operação de dobra ocorra, pois os recursos bloquearão a capacidade da ferramenta de dobrar no local apropriado.
A distância mínima do recurso que deve ser utilizada é a mesma da altura mínima da curvatura. Em outras palavras, sempre que um recurso adicional for adicionado acima de um local de curvatura, ele deve ser espaçado pelo menos maior ou igual ao BR somado com duas vezes a espessura do material, ou H ≥ 2t + R.
Interferência de flange dobrada
Quando um formato de caixa é desejado ou duas paredes serão dobradas em um canto compartilhado, é importante prestar atenção ao espaço "compartilhado" em que ambas as paredes se cruzarão. Normalmente, um deslocamento em uma parede é adicionado para reduzir a probabilidade de interferência dos flanges. Quanto maior o deslocamento, maior a chance de uma dobra bem-sucedida, mas mais difícil será a solda se as costuras forem soldadas juntas. Na maioria dos casos, um deslocamento de 0,2 mm é adequado.
Tolerância de curvatura na dobra de chapas metálicas
Bend Allowance é um conceito centrado no fato de que quando uma chapa metálica é dobrada, há 3 dimensões a serem consideradas. Essas dimensões são o comprimento do arco do raio externo da dobra, o comprimento do arco do raio interno da dobra e a espessura do material em si. Para cada dobra criada, a soma dos comprimentos do arco dos raios interno e externo é sempre maior do que a espessura do material em si. A diferença entre essa soma dos comprimentos do arco dos raios e a espessura do material é conhecida como tolerância de dobra.
Determinar a tolerância de curvatura é uma questão relativamente complexa, e é recomendado que os fabricantes sejam consultados para entender seus parâmetros de projeto específicos em torno da tolerância de curvatura. Ao falar com os fabricantes, você entenderá como eles calculam o raio de curvatura apropriado (normalmente identificado por meio de uma tabela padronizada) e aumentam a eficácia de seus projetos com relação à capacidade de fabricação geral.
O relevo de curvatura é um daqueles pequenos detalhes em uma peça curvada que é facilmente esquecido.
Relevos de curvatura de chapa metálica
Os relevos de curvatura são comumente encontrados em aplicações de curvatura de chapas metálicas, pois evitam o rasgo ou a falha geral de pontos de alta tensão, geralmente cantos, durante o processo de curvatura. Os relevos de curvatura são simplesmente duas incisões cortadas na chapa metálica para separar as curvaturas separadas que ocorrerão no final. As curvaturas de chapa metálica são necessárias apenas quando o material estará presente em ambos os lados de uma curvatura.
Os relevos de curvatura podem aumentar a resistência da curvatura geral, bem como reduzir o risco de rasgos durante o processo de fabricação. Esses relevos podem ser feitos em qualquer formato, mas furos circulares em cantos ou fendas retangulares são geralmente a forma mais comum de relevos de curvatura vistos na indústria.
O teste magnético é um dos métodos de teste não destrutivo (END) mais comumente usados porque é rápido e relativamente barato.
Valores de tolerância para diferentes medidas dimensionais
É importante notar que, à medida que múltiplas dobras se somam umas às outras, a probabilidade de desalinhamento de características cresce cada vez mais. Essa probabilidade de erro e desalinhamento é causada pela faixa de tolerância relativamente grande da conformação de chapas metálicas.
Ao trabalhar com múltiplas dobras na mesma peça, é aconselhável falar com o fabricante final para obter seu feedback sobre potenciais considerações de design para evitar esses problemas. Por fim, se a peça for destinada a ser fabricada em grandes quantidades, a prototipagem do primeiro artigo deve ser feita até que o resultado desejado seja alcançado por meio de princípios de design padrão.
Alguns desses princípios de design incluem:
- Projetar furos maiores para que absorvam parte da variação na tolerância
- Incorporar furos de alinhamento na base do componente de chapa metálica para que as peças possam ser encaixadas mais facilmente durante a montagem final.
- Dobrar os componentes sem os furos presentes e adicionar os furos por meio de pós-processamento adicional, como estampagem ou usinagem. Embora essa abordagem tenha a maior chance de sucesso, ela não é recomendada, pois o aumento no custo geral de produção normalmente não compensa a facilidade de montagem.
O raio de curvatura da chapa metálica é um fator essencial a ser considerado durante processos de conformação de metal, como dobra a ar ou dobra de metal com uma prensa dobradeira. O raio de curvatura se refere à curvatura de uma dobra e é determinado pelo tipo de material, espessura e ângulo de curvatura.
Ao executar a dobra de metal, o ponto tangente é onde o metal começa a dobrar, e o raio começa a se formar. É crucial manter o ponto tangente no local correto para garantir um raio de dobra adequado. As ferramentas de dobra de metal e a prensa dobradeira usadas devem ser apropriadas para o tipo e espessura do material para garantir que o raio de dobra correto seja alcançado sem rachar ou danificar o material.
O tipo de material é um fator crucial a ser considerado ao determinar o raio de curvatura apropriado. O raio de curvatura deve ser selecionado com base na capacidade do material de suportar deformação e não causar qualquer estresse ou dano ao material.
Ao dobrar chapas metálicas, o ângulo de dobra também deve ser levado em conta. O ângulo de dobra se refere ao ângulo formado entre as duas superfícies adjacentes do metal após a dobra. O raio de dobra necessário para um ângulo de dobra específico dependerá do tipo e da espessura do material.
Para atingir o raio de curvatura correto da chapa metálica, é crucial usar técnicas, equipamentos e ferramentas adequadas. Usar a prensa dobradeira e as ferramentas de dobra de metal apropriadas e seguir os procedimentos adequados de dobra de ar ou de metal pode garantir um raio de curvatura consistente e preciso. Com a consideração cuidadosa de todos os fatores envolvidos, incluindo tipo de material, espessura, ângulo de curvatura e ponto tangente, a dobra de chapa metálica de alta qualidade com o raio de curvatura desejado pode ser alcançada.
Conclusão
Ao projetar produtos que serão compostos de chapas metálicas, há muitas regras básicas importantes a serem lembradas. Primeiramente, raio de curvatura, altura de curvatura e tolerância de curvatura ditarão a maioria de suas escolhas de design conforme você avança em seu conceito. Outros fatores, como geometrias de alívio de curvatura e deslocamentos de flange, completarão suas escolhas de design e produzirão um design de qualidade adequado para produção. É sempre recomendável entrar em contato com o(s) fabricante(s) pretendido(s) para obter suas contribuições e entender suas capacidades específicas que, em última análise, ditarão suas escolhas de design.