O que é fabricação de chapas metálicas
Fabricação de chapas metálicas se destaca como um pilar crucial em várias indústrias, abrangendo desde construção e aeroespacial até automotivo e além. Este refinado processo de fabricação desempenha um papel integral na criação de uma miríade de produtos do dia a dia.
Embora a fabricação de metal ostente uma história centenária, ela permanece em um estado perpétuo de evolução, continuamente impulsionada por avanços tecnológicos. Suas aplicações variam desde a produção de peças de precisão para máquinas até a construção de estruturas metálicas para edifícios e pontes, ressaltando sua versatilidade e indispensabilidade.
Neste guia abrangente, abordaremos os seguintes aspectos:
Compreendendo a fabricação de chapas metálicas: Mergulhe na essência da fabricação de chapas metálicas, desvendando sua importância e relevância em vários setores.
Insights do processo: Obtenha insights sobre os meandros do processo de fabricação, explorando as metodologias e técnicas empregadas para moldar matérias-primas em componentes funcionais.
Tipos de chapas metálicas e suas aplicações: Navegue pelo cenário diversificado de variedades de chapas metálicas e suas respectivas aplicações em diferentes setores, desde painéis leves de alumínio na indústria aeroespacial até componentes de aço duráveis na fabricação automotiva.
Vantagens da fabricação de chapas metálicas: Explore os inúmeros benefícios oferecidos pela fabricação de chapas metálicas, desde a relação custo-benefício e eficiência do material até relações superiores de resistência e peso e flexibilidade de design.
Ao nos aprofundarmos nessas áreas principais, pretendemos fornecer uma compreensão abrangente da fabricação de chapas metálicas, capacitando os leitores a apreciar sua importância e aproveitar seu potencial em vários domínios industriais.
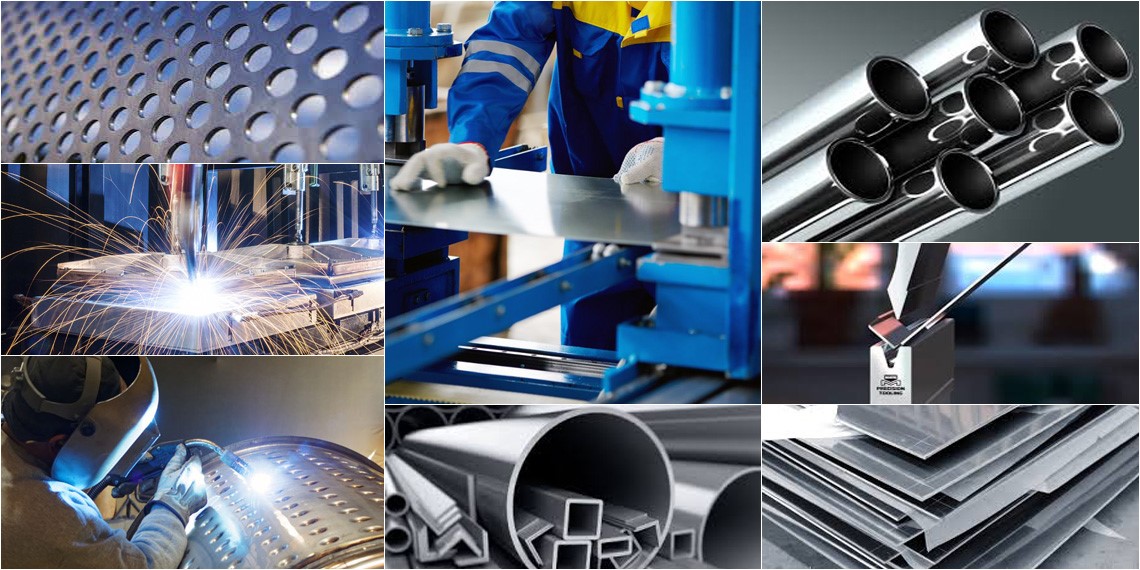
Como funciona o processo de fabricação de chapas metálicas
Fabricação de metais tende a começar a partir do processamento de matérias-primas, que geralmente são grandes e grossas – por exemplo, aço, alumínio e cobre. A chapa metálica pode ser cortada, dobrada ou esticada na maioria dos formatos desejados.
Aqui estão as etapas típicas de como isso funciona:
Projeto
A fase de design é onde a base para o projeto é estabelecida. Os designers geralmente criam esboços iniciais ou modelos 2D/3D do produto, que podem ser feitos usando software de design auxiliado por computador (CAD) ou manualmente.
Fatores importantes como o uso pretendido do produto, as dimensões e tolerâncias necessárias e quaisquer materiais ou acabamentos específicos que serão necessários são mapeados antes do início da fabricação.
Corte
O corte a laser é normalmente o primeiro passo no processo de fabricação. O corte a laser é uma das formas mais precisas de cortar chapas metálicas, pois os lasers conseguem seguir o design programado e cortar o material com precisão.
Dobrando
O processo de dobra é conhecido como dobra CNC e é uma prática que pode ser concluída usando uma variedade de máquinas. Por exemplo, uma prensa dobradeira manual ou uma máquina de dobra de painel automatizada.
A máquina forma a peça metálica fixando a chapa metálica e aplicando pressão para manter a curvatura desejada.
Formando
O processo de conformação dobra ou deforma o material no formato necessário. Diferente do corte, que subtrai o material, a conformação na verdade remodela o material sem diminuir nada de sua massa.
Soldagem
Há uma variedade de técnicas de soldagem que podem ser usadas ao trabalhar com chapas metálicas, incluindo soldagem MIG, soldagem TIG, soldagem MIG robótica e soldagem a ponto.
- Soldagem com gás inerte de metal (MIG): Uma opção de soldagem normalmente rápida, melhor para materiais mais espessos.
- Soldagem de gás inerte de tungstênio (TIG): Oferece maior controle e precisão do que MIG. Melhor para materiais mais finos. Você também pode vê-la referida como soldagem de arco de tungstênio a gás (GTAW)
- Soldagem MIG robótica: Esta é uma versão automatizada da soldagem MIG mais tradicional.
- Soldagem a ponto: segue um processo de soldagem por resistência elétrica.
Acabamento
O acabamento é o último passo ao preparar produtos de metal para uso e torna os produtos mais resistentes à corrosão, adicionando outra camada de durabilidade. Também ajuda a fazer com que as superfícies pareçam atraentes.
Os retoques finais comuns podem incluir preparação da superfície, polimento e revestimento em pó em uma variedade de cores, anodização, passivação e marcação a laser (como logotipos ou gravação de algum texto).
Conjunto
Em um projeto de fabricação de chapas metálicas, montagem se refere à montagem dos produtos necessários antes que eles sejam embalados e entregues onde precisam estar.
Principais tipos de chapas metálicas
Alumínio:
Usado para peças automotivas, dispositivos elétricos e recipientes de cozinha. Oferecendo inúmeros benefícios, incluindo uma boa relação resistência-peso e alta condutividade.
Aço aluminizado:
Este metal combina a alta resistência do aço carbono com a resistência superior à corrosão do alumínio. Folhas de aço aluminizado são usadas para produtos destinados a ambientes de alta temperatura, como eletrodomésticos de cozinha.
Aço carbono:
O aço carbono é usado nos mercados industrial e de consumo para uma variedade de produtos. É uma liga de aço que contém carbono, resultando no aumento da dureza e resistência do material quando ele passa por tratamento térmico.
Cobre:
Exemplos de produtos feitos de cobre são pias, telhados, calhas de chuva e portas. O cobre apresenta maior condutividade elétrica e térmica em comparação ao alumínio, mas pode ser mais caro.
Aço galvanizado:
Chapas de aço galvanizado tendem a ser usadas para fazer carrocerias de automóveis, canos de água, cercas, telhados e escadas. Elas são feitas revestindo o aço com zinco por meio de um processo de imersão a quente, ajudando a torná-lo mais resistente à corrosão.
Aço de alta resistência:
Placas de blindagem militar tendem a ser feitas de folhas de aço de alta resistência. O material é produzido pela liga de aço com uma variedade de elementos como carbono, manganês e cobre. Isso ajuda a melhorar sua dureza.
Aço inoxidável:
Usado para recipientes de cozinha, tanques de armazenamento para produtos químicos e máquinas de processamento de alimentos. O aço inoxidável oferece resistência superior à corrosão, resistência ao fogo e ao calor, relação resistência-peso e capacidade de fabricação.
Titânio:
Produtos típicos feitos de titânio incluem peças de aviação, equipamentos médicos e elementos de construção. É usado principalmente por sua alta relação resistência-peso e resistência à corrosão. Também é reciclável.
Aplicações da fabricação de chapas metálicas
Quiosques, máquinas de venda automática e gabinetes: A fabricação de chapas metálicas desempenha um papel vital na construção de quiosques, máquinas de venda automática e gabinetes, garantindo durabilidade e segurança para essas instalações voltadas para o cliente. Essas máquinas exigem vários componentes de precisão, tornando a fabricação de chapas metálicas indispensável em seu processo de fabricação.
Construção e Segurança: Nos setores de construção e segurança, a fabricação de chapas metálicas é fundamental na produção de uma ampla gama de produtos, como portas de segurança, grades de proteção, grades de segurança e gabinetes personalizados. Esses componentes metálicos fabricados fornecem integridade estrutural e aumentam a segurança em vários ambientes.
Expositores de varejo: Ambientes de varejo dependem de displays visualmente atraentes para atrair clientes e exibir produtos de forma eficaz. A fabricação de chapas metálicas é usada para criar uma variedade de unidades de display de varejo, incluindo displays de bar, cubos de display de varejo, displays portáteis e estandes de ponto de venda, combinando estética com funcionalidade.
Ciência, Medicina e Indústrias Alimentícias: Indústrias como ciência, medicina e produção de alimentos utilizam a fabricação de chapas metálicas para fabricar equipamentos e infraestrutura essenciais. Em cozinhas comerciais e industriais, a fabricação de aço inoxidável é predominante para superfícies de bancadas, unidades de armazenamento, pias e outros acessórios sanitários devido à sua durabilidade e resistência à corrosão.
Transporte: O setor de transporte depende muito da fabricação de chapas metálicas para produzir uma ampla gama de componentes usados em veículos. Veículos de emergência, por exemplo, exigem peças metálicas fabricadas, como compartimentos para porta-luvas, degraus laterais, suportes para maçanetas de portas e cercas de aço para portas de elevadores traseiros. Além disso, a fabricação de chapas metálicas é empregada na construção de trilhos de segurança, alçapões de escotilhas de escadas e outros equipamentos de segurança usados em infraestrutura de transporte.
Ao aproveitar os recursos de fabricação de chapas metálicas, as indústrias podem obter precisão, durabilidade e versatilidade na fabricação de um amplo espectro de produtos adaptados às suas necessidades e requisitos específicos.
Faça uma escolha para sua fabricação de metal
A Krrass é uma empresa renomada especializada na fabricação e distribuição de máquinas para fabricação de chapas metálicas. Com presença global e reputação de excelência, a Krrass se estabeleceu como fornecedora líder de equipamentos de alta qualidade para uma gama diversificada de indústrias.
Fundada em 1998, a Krrass cresceu de forma constante ao longo dos anos, impulsionada por um compromisso com a inovação, confiabilidade e satisfação do cliente. A extensa linha de produtos da empresa inclui prensas dobradeiras CNC, máquinas de corte, máquinas de corte a laser, máquinas de laminação e muito mais, atendendo às variadas necessidades dos profissionais de metalurgia em todo o mundo.
Conclusão
A fabricação de chapas metálicas é um processo de fabricação versátil e amplamente utilizado, oferecendo uma solução econômica para produzir uma ampla gama de produtos e componentes em setores como automotivo, aeroespacial, construção, eletrônicos e muito mais. Sua flexibilidade, eficiência e capacidade de criar formas complexas o tornam uma parte essencial da fabricação moderna.