Você tem um projeto de fabricação que requer automação, precisão e flexibilidade? Você está trabalhando com tubos de metal e precisa de padrões intrincados cortados neles? Se sua resposta for sim, então corte a laser de tubo é provavelmente a solução perfeita para suas necessidades. Esta tecnologia de ponta garante cortes e designs de alta qualidade, prontos para montagem em indústrias como construção e automotiva.
Para cortes limpos e precisos que não requerem acabamento adicional, corte a laser de tubo se destaca como a melhor escolha.
Para ajudar você a decidir se corte a laser de tubo é certo para sua operação, criamos este guia abrangente. Mergulhe para aprender tudo o que você precisa saber sobre o processo e como ele pode transformar a maneira como você corta seus tubos de metal. Este guia irá equipá-lo com o conhecimento para fazer uma escolha informada e inteligente para o seu negócio.
O que é corte de tubos a laser?
O corte a laser de tubos é exatamente o que seu nome indica: um processo de usinagem projetado para cortar tubos de vários formatos em comprimentos específicos ou para gravar padrões neles. Essa técnica automatizada oferece velocidade e precisão significativamente maiores em comparação a métodos tradicionais como serrar ou furar manualmente.
As aplicações para corte a laser de tubos abrangem vários setores. Por exemplo, um de nossos clientes recentes é especialista na fabricação de mesas de soldagem. Depois de passar inúmeras horas serrando e furando centenas de pernas de mesa, ele ficou surpreso com a eficiência de nossa máquina de corte a laser de tubos. Ele não conseguia acreditar que uma solução tão produtiva existia para cortar pernas de tubos, especialmente porque sua oficina local de fabricação de metal personalizada estava oferecendo essa capacidade o tempo todo!
O que é laser de tubo
Os lasers de tubo são projetados para cortar com eficiência vários formatos estruturais leves, que normalmente incluem:
- Tubo redondo
- Tubo redondo
- Tubo quadrado
- Tubo retangular
- Ângulo
- Canal
- Extrusões de formato personalizado
Essas máquinas vêm em tamanhos diferentes, mas geralmente são construídas para lidar com comprimentos de 20 a 24 pés para os formatos e tamanhos mencionados acima.
A maioria das máquinas de laser de tubo são equipadas com carregadores automáticos ou semi-automáticos, permitindo que movam feixes de material pelo processo de corte em alta velocidade. Essa automação aumenta significativamente a produtividade, reduzindo o tempo de manuseio manual.
Um laser de tubo padrão pode cortar tubos com um diâmetro externo (DE) variando de 1" a cerca de 8". Lasers de tubo maiores são capazes de cortar materiais de até 14" de DE.
A complexidade dessas máquinas é impressionante. Imagine-as segurando um pedaço de tubo, movendo-o lateralmente da esquerda para a direita, girando o tubo e, simultaneamente, cortando em ângulos diferentes — tudo com extrema precisão.
Ainda mais impressionante é a programação sofisticada necessária para cortar diferentes formatos — sejam eles redondos, quadrados, angulares ou canais — cada um deles exige cálculos e movimentos precisos.
A maioria desses lasers de tubo são considerados máquinas de 5 eixos. Observá-los em ação revela o nível de coordenação acontecendo simultaneamente, enquanto eles realizam múltiplas tarefas complexas para produzir cortes precisos e intrincados.
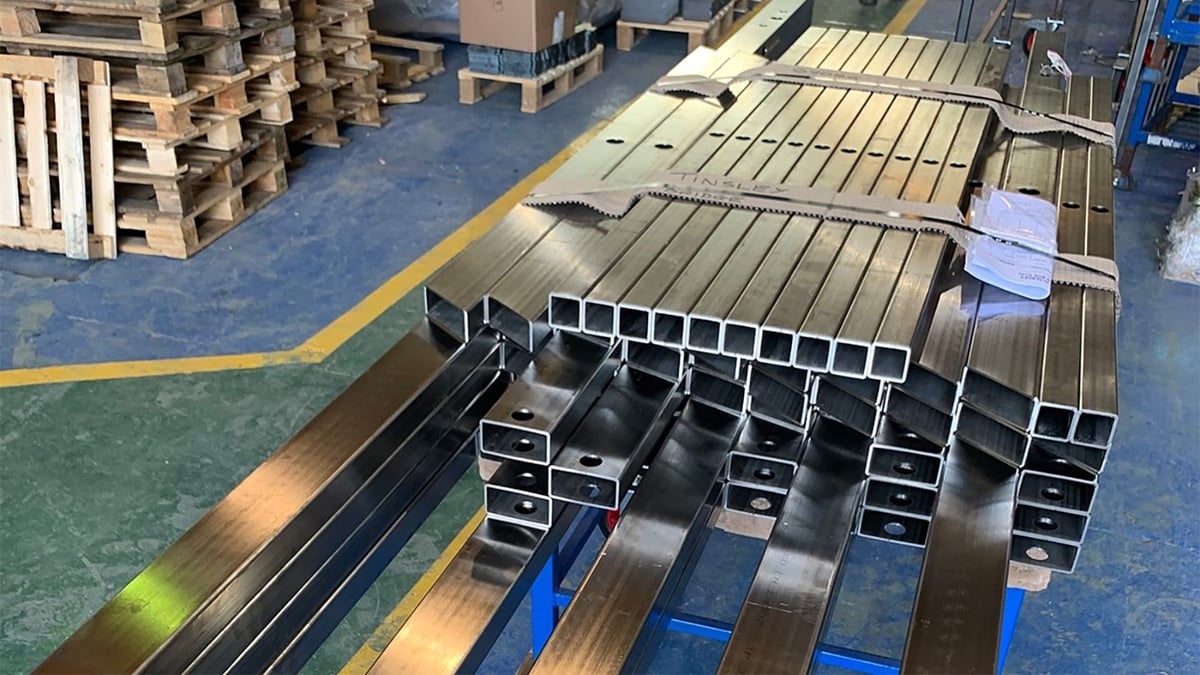
Como funciona o corte de tubos a laser?
O corte de tubos a laser é um processo de usinagem altamente preciso que emprega um laser de alta potência para cortar vários tipos de tubos ou canos de metal com precisão e eficiência notáveis. Aqui está uma visão geral detalhada de como o processo funciona:
Preparação
O primeiro passo envolve montar com segurança o tubo ou cano na máquina de corte. Isso garante estabilidade e precisão durante o processo de corte. A máquina de corte a laser é normalmente programada com um padrão de corte específico e as dimensões necessárias. O software avançado permite que designs intrincados sejam inseridos, permitindo que a máquina execute cortes complexos que podem ser desafiadores de serem alcançados com métodos tradicionais.
Focalizando o Laser
Uma vez que a máquina é configurada, o feixe de laser é direcionado para a superfície do tubo de metal. Uma lente especializada foca o feixe de laser, ajustando-o para levar em conta a espessura e a largura do corte. Este mecanismo de foco é crucial, pois determina a intensidade e a precisão do corte, permitindo que espessuras variadas de metal sejam manuseadas de forma eficiente.
Processo de corte
Com o feixe de laser focado, ele é ativado ao longo do caminho designado do tubo, iniciando o processo de corte. O feixe de laser de alta energia penetra na parede do tubo, vaporizando efetivamente o metal ao longo da linha de corte. Isso resulta em bordas limpas e precisas, reduzindo significativamente a necessidade de usinagem adicional ou trabalho de acabamento. A velocidade e a precisão do corte a laser também permitem altas taxas de produção, tornando-o uma escolha ideal para ambientes de fabricação onde a eficiência é fundamental.
Pós-processamento
Após o corte ser concluído, quaisquer bordas afiadas ou rebarbas são removidas por meio de técnicas de pós-processamento, como rebarbação, lixamento ou polimento. Esses retoques finais são importantes para garantir a segurança e a qualidade do produto final, especialmente se os tubos cortados forem usados em aplicações que exigem um acabamento suave para montagem ou soldagem.
No geral, o corte de tubos a laser é um processo sofisticado que combina tecnologia avançada com engenharia de precisão, resultando em cortes de alta qualidade que atendem aos requisitos exigentes de vários setores, incluindo automotivo, aeroespacial e construção.
Cinco vantagens do corte de tubos a laser
O corte de tubos a laser traz muitas vantagens. Vamos dar uma olhada em algumas.
Flexibilidade
O corte de tubos a laser pode lidar com muitos tamanhos e formatos diferentes de tubos. De menos de uma polegada até 9 polegadas, corte o diâmetro do tubo que você precisa. Tubos retangulares também podem ser cortados com até 9 polegadas de diâmetro.
O comprimento também não é problema. Tubulação padrão de 24 pés é facilmente cuidada.
Um quarto de polegada de aço carbono não é páreo para corte de tubo a laser. As máquinas também podem cortar aço inoxidável de até 0,25 polegadas. E em titânio, o corte de tubo a laser passa por 0,04 polegadas sem problemas também.
Use o corte de tubos a laser em tubos com perfis redondos, retangulares ou irregulares.
Formato, tamanho e espessura não são problemas. A variedade que o corte de tubos a laser pode lidar mostra a ampla flexibilidade com que essas máquinas podem lidar.
Materiais
O corte de tubos a laser funciona em uma ampla gama de materiais. Escolha este método para aço carbono, alumínio, aço inoxidável e titânio.
Se você precisar cortar material refletivo, opte por um laser de fibra em vez de um cortador de CO2.
Você pode até cortar não metais. Um cortador de tubo a laser pode trabalhar em tudo, desde um pedaço de pão até madeira, plástico e isopor.
Eficiência
Como os cortadores de tubos a laser são tão precisos e flexíveis, eles também são extremamente eficientes. Os tubos cortados com essas máquinas não precisam de nenhum processamento extra após o corte. Os cortes são limpos e precisos, então não há sobras de materiais para remover.
Cortar no comprimento e fazer designs complexos são feitos com uma máquina. Não há necessidade de ferramentas adicionais. Isso significa que você não precisa trocar peças ou partes, então seu fluxo de trabalho é melhorado.
Ao usar uma peça de metal bruto para todas as peças, os cortadores de tubos a laser reduzem o desperdício. Isso reduz o custo do seu projeto.
As peças cortadas por um cortador de tubos a laser se encaixam facilmente e com precisão. Isso significa que a construção secundária é simples e eficiente também.
Precisão
A precisão do corte de um cortador de tubo a laser significa que nenhuma operação secundária é necessária. As peças estão prontas para uso ou montagem assim que saem do cortador.
Custo
A eficiência e a precisão dos cortadores de tubos a laser significam que produzir até mesmo peças complexas é simples e automatizado. A automação reduz o trabalho manual e melhora o tempo de conclusão. Sua linha de produção será menos custosa ao usar um cortador de tubos a laser.
Capacidades de corte de lasers de tubo
Que tipos de materiais os lasers de tubo podem cortar?
Os lasers de tubo são bastante semelhantes aos lasers de folha plana em termos dos materiais que podem manipular. Lasers de CO2 são capazes de cortar metais tradicionais, como aço, aço inoxidável, alumínio e materiais galvanizados.
Por outro lado, lasers de tubo de fibra vá além disso cortando também metais altamente refletivos como cobre e latão, que são desafiadores para lasers de CO2. A principal diferença está na tecnologia de corte: os lasers de CO2 lutam com materiais refletivos, enquanto os lasers de fibra são bem equipados para lidar com eles de forma eficiente. Isso torna os lasers de tubo de fibra mais versáteis para cortar uma gama mais ampla de metais.
Quais tamanhos de formatos os lasers de tubo podem cortar?
Os lasers de tubo vêm em vários tamanhos, cada um projetado para lidar com faixas específicas de formatos de tubo. Algumas máquinas são capazes de cortar tubos grandes de até 16-18 polegadas de diâmetro, enquanto outras são limitadas a formatos menores, cortando tubos de até 2 polegadas de diâmetro.
A maioria das oficinas de fabricação opta por máquinas que ficam em algum lugar no meio, capazes de lidar com formatos de tubos que variam de 1 a 8 polegadas.
No entanto, máquinas maiores tendem a operar mais lentamente do que as menores. Isso cria um tradeoff entre flexibilidade e velocidade, onde máquinas maiores oferecem mais versatilidade, mas ao custo de desempenho de corte mais lento.
Quais formatos de materiais os lasers de tubo podem cortar?
Como o nome sugere, os lasers de tubo se destacam no corte a laser de vários tipos de tubos. Isso inclui uma ampla variedade de formatos e tamanhos, como tubos redondos, quadrados, retangulares e até ovais.
No entanto, muitas pessoas não percebem que os lasers de tubo também são altamente eficazes no corte de outras formas estruturais. Além de tubos, essas máquinas podem cortar precisamente ângulos, canais, vigas e até mesmo extrusões de formato personalizado, tornando-as incrivelmente versáteis para diversas necessidades de fabricação.
Quais tolerâncias de corte os lasers de tubo podem atingir?
Cortar chapas planas e cortar materiais moldados como tubos, ângulos e canais apresentam desafios diferentes. Diferentemente de chapas planas, esses materiais moldados geralmente têm mais variabilidade, como arcos ou torções, o que pode dificultar a obtenção de tolerâncias apertadas.
Apesar desses desafios, a maioria dos lasers de tubo pode manter tolerâncias de +/- .010. Para aumentar a precisão, muitas máquinas utilizam tecnologia de sonda de toque, que toca fisicamente o tubo antes do corte para garantir a precisão. Embora isso resulte em peças altamente precisas, pode retardar o processo de corte.
Em comparação, o corte a laser plano frequentemente atinge tolerâncias mais apertadas, em torno de +/- .005, mas para o corte a laser de tubo, +/- .010 é tipicamente a tolerância máxima atingível. Mesmo assim, esse nível de precisão ainda é bastante impressionante, especialmente quando comparado a métodos tradicionais como corte de serra e perfuração.
Aplicação da máquina de corte a laser de tubos
Máquinas de corte a laser de tubos são amplamente utilizados em vários setores devido à sua precisão, flexibilidade e eficiência. Aqui estão algumas aplicações principais:
Indústria Automotiva
O corte a laser de tubos é usado para produzir componentes precisos e leves, como sistemas de escapamento, estruturas de chassis e gaiolas de proteção, melhorando o desempenho do veículo e a eficiência de combustível.
Indústria aeroespacial
Os fabricantes aeroespaciais contam com o corte a laser de tubos para componentes complexos e de alta precisão, como estruturas de aeronaves, trens de pouso e estruturas de suporte, garantindo precisão e reduzindo o desperdício de material.
Indústria da Construção
Elementos estruturais como vigas, colunas e armações arquitetônicas são produzidos usando lasers de tubo para criar juntas e encaixes fortes e precisos que melhoram a estabilidade geral das construções.
Fabricação de Móveis
Os lasers de tubo são usados na produção de designs de móveis modernos e elegantes, cortando tubos de metal para cadeiras, mesas e estantes com alta precisão e desperdício mínimo.
Fabricação de dispositivos médicos
Na área médica, o corte a laser de tubos é crucial para a criação de instrumentos cirúrgicos, stents e outros dispositivos médicos que exigem tolerâncias rigorosas e geometrias complexas.
Equipamentos de ginástica
Tubos cortados a laser são frequentemente usados na fabricação de equipamentos de ginástica, como máquinas de treino e estruturas de suporte, garantindo durabilidade e montagem precisa.
Construção Naval e Indústria Marítima
Os lasers de tubo auxiliam no corte de tubos e elementos estruturais usados na construção naval, garantindo cortes resistentes à corrosão e de alta qualidade para aplicações marítimas.
Fabricação e Arte Personalizada
Os lasers de tubo são frequentemente usados em fabricações de metal personalizadas e instalações artísticas, permitindo que designers criem padrões e formas complexas em tubos de metal para projetos exclusivos.
Com capacidade para lidar com diversos materiais e formas, máquinas de corte a laser de tubos desempenham um papel vital em indústrias onde precisão e eficiência são críticas.
Como os lasers de tubo estão transformando o mundo da manufatura
O corte a laser de tubos está revolucionando a fabricação, oferecendo aos engenheiros e fabricantes novas possibilidades que antes eram difíceis ou caras de se obter. Formas e tamanhos complexos, como corte de ranhuras em tubos, eram tarefas demoradas que exigiam usinagem. Hoje, o corte a laser de tubos torna esses processos fáceis e eficientes.
Ao projetar peças com capacidades de laser de tubo em mente, os engenheiros têm mais flexibilidade e podem explorar uma gama mais ampla de resultados de design. O impacto vai além do design, melhorando significativamente os processos de fabricação downstream também.
Tradicionalmente, o corte de tubos e formas era feito com serras, um método lento e impreciso. O corte com serra não só leva tempo, mas também resulta em imprecisões que podem causar problemas em estágios subsequentes, como soldagem. Por exemplo, fabricar uma estrutura retangular simples a partir de um tubo quadrado de 2,0 x 2,0 x 0,125 exigiria vários cortes de esquadria em ângulos precisos de 45 graus. Com uma serra, configurar e cortar esses ângulos é trabalhoso e frequentemente impreciso.
Quando as peças são cortadas de forma imprecisa, os soldadores são deixados para lidar com lacunas variáveis que levam a tempos de montagem mais longos e soldas inconsistentes. Isso pode resultar no quadro sendo puxado para fora do alinhamento. Soldadores habilidosos podem gerenciar esses problemas, mas isso retarda todo o processo.
Em contraste, os lasers de tubo fornecem tal precisão que não há lacunas inconsistentes ou encaixes ruins, acelerando significativamente os processos de corte e soldagem. Embora este seja um exemplo simples, as vantagens do corte a laser de tubo se tornam ainda mais pronunciadas com peças complexas.
No geral, os lasers de tubo estão transformando o mundo da manufatura, melhorando tanto a flexibilidade do design quanto a eficiência da fabricação.
Desafios no corte a laser de tubos
Além de lidar com torções e dobras em formas estruturais, os lasers de tubo podem enfrentar desafios devido à variabilidade nos raios de borda. Por exemplo, ao trabalhar com um tubo de 2,0 x 2,0 x 0,125, alguns fabricantes produzem tubos com um raio de borda de 0,125 polegadas, enquanto outros podem ter um raio de borda de 0,187 polegadas. Essa diferença aparentemente pequena de 0,062 polegadas pode representar desafios significativos para programadores que tentam executar cortes detalhados ao redor do tubo.
Para atenuar esse problema, uma estratégia eficaz é encomendar lotes de tamanhos de tubos do mesmo fabricante, garantindo consistência nos raios das bordas.
Outro desafio é que materiais moldados são frequentemente menos limpos do que chapas metálicas tradicionais. Fatores como ferrugem, detritos, sujeira e acabamentos de laca podem complicar o corte a laser, levando a tempos de processamento mais lentos. Reconhecendo a importância de materiais limpos para o corte a laser de tubos eficaz, os fornecedores de metal começaram a tomar medidas para melhorar a qualidade dos materiais moldados, semelhantes aos avanços feitos em chapas e placas metálicas.
Como escolher um cortador de tubo a laser
Ao selecionar a máquina de corte a laser de tubos de metal certa, há vários fatores importantes a serem considerados:
- Material de corte: Identifique o tipo de tubo de metal com o qual você trabalhará e garanta que a máquina de corte a laser de tubo seja capaz de lidar com esses materiais específicos. Máquinas diferentes podem ter capacidades variadas quando se trata de cortar vários tipos e espessuras de metal.
- Precisão e qualidade de corte: Avalie a precisão e a qualidade do corte da máquina. Procure por características como alta velocidade de corte, precisão e suavidade do corte. Esses fatores são essenciais para garantir que seus produtos acabados atendam às especificações desejadas.
- Serviço pós-venda: Avalie a qualidade e a disponibilidade do serviço pós-venda oferecido pela marca. Isso inclui suporte técnico, manutenção e acessibilidade de peças de reposição. Um serviço pós-venda confiável é crucial para manter seu corte a laser de tubo máquina operando sem problemas e para resolver quaisquer problemas que possam surgir prontamente.
A KRRASS se orgulha de sua dedicada equipe de atendimento ao cliente, composta por mais de 200 membros que fornecem respostas rápidas e suporte técnico 24 horas em 12 idiomas diferentes, tanto online quanto offline. Estamos comprometidos em fornecer um serviço de pós-venda abrangente e dedicado para garantir que nossos clientes experimentem o mais alto nível de suporte e satisfação. Nossa equipe de profissionais altamente treinados está sempre pronta para ajudar com quaisquer preocupações ou problemas que possam surgir após a compra de nossos produtos. Da solução de problemas técnicos ao fornecimento de reparos e substituições oportunos, a KRRASS estabeleceu um processo simplificado que garante comunicação eficiente, tempos de resposta rápidos e resolução eficaz de consultas e solicitações de clientes.