À medida que os setores industrial e de manufatura continuam a crescer, também crescem as demandas e expectativas dos usuários e proprietários em relação às suas máquinas e produtos. Essa tendência é particularmente evidente nas indústrias de forjamento e manufatura de chapas metálicas. As prensas dobradeiras CNC desempenham um papel crucial neste setor. Para entender melhor as vantagens do seu prensa dobradeira CNC servo híbrida sistema, é essencial estar familiarizado com suas principais características.
Índice
O que é uma prensa dobradeira CNC servo híbrida?
O prensa dobradeira CNC servo híbrida a máquina opera como um sistema de dobra controlado por bomba, onde a sincronização depende do controle preciso da bomba. A estrutura da máquina é altamente estável, tendo sido moldada em um único processo de fixação usando um centro de usinagem tridimensional importado, garantindo superfícies de montagem paralelas e perpendiculares. O computador gerencia o fluxo e a pressão dos cilindros Y1 e Y2 por meio de dois sistemas de bomba bidirecional servo. Essas bombas transferem óleo da câmara superior do cilindro para a câmara inferior para levantar a matriz superior e reverter o processo para dobrar a chapa metálica. A sincronização dos lados esquerdo e direito da matriz superior é controlada por conjuntos separados de bombas bidirecionais servo. Este design fornece alta precisão, eficiência energética, baixo ruído e estabilidade e confiabilidade aprimoradas. Além disso, ele usa menos óleo, tornando-o ideal para a fabricação de máquinas de dobra de grande curso e ultra-alta velocidade.
O que é um servo motor híbrido?
Servomotores híbridos (também chamados de motores de passo híbridos) são motores que usam a alta contagem de polos de um motor de passo, mas apresentam a funcionalidade de malha fechada de um servomotor.
Ao levar um motor de passo tradicional ao limite, é possível perder um passo. Adicionar um encoder aos motores de passo melhora a precisão e permite que os motores de passo sejam executados em RPMs mais altos. RPMs mais altos significam mais velocidade para sua máquina sem o alto custo dos servomotores.
Características da tecnologia de servoacionamento
A tecnologia de servo drive é o núcleo das Hybrid Servo CNC Press Brakes, que utilizam servo motores como fonte de energia para obter dobramento preciso de chapas controlando precisamente a velocidade e a posição dos motores. Os servo motores são caracterizados por velocidade de resposta rápida, alta precisão de posicionamento e operação estável, o que permite que as Hybrid Servo Press Brakes obtenham controle automatizado eficiente durante o processamento.
O princípio de operação do servo motor é baseado nos princípios de indução eletromagnética e equilíbrio de torque. Ao controlar a corrente e a voltagem do motor, o controle preciso do motor pode ser realizado. Durante o processo de frenagem, a tecnologia de servo drive pode realizar o controle preciso do ângulo de curvatura, velocidade e força da placa, de modo a garantir a qualidade do processamento e a eficiência da produção.
Compreendendo o sistema de controle servo
As prensas dobradeiras servo híbridas são equipadas com um sofisticado sistema de controle projetado para monitoramento em tempo real e gerenciamento preciso das operações do equipamento. Este sistema de controle compreende componentes de hardware e software. O hardware inclui sensores, atuadores e controladores, enquanto o software lida com o processamento de dados, análise e execução da lógica de controle.
O sistema de controle é crucial para otimizar o processo de frenagem e aumentar a eficiência da produção. Ao adquirir e analisar continuamente vários parâmetros durante o processo de dobra de chapa, o sistema de controle pode ajustar precisamente o estado operacional do motor e os parâmetros de processamento para atingir resultados ideais. Além disso, o sistema de controle fornece avisos antecipados e diagnostica falhas no equipamento, melhorando assim a confiabilidade e a eficiência da manutenção do equipamento.
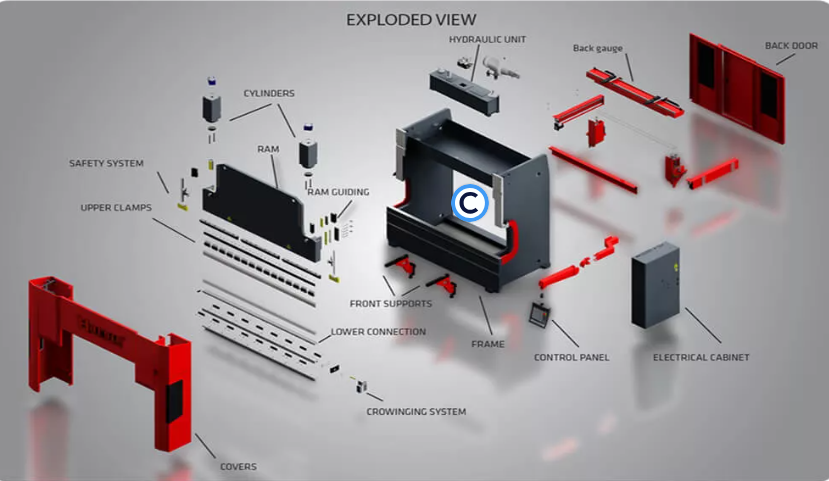
Tipos de prensa dobradeira CNC servo híbrida
Prensas dobradeiras servo híbridas de mesa fixa
Em servoprensas híbridas de mesa fixa, a mesa (matriz) permanece parada enquanto o carneiro (punção) se move, com servomotores oferecendo controle preciso sobre o movimento do carneiro. Este design é particularmente adequado para aplicações que exigem alta precisão e repetibilidade, como nas indústrias automotiva e aeroespacial. A máquina se destaca em fornecer alta precisão e consistência na dobra, tornando-a ideal para produção de alto volume, onde especificações consistentes de peças são cruciais.
Dobradeiras de servo-prensa híbridas de mesa ajustável
As prensas dobradeiras servo híbridas de mesa ajustável são projetadas com uma mesa móvel e um êmbolo, permitindo ajustes em ambos os componentes. Os servomotores controlam precisamente o movimento da mesa e do êmbolo, tornando essas máquinas versáteis para várias tarefas de dobra e espessuras de material. Essa flexibilidade permite que elas manipulem uma ampla gama de materiais e tamanhos de peças, tornando-as adequadas para diversos ambientes de fabricação e acomodando diferentes requisitos de dobra.
Dobradeiras de prensa híbridas servoelétricas
As prensas dobradeiras híbridas servoelétricas combinam servomotores elétricos com sistemas hidráulicos para atingir alta precisão e eficiência energética. Essas máquinas usam motores elétricos para acionar componentes hidráulicos, tornando-as ideais para indústrias onde a eficiência energética e a precisão são cruciais, como na produção de peças e componentes metálicos de alta qualidade. Elas oferecem operação com eficiência energética com consumo reduzido de óleo hidráulico, alta velocidade e precisão, juntamente com baixos requisitos de manutenção.
Dobradeiras de prensa servo híbridas de acionamento duplo
As prensas dobradeiras servo híbridas de acionamento duplo utilizam servomotores duplos para melhorar o controle e a distribuição de potência, permitindo uma dobra precisa e eficiente de materiais grandes e pesados. Esta configuração é ideal para aplicações de serviço pesado e produção em larga escala, onde o controle preciso e a potência substancial são essenciais. A máquina oferece maior capacidade e potência de dobra, juntamente com controle aprimorado sobre tarefas de dobra grandes e complexas.
Dobradeiras de prensa servo híbridas modulares
Os freios de prensa servo híbridos modulares apresentam um design que permite personalização e adaptabilidade ao permitir que componentes sejam adicionados ou removidos com base em necessidades específicas de produção. Isso os torna adequados para fabricantes que exigem flexibilidade e personalização em seus sistemas de freios de prensa. O design modular suporta atualizações e manutenção fáceis, e a adaptabilidade do sistema garante que ele possa atender às mudanças nos requisitos de produção de forma eficaz.
Características da prensa dobradeira servo híbrida
Quando uma máquina de freio CNC servo híbrida está em modo de espera, ela opera silenciosamente enquanto o motor permanece estacionário. Essa operação silenciosa contrasta com o ruído normalmente gerado por máquinas tradicionais. Em termos de eficiência energética, o sistema híbrido se destaca, pois consome praticamente nenhuma energia durante os modos de espera e rápido. O consumo de óleo de máquinas servo híbridas é significativamente menor, usando apenas um terço do óleo em comparação com máquinas síncronas hidráulicas elétricas. Isso resulta em uma temperatura de óleo administrável que geralmente permanece estável, eliminando a necessidade de trocas de óleo hidráulico por até três anos.
A tecnologia avançada de servomotor melhora o desempenho da máquina ao fornecer uma frequência de resposta que supera a das válvulas proporcionais, resultando em um tempo de ciclo de dobra 30% mais rápido do que o das tradicionais prensas dobradeiras hidráulicas CNC síncronas. A adoção da tecnologia de controle de bomba, que substitui o controle de válvula convencional, elimina perdas por estrangulamento e transbordamento, levando a uma redução de 70% no consumo de energia.
Além disso, a capacidade do servo motor de lidar com sobrecargas de curto prazo significa que a potência instalada é de apenas 50% do que seria teoricamente necessário, enquanto a redução no volume do tanque de óleo em 75% diminui significativamente o uso de óleo hidráulico. O equilíbrio térmico aprimorado reduz a necessidade de dispositivos de resfriamento, estendendo assim a vida útil dos componentes hidráulicos.
O design da prensa dobradeira CNC servo híbrida contribui para um ambiente de trabalho mais eficiente e silencioso. Com um nível de ruído drasticamente reduzido durante as fases de marcha lenta, queda rápida, manutenção de pressão e retorno, as condições de trabalho são consideravelmente melhoradas. A resposta rápida do servo motor permite uma troca mais rápida de pressão e fluxo, o que é especialmente benéfico em situações de emergência. Sob condições específicas, a máquina pode atingir velocidades rápidas de descida e retorno de até 300 mm/s, e a velocidade de trabalho pode atingir entre 20-25 mm/s. Essas melhorias em velocidade e capacidade de resposta contribuem para um processo de produção mais eficiente, destacando as vantagens tecnológicas avançadas da prensa dobradeira CNC servo híbrida.
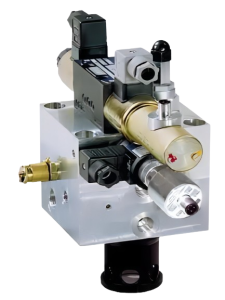
Como funciona uma prensa dobradeira servoelétrica?
Entender a operação de uma Servo-Electric Press Brake é crucial para maximizar sua eficiência e mantê-la eficazmente. Esse conhecimento permite que você aproveite totalmente o potencial da máquina e garanta um desempenho de longo prazo. Vamos nos aprofundar em como essa máquina avançada funciona.
1. Componentes e mecanismo principais
As máquinas de dobra de prensa geralmente consistem em dois componentes primários que trabalham juntos para atingir o efeito de dobra desejado: a matriz e o punção. Em alguns modelos, a matriz é fixada enquanto o punção se move, enquanto em outros, o punção é fixado e a matriz se move. O princípio de funcionamento envolve aplicar pressão ao material colocado entre esses dois componentes para atingir o formato desejado.
2. Operação Servo-Elétrica
Ao contrário das tradicionais prensas dobradeiras hidráulicas que usam pressão hidráulica, a Servo-Electric Press Brake opera usando energia elétrica. Em modelos como a Accurl Electro Servo Press Brake, dois servomotores substituem o sistema hidráulico. Esses motores geram a força necessária para mover o punção ou matriz, dependendo da configuração da máquina, para aplicar pressão precisa no material.
3. Distribuição de pressão
Para garantir uma dobra precisa e uniforme, os servomotores são conectados a um sistema de polias. Essas polias ajudam a distribuir a pressão uniformemente por todo o comprimento do material. Esse mecanismo é crucial para obter dobras consistentes e precisas em toda a peça de trabalho.
4. Integração do sistema CNC
Muitas Servo-Electric Press Brakes vêm equipadas com um sistema CNC (Computer Numerical Control) integrado. Este sistema permite um controle preciso do processo de dobra. Os usuários inserem os ajustes e especificações necessários no sistema CNC, que então direciona a máquina e os servomotores para executar os movimentos e operações precisos necessários.
5. Automação e Precisão
O sistema CNC automatiza o processo de dobra, eliminando a necessidade de ajustes manuais enquanto fornece resultados altamente precisos. Uma vez que o sistema CNC processa os dados de entrada, ele se comunica com os servomotores para aplicar a quantidade correta de energia e movimento. Essa automação garante que o material seja dobrado precisamente de acordo com os requisitos especificados, aumentando a eficiência e a precisão.
Em resumo, a Servo-Electric Press Brake combina tecnologia avançada de motor elétrico com controles CNC automatizados para oferecer um alto nível de precisão e eficiência em metalurgia. Entender esses aspectos operacionais ajuda a utilizar a máquina de forma eficaz e a manter seu desempenho ao longo do tempo.
Por que a prensa dobradeira CNC servo híbrida é melhor do que os freios tradicionais
Controle de alta precisão: As prensas de freio servo híbridas oferecem precisão excepcional no controle da força de frenagem por meio da manipulação precisa de servomotores. Essa capacidade de ajuste preciso garante que a força de frenagem possa ser finamente ajustada para atender aos requisitos específicos de vários processos, resultando em alta precisão de frenagem.
Resposta rápida: O sistema de controle servo em Hybrid Servo Press Brakes é caracterizado por suas altas capacidades de resposta dinâmica. Isso permite que as prensas dobrem atinjam a força de frenagem necessária rapidamente, aumentando significativamente a eficiência da produção ao reduzir o tempo de resposta.
Economia de energia e proteção ambiental: Comparados aos sistemas de frenagem hidráulicos ou pneumáticos tradicionais, os freios de prensa servo híbridos são mais eficientes em termos de energia e ecologicamente corretos. Eles consomem menos energia e produzem menos emissões, levando a custos de produção reduzidos e a uma pegada ambiental menor.
Alta confiabilidade: Equipadas com sensores e sistemas de controle avançados, as Hybrid Servo Press Brakes monitoram continuamente as condições de frenagem e diagnosticam falhas em tempo real. Esse monitoramento em tempo real melhora a confiabilidade do equipamento e simplifica a manutenção, garantindo desempenho consistente.
Alta flexibilidade: A programabilidade do sistema de controle servo em Hybrid Servo Press Brakes permite fácil adaptação a várias necessidades de produção e mudanças de processo. Essa flexibilidade aumenta a capacidade da linha de produção de lidar com diferentes tarefas e se ajustar a novos requisitos de forma eficiente.
Por que usar uma prensa dobradeira CNC servo híbrida? - Análise de vantagens
O sistema de prensa dobradeira híbrida combina os melhores recursos das prensas dobradeiras hidráulicas e servoelétricas, eliminando efetivamente as deficiências de cada opção individual. Essa abordagem inovadora é o resultado de uma pesquisa dedicada que visa melhorar o desempenho das prensas dobradeiras hidráulicas e elétricas.
Pesquisadores na área buscaram melhorar os projetos existentes de sistemas hidráulicos e servoelétricos separadamente. Eventualmente, eles conceberam a ideia de fundir essas duas tecnologias, criando um sistema híbrido que alavanca os pontos fortes de ambas enquanto aborda suas fraquezas. Isso resultou em um sistema de prensa dobradeira potente e altamente eficiente que oferece inúmeras vantagens.
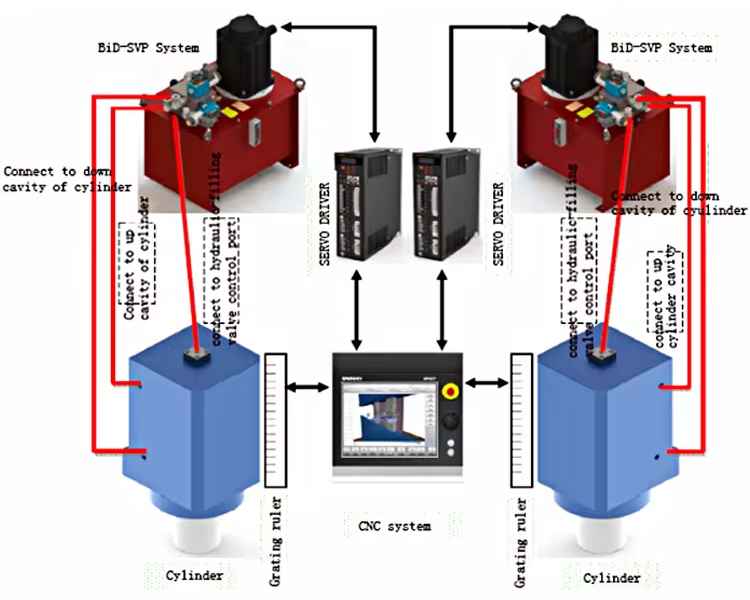
De uma perspectiva ampla, os benefícios mais significativos introduzidos pelo sistema de servoprensa híbrida incluem:
- Amizade ambiental
- Economias significativas de energia
- Eficiência operacional aprimorada
- Automação completa sem necessidade de assistência manual
- Excelente relação custo-benefício
Nas seções a seguir, abordaremos os recursos em detalhes.
Precisão e estabilidade aprimoradas
As prensas dobradeiras servo híbridas alavancam a tecnologia de servoacionamento para atingir precisão excepcional na dobra de chapas, controlando com precisão a velocidade e a posição do motor. Essa tecnologia garante que as prensas dobradeiras servo híbridas forneçam alta precisão e estabilidade durante a operação, atendendo às demandas de várias condições de trabalho complexas. Seja realizando usinagem de alta velocidade ou alta precisão, essas prensas dobradeiras se destacam, garantindo qualidade superior do produto e eficiência de usinagem.
Além disso, as Hybrid Servo Press Brakes são equipadas com um sistema de controle avançado que monitora o status operacional do equipamento em tempo real e fornece controle preciso. Este sistema otimiza o ajuste de vários parâmetros ao longo do processo de dobra de chapas. Como resultado, as Hybrid Servo Press Brakes podem manter resultados de processamento consistentes e estáveis ao trabalhar com diferentes materiais e espessuras de chapas, aumentando assim a confiabilidade e a consistência da produção.
Eficiência Energética e Benefícios Ambientais
As Hybrid Servo Press Brakes usam um sistema de energia híbrido que combina acionamento mecânico tradicional e tecnologia de servoacionamento para atingir maior eficiência energética e menor consumo de energia. Comparadas às máquinas tradicionais de processamento de chapas, as Hybrid Servo Press Brakes conseguem utilizar energia de forma mais eficiente durante o processamento e reduzir o desperdício de energia. Sua tecnologia de servoacionamento e sistema híbrido reduzem o atrito mecânico e a perda no processo de conversão de energia, reduzindo o ruído e as emissões de escapamento, e tendo um impacto menor no meio ambiente. Com a crescente conscientização sobre a proteção ambiental, as vantagens ambientais das Hybrid Servo Press Brakes serão mais proeminentes.
Custos de manutenção reduzidos
As prensas dobradeiras servo híbridas são projetadas com uma estrutura otimizada e simplificada, o que simplifica a manutenção e a torna mais conveniente. Os servomotores e sistemas híbridos usados nessas prensas dobradeiras são construídos para durabilidade e confiabilidade, resultando em uma longa vida útil e menores taxas de falhas. Isso reduz a necessidade de manutenção frequente e substituições de peças.
Além disso, o sistema de controle avançado de Hybrid Servo Press Brakes inclui recursos inteligentes de aviso e diagnóstico de falhas. Esses recursos permitem a detecção e resolução antecipadas de problemas potenciais, minimizando a manutenção e o tempo de inatividade. O design modular aumenta ainda mais a eficiência da manutenção, pois os componentes individuais podem ser facilmente removidos e substituídos sem exigir uma desmontagem extensa de toda a máquina. Essa abordagem não apenas acelera os processos de manutenção, mas também ajuda a reduzir os custos gerais de manutenção.
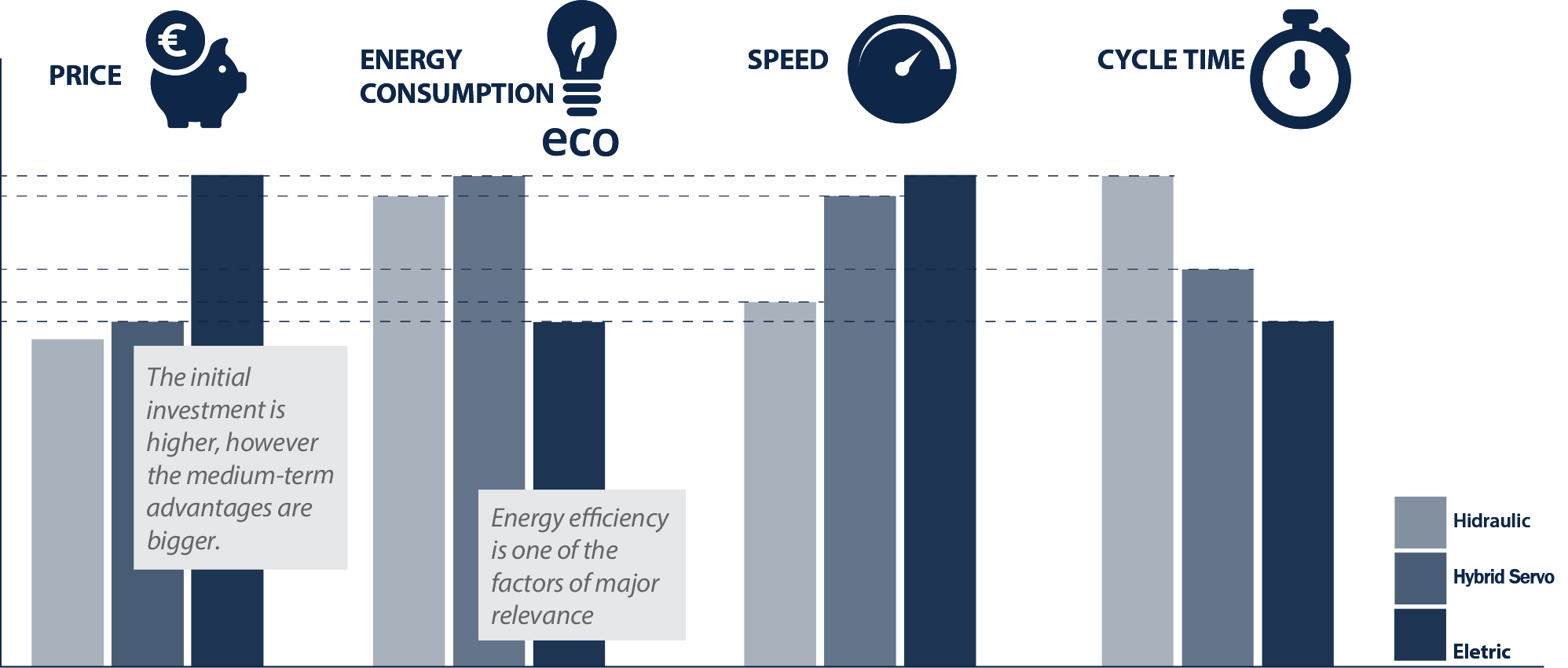
Manutenção Preditiva e Monitoramento Remoto
Outra grande vantagem dos servo freios de prensa é sua capacidade de prever as necessidades de manutenção e monitorá-las remotamente. Ao usar sensores integrados e sistemas de diagnóstico, essas máquinas monitoram constantemente seu desempenho e podem identificar problemas potenciais antes que se tornem problemas sérios que levem a um tempo de inatividade dispendioso. Com dados em tempo real, os cronogramas de manutenção podem ser otimizados, garantindo que componentes cruciais recebam manutenção proativa para evitar quebras inesperadas. Além disso, os recursos de monitoramento remoto permitem que os técnicos acessem o status da máquina e as informações de solução de problemas à distância, permitindo tempos de resposta rápidos e minimizando interrupções na produção.
Áreas de aplicação de prensas dobradeiras CNC servo híbridas
1. Indústria Automotiva
Freios de prensa CNC servo híbridos são amplamente usados na indústria automotiva para fabricar componentes como peças de chassis, suportes e painéis. Sua alta precisão e eficiência garantem que as peças automotivas atendam a rigorosos padrões de qualidade e sejam produzidas em altos volumes.
2. Indústria aeroespacial
No setor aeroespacial, essas prensas dobradeiras são empregadas para fabricar componentes complexos e de alta tolerância para estruturas de aeronaves. A precisão e a estabilidade das prensas dobradeiras CNC servo híbridas são cruciais para produzir peças que aderem a rigorosas especificações de segurança e desempenho.
3. Fabricação de metais e trabalho em chapas metálicas
Os freios de prensa CNC servo híbridos são essenciais na fabricação geral de metais e no trabalho com chapas metálicas. Eles são usados para dobrar várias chapas metálicas em formatos e tamanhos desejados, tornando-os ideais para produzir peças e produtos personalizados na fabricação e construção.
4. Indústria de HVAC
Na indústria de HVAC, freios de prensa CNC servo híbridos são usados para criar dutos, conexões e outros componentes de chapas metálicas. Sua capacidade de lidar com diferentes materiais e espessuras com alta precisão ajuda a garantir a eficiência e eficácia dos sistemas de HVAC.
5. Eletrônicos e Equipamentos Elétricos
Essas prensas dobradeiras são utilizadas na indústria de equipamentos eletrônicos e elétricos para fabricar gabinetes, painéis e alojamentos. A precisão das prensas dobradeiras CNC servo híbridas garante que os componentes se encaixem corretamente e funcionem adequadamente em dispositivos eletrônicos.
6. Aplicações arquitetônicas e estruturais
Em arquitetura e engenharia estrutural, prensas dobradeiras CNC servo híbridas são empregadas para criar componentes de metal para edifícios e infraestrutura. Sua precisão e flexibilidade permitem a produção de peças de metal personalizadas que melhoram tanto os aspectos estéticos quanto estruturais dos projetos arquitetônicos.
7. Máquinas agrícolas
As prensas dobradeiras CNC servo híbridas também são usadas no setor de máquinas agrícolas para fabricar peças como armações, suportes e painéis para vários tipos de equipamentos agrícolas. A confiabilidade e a eficiência dessas prensas dobradeiras dão suporte à produção de máquinas duráveis e de alto desempenho.
8. Energia Renovável
No setor de energia renovável, as prensas dobradeiras CNC servo híbridas desempenham um papel na produção de componentes para turbinas eólicas, painéis solares e outras tecnologias verdes. Sua precisão e eficiência contribuem para o desempenho confiável de sistemas de energia renovável.
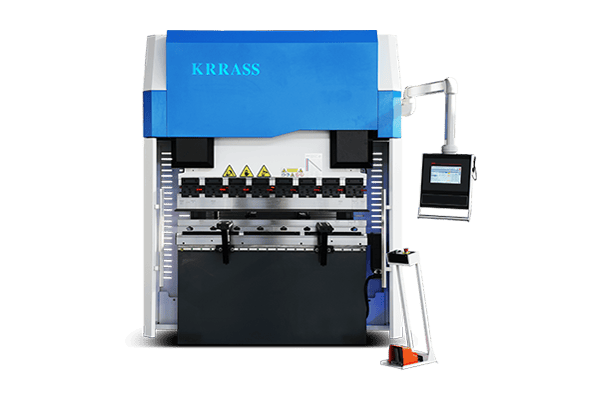
Como a prensa dobradeira híbrida influencia o custo de fabricação
Do ponto de vista de custo e benefício, as servoprensas reduzem significativamente os custos de fabricação e aumentam os benefícios da produção.
Primeiro, em termos de custos de energia, estudos mostram que servoprensas dobradeiras são até 50% mais eficientes em termos de energia do que as tradicionais prensas dobradeiras hidráulicas, potencialmente economizando milhares de dólares anualmente. Por exemplo, uma servoprensa dobradeira operando por 2.000 horas por ano pode economizar aproximadamente $3.000 em custos de eletricidade.
Em segundo lugar, os custos de manutenção são significativamente menores. Com menos desgaste mecânico, as despesas anuais de manutenção podem ser reduzidas em 20% a 30%. Supondo que o custo anual de manutenção de uma prensa dobradeira hidráulica seja de $5.000, mudar para uma servoprensa dobradeira pode economizar de $1.000 a $1.500 por ano. Além disso, a alta precisão das servoprensas dobradeiras reduz o desperdício de material em 10% a 20%. Se o custo anual do material for de $50.000, isso equivale a $5.000 a $10.000 em economia de material anualmente.
No geral, a economia em custos de energia, manutenção e material com uma servoprensa dobradeira pode totalizar aproximadamente $9.000 a $13.500 por ano. Isso não apenas reduz despesas, mas também melhora a eficiência da produção e a qualidade do produto, resultando em maior lucratividade e competitividade.
Conclusão
As prensas dobradeiras CNC servo híbridas são um divisor de águas para os fabricantes que buscam otimizar seus processos de dobra. Combinando o melhor das tecnologias servoelétricas e hidráulicas, essas máquinas oferecem controle e flexibilidade aprimorados, proporcionando dobras precisas, reduzindo o risco de danos às ferramentas e garantindo dobras precisas. Os recursos rápidos de programação e configuração permitem tempos de configuração mais rápidos e o manuseio eficiente de uma ampla gama de materiais.
Ao melhorar a qualidade do produto final e aumentar a produtividade, as prensas dobradeiras CNC servo híbridas provam ser um recurso valioso para fabricantes que buscam aumentar a eficiência e cortar custos. Sua tecnologia avançada permite que os fabricantes otimizem as operações e mantenham uma vantagem competitiva no mercado.
Investir em freios de prensa CNC servo híbridos pode levar a melhorias significativas em produtividade, precisão e economia geral de custos. À medida que os fabricantes priorizam eficiência e qualidade, essas máquinas estão se tornando ferramentas essenciais na indústria. Adotar essa tecnologia não só refinará o processo de dobra, mas também contribuirá para o sucesso geral das operações de fabricação. Para desempenho e confiabilidade de primeira linha, considere a linha de freios de prensa CNC servo híbridos da Krrass, projetados para atender aos mais altos padrões de precisão e eficiência.