"O que é prensa dobradeira?" Essa questão surge frequentemente no campo da metalurgia, especialmente entre os novatos na indústria. Uma prensa dobradeira, um equipamento essencial na fabricação de metais, tem importância significativa na modelagem de chapas metálicas com precisão e eficiência.
Da criação de componentes intrincados para engenharia automotiva à formação de peças essenciais para máquinas industriais, a prensa dobradeira se destaca como uma pedra angular dos processos de fabricação modernos. Neste artigo, nos aprofundamos nas complexidades das prensas dobradeiras, explorando suas funções, capacidades e aplicações generalizadas em vários setores.
O que é prensa dobradeira: tudo o que você precisa saber
Evolução da prensa dobradeira
Datada de mais de um século, a prensa dobradeira, frequentemente chamada de prensa dobradeira, solidificou seu status como um método tradicional para processamento de materiais metálicos. Notavelmente, suas origens remontam a 1882, quando o primeiro freio, conhecido como freio de cornija, foi patenteado. Este aparelho do século XIX, criado a partir de componentes de ferro fundido personalizados fixados em peças de carvalho, utilizava um mecanismo de folha operado manualmente para dobrar chapas metálicas em linha reta - um testamento da natureza laboriosa das primeiras técnicas de metalurgia.
A evolução desses humildes começos para as prensas dobradeiras tecnologicamente avançadas de hoje, movidas por sistemas hidráulicos e computadorização, marca uma transformação significativa. Essas máquinas contemporâneas moldam sem esforço tanto chapas quanto placas de metal, atendendo às necessidades de diversas indústrias ao fabricar componentes simples e complexos.
O que é a conformação de prensa dobradeira
As prensas dobradeiras funcionam usando um punção e uma matriz ajustados em ângulos pré-determinados para dobrar ou cortar metal em vários formatos e formas.
O princípio básico da conformação de freios depende da força, também conhecida como tonelagem. Isso determina a quantidade total de pressão que pode ser aplicada pelo punção durante uma dobra. Quanto maior a tonelagem, mais espessos os materiais que podem ser dobrados e vice-versa.
Junto com a tonelagem vem o comprimento de dobra, que é o comprimento máximo de chapa metálica que pode ser dobrada. Por exemplo, se você tem uma máquina com um comprimento de dobra de 14', qualquer chapa metálica maior que 14' será muito longa para aquela máquina processar.
Dependendo da aplicação e do tamanho/espessura do material, diferentes máquinas com diferentes tonelagens e comprimentos de dobra são necessárias para a fabricação adequada. Na verdade, esses fatores são importantes porque ajudam a determinar o limite de carga da prensa dobradeira - um limite calculado em toneladas por polegada.
Conhecer o limite de carga e a potência de prensa de cada máquina é importante porque, se for usada a tonelagem ou o comprimento errado, o equipamento pode ser danificado ou danificado.
O que são tipos de prensa dobradeira
As prensas dobradeiras modernas são muito mais seguras e não exigem tanto esforço quanto os modelos anteriores. Na verdade, os freios modernos aumentaram a velocidade, a qualidade e a eficiência da dobra de metais. Quando se trata desses freios modernos, há três tipos comuns: manual, hidráulico e CNC.Prensa dobradeira manual
Prensas dobradeiras manuais:
Também conhecidos como freios de chapa metálica, esses são os tipos mais comuns de freios. As prensas de freio manuais exigem que você ajuste manualmente as dimensões e o ângulo de dobra em cada corte e são mais bem usadas para a produção em massa de tamanhos e ângulos de dobra definidos.
Dobradeiras Hidráulicas:
Essas prensas de freio utilizam dois cilindros hidráulicos, permitindo mais controle e golpes consistentes. Elas são frequentemente classificadas por seu movimento, de ação para cima ou para baixo, com cada estilo tendo suas próprias vantagens distintas. Saiba mais sobre suas diferenças aqui!
Prensas dobradeiras CNC:
Esses tipos de freios têm as mais altas habilidades de precisão e personalização, utilizando tecnologia de computador para controlar a precisão e aumentar a eficiência. Ao usar prensas de freio CNC, dados como ângulo de curvatura, espessura da placa, largura e grau são inseridos em um controlador por um operador treinado, e o freio facilmente lida com o resto.
Qual é o custo da prensa dobradeira
O custo de uma prensa dobradeira pode variar significativamente com base em vários fatores, incluindo tamanho, capacidade, características, marca e se é novo ou usado. Geralmente, prensas dobradeiras menores e menos complexas, projetadas para cargas de trabalho mais leves, podem custar a partir de alguns milhares de dólares. Por outro lado, modelos maiores e mais avançados, equipados com recursos de ponta, podem custar centenas de milhares de dólares ou mais.
Por exemplo, as prensas dobradeiras de nível básico adequadas para pequenas oficinas ou amadores podem variar de $5.000 a $20.000. Enquanto isso, os modelos de médio porte adequados para oficinas de fabricação de médio porte podem variar de $20.000 a $100.000. As prensas dobradeiras de nível industrial com maiores capacidades e recursos avançados, como controles CNC e sistemas hidráulicos, podem custar mais de $100,000 para várias centenas de milhares de dólares.
Além disso, fatores como ferramentas adicionais, custos de instalação, treinamento e manutenção contínua também devem ser considerados ao determinar o custo total de propriedade de uma prensa dobradeira.
É essencial pesquisar e comparar diferentes modelos e fornecedores para encontrar uma prensa dobradeira que atenda às suas necessidades específicas, mas que permaneça dentro do seu orçamento. Além disso, considere entrar em contato com fabricantes ou distribuidores para obter informações detalhadas sobre preços com base em suas necessidades.
Conclusão
Poucas máquinas rivalizam com a prensa dobradeira em sua capacidade de dobrar chapas e placas de metal com precisão em comprimentos e ângulos precisos.
No vasto panorama da indústria metalúrgica, a pressione o freio se destaca como uma pedra fundamental, facilitando a entrega de peças personalizadas para uma variedade de setores. De automotivo e aviação a agricultura, energia, militar, transporte e além, sua versatilidade não conhece limites.
Embora os requisitos específicos de produção e materiais determinem o tipo de freio necessário para a conformação ideal, um centro de serviços de metal confiável continua sendo fundamental para orientar os fabricantes em direção à máquina mais adequada para a tarefa em questão. Possuir um freio de prensa confiável não é apenas vantajoso, mas essencial para a eficiência operacional e o sucesso final de qualquer empreendimento de fabricação de metal.
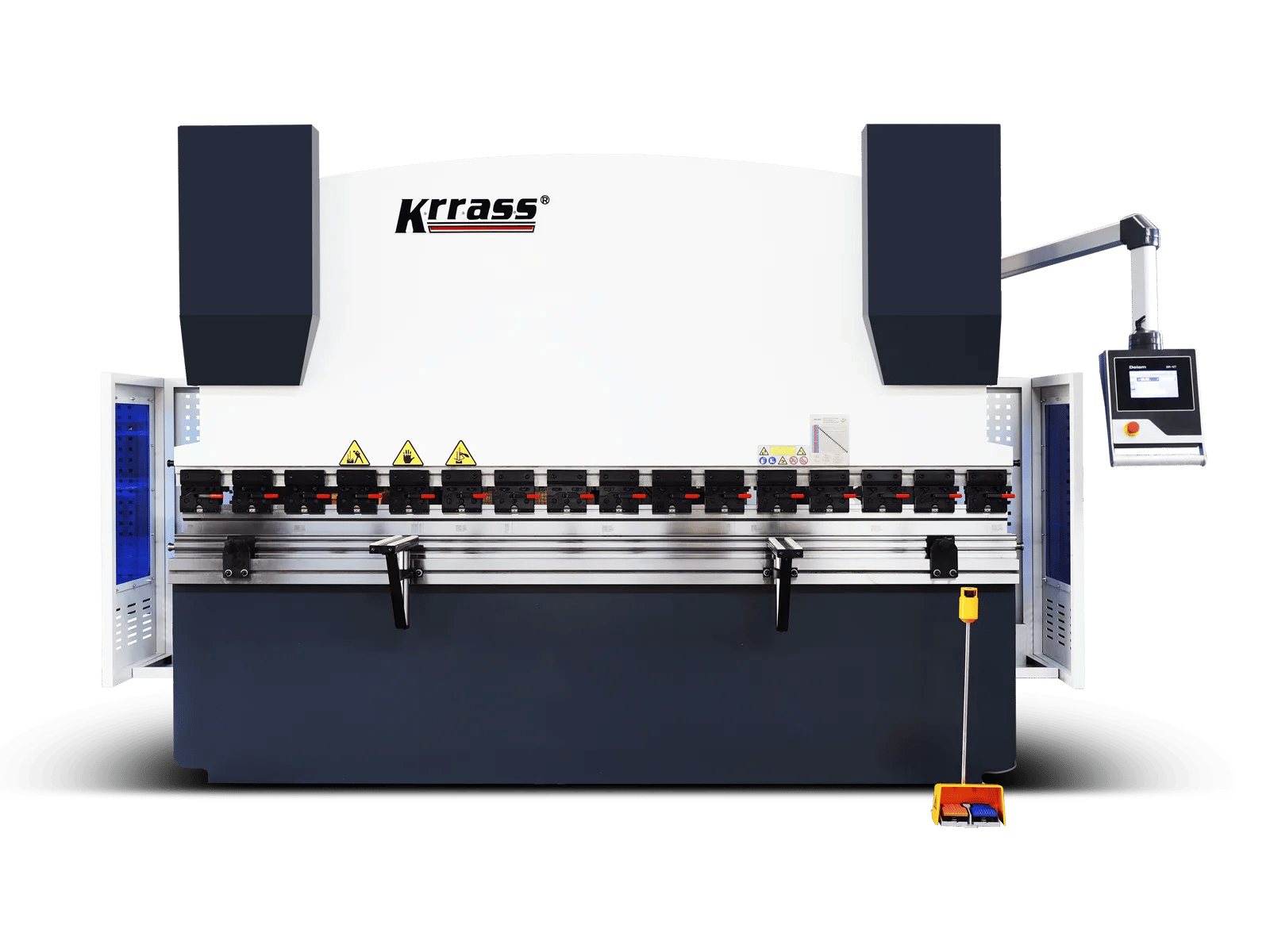