Índice
Visão geral
UM Máquina de corte de chapas metálicas é uma ferramenta especializada usada na indústria de chapas metálicas para cortar chapas de metal em vários formatos e tamanhos.
Ele é composto por vários componentes principais, como lâminas, polias, defletores e um sistema de controle elétrico.
A matriz da máquina, usada para cortar chapas de metal, pode ser encontrada em diferentes formatos, incluindo lâminas retas e lâminas redondas.
As máquinas de corte de chapas metálicas são amplamente utilizadas em vários setores, como fabricação automotiva e aeroespacial, produção de máquinas, produção de eletrodomésticos e construção.
A eficácia de uma máquina de corte de chapas metálicas é determinada por vários fatores, como sua capacidade de corte, precisão, velocidade e confiabilidade.
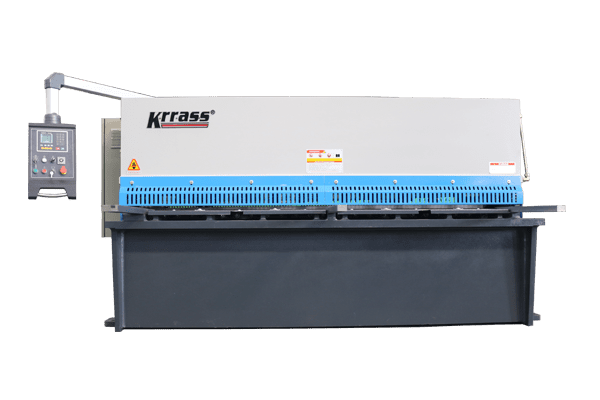
Tipos de máquinas de corte
Dependendo do modo de condução, os tipos comuns de máquinas de corte incluem principalmente máquinas de corte manuais de chapas metálicas, máquinas de corte mecânicas, máquinas de corte hidráulicas e máquinas de corte pneumáticas.
Tesouras manuais para chapas metálicas são equipamentos que podem realizar o corte de chapas movendo manualmente a lâmina para cima e para baixo.
Essas tesouras são fáceis de operar e adequadas para cortar chapas pequenas, mas sua precisão de corte é baixa e não atende aos requisitos de chapas grandes.
A máquina de corte mecânica opera usando um dispositivo de energia composto por um motor, volante, eixo sem-fim e embreagem.
Ela tem velocidades de corte mais rápidas e mais golpes por minuto em comparação com a máquina de corte hidráulica.
O volante da máquina de corte mecânica armazena energia, permitindo o uso de um motor com menor potência.
As máquinas de corte mecânicas podem ser divididas em tipos de movimento ascendente e descendente, com base no modo de operação.
A máquina de corte hidráulica é alimentada por um cilindro hidráulico e motor. O motor aciona o cilindro hidráulico para aplicar pressão de óleo hidráulico ao pistão, fornecendo energia ao pistão da lâmina superior.
A máquina de corte hidráulica tem um curso mais longo e pode lidar com diferentes capacidades de carga.
Materiais cortados com uma máquina de corte hidráulica têm uma superfície lisa com marcações mínimas.
Essas máquinas são conhecidas por sua grande força de cisalhamento, operação estável e boa controlabilidade.
A máquina de corte hidráulica pode ser categorizada em dois tipos: a máquina de corte de viga oscilante e a máquina de corte guilhotina.
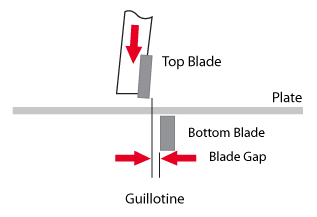
A máquina de corte de viga oscilante realiza o movimento de corte girando o apoio da ferramenta, resultando em alta velocidade, alta precisão de corte e alta eficiência.
A máquina de corte guilhotina pode ser acionada por meios hidráulicos ou mecânicos.
É composto por uma mesa de trabalho, lâminas superior e inferior, um pistão hidráulico, uma ferramenta de fixação e um suporte para chapas.
Esta máquina pode cortar chapas de espessuras e comprimentos variados. A lâmina móvel da máquina de corte de guilhotina pode ser reta ou angulada para reduzir a força de corte.
Com alta velocidade de corte, a guilhotina pode lidar com grandes espessuras e comprimentos de corte, o que a torna ideal para produção em massa.
Entretanto, as bordas cortadas produzidas são ásperas e pouco atraentes.
A máquina de corte pneumática refere-se ao equipamento que utiliza um sistema pneumático para controlar o movimento para cima e para baixo da lâmina para corte de chapas.
A máquina de corte pneumática de placas oferece alta velocidade e precisão de corte, pois o movimento de sua lâmina pode ser ajustado por meio de pressão de ar.
É comumente usado para cortar chapas especiais, como aquelas com alta dureza e resistência.
Graças à sua alta velocidade de corte e precisão, a máquina de corte pneumática é ideal para cortes de alta velocidade e alta precisão.
Existem dois tipos principais de máquinas de corte para cortar chapas: lineares e circulares.
A máquina de corte linear é alimentada por dispositivos hidráulicos e pode manusear chapas metálicas mais espessas.
A máquina de corte de placas circulares é alimentada por um motor e pode cortar placas metálicas circulares.
Cada tipo de máquina de corte tem suas próprias vantagens e é adequada para diferentes necessidades de corte.
Os usuários podem selecionar o tipo mais adequado de máquina de corte com base em suas necessidades e nas propriedades do material.
Por exemplo, máquinas de corte manuais são ideais para cortar chapas pequenas, enquanto chapas grandes podem exigir uma máquina de corte guilhotina ou uma máquina de corte pneumática.

Principais componentes da máquina de corte
Os principais componentes de uma máquina de corte são a mesa de trabalho, as lâminas de corte superior e inferior, as ferramentas de fixação, os defletores e os elementos elétricos.
As lâminas, normalmente feitas de aço de alta resistência com boa dureza e resistência ao desgaste, são o principal componente de trabalho da máquina.
Eles podem ser movidos para cima e para baixo para executar o corte da chapa metálica. O grampo é usado para fixar a chapa metálica no lugar para um corte preciso.
O defletor serve como uma medida de proteção para a máquina de corte de chapas. Feito de materiais metálicos de alta resistência, ele protege contra forças externas que impactam a chapa.
O defletor é normalmente instalado próximo à lâmina da máquina para máxima segurança dos trabalhadores.
Os elementos elétricos controlam a operação da máquina de corte e consistem em uma placa de circuito, motor e controlador.
Esses elementos monitoram e controlam o estado de funcionamento da máquina para garantir uma operação segura.
Princípio de funcionamento da máquina de corte de chapas metálicas
O princípio de funcionamento de uma máquina de corte é cortar chapas de metal no tamanho e formato desejados movendo sua lâmina para cima e para baixo.
Para começar, a placa deve ser colocada sobre a lâmina, garantindo que ela faça contato com a lâmina.
A máquina é então ativada controlando os elementos elétricos para dar partida no motor, fazendo com que a lâmina se mova para cima e para baixo.
O sistema de acionamento então aciona a lâmina para cortar a folha.
Durante todo o processo, um dispositivo de proteção é instalado para garantir a segurança e evitar que a placa seja afetada por forças externas.
A velocidade da lâmina também é ajustada pela máquina de corte, com base no tipo e tamanho do material que está sendo trabalhado, para garantir um corte preciso da chapa.
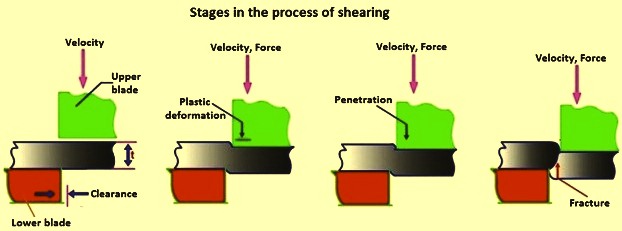
Conclusão
Máquinas de corte de chapas metálicas são amplamente utilizadas em várias indústrias, incluindo fabricação de metais, fabricação automotiva, aeroespacial, construção e muito mais. Elas são comumente empregadas para cortar chapas metálicas, placas, barras e outras formas de estoque de metal em formatos como quadrados, retângulos, tiras e ângulos.
Além disso, as máquinas de corte são ferramentas essenciais para cortar e moldar materiais metálicos com precisão e eficiência, contribuindo para a fabricação de uma ampla gama de produtos e componentes em diferentes indústrias.