Apresentamos os resultados de experimentos que exploram a viabilidade do uso de um Nd acoplado à fibra:Laser YAG para cortar chapas grossas de aço macio (espessura > 15 mm). Os testes foram conduzidos com um laser Nd:YAG de onda contínua de 2,5 kW, que foi entregue à peça de trabalho por meio de uma fibra óptica de núcleo de sílica de 0,6 mm de diâmetro. As amostras de aço macio usadas no estudo variaram de 10 a 50 mm de espessura. Os efeitos de vários parâmetros operacionais — incluindo tamanho do ponto focal, posição do bico de corte em relação à superfície do aço, pressão do gás auxiliar, potência do laser e velocidade de corte — na qualidade das superfícies de corte foram investigados e analisados.
Resultados preliminares indicam que é possível cortar chapas de aço macio de até 50 mm de espessura a velocidades de até 200 mm/min com apenas 500 W de potência do laser Nd:YAG. As superfícies de corte resultantes eram lisas e livres de escória, sugerindo que a tecnologia do laser Nd:YAG tem potencial significativo para cortar chapas de aço espessas.
Introdução
Corte a laser na indústria de processamento de materiais
O corte a laser é responsável por aproximadamente um quarto da indústria de processamento de materiais a laser [1]. Nos últimos 30 anos, desde que o primeiro corte a laser assistido por gás foi alcançado [2], o método fundamental de corte a laser viu pouca mudança. Para cortar aços macios, o feixe de laser é tipicamente focado na superfície da peça de trabalho ou próximo a ela e é cercado por um fluxo coaxial de gás auxiliar de oxigênio. Normalmente, potências de laser de até 3 kW são empregadas para cortar aços macios com espessuras variando de 12 a 15 mm, enquanto chapas mais espessas são geralmente cortadas usando sistemas de plasma ou oxi-combustível. Embora os lasers de CO2 sejam capazes de cortar metais de até 40 mm de espessura, há uma redução significativa na qualidade do corte e na reprodutibilidade com o aumento da espessura [3].
Desafios no corte de materiais mais espessos
Uma abordagem para cortar chapas de aço macio mais espessas é aumentar a potência do laser. Embora esse método ofereça várias vantagens, ele também apresenta desafios significativos. Em potências mais altas (3,5 kW e acima), a qualidade do feixe pode se tornar instável, reduzindo a vida útil dos componentes ópticos, aumentando os custos de equipamento e operação e prejudicando a precisão do corte. Conforme demonstrado em [4], embora a espessura do corte permaneça aproximadamente constante para uma determinada qualidade de acabamento de superfície, a velocidade de corte não diminui em proporção direta à espessura do material, o que sugere um declínio na eficiência do corte à medida que a espessura do material aumenta.
Essa redução na eficiência de corte com o aumento da espessura do material é atribuída à capacidade decrescente do gás auxiliar de cisalhar o material fundido. À medida que a espessura aumenta, a pressão do gás auxiliar também deve aumentar para remover efetivamente o material fundido. No entanto, com o oxigênio como gás auxiliar, a reação exotérmica que ocorre no corte requer uma redução na pressão do oxigênio à medida que a espessura do material aumenta para evitar queima excessiva e reação exagerada. Portanto, gerenciar a pressão do oxigênio se torna crucial para evitar queima descontrolada fora da área aquecida. Isso cria uma contradição nos requisitos: embora aumentar a potência do laser possa estender o desempenho do corte, não é suficiente para superar as limitações impostas pela necessidade de controlar a pressão do oxigênio. Isso representa uma barreira para atingir maiores espessuras de corte, apesar do potencial de maior potência do laser.
Métodos alternativos para cortar aço grosso
Para superar as limitações do aumento da potência do laser, inúmeras técnicas foram desenvolvidas para manter ou melhorar o desempenho do corte à medida que a espessura do aço macio aumenta. Alguns desses métodos incluem: corte a laser com chama [5], lentes de foco duplo [6], serragem de feixe com óptica adaptativa [7], corte a laser usando um bico coaxial (anular) [8], corte a laser de CO2 de feixe duplo [9], feixes de laser giratórios [13, 14] e corte a laser assistido por oxigênio (Lasox©) [10 – 12].
Corte a laser Nd:YAG oscilante e dominado por oxigênio
Em trabalhos anteriores, relatamos o corte de chapas de aço macio mais espessas usando um feixe de laser Nd:YAG giratório [14]. Neste estudo, investigamos o uso de um laser Nd:YAG entregue por fibra com um feixe oscilante (uma técnica semelhante à rotação do feixe) e o método de corte a laser dominado por oxigênio, semelhante ao corte Lasox [10, 11, 12]. Os ensaios de corte a laser Nd:YAG dominado por oxigênio foram conduzidos primeiro com baixas pressões de gás de assistência de oxigênio e depois com altas pressões de oxigênio.
Esta nova abordagem visa abordar os desafios do corte de aço macio espesso, melhorando a eficiência da remoção de material e, ao mesmo tempo, gerenciando os problemas relacionados à pressão do gás de assistência e à estabilidade da viga.
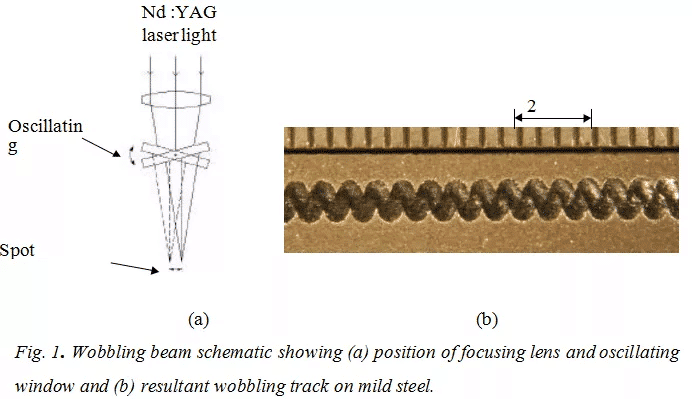
2.2 Corte de aços usando abordagem dominada por oxigênio assistida por laser
O método de corte dominado por oxigênio assistido por laser foi implementado em chapas de aço macio AS3678 de espessura de 16 a 50 mm. As pressões de gás de assistência de oxigênio foram mantidas em menos de 120 kPa (corte de oxigênio de baixa pressão – LoPOx) ou em altas pressões (corte de oxigênio de alta pressão – HiPOx). Os resultados do corte foram registrados como uma função da qualidade do corte (estrias de corte, formato do corte, escória excessiva) e velocidade de corte.
Resultados
3.1Oscilação do feixe de laser.
Ao oscilar o feixe na peça de trabalho, a espessura máxima de corte foi aumentada de 12 mm, encontrada com o corte convencional, para 16 mm. Um gráfico da velocidade máxima de corte para várias espessuras e potências de laser, visto na Figura 2, indica que, embora a espessura de corte tenha sido melhorada com o feixe oscilante, a velocidade de corte é semelhante à do corte convencional (CW). Isso indica que o processo de corte que ocorre dentro do corte permanece inalterado durante o corte do feixe oscilante. Velocidades de corte semelhantes também foram obtidas com o feixe giratório [14].
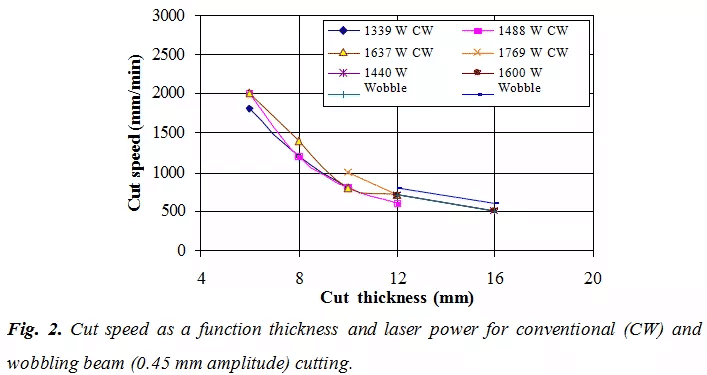
O aumento da espessura do corte pode ser atribuído ao aumento da largura do corte. Isso é demonstrado pela variação da amplitude da oscilação, conforme mostrado na Figura 3. Aqui, à medida que a amplitude da oscilação é reduzida sequencialmente de uma amplitude máxima de 0,45 mm para zero, a largura do corte é reduzida, correspondendo a uma redução na capacidade de limpar o fundido. Isso demonstra claramente a necessidade de ter largura de corte adequada para permitir que a escória seja limpa. Essa visão também é expressa por outros [12], onde é sugerido que tanto a dinâmica de fluidos quanto a termodinâmica são restringidas por cortes estreitos.
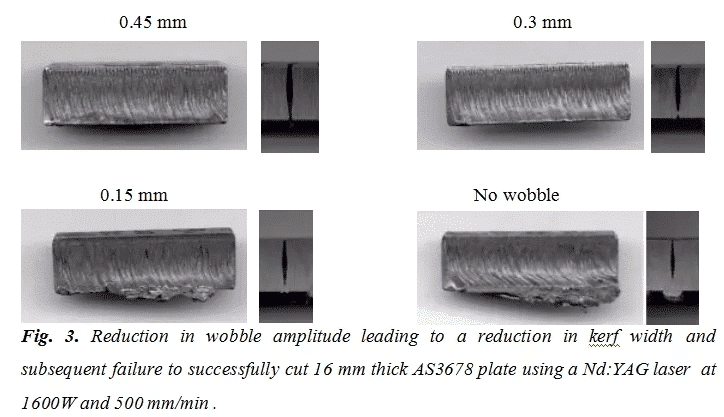
3.2 Corte de aços usando abordagem dominada por oxigênio assistida por laser
3.2.1 Corte dominado por oxigênio de baixa pressão – LoPOx
O processo de corte LoPOx usa o mesmo feixe de laser de diâmetro maior e jato de oxigênio estreito e imponente no topo da peça de trabalho, como visto no processo Lasox, porém com pressões de gás de assistência abaixo de 120 kPa. As superfícies de corte mostradas na Figura 4 usando o processo LoPOx demonstram que as baixas potências de laser incidentes não impedem o corte a laser, desde que a iniciação primária e contínua do corte possa ocorrer. De fato, à medida que a velocidade de corte aumenta, a potência do laser incidente pode contribuir com muita energia e, portanto, causar estrias excessivas. Isso é demonstrado na figura observando a velocidade de corte de 450 mm/min, onde uma superfície melhor foi gerada pela potência do laser incidente de 533 W do que foi alcançada em 1420
W. Aqui, a taxa de reação exotérmica é determinada pela velocidade de corte. A potência do laser incidente é necessária apenas para aquecer a superfície superior a mais de 1000C [11] e iniciar o processo de fusão reativa. A potência excessiva do laser incidente reduz a qualidade do corte. Isso demonstra que questões de interação oxigênio-ferro, não a potência do laser incidente, agora governam principalmente a qualidade do corte. Portanto, este é um processo de corte a laser dominado por oxigênio.
Na Figura 4, à medida que a potência é reduzida para cada velocidade de corte, as primeiras indicações de potência incidente mínima são o início ruim do corte, como visto na extremidade direita. Isso demonstra que os requisitos de potência no início do corte são maiores do que aqueles do processo de corte em andamento e a potência necessária para o rápido estabelecimento de um processo de corte estável e não a potência para o processo em andamento é o critério essencial.
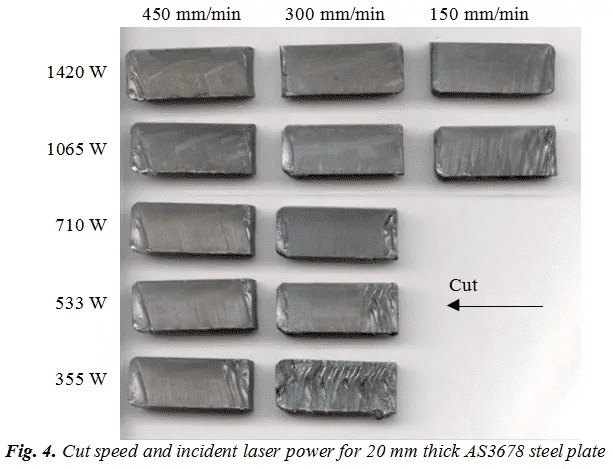
Ao cortar com LoPOx usando um diâmetro de bico coaxial menor para o mesmo material de espessura, as mesmas velocidades de corte são obtidas, mas com uma largura de corte mais estreita e, consequentemente, fluxo de oxigênio reduzido. No entanto, os cortes de alta qualidade não puderam ser obtidos nas potências de laser mais baixas com o diâmetro de bico maior usado na Figura 4. Isso ocorre apesar de um ponto de laser mais intenso como resultado da passagem por um bico de diâmetro menor. Isso demonstra que a exigência de um corte suficientemente largo para permitir que a escória seja removida se aplica igualmente ao processo de corte dominado por oxigênio.
Os lados do corte são mais cônicos do que aqueles encontrados no corte convencional (dominado por laser). A natureza dominada por oxigênio do processo de corte significa que o corte é influenciado pelo formato do jato de oxigênio imponente, com o topo do corte tendo a mesma largura do bico coaxial usado.
A folga entre o bico e a peça de trabalho foi variada com resultados típicos dessa variação mostrados na Figura 5. Para vários diâmetros de bico, a qualidade do corte foi reduzida significativamente com folgas maiores que 25% do diâmetro do bico. Aumentos na folga bico-peça de trabalho expuseram mais do fluxo do bico aos gases atmosféricos do ambiente antes de entrar no corte [8]. A mudança na folga foi realizada sem mudanças correspondentes no diâmetro do ponto do laser com resultados semelhantes. Isso demonstra ainda mais que as mudanças no gás auxiliar e não na intensidade da potência do laser incidente foram o fator que afetou a qualidade do corte a laser na faixa testada. A Figura 5 também mostra o efeito de uma folga muito pequena (0,1 mm) onde o feixe convergente ainda não está excedendo o diâmetro do jato de gás, portanto, não permitindo que o processo de corte a laser dominado por oxigênio opere.
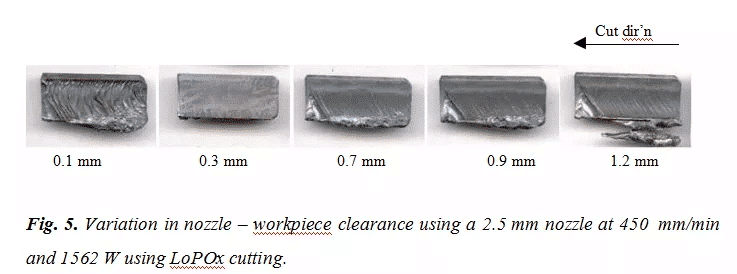
Uma espessura máxima de corte de 32 mm foi alcançada usando o corte Nd:YAG LoPOx. Cortar além dessas espessuras com os diâmetros de bico usados causou a formação de escória excessiva dentro do corte e uma perda de perpendicularidade do corte. Isso demonstra ainda mais a relação entre a largura do corte e a espessura do corte quando baixas pressões de corte (convencionais) são usadas.
3.2.2 Corte a laser Nd:YAG dominado por oxigênio de alta pressão – HiPOx
Usando pressões de fornecimento muito maiores e bicos de diâmetro menor, descobriu-se que era possível cortar aços mais espessos do que aqueles obtidos anteriormente pelo processo LoPOx. A capacidade de corte foi mostrada entre 32 e 50 mm de espessura usando chapa de aço AS 3679. As velocidades de corte típicas com relação à espessura do material e à potência do laser são mostradas na Figura
6. A figura mostra uma continuação dos processos de corte da região de baixa pressão usada para materiais mais finos.
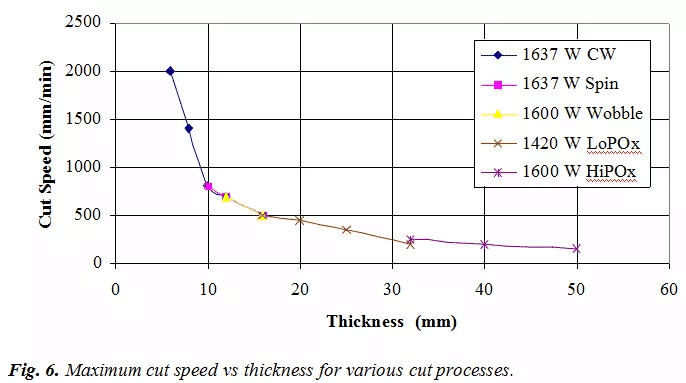
O efeito do uso de altas pressões de entrega significa que o fluxo do gás é complexo e pode dar origem a características de choque interno. A evidência da interação das estruturas de choque durante o corte pode ser vista como “cristas” ou marcas menores na superfície de corte e vistas como linhas perpendiculares à estria. Além disso, o deslocamento dessas cristas com a folga do bico-peça de trabalho resulta do reforço ou anulação dos choques internos do gás de assistência e do choque característico que aparece no início do corte em forma de “X” [15]. O trabalho [16, 17] também indica uma interação complexa e às vezes oscilatória dos choques com as paredes do corte. A evidência da natureza oscilatória do corte está no “zumbido” constante que pode ser ouvido em algumas condições de corte.
Usando um bico coaxial de 1,5 mm de diâmetro, a capacidade de corte mostrou-se satisfatória para chapas de 32 e 40 mm, com resultados de corte de chapas de 40 mm mostrados na Figura 7. A folga bico-peça de trabalho foi significativamente aumentada com as altas pressões de gás de assistência e o formato do corte foi muito menos cônico do que o visto em LoPOx como resultado do fluxo de gás de alta velocidade menos divergente. Esses cortes podem ser vistos na Figura 8.
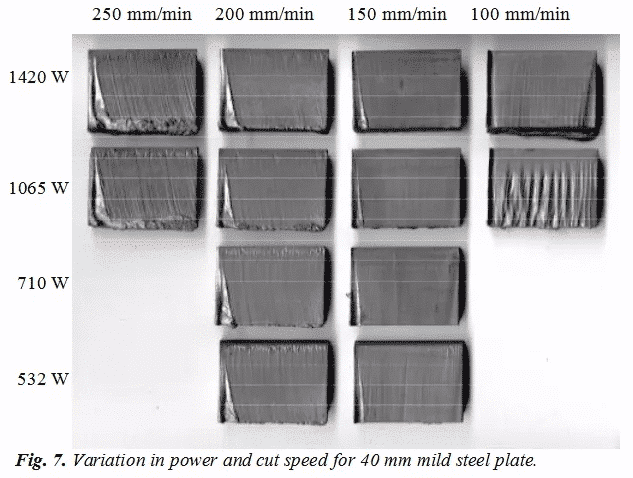
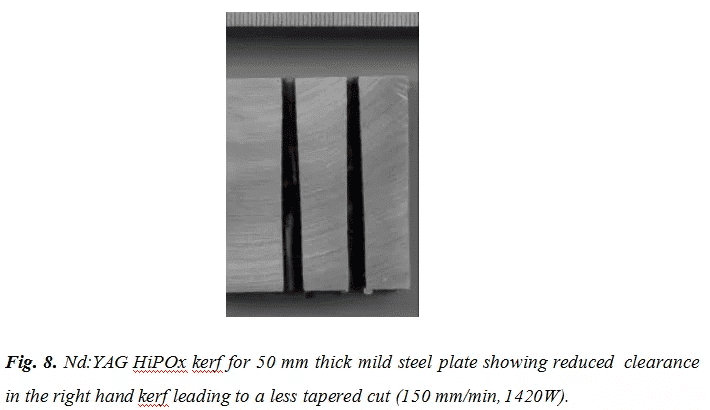
O corte de perfil usando a técnica Nd:YAG LoPOx entregue por fibra é viável com exemplos mostrados na Figura 9. Aqui, aumentos de temperatura no interior dos cantos resultam em aumento do afunilamento nesses pontos. Isso é visto no corte circular da Figura 9 (a) e no rebaixo dos cantos na Figura 9 (b). O rebaixo dos cantos afiados é melhor superado pelo uso de velocidades de corte reduzidas, conforme mostrado na figura.
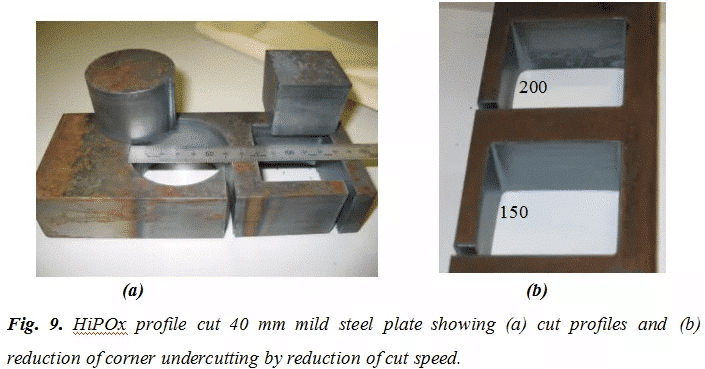
O corte dominado por oxigênio de alta pressão usando o laser Nd:YAG como o usado com o CO2 [12] também se mostra excelente na perfuração com menos de um segundo necessário para perfurar a placa AS3679 de 32 mm. A remoção da escória ejetada para cima continua sendo um problema, com sua presença na superfície da placa no caminho do corte prejudicial à qualidade do corte
Discussão
Desafios do corte de chapas de aço espessas
Apesar dos novos avanços nas técnicas de corte a laser e da capacidade de cortar materiais mais espessos, o processo fundamental de corte permanece praticamente inalterado. Isso é evidente pela redução na velocidade de corte conforme a espessura do material aumenta, bem como pelas velocidades de corte consistentes observadas nos métodos convencionais, de feixe giratório e de feixe oscilante. Em todos os casos, os principais fatores que regem o corte de chapas de aço espessas por fusão reativa — como perdas de calor por condução e limitações na remoção do fluxo de fusão devido à viscosidade e à tensão superficial — continuam a representar desafios significativos. Esses fatores não são facilmente superados, mesmo com o desenvolvimento de novos métodos de corte.
O papel da largura do corte e do consumo de oxigênio
As larguras de kerf variáveis produzidas pela oscilação do feixe de laser, bem como aquelas geradas no corte a laser dominado por oxigênio com o laser Nd:YAG, destacam a necessidade de kerfs apropriadamente largos conforme a espessura do material aumenta. No entanto, em espessuras moderadas de material (~32 mm), aumentar o kerf além daquele produzido pelo maior bico LoPOx se torna impraticável devido ao consumo proibitivo de oxigênio.
Neste contexto, a utilização de HiPOx (oxigênio de alta pressão) fornece uma solução promissora. O fluxo de gás auxiliar de alta pressão e alta velocidade ajuda a reduzir a mistura de oxigênio com gases atmosféricos, disponibilizando mais oxigênio para o processo de fusão reativa. Além disso, o aumento da pressão gera forças de cisalhamento significativamente maiores no material fundido, auxiliando na remoção do fundido do corte. Outra vantagem da técnica HiPOx é a grande folga do bico para a peça de trabalho que ela permite, o que garante a operação confiável de bicos de alta pressão, especialmente ao cortar materiais espessos.
Requisitos de potência do laser para corte dominado por oxigênio
O corte dominado por oxigênio depende principalmente da potência do laser incidente para iniciar e sustentar o corte. Os resultados deste estudo indicam que a potência do laser necessária para o corte dominado por oxigênio é substancialmente menor do que a necessária para o corte a laser convencional. No entanto, embora a potência necessária para manter um corte estável seja menor, potências maiores são necessárias inicialmente para estabelecer o corte. Uma vez que o corte é iniciado, a potência do laser pode ser reduzida a um nível que sustente o processo de corte. Isso sugere que um aumento de potência no início do corte pode maximizar a eficiência geral do corte, usando potência maior apenas quando necessário para a iniciação.
Corte de perfil e rebaixo de canto
O corte de perfil usando o processo de laser Nd:YAG dominado por oxigênio demonstrou ser viável. No entanto, um problema comum é o corte inferior nos cantos internos do perfil cortado. Esse problema pode ser gerenciado programando cuidadosamente a velocidade de corte nessas posições específicas para evitar remoção excessiva de material e garantir cortes limpos.
Gerenciamento de piercings e escórias
Perfurar chapas grossas de aço com um laser Nd:YAG também é viável, mas surgem desafios da ejeção ascendente de escória derretida durante o processo de perfuração. Essa escória pode interferir no fornecimento de gás auxiliar durante o corte subsequente, levando a uma qualidade de corte ruim. Uma solução para esse problema poderia ser a introdução de um jato de ar anular voltado para fora ao redor do bico, o que ajudaria a direcionar a escória para longe do corte. Alternativamente, o problema poderia ser resolvido programando um Comando de espera CNC depois que todas as operações de perfuração forem concluídas, permitindo tempo para a remoção de qualquer escória ejetada antes que o corte continue. Isso ajudaria a manter um fluxo consistente de gás auxiliar e melhoraria o desempenho geral do corte.
Conclusão
O corte a laser dominado por oxigênio, juntamente com larguras de corte maiores, prova ser um método viável para usar um laser Nd:YAG de potência moderada e entrega de fibra para cortar chapas grossas de aço macio. Esta técnica é eficaz para cortar aço macio de até 32 mm de espessura com entrega de gás de baixa pressão. Para espessuras maiores, a entrega de gás de alta pressão permite cortar aço de até 50 mm de espessura, ao mesmo tempo em que permite a perfuração rápida do material. No entanto, os desafios persistem em obter qualidade de corte consistente, especialmente em termos de artefatos de choque e rebaixos nos cantos, que podem ser resolvidos por meio de CNC programação. Além disso, a perfuração bem-sucedida de placas mais espessas requer o gerenciamento da remoção da escória ejetada para garantir que o fluxo de gás auxiliar não seja obstruído, mantendo assim a alta qualidade de corte durante o restante do processo de corte.