Оглавление
What is A Stamping Press Machine
А штамповочный пресс-машина, also known as a stamping press or simply a press, is a versatile machine used in metalworking and manufacturing industries to shape and form metal materials into various components and parts. It operates by applying pressure to a workpiece using specialized dies and tooling to create specific shapes, designs, or patterns.
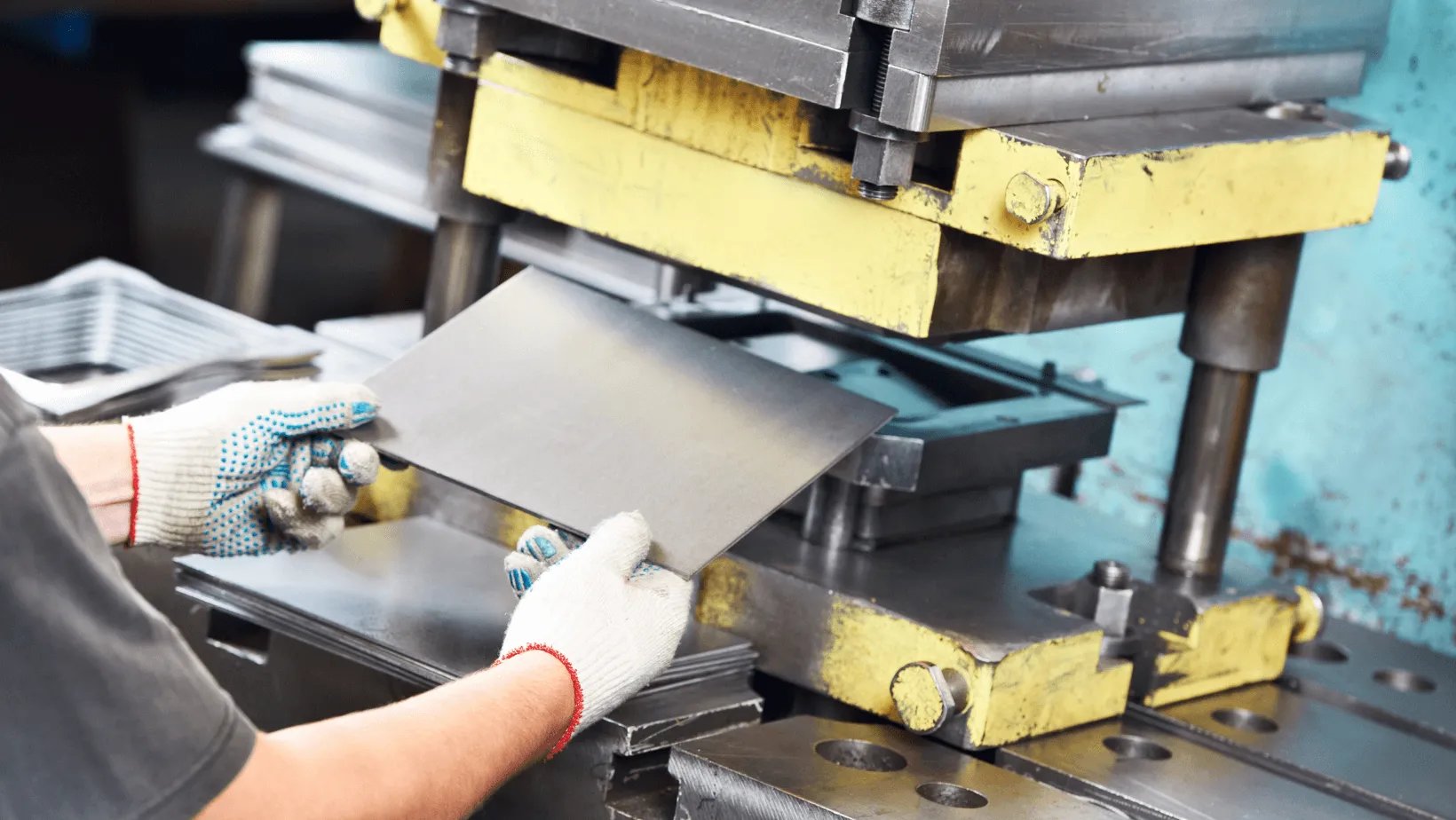
Types of Stamping Press Machine
Stamping press machines are versatile tools used in various industries for: shaping, cutting, and forming metal. These machines come in various types, each designed to serve specific purposes and applications.
Here are eight types of stamping press machines:
Гидравлические прессы
Hydraulic presses use liquid (usually oil) pressure to generate force. A piston moves downward within an oil-filled chamber, applying pressure to a baseplate (or another piston) that is then pushed downward. They are known for their immense power and are often used for heavy-duty tasks such as: forging, deep drawing, and forming thick materials like steel. Hydraulic presses can exert a consistent force throughout the entire stroke, making them suitable for precision applications.
Пневматические прессы
Pneumatic presses use compressed gas or air to apply force. Air is pushed into a cylinder, and when pressure is added, the press mechanism moves with force (usually downward). When the machine finishes its job, the air is let out through some valves, and then springs help lift the ram back up in the cylinder.
Pneumatic presses are generally faster than hydraulic presses and are commonly used for tasks like: punching, riveting, and embossing. These machines are generally simple, easy to use, durable, and require low maintenance. The only drawback with pneumatic presses is that they do not perform well in high-pressure applications. Pneumatic presses are preferred for applications in which speed and simplicity are essential.
Mechanical Presses
Mechanical presses are driven by mechanical mechanisms such as flywheels or eccentrics that build up kinetic energy and release it. The process kicks off with the motor, which sets the flywheel in motion. As the flywheel spins, it accumulates energy and stores it until a specific threshold is reached. Once that threshold is met, the flywheel discharges its stored energy through various drive systems, transmitting it to the ram, which is then driven down onto the workpiece.
After the ram completes its action, it retracts, and the motor and flywheel start the cycle of energy generation anew. With each press stroke, the energy in the flywheel is utilized, prompting the need to replenish it through the motor.
Mechanical presses are known for their high speed and accuracy, making them suitable for tasks like: blanking, coining, and piercing. A mechanical press is ideal for a production line in which both speed and high volume are crucial. It’s easy to set up, and operators can effortlessly control the speed. In general, the initial setup costs also tend to be lower than for other presses like hydraulic presses, for example. Mechanical presses can be single crank, double crank, or eccentric gear-driven, each with its advantages.
To learn more, see our full guide on Mechanical Presses.
Servo Presses
A servo press is a type of press machine powered by a servomotor, often used in situations in which hydraulic presses are traditionally employed. In a hydraulic system, the actuator needs to wait for pressure to build before force is generated, whereas an electric actuator generates force instantly.
This difference allows the servomotor to have control over both the position and speed of the output shaft, rather than being limited to a fixed cycle speed. Servo presses combine the precision of hydraulic presses with the speed of mechanical presses and are ideal for applications in which accuracy and repeatability are critical, such as micro-stamping and electronics manufacturing.
Gap Frame Presses
C-frame presses, also called gap frame presses, are versatile machines known for their three-sided access to the working area. This unique design makes it easy to load and unload parts and perform essential die maintenance. C-frame presses are often a cost-effective option, particularly attractive for small-scale operations or those with budget constraints.
They excel in light-duty applications, but there’s a tendency for them to deflect or "yawn” when subjected to extreme forces. To address this challenge in high-tonnage scenarios, Beckwood, a press manufacturer, employs reinforced steel frames and gib-guided ram bolsters in their machine designs.
C-frame presses offer flexibility with both vertical and horizontal configurations. When set up horizontally, they’re often referred to as bulldozer presses. These machines can handle long parts loaded from either side, making them perfect for bending or straightening tasks.
C-frame presses with servo-electric actuation are the preferred choice for applications that demand high precision, accuracy, and cleanliness. This advanced technology ensures superior control and consistency, making them suitable for precision-critical tasks. They are versatile and suitable for a wide range of tasks, from bending and forming to progressive die stamping.
Transfer Presses
Transfer presses are used for high-volume production of complex parts. They consist of multiple stations at which the workpiece is transferred from one station to another, with each station performing a specific operation, such as: cutting, bending, or stamping. Transfer presses exhibit remarkable versatility, as they allow for the inclusion of various part features like pierced holes, cut-outs, chamfering, knurls, ribs, and threading in the primary press operations. This eliminates the need for costly secondary operations.
Transfer presses are efficient for mass production and automation, often with the added advantage of minimal initial tooling expenses. They also provide an excellent choice for manufacturing larger parts like: tubes, shells, frames, and other structural components. Transfer presses can also be used to produce parts with knurls, ribs, cutouts, threads, and/or other complex design elements, which eliminates the need for additional post-processing operations, and consequently results in lower production costs.
Turret Presses
Turret presses are commonly used in the sheet metal industry for tasks like punching and forming. They feature a rotating turret with multiple tool stations or dies, allowing quick tool changes without the need for manual adjustments. Turret presses can accommodate as many as seven dies, depending on the model. Turret presses are versatile and can handle various tasks with minimal setup time.
Progressive Die Presses
Progressive die presses are specialized machines used for continuous, high-speed stamping of parts. They utilize progressive dies that perform multiple operations in a single pass, reducing cycle times and material waste. Progressive die presses function similarly to transfer press stamping. The primary distinction between these two manufacturing methods lies in their approach.
In transfer press stamping, the initial step involves separating the part from the main strip, and a mechanical transport system transfers it from station to station. Conversely, in progressive die stamping, the main strip is automatically advanced from station to station, with the part being separated from it in the final step.
Progressive die presses are commonly used in the automotive and appliance industries for producing components with tight tolerances. It is ideal for the production of smaller parts in high volumes. Nevertheless, when it comes to high-volume progressive die stamping operations, there’s a requirement for investment in permanent tool steel dies. These are known for their durability, but this durability comes at a higher cost.
What Is the Best Type of Stamping Press Machine for Metal Stamping?
The ideal stamping press machine for metal stamping depends on various factors. The choice of the best stamping machine for metal stamping depends on the specific material, part design, volume, and precision requirements. Hydraulic presses, driven by hydraulic fluid, are versatile and can handle a wide range of metal stamping tasks, making them a common choice.
Pneumatic presses, using compressed air, are faster and simpler, suited for tasks like punching and embossing. Mechanical presses, powered by mechanisms like flywheels, offer high-speed precision for operations like blanking and coining. Servo presses, driven by servomotors, provide precise control for applications requiring accuracy and repeatability.
C-frame presses, also known as gap frame presses, offer three-sided access and are cost-effective, making them attractive for various metal stamping tasks. Transfer presses are efficient for high-volume production with minimal initial tooling expenses, suitable for complex parts. Progressive die presses are specialized for continuous, high-speed stamping, reducing cycle times and material waste.