Panel Bender Machine
А panel bending machine, also known as a press brake or folder, is a machine tool designed for bending sheet metal panels and plates. It is widely used in metalworking and manufacturing industries for shaping metal components with precision. The primary function of a panel bending machine is to apply force to a workpiece, typically a flat sheet of metal, to bend it into a desired shape or angle.
Here are the key components and features of a panel bending machine:
1.Press Brake:
The press brake is the main component responsible for bending the metal. It consists of a punch (upper tool) and a die (lower tool) between which the metal sheet is placed.
The гибочный пресс can be hydraulic, mechanical, or electric, and it exerts force on the sheet metal to bend it.
2.Back Gauge:
The back gauge is a feature that helps position the metal sheet accurately before bending. It ensures consistent and precise bending along the length of the sheet.
3.Bending Length:
The bending length is the distance between the back gauge and the position where the metal sheet is bent. This parameter determines the maximum size of the workpiece that can be accommodated by the machine.
4.Tooling:
The punch and die are the essential tooling components of a panel bending machine. Different shapes and sizes of punches and dies allow for a variety of bending operations, producing different angles and forms.
5.CNC Control:
Many modern panel bending machines are equipped with computer numerical control (CNC) systems. CNC technology allows for precise programming of bending sequences, angles, and dimensions.
6.Safety Features:
Panel bending machines are equipped with safety features to protect operators and prevent accidents. These may include safety guards, emergency stop buttons, and light curtains.
7.Material Support System:
The machine may have systems in place to support and guide the material during the bending process, ensuring accurate and repeatable results.
Panel bending machines are used in various industries, including metal fabrication, automotive manufacturing, aerospace, and construction. They are capable of producing a wide range of components, from simple brackets to complex-shaped metal parts. The versatility and precision of panel bending machines make them essential tools for forming metal sheets into the required shapes for specific applications.
Как работает панелегиб?
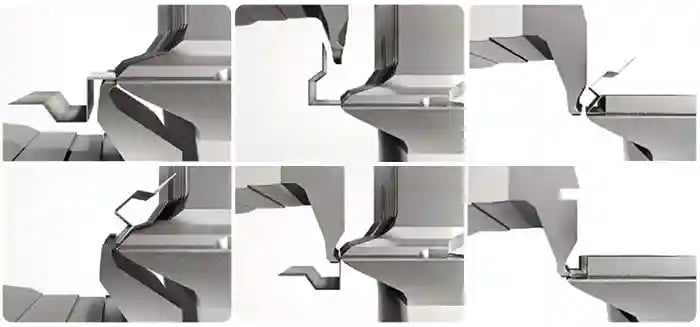
A panel bender, or press brake, works by using a punch and die set to apply force to a flat sheet of metal, causing it to bend into a desired shape. The process involves several key steps:
1.Material Placement:
The process begins with placing a flat sheet of metal onto the bed of the press brake, between the punch (upper tool) and the die (lower tool).
2.Back Gauge Adjustment:
The back gauge is adjusted to position the metal sheet accurately. This ensures that the bending occurs at the correct location along the length of the sheet.
3.Tooling Selection:
The appropriate punch and die tooling are selected based on the desired bend angle and shape. Different tooling options allow for a variety of bending operations.
4.Clamping:
The machine clamps the metal sheet securely between the punch and die to prevent any movement during the bending process.
5.Bending Process:
The press brake exerts force on the metal sheet, causing it to deform and bend. The force is applied by the downward movement of the punch onto the metal. The amount of force applied and the length of the bending process determine the final angle and shape of the bend.
6.Release and Unclamping:
Once the bending process is complete, the machine releases the clamping mechanism, and the bent metal sheet is removed.
7.Repeat or Sequential Bending:
In cases where multiple bends are needed on a single workpiece, the back gauge and tooling are adjusted, and the process is repeated to achieve the desired overall shape.
For CNC-controlled panel benders, the process is automated and controlled by a computer numerical control system. Operators input the bending parameters, such as bend angle, length, and sequence, into the CNC system. The machine then carries out the bending operations precisely according to the programmed instructions.
The versatility of panel benders allows for the production of a wide range of parts and components with different shapes and dimensions. The bending process can be applied to various materials, including steel, aluminum, and other metals. The accuracy and repeatability of panel benders make them essential tools in metal fabrication, manufacturing, and other industries where precision bending of sheet metal is required.
Каковы особенности панелегиба?
A panel bender, or press brake, works by using a punch and die set to apply force to a flat sheet of metal, causing it to bend into a desired shape. The process involves several key steps:
1.Material Placement:
The process begins with placing a flat sheet of metal onto the bed of the press brake, between the punch (upper tool) and the die (lower tool).
2.Back Gauge Adjustment:
The back gauge is adjusted to position the metal sheet accurately. This ensures that the bending occurs at the correct location along the length of the sheet.
3.Tooling Selection:
The appropriate punch and die tooling are selected based on the desired bend angle and shape. Different tooling options allow for a variety of bending operations.
4.Clamping:
The machine clamps the metal sheet securely between the punch and die to prevent any movement during the bending process.
5.Bending Process:
The press brake exerts force on the metal sheet, causing it to deform and bend. The force is applied by the downward movement of the punch onto the metal. The amount of force applied and the length of the bending process determine the final angle and shape of the bend.
6.Release and Unclamping:
Once the bending process is complete, the machine releases the clamping mechanism, and the bent metal sheet is removed.
7.Repeat or Sequential Bending:
In cases where multiple bends are needed on a single workpiece, the back gauge and tooling are adjusted, and the process is repeated to achieve the desired overall shape.
For CNC-controlled panel benders, the process is automated and controlled by a computer numerical control system. Operators input the bending parameters, such as bend angle, length, and sequence, into the CNC system. The machine then carries out the bending operations precisely according to the programmed instructions.
The versatility of panel benders allows for the production of a wide range of parts and components with different shapes and dimensions. The bending process can be applied to various materials, including steel, aluminum, and other metals. The accuracy and repeatability of panel benders make them essential tools in metal fabrication, manufacturing, and other industries where precision bending of sheet metal is required.