The press brake, also known as a brake press, is one of the more traditional methods for processing metal materials and has been in use for over a century. Interestingly, the first brake was patented in 1882. This early model, called the cornice brake, was constructed from custom cast iron parts attached to finished pieces of oak and featured a manually operated leaf that bent a clamped piece of sheet metal in a straight line—a truly labor-intensive press brake forming! You can learn more about the origins of the press brake here.
Today, the press brake forming has evolved significantly with the advent of advanced hydraulic systems and computer technology. Modern press brakes can effortlessly bend sheet and plate metal, providing various industries with both simple and complex parts.
What Is A Press Brake
A press brake is a type of brake, a machine used for bending sheet metal and metal plate. It forms predetermined bends by clamping the workpiece between a matching top tool and bottom die. Typically, two C-frames form the sides of the press brake, connected to a table at the bottom and on a movable beam at the top.
How Does Press Brake Work?
Press brakes rely upon two tools- the punch and die. Die is a tool placed under the workpiece. It is usually in a V-shape. The punch is a movable component over the workpiece. It applies force on the workpiece to bend it. The punch is typically long with a narrow width.
A ram drives the movement of the punch. There are multiple options for the ram movement, such as mechanical, servo motors, hydraulic, and pneumatic. The entire setup is housed on the workbench.
Some terms to remember while working with press brakes are:
- Tonnage: Tonnage refers to the bending force of the particular press brake. Tonnage determines the press brake’s load limit. If a press brake has a higher tonnage, it can bend thicker and longer sheet metal.
- Bending Angle: The bending angle is the angle between the two sides of the bend.
- Bending Length: The bending length is the maximum length limit of the sheet metal that you can bend with a particular press brake.
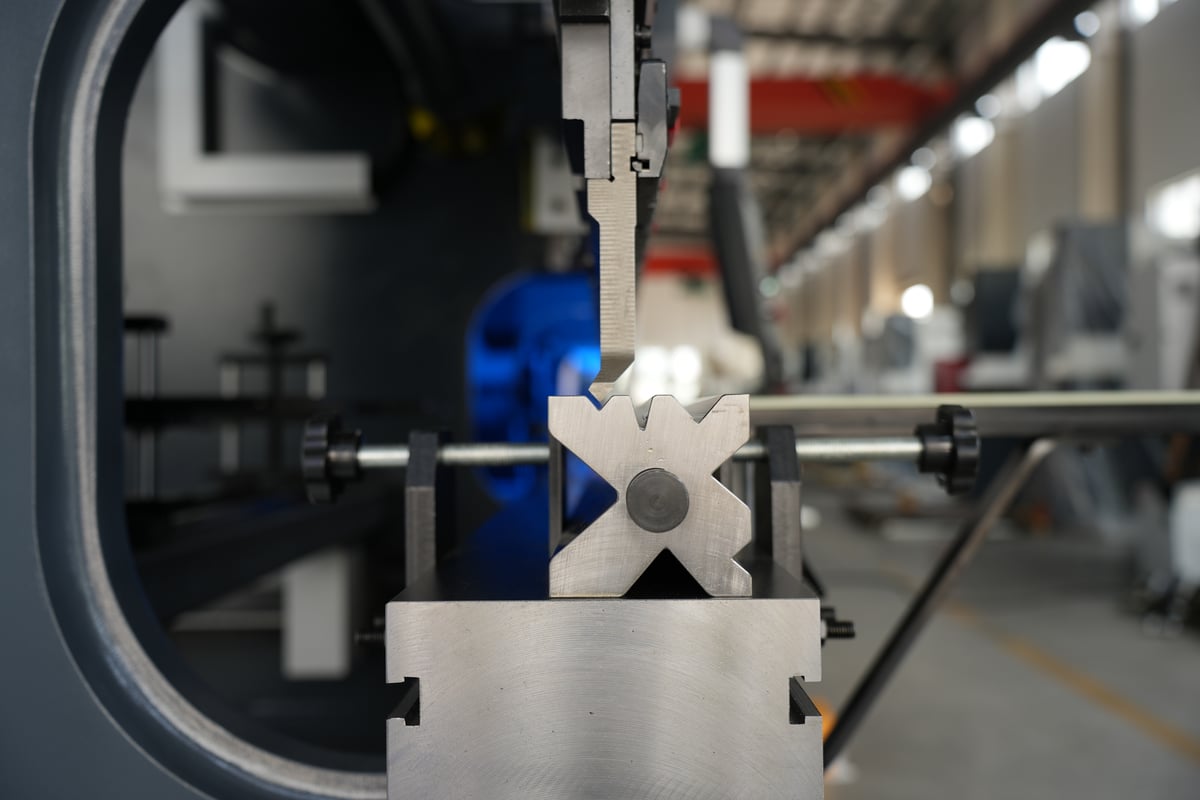
Why Use Press Brake
There is no other machine quite like the press brake when it comes to bending sheet and plate metals to precise lengths and angles.
As one of the many important pieces of equipment in the metal industry, the press brake helps deliver custom parts to a wide range of industries, including auto, aviation, agricultural, energy, military, transportation, and more!
Though production needs and materials will determine the type of brake required for proper forming, a good metal service center will always help determine what machine is best suited for the job and offer a solution for bending needs. Having a good press brake on-hand is crucial to any metal fabricator’s operations and success!
Типы листогибочных прессов
Modern press brakes are much safer and don’t require nearly as much effort as earlier models. In fact, modern brakes have increased the speed, quality, and efficiency of bending metals. When it comes to these modern brakes, there are three common types: manual, hydraulic, and CNC.
Manual Press Brakes: also known as sheet metal brakes, these are the most common type of brakes. Manual brake presses require you to manually adjust the bending dimensions and angle at each cut and are best used for the mass production of set bending sizes and angles.
Hydraulic Press Brakes these brake presses utilize two hydraulic cylinders, allowing more control and consistent strokes. They are often classified by their movement, up-acting or down-acting, with each style having its own distinct advantages.
Листогибочные прессы с ЧПУ: these types of brakes have the highest precision and customization abilities, utilizing computer technology to control accuracy and increase efficiency. When using CNC brake presses, data such as bending angle, plate thickness, width, and grade are entered into a controller by a trained operator, and the brake easily handles the rest.
Press Brake Forming Basics
The basic principle of brake forming relies on force, also known as tonnage, which determines the total amount of pressure that can be applied by the punch during a bend. The greater the tonnage, the thicker the materials that can be bent, and vice versa.
Another important factor is the bending length, which is the maximum length of sheet metal that can be bent. For example, if you have a machine with a 14-foot bending length, any sheet metal longer than 14 feet will be too large for that machine to process.
Depending on the application and the size and thickness of the material, different machines with varying tonnages and bending lengths are required for proper fabrication. These factors are crucial because they help determine the press brake’s load limit, which is calculated in tons per inch.
Evolution of Press Brake Metal Forming
Today, we’re discussing the basics of press brake forming. Before diving in, you might be curious about the origin of the term “press brake.”
In the 15th century, the word “brake” referred to “an instrument for crushing or pounding.” Over time, the meaning evolved, and “brake” became synonymous with “machine.” Essentially, a “pressing machine” and a “press brake” refer to the same concept.
As technology advanced, the press brake machine evolved through various stages, including manual press brakes, mechanical press brakes, hydro-mechanical press brakes, hydraulic press brakes, and finally, electro press brakes. Regardless of the name or type, the term “press brake” always refers to a machine used for “bending” metal.
What Is Press Brake Forming?
Press brake metal forming is one of the oldest mechanical metal deformation processes. This process involves “forming” a piece of metal along a straight axis using a punch and die set, which can be “V”-shaped, “U”-shaped, or channel-shaped.
While press brake metal forming seems straightforward, achieving accuracy can be challenging. Precision bending relies on the interplay between the press, tooling, and workpiece material. Factors such as yield strength, ductility, hardness, and the material condition all influence the amount of spring-back the material experiences.
Key characteristics of the press brake metal forming process include:
- The ability to form ductile materials.
- Its application in both low- and medium-production runs.
- The requirement for minimal tooling.
- Suitability for producing smaller parts.
- The capability to create long workpieces using “V,” “U,” channel, or other shaped punches and dies.
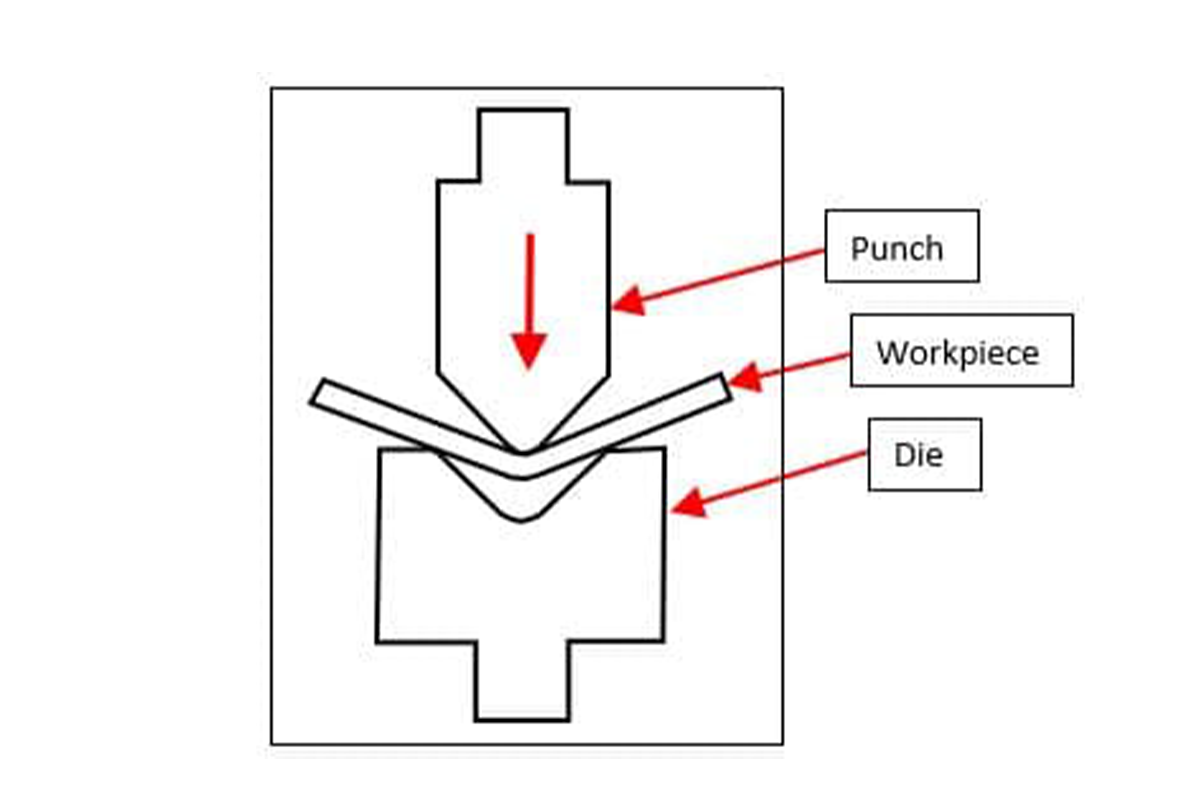
Types Of Press Brake Forming
The three types of press forming most often employed by metal fabricators include air bending, bottom bending, and coining.
Air Bending
Air bending is the most common industrial press braking process. Air bending relies upon three-point bending. The bend’s angle is decided by how far the punch tip penetrates the “V” cavity. The greater the penetration of the punch tip, the greater the rise achieved.
Air bending’s main benefit is that it uses much less force than other methods to achieve a 90° bend. This is due to the leverage effect.
With air bending, the metal makes even less contact than with bottom bending. The tooling only touches the material at three points: the punch, tip, and the die shoulders.
The factor that determines the bend’s angle is how far the punch descends into the die. The further in the force descends, the more acute the resulting angle.
Because the depth of the stroke (and not the tooling itself) determines the bend angle, one can get a wide range of bend angles from one set of tooling.
Since force doesn’t produce the bend in air bending, you don’t need as much power as you do with coining. Like bottom bending, there will be a certain amount of spring back expected with air bending. That said, you will likely need to bend to a slightly more acute angle to get the final bend you want.
Advantages of Air Bending
Air bending offers several advantages in metal forming, primarily due to its efficient use of power and the leverage effect. This method requires less energy to achieve a 90° bend since the metal only makes contact with the punch tip and die shoulder, minimizing friction and reducing tool wear. The bending angle is determined by the stroke depth, allowing a single set of tools to produce multiple bending angles, ranging from 30° to 180°, making air bending highly versatile and adaptable.
Another significant benefit is the speed of air bending compared to other methods. Instead of increasing bending force and machine standby to manage spring back, air bending involves pushing the punch tip into a V-shaped die, which naturally accounts for spring back. This technique requires less force because a wider V-shaped die can be used, enabling low-tonnage press brakes to be employed.
Air bending is also more economical due to its lower cost and reduced power consumption. The minimal contact between the metal sheet and the tools results in less abrasion, extending the lifespan of the tooling. These features make air bending an efficient and cost-effective choice for many metal fabrication applications.
Disadvantages of Air Bending
Air bending, while economical and versatile, does have its limitations. One major disadvantage is its lower precision compared to other bending methods, with a typical tolerance of ¾ of a degree (45′). This can result in less accuracy in the bending angle, as the actual shape formed at the tip is often elliptical rather than a perfect angle.
The method also experiences more significant springback because the metal sheet is not fully yielding during the process. This can make it challenging to achieve precise angles without adjustments. Additionally, if there are holes along the bending line, they can become deformed during the process, further complicating efforts to maintain accuracy and consistency in the final product.
Bottom Bending
In bottom bending or “bottoming,” punch and die are brought together so the metal contacts with the punch tip and the sidewalls.
Bottom bending differs from coining in that the punch and die don’t make full contact with the metal. Also, there isn’t enough tonnage used to imprint or thin the metal.
Because bottom bending uses less force than coining, the material doesn’t entirely conform to the tooling’s bend angle. In fact, with bottoming, the metal experiences a “spring back,” which happens when it relaxes to a broader angle after being bent. So, with bottom bending, to get a certain angle, you need to use tooling that has a slightly sharper angle to account for the spring back that will naturally occur once the sheet metal is released. Different thicknesses and different materials result in different amounts of spring back.
Advantages of Bottom Bending
- Высокая точность: Bottom bending offers greater precision compared to air bending, achieving tolerances as tight as ±0.25 degrees. This is because the sheet metal is forced against the die’s bottom, resulting in more accurate and consistent angles.
- Reduced Springback: The method minimizes springback because the metal is fully compressed between the punch and the die, which means the material yields more completely. This leads to more accurate and stable bend angles.
- Consistent Bend Angles: Since the metal is pressed fully into the die, bottom bending provides consistent results, making it suitable for applications requiring high precision and repeatability.
- Tighter Bend Radius: Bottom bending can achieve a tighter bend radius, which is beneficial for producing complex parts with precise angles and intricate shapes.
- Less Force Needed: Compared to coining, another high-precision bending method, bottom bending requires less force, making it more accessible for standard press brakes.
Disadvantages of Bottom Bending
- Increased Tool Wear: Because the sheet metal is pressed tightly against the die, there is more contact and friction, leading to faster tool wear and potential damage over time.
- Higher Tooling Costs: Bottom bending typically requires specific dies for each desired angle and radius, increasing tooling costs. This can be a significant investment, especially for operations with varying product specifications.
- Limited Flexibility: Unlike air bending, which allows a single set of tools to create multiple angles, bottom bending requires different tools for each specific angle, reducing flexibility and adaptability in the production process.
- Greater Setup Time: The need for precise tool alignment and specific dies increases setup time, which can be a drawback for short production runs or operations requiring frequent changes.
- Risk of Material Damage: There is a higher risk of surface damage to the material due to the greater contact and pressure exerted during the process, which can be an issue for sensitive or delicate materials.
Coining
The term “coining” comes from coin making. To put Lincoln’s face on a penny, machines using too high force compress a disc with enough power to make it conform to his image inscribed on the die set.
In that same vein, “coining” with a press brake involves using enough force to conform to the punch’s precise angle and die used.
During the process of coining, the metal is more than bent. It is thinned by the punch and die’s impact, as it is compressed between them and along the bending surfaces.
The theory behind coining is: with enough force, your metal will bend to the precise angle of your tooling. Therefore, your tooling should be an identical match to the grade you want.
Advantages of Coining
- Consistent Results: Coining delivers highly consistent results, ensuring uniformity across multiple parts.
- Exceptional Tolerance: It achieves very tight tolerances, with accuracy up to ¼ of a degree, making it suitable for applications requiring precise angles.
- Accommodates Thickness Variations: Coining can handle sheet metal with significant thickness tolerances, providing flexibility in material processing.
- Springback Elimination: The high tonnage used during coining penetrates the material effectively, completely eliminating springback and ensuring accurate bend angles.
- Tight Radii: The process allows for the creation of very tight radii, as small as half the sheet metal thickness, which is ideal for intricate designs.
Disadvantages of Coining
- Rapid Tool Wear: The high forces involved in coining lead to quicker wear and tear of both the press brake and the tools, increasing maintenance costs.
- Appearance of Finished Metal: The finished metal may have an unsightly appearance after bending, which can be a concern for applications where aesthetics are important.
- Specific Tool Requirements: For each angle and internal radius, dedicated punches and dies are needed, increasing tooling costs and complexity.
- Thickness Limitations: Coining is not suitable for sheet metal thicker than 2 mm, limiting its use to thinner materials.
Press Brake Forming Process: Versatility and Characteristics
Press Brake Forming Process
The press brake forming process is a highly flexible and versatile method of metal fabrication, capable of producing a wide variety of shapes and parts. The diversity of this process stems largely from the different designs of punches and dies used.
- 0-90° Air Bending: The most common bending technique, suitable for metal sheets ranging from 18-gauge to 3/8 inch in thickness.
- Acute Bending: Used to create sharp bending angles, typically applied to materials 14-gauge or thinner.
- Channel and Gooseneck Bending: Ideal for producing specific shapes such as U-shaped and V-shaped grooves.
- Flattening and Hemming: Used to create flattened and hemmed parts.
- Hat Channel and Open Hat Channel: Employed to produce parts with particular cross-sections.
- Offset and M.T. Offset: Specially designed for applications like oven panels.
- Radius Punches Up to 3” Diameter: Capable of producing arcs with diameters up to 3 inches.
- Urethane Film: Used when needed to protect the surface of the workpiece during bending.
- Wipe Die: Designed for creating parts with complex curves.
Process Characteristics
Strong Adaptability: Whether for single-piece or mass production, press brake forming can be easily adapted to meet various production needs.
Ability to Form Ductile Materials: The press brake is well-suited for working with ductile metals such as aluminum, bronze, and soft steel.
Minimal Tooling Required: Compared to other metal forming technologies, press brake forming typically requires only a set of punches and dies.
Ideal for Smaller Parts: This method is particularly effective for producing small to medium-sized parts.
Capable of Producing Long Workpieces: With the right punch and die, press brakes can create longer workpieces that might be challenging for other forming methods.
High Automation: Modern press brakes often come equipped with CNC systems, allowing for highly automated production.
Fast and Efficient: Press brakes are economical and efficient, with reduced setup times and quick tool changes.
Materials Suitable for Press Brake Forming
Aluminum Alloy: Known for being lightweight and versatile, aluminum alloy is widely used in the aviation and automotive industries. Its plasticity allows it to be formed into complex three-dimensional shapes using a press brake, producing products with smooth and sharp edges. Additionally, aluminum alloys are popular in decorative industries.
Light Steel: Commonly used in construction, light steel is a low-cost material with excellent bending performance, making it a staple in bending manufacturing. It can be quickly formed into various models through bending.
Нержавеющая сталь: A prevalent material in press brake forming, stainless steel offers high strength, plasticity, and corrosion resistance. It is ideal for manufacturing and forming with a press brake, providing smooth edges and reliable shapes. Stainless steel is indispensable in machinery, home appliances, and many other products.
Other materials suitable for press brake forming include brass, cold-rolled carbon steel, and hot-rolled carbon steel. These materials offer various properties that can be advantageous in different applications.
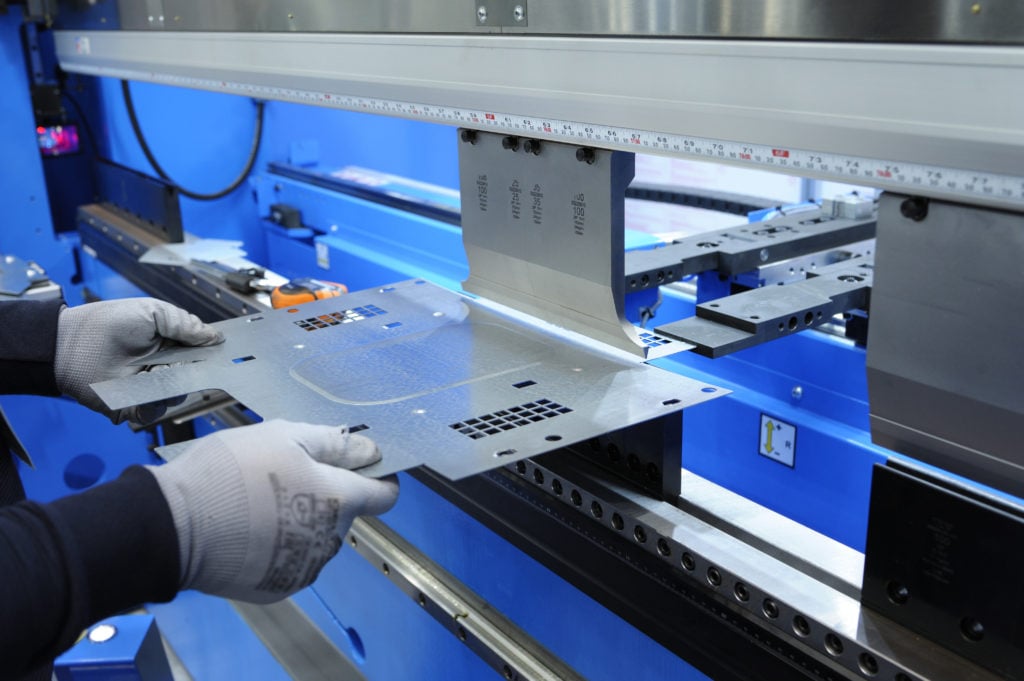
Is There Any Alternative to a Press Brake?
While press brakes are a popular and versatile choice for metal forming, several alternatives can be used depending on the specific requirements of the project. Here are some common alternatives to press brakes:
Panel Benders:
Panel benders are specialized machines designed for automated bending processes. They are well-suited for high-volume production and complex bending operations, offering speed and consistency that might be challenging with a press brake.
Folding Machines:
Folding machines are used to bend sheet metal by clamping the workpiece between a punch and a die, then folding the material around a pivot point. They are particularly effective for creating long, straight folds and are often used in architectural metalwork and enclosure manufacturing.
Roll Forming Machines:
These machines are used for continuous bending of long strips of metal, often coiled steel, into desired cross-sectional profiles. Roll forming is ideal for producing large quantities of complex shapes with a consistent finish.
Press Brake Forming vs Roll Forming: What’s the Difference
Press brake forming is a metalworking process where a press brake machine uses a punch and die to bend sheet metal into desired angles and shapes. The metal is clamped between a punch and a die, and force is applied to achieve the bend;Roll forming involves passing a continuous strip of metal through a series of rollers to gradually shape it into a desired profile. The metal is shaped incrementally as it moves through the rollers.
Feature | Press Brake Forming | Roll Forming |
---|---|---|
Process Overview | Uses a punch and die to bend sheet metal into shapes. | Metal passes through rollers to achieve a continuous profile. |
Точность | High precision with tolerances up to ±0.25 degrees. | Good precision for consistent profiles, less tight tolerances. |
Material Types | Works well with various metals, including aluminum, stainless steel, and light steel. | Suitable for steel, aluminum, and other metals, primarily for continuous lengths. |
Production Volume | Versatile for low and medium production volumes; ideal for custom or batch runs. | Ideal for high-volume production; efficient for long, uniform sections. |
Tooling | Requires specific tools for different bends; higher tooling costs, especially for custom designs. | Requires specific roll sets for each profile; initial tooling costs can be high, but cost-effective for large volumes. |
Преимущества | – High precision and repeatability – Effective for complex and small parts – Reduced springback with proper tooling | – High efficiency for long, continuous parts – Consistent profiles with minimal waste – Low operational costs for high volumes |
Недостатки | – Higher tooling costs and setup times – Limited to specific angles and shapes – Potential for increased tool wear | – Less flexibility for custom or complex shapes – Significant initial tooling costs – Limited to profiles achievable with rolling equipment |
This table provides a concise comparison between press brake forming and roll forming, highlighting their respective features, advantages, and disadvantages.
4 Factors to Consider When Choosing a Fabrication Method
Here are four things to consider before choosing between press braking and roll forming.
1. Length
The length of your parts is essential to the fabrication method you choose.
Longer parts are best used with roll forming over press braking. This is because press braking cannot handle the manufacturing of longer parts.
Press braking material has to be split, sheeted, and cut to length before they can be entered into the press brake. Long parts such as slit coil can be added directly into the roll forming line.
2. Metal Fabrication Design
Consider your fabrication design and the shapes you’ll need before you choose a fabrication method. Press braking and roll forming follow different processes, and each process has varying lengths of time depending on the complexity of the shapes you’re bending.
For instance, press braking can only handle a certain amount of bends, and each one requires a separate hit. But roll forming can form complex linear shapes in one pass, which reduces production time and costs.
3. Material Selection
Some fabrication processes do better with specific materials. The material you select can make the best of your fabrication process and may even save you money.
Press braking and roll forming can form lighter materials such as flat-rolled steel or high-strength low-alloy steel (HSLA). High-strength material is difficult to press brake and roll form.
4. Tooling Costs
Tooling costs are often the same between press braking and roll forming. The price typically depends on the type of project you are doing.
Generally, the larger the volume you use with roll forming, the tooling costs are less expensive for each piece. If the volume is small, then press brake tooling is likely the most cost-effective option.
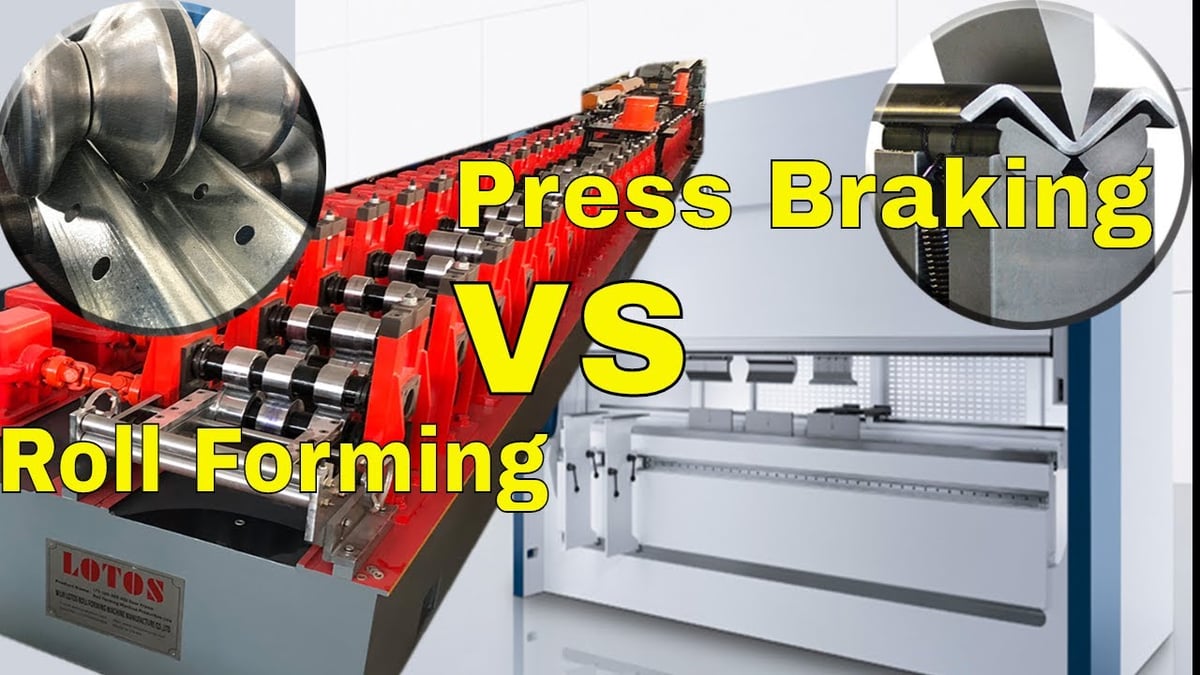
Заключение
From its historical evolution to its modern applications, the press brake forming process is essential across various industries, whether for simple components like brackets or complex parts such as metal shells and structures.
Interested in learning more about press brake forming or seeking expert metal forming services? Reach out to KRRASS. Our team is ready to assist and provide guidance tailored to your needs.
Visit our official website for more details.