CNC hydraulic shearing machines have emerged as indispensable tools in modern metalworking industries, facilitating precise and efficient cutting operations. Integrating computer numerical control (CNC) technology with hydraulic systems, these machines offer unparalleled accuracy and flexibility in metal shearing processes. With CNC capabilities, operators can program intricate cutting patterns and parameters, ensuring consistent results with minimal human intervention.
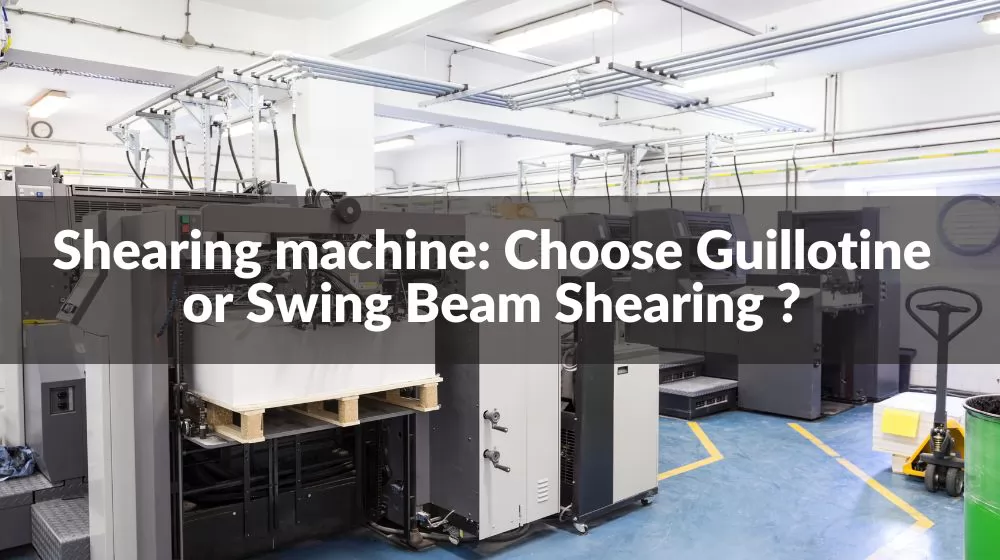
Введение
The decision between a guillotine and a swing beam shear largely depends on the specific requirements of the application. Guillotine shears, characterized by their vertically descending blades, excel in straight-line cutting of thick materials. Their robust construction and powerful hydraulic systems enable them to effortlessly slice through heavy-duty metal sheets with precision.
On the other hand, swing beam shears employ a pivoting upper beam mechanism, making them ideal for cutting thinner materials and complex shapes. This design allows for better visibility of the cutting line and reduces material distortion, particularly in delicate workpieces.
In terms of operation, CNC hydraulic guillotine shears offer straightforward setup and programming, making them suitable for batch production and high-volume cutting tasks. The vertical blade movement ensures uniform force distribution across the entire cutting length, resulting in clean, straight cuts even on thick materials.
Conversely, CNC hydraulic swing beam shears provide enhanced versatility, allowing for angled cuts and intricate shapes with ease. The swinging motion of the upper beam minimizes material deformation and eliminates the need for material repositioning between cuts, improving overall efficiency and accuracy.
What Is A Guillotine Shear
Guillotine Shearing Machine is a kind of metal cutting equipment, commonly used to cut metal sheet according to the required size and shape. It works like a guillotine, hence the name. The Guillotine Shearing Machine consists of a knife frame that moves up and down, and a blade is installed on the knife frame, and the cutting of metal materials is realized through the up and down movement of the knife frame.
During the cutting process, the metal sheet is placed in the cutting area, and then the knife holder is pressed down from above, similar to the movement of the guillotine, so that the metal sheet is cut into the desired shape and size. Guillotine Shearing Machine is often used in sheet metal processing, metal manufacturing, construction and other fields. It has a simple structure and easy operation, and is suitable for cutting metal materials of different thicknesses and sizes.
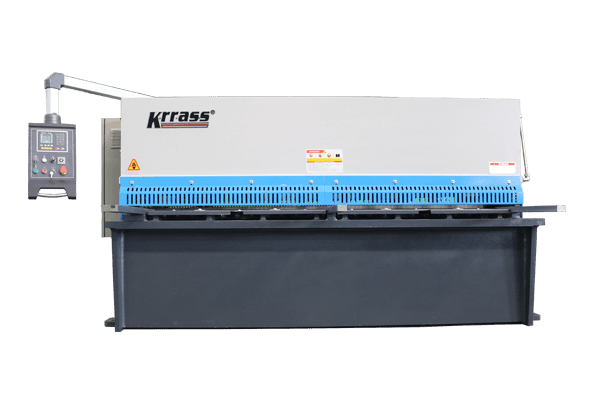
What Is A Swing Beam Shear
Swing Beam Shearing Machine is a kind of metal cutting equipment. Its working principle is to realize the cutting of metal materials through a swinging beam (also known as a swing rod) that moves up and down. During the cutting process, the metal material is placed in the cutting area, and the swing beam swings from above to below to drive the blade to cut the metal material. The Swing Beam Shearing Machine usually has a larger work surface to accommodate sheet metal cutting needs of different sizes.
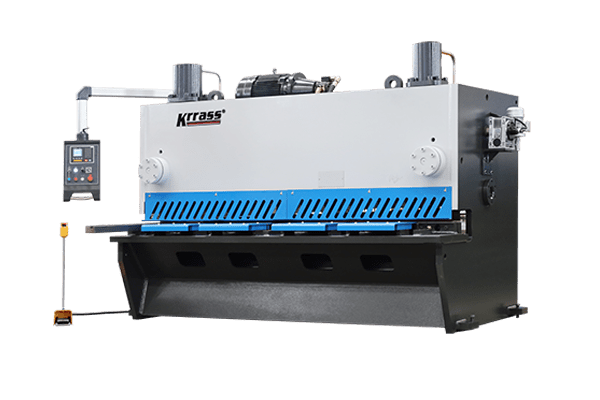
Advantages of Guillotine Shearing Machine
High cutting precision: Guillotine Shearing Machine adopts the design of the upper and lower knife holders, the vertical movement of the knife holder can ensure the precision and consistency of cutting, so as to obtain high-quality cutting results.
Wide range of application: Guillotine Shearing Machine is suitable for cutting metal materials of different types and thicknesses, including steel plate, aluminum plate, stainless steel, etc., making it widely used in various industries.
Easy to operate: Simple design, clear operation interface, easy to operate and control. The operator only needs to master the basic operation skills to complete the cutting task.
Fast cutting speed: The tool holder of Guillotine Shearing Machine moves at a fast speed, which can complete a large number of cutting tasks in a short time and improve production efficiency.
Durable and Reliable: The design is solid, and it is made of durable materials, which has strong durability and stability, and can run stably for a long time.
Easy Blade Replacement: Blades are usually relatively easy to replace for easy maintenance and maintenance to maintain cutting quality and efficiency.
High safety: Guillotine Shearing Machine is usually equipped with safety devices, such as protective cover, emergency stop button, etc., to ensure the safety of operators.
Material saving: The blade layout and motion trajectory during cutting can minimize material waste, resulting in cost savings.
Высокая степень автоматизации: Some Guillotine Shearing Machines are equipped with automatic feeding and discharging systems, which can achieve a higher degree of automation of the cutting process.
Advantages of Swing Beam Shearing Machine
Универсальность: One of the standout features of the Swing Beam Shearing Machine is its versatility. It can handle a wide range of materials, including steel, aluminum, stainless steel, and various alloys. This versatility makes it suitable for a broad spectrum of applications across different industries.
Precision Cutting: The swing beam design allows for precise cutting, even on thin or delicate materials. This ensures high-quality finished products with minimal distortion or warping, meeting the stringent demands of precision engineering and fabrication projects.
Ease of Operation: With its user-friendly interface and intuitive controls, the Swing Beam Shearing Machine is easy to operate. Operators can quickly learn to set up and operate the machine efficiently, minimizing downtime and maximizing productivity.
Reduced Material Waste: The swing beam mechanism minimizes material waste by optimizing the cutting trajectory, resulting in efficient use of raw materials and cost savings for the business.
Enhanced Safety Features: Swing Beam Shearing Machines are equipped with advanced safety features to protect operators during operation. These may include protective covers, emergency stop buttons, and safety interlocks, ensuring a safe working environment.
Low Maintenance Requirements: The robust construction and reliable components of the Swing Beam Shearing Machine contribute to its low maintenance requirements. With proper care and maintenance, the machine can deliver consistent performance over an extended lifespan, reducing overall operating costs.
High Productivity: The efficient cutting process of the Swing Beam Shearing Machine, coupled with its fast operating speed, enables high productivity. This makes it an ideal choice for businesses with high-volume production requirements.
Flexibility in Cutting Length: Swing Beam Shearing Machines are available in various sizes and configurations, offering flexibility in cutting length to accommodate different project requirements. This ensures that businesses can choose the machine size that best fits their production needs.
Shortcomes For Both of Them
Guillotine Shear
- Limited Cutting Thickness: Guillotine shears may struggle with cutting very thick materials, as the blade clearance and cutting capacity are typically limited compared to other types of shearing machines.
- Straight-Cut Only: Guillotine shearing machines are primarily designed for straight-line cuts. They may not be suitable for applications requiring intricate shapes or curved cuts, limiting their versatility in certain fabrication projects.
- Material Distortion: Due to the downward force exerted by the blade during cutting, guillotine shearing machines can sometimes cause material distortion, especially with thinner or softer metals. This distortion can affect the accuracy of the cut and may require additional processing to correct.
- Blade Wear: The blades of guillotine shearing machines are subject to wear over time, especially when cutting abrasive materials or high volumes of metal. Regular blade maintenance and replacement are necessary to ensure optimal cutting performance and accuracy.
- Footprint and Space Requirements: Guillotine shearing machines tend to have a larger footprint compared to other types of shearing machines, requiring more floor space in the workshop or manufacturing facility. This can be a consideration for businesses with limited space availability.
- Operator Skill Required: While guillotine shearing machines are generally straightforward to operate, achieving optimal results may require some skill and experience, particularly when setting blade clearance and adjusting cutting parameters for different materials and thicknesses.
- Noise and Vibration: Guillotine shearing machines can generate significant noise and vibration during operation, which may require additional measures to mitigate noise levels and ensure a comfortable working environment for operators.
- Initial Investment and Maintenance Costs: The initial cost of purchasing a guillotine shearing machine, as well as ongoing maintenance and blade replacement expenses, can be significant. Businesses need to consider these costs alongside the expected return on investment when evaluating the suitability of guillotine shears for their operations.
Swing Beam Shear
- Limited Cutting Thickness: Swing beam shearing machines may not be suitable for cutting very thick materials due to limitations in blade clearance and cutting capacity. They may struggle with materials beyond a certain thickness, requiring alternative cutting methods for thicker metal sheets.
- Restricted Cutting Length: Swing beam shearing machines typically have a fixed cutting length, which may limit their suitability for projects requiring longer cuts or continuous shearing of large workpieces. Businesses with specific cutting length requirements may need to invest in larger or customized machines.
- Complexity in Operation: Compared to simpler shearing machines like guillotine shears, swing beam shearing machines may have a more complex operating mechanism. This complexity can require additional training for operators to fully understand and utilize the machine's capabilities effectively.
- Higher Initial Investment: Swing beam shearing machines tend to have a higher initial cost compared to some other types of shearing machines. The advanced design and features of swing beam shears can result in a larger upfront investment, which may be a consideration for businesses with budget constraints.
- Maintenance Requirements: The swing beam mechanism of these machines may require more frequent maintenance compared to simpler shearing machines. Regular lubrication, adjustment, and inspection of moving parts are necessary to ensure optimal performance and longevity of the machine.
- Reduced Efficiency for Thin Materials: While swing beam shearing machines excel in cutting thicker materials, they may be less efficient when cutting thin or delicate materials. The swinging motion of the beam can cause material vibration and distortion, leading to less precise cuts and potential material waste.
- Limited Versatility in Cutting Shapes: Swing beam shearing machines are primarily designed for straight-line cuts. They may not be suitable for applications requiring intricate shapes or curved cuts, limiting their versatility compared to some other types of shearing machines.
- Footprint and Space Requirements: Like guillotine shearing machines, swing beam shearing machines may have a larger footprint and space requirements in the workshop or manufacturing facility. Businesses with limited space availability may need to consider the space implications of installing a swing beam shear.
Selection Consideration of Guillotine Shearing Machine
- Determine your cutting needs, including material type, thickness, size and cutting volume, in order to choose the appropriate Shearing Machine specifications.
- Consider the cutting precision and consistency you need, and choose a Shearing Machine with stable carriage motion and precise control systems.
- Pay attention to the blade quality of Shearing Machine, high-quality blades can provide longer life and better cutting results.
- Choose a Shearing Machine that is easy to operate and control, with a clear operator interface and user-friendly control system.
- Make sure the Shearing Machine is equipped with the necessary safety devices, such as emergency stop buttons, protective covers, etc., to ensure the safety of the operator.
- Choose a Shearing Machine with solid construction and durable materials to increase the longevity and stability of your equipment.
- Consider the maintenance and upkeep requirements of the Shearing Machine, choose equipment that is easy to maintain and maintain, and reduce downtime.
- Choose a manufacturer or supplier with reliable after-sales service support, so that you can get timely support when repairs or upgrades are required.
- According to budget constraints, choose a cost-effective Shearing Machine to balance the relationship between performance and cost.
- Consider whether the Shearing Machine has advanced technological innovations, such as automatic control, numerical control system, etc., to improve production efficiency and cutting quality.
Factors To Consider When Choose Swing Beam Shear
- Determine your cutting needs, including metal material type, thickness, size and cutting volume, so as to choose the suitable Shearing Machine specification.
- Considering the cutting precision and consistency required, choose a Shearing Machine with stable swinging beam motion and precise control system.
- Make sure that the Swing Beam Shearing Machine can adapt to different types and thicknesses of metal material cutting to meet the needs of a variety of industries.
- Choose a Shearing Machine with intuitive operation interface, easy operation and control to reduce the difficulty of operation.
- Make sure that the Swing Beam Shearing Machine is equipped with necessary safety devices, such as protective covers, emergency stop buttons, etc., to ensure the safety of operators.
- Choose a Shearing Machine with solid construction and durable materials to increase the longevity and stability of your equipment.
- Consider the difficulty of blade replacement and maintenance of the Shearing Machine, choose equipment that is easy to maintain and maintain, and reduce downtime.
- Choose a manufacturer or supplier with reliable after-sales service support for prompt repairs and support.
- According to budget constraints, choose a cost-effective Shearing Machine to balance the relationship between performance and cost.
- Consider whether the Shearing Machine has advanced technological innovations, such as automatic control, numerical control system, etc., to improve production efficiency and cutting quality.
Заключение
In conclusion, the decision between a Guillotine Shearing Machine and a Swing Beam Shearing Machine hinges on specific project requirements and desired outcomes. Each machine offers distinct advantages suited to different applications, ultimately contributing to enhanced productivity and cost-efficiency in metalworking operations.
As a leading manufacturer of CNC machinery, KRRASS specializes in mechanical automation and technology research and development, supported by a dedicated R&D team. For further inquiries or assistance, please do not hesitate to reach out to us. Your success in metalworking is our priority!