Оглавление
The bending process in a CNC press brake involves various techniques and methods to achieve different types of bends in metal fabrication. Here's an introduction to the types of bending processes commonly performed on a CNC press brake:
3 Main Typical Bending Process of CNC Press Brake
Air Bending
In air bending, the punch forces the workpiece into the die, but does not fully penetrate it. Instead, the material is bent to the desired angle while floating above the bottom of the die cavity. This process allows for flexibility in bending angles and minimizes tool wear. Air bending is commonly used for a wide range of applications due to its versatility and ease of setup.
Bottoming (Coining)
Bottoming, also known as coining, involves fully penetrating the workpiece into the die cavity to achieve precise bending angles and high accuracy. The material is forced to conform tightly to the shape of the die, resulting in sharp bends with minimal springback. Bottoming is ideal for applications that require tight tolerances and precise geometric shapes.
Coining
Coining is a variation of bottoming where the punch applies high pressure to the workpiece to produce extremely precise bends. This process is commonly used for forming intricate details, embossing, and creating complex shapes with sharp corners and crisp edges. Coining requires careful control of press parameters to avoid damaging the tooling or workpiece.
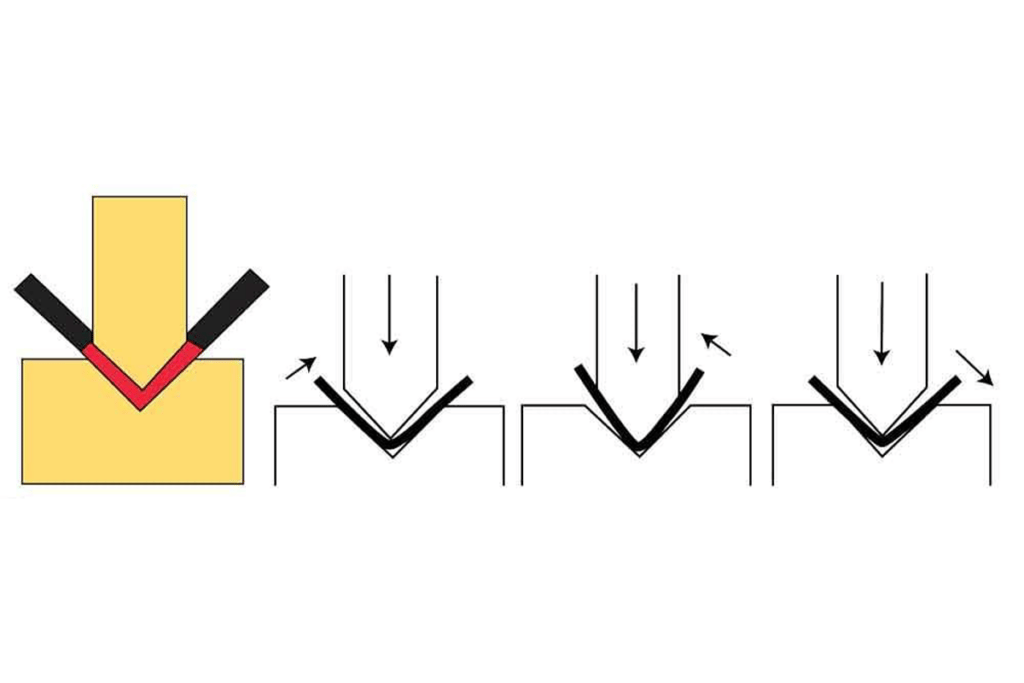
Заключение
These bending processes can be selected based on factors such as material type, thickness, bend angle, and required accuracy. Листогибочные прессы с ЧПУ offer the flexibility to perform multiple bending processes, allowing manufacturers to produce a wide variety of parts and components with high efficiency and accuracy.