Оглавление
What is Laser Cutting and How Does it Work?
Laser cutting is a process where a laser beam is used to cut or engrave materials. The laser, either a carbon dioxide (CO2) or a fiber laser, produces a beam that is directed by mirrors onto the material. The focused beam has a diameter as small as a few microns, comparable to the thickness of a human hair.
Its accuracy depends on several factors, including the type of laser, the power of the laser, and the material being cut. Cutting tolerances are typically within ±0.005 inches, ensuring high precision in manufacturing applications.
How Accurate is Laser Cutting?
The dimensional accuracy of лазерная резка is impressive, usually within ±0.005 inches. The cut width, or laser cutting kerf, can be as narrow as 0.004 inches, depending on the laser power and material thickness.
Laser cutting can focus down to 10-20 microns, showcasing its ability to produce highly intricate and detailed work. This precision is crucial in industries like aerospace, electronics, and automotive, where exacting standards are the norm.
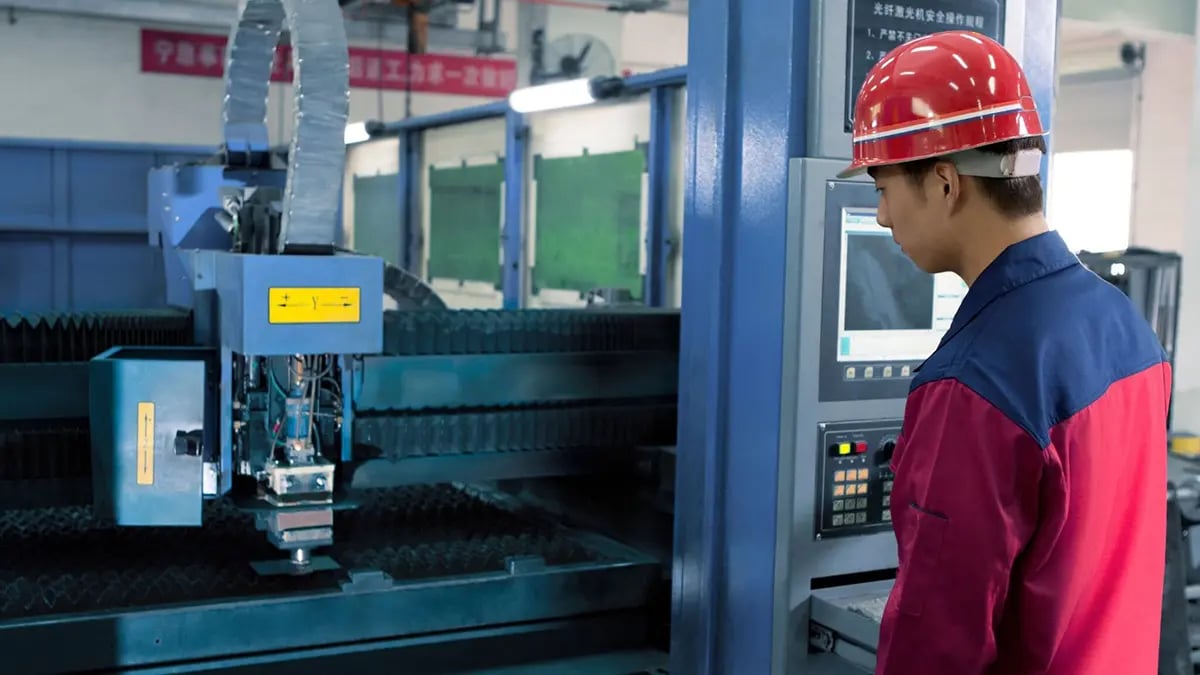
How Does Laser Cutting Compare in Precision to Other Cutting Methods?
Compared to traditional cutting methods like plasma cutters and mechanical cutting tools, laser cutting offers superior precision.
For instance, plasma cutting typically has a tolerance of ±0.020 inches, which is less precise than laser cutting.
Mechanical cutting tools, while versatile, can’t match the intricate detailing possible with laser cutting. The ability to produce complex shapes and designs with high repeatability makes laser cutting a preferred choice for many applications.
Types of Laser Cutters: Which Is the Most Accurate?
Different types of laser cutters offer varying levels of accuracy, each suited to specific materials and applications. The three primary types are fiber laser cutters, CO2 laser cutters, and crystal laser cutters.
Fiber Laser Cutters
Fiber laser cutting technology uses banks of diodes to create a laser that is channeled and amplified through fiber-optic cable. This results in a focused, high-intensity laser beam.
Dimensional Accuracy: Fiber laser cutters are known for their exceptional precision, often achieving tolerances as tight as ±0.003 inches. The focused beam spot size can be extremely small, allowing for intricate cuts and detailed work.
Приложения: Ideal for cutting metals like stainless steel and aluminum, fiber lasers are widely used in industries where precision is paramount, such as aerospace and automotive manufacturing.
Advantages: They offer faster cutting speeds and lower operating costs compared to other types. Their ability to precisely cut thin materials is particularly noteworthy.
CO2 Laser Cutters
CO2 laser cutters use a gas mixture, typically involving carbon dioxide, to produce the laser beam. The beam is then directed and focused using mirrors and lenses.
Dimensional Accuracy: CO2 laser cutters generally provide tolerances around ±0.005 inches. They are highly effective for cutting thicker materials and deliver clean, precise cuts.
Приложения: Commonly used for a wide range of materials, including plastics, wood, and metals. They are a staple in industries like HVAC and signage, where versatility in material cutting is required.
Advantages: These cutters are known for their versatility and are capable of cutting a wide range of materials with high-quality results.
Crystal Laser Cutters
Crystal laser cutters use crystals like neodymium-doped yttrium aluminum garnet (Nd:YAG) to produce the laser beam. These crystals allow for very high-intensity beams.
Dimensional Accuracy: The accuracy of crystal laser cutters is comparable to fiber lasers, often achieving tolerances within ±0.004 inches. They are well-suited for cutting both thin and moderately thick materials.
Приложения: Frequently used for tasks requiring high precision, such as in the medical device and electronics industries.
Advantages: These lasers can handle a variety of materials, including metals, ceramics, and some plastics, with high precision and speed.
What are the Factors That Determine the Precision of Laser Cutting?
In the intricate world of laser cutting, precision is paramount. The accuracy of laser cutters is not a singular attribute but a composite result of several interlinked factors. Understanding these determinants is crucial for any professional in manufacturing applications, from aerospace to electronics, where laser cutting technology plays a pivotal role.
Laser Type: The choice between CO2, fiber, and crystal lasers significantly influences cutting precision. Fiber lasers, for example, offer tighter focus and hence, higher precision, especially for thin materials.
Мощность лазера: Higher-powered lasers can cut thicker materials but might sacrifice precision. Conversely, lower power can enhance accuracy but limit material thickness capabilities.
Толщина материала: Thicker materials often challenge the laser’s ability to maintain precision, as the beam may spread slightly over greater distances.
Тип материала: Different materials respond uniquely to laser cutting. Metals like stainless steel and aluminum might require different settings compared to plastics or wood.
Скорость резки: Faster speeds can reduce cutting time but might compromise accuracy. A balance must be found for optimal precision.
Machine Quality and Maintenance: High-quality laser cutting machines and regular maintenance ensure consistent precision. Worn components or misalignments can significantly affect accuracy.
Environmental Factors: Factors like ambient temperature and humidity can affect both the laser cutter and the material, impacting the cutting precision.
Operator Skill: The experience and expertise of the machine operator play a significant role in achieving high precision in laser cutting.
How Do Cutting Tolerances Influence Laser Cutting Accuracy?
Laser cutting tolerances are critical for achieving high precision in various manufacturing applications. These tolerances refer to the degree of variation permissible in the cutting process.
Kerf Width: The kerf, or the width of the cut, is typically in the range of 0.004 to 0.012 inches for most lasers. This narrow kerf allows for intricate cuts and minimal material waste.
Dimensional Tolerance: Dimensional accuracy generally falls within ±0.005 inches, allowing for precise cuts and fitting parts with high accuracy.
Positioning Tolerance: Positioning tolerance, which refers to the laser’s accuracy in placing cuts, is usually within ±0.002 inches, ensuring that each cut is made exactly where intended.
These tolerances illustrate why laser cutting is favored for its precision, especially in fields requiring intricate details and exact measurements, like electronics and aerospace.