А plasma cutter is a machine used in metalworking to cut through electrically conductive materials such as steel, stainless steel, aluminum, brass, and copper. It utilizes a high-temperature, ionized gas called plasma to melt through the metal and create clean, precise cuts. Here's how a plasma cutter works and its typical uses:
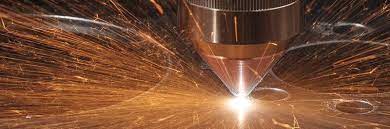
Operation: Plasma cutters work by passing a high-velocity jet of ionized gas (plasma) through a constricted nozzle. This nozzle creates a narrow, focused stream of plasma that reaches temperatures of up to 30,000 degrees Fahrenheit (16,650 degrees Celsius). The intense heat melts the metal, while the high-velocity plasma blows away the molten material, creating a clean cut.
Components: A typical plasma cutting system consists of several key components:
Power Supply: Provides the electrical energy necessary to generate the plasma arc.
Torch: The handheld or mechanized device that directs the plasma jet onto the metal workpiece.
Gas Supply: Supplies the gas (usually compressed air, nitrogen, or oxygen) that is ionized to create the plasma arc.
Control Console: Controls the operation of the plasma cutter, including adjusting cutting parameters such as voltage, current, and gas flow.
Универсальность: Plasma cutting is versatile and can be used to cut a wide range of thicknesses, from thin sheet metal to thick plates, depending on the power of the plasma cutter. It is commonly used in various industries, including metal fabrication, automotive repair, construction, and manufacturing.
Точность: Plasma cutting can achieve high levels of precision and accuracy, making it suitable for intricate designs and complex shapes. CNC (Computer Numerical Control) plasma cutting systems further enhance precision by automating the cutting process based on digital designs or patterns.
Speed: Plasma cutting is generally faster than traditional methods such as oxy-fuel cutting or mechanical sawing. It allows for rapid cutting speeds, reducing production time and increasing efficiency.
Clean Cuts: Plasma cutting produces clean, smooth cuts with minimal dross (residue) and distortion, especially when performed using high-quality equipment and appropriate cutting parameters.
Cost-Effectiveness: While the initial investment in a plasma cutting system may be significant, its versatility, speed, and efficiency often result in cost savings over time, particularly for high-volume production or repetitive cutting tasks.
Overall, plasma cutting machines offer a fast, precise, and versatile solution for cutting metal, making them indispensable tools in various industries involved in metal fabrication and manufacturing.
Using Consumables Until They Burn Out
Consumables in a plasma cutter include items like electrodes, nozzles, and shields. These components play crucial roles in ensuring the smooth operation of the cutter. If these parts are used until they are entirely worn out or “blown,” the quality of the cuts may be compromised, resulting in uneven edges and inaccurate dimensions. Regularly inspecting consumables and making timely replacements can help maintain optimal performance of your plasma cutter.
Improper Torch Assembly and Cleaning
A properly assembled and clean torch is essential for a plasma cutter to function efficiently. An improperly assembled torch can result in poor cut quality and may even lead to equipment damage.
Similarly, neglecting to clean the torch tip can cause build-up of slag and dross, which can hinder the plasma arc and affect the cut quality. It’s important to ensure that the torch is correctly assembled and the tip is kept clean to avoid these issues.
Attempting To Cut the Wrong Kind of Metals
A robotic plasma cutter is a versatile tool capable of cutting various types of metals. However, not all metals are suitable for plasma cutting. For instance, attempting to cut highly reflective metals like aluminum and copper can result in the deflection of the plasma arc, causing damage to the torch or poor cut quality. And for plasma cutters to work, the workpiece must be electrically conductive. A plasma cutter can’t make good cuts in metals with low conductivity, such as tungsten, tin, and manganese. It is essential to understand the limitations of your plasma cutter and ensure that the metal you are cutting is suitable for plasma cutting.
Setting the Wrong Height or Pressure
The height at which the torch is set and the pressure of the plasma gas significantly impact the quality of the cut. Setting the wrong height or pressure can lead to problems such as angularity, dross, and warping. It is paramount to follow the manufacturer’s guidelines on the correct height and pressure settings for different materials and thicknesses to achieve the best cut quality.