Оглавление
Развитие лазерной резки
Развитие технологии лазерной резки стало значительным шагом вперед в процессах производства и изготовления. Вот краткий обзор основных этапов развития лазерная резка:
Изобретение лазера (1960-е годы): Концепция лазера (усиление света путем вынужденного излучения) была впервые предложена учеными в 1950-х годах, а первый работающий лазер был разработан в 1960 году. Это новаторское изобретение проложило путь для многочисленных применений, включая лазерную резку.
Ранние эксперименты (1960-1970-е годы): В ранние годы лазерной технологии исследователи проводили эксперименты по изучению ее потенциальных применений. Ранние эксперименты по лазерной резке включали использование CO2-лазеров для резки таких материалов, как металлы, пластики и ткани.
Промышленное внедрение (1980-е годы): К 1980-м годам достижения в области лазерных технологий привели к коммерциализации систем лазерной резки для промышленного применения. CO2-лазеры стали предпочтительным выбором для промышленной лазерной резки благодаря своей способности резать широкий спектр материалов с высокой точностью и эффективностью.
Достижения в области лазерных технологий (1990-е–2000-е годы): В течение 1990-х и 2000-х годов были достигнуты значительные успехи в лазерной технологии, что привело к улучшению скорости резки, точности и универсальности. Волоконные лазеры, которые используют оптические волокна для генерации лазерных лучей, появились как альтернатива CO2-лазерам, предлагая такие преимущества, как более высокая скорость резки и более низкие эксплуатационные расходы.
Интеграция технологии ЧПУ: Интеграция технологии числового программного управления (ЧПУ) с системами лазерной резки произвела революцию в отрасли. Контроллеры ЧПУ обеспечили точный контроль над процессом резки, что позволило с легкостью вырезать сложные формы и конструкции.
Диверсификация применений: По мере развития технологии лазерной резки ее применение диверсифицировалось в различных отраслях, включая автомобилестроение, аэрокосмическую промышленность, электронику, медицинские приборы и архитектурный дизайн. Лазерная резка стала предпочтительным методом резки сложных узоров, контуров и прототипов в этих отраслях.
Достижения в области автоматизации и робототехники: В последние годы наблюдается тенденция к автоматизации и интеграции робототехники в системы лазерной резки. Автоматизированная обработка материалов, сортировка деталей, роботизированная загрузка и выгрузка еще больше повысили производительность и эффективность операций лазерной резки.
Новые тенденции: Заглядывая вперед, текущие исследования и разработки продолжают стимулировать инновации в технологии лазерной резки. Новые тенденции включают разработку гибридных систем лазерной резки, аддитивное производство с использованием лазерного осаждения и достижения в лазерных источниках и оптике для улучшения производительности резки.
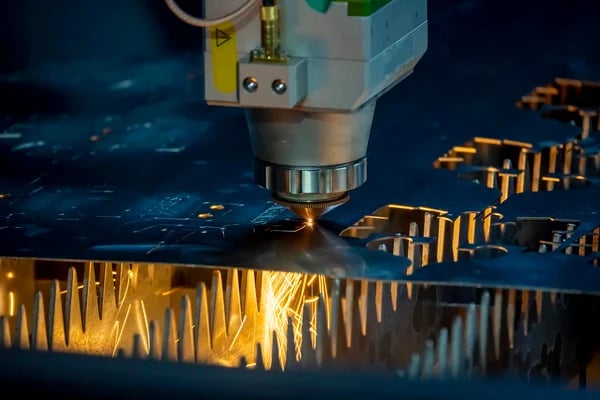
Что такое лазерная резка и как она работает
Лазерная резка использует мощный лазер, который направляется через оптику и числовое программное управление (ЧПУ) для направления луча или материала. Обычно процесс использует систему управления движением для следования за ЧПУ или G-кодом рисунка, который должен быть вырезан на материале. Сфокусированный лазерный луч сжигает, плавит, испаряется или сдувается струей газа, оставляя высококачественную обработанную поверхность.
Лазерный луч создается путем стимуляции лазерных материалов посредством электрических разрядов или ламп внутри закрытого контейнера. Лазерный материал усиливается путем внутреннего отражения через частичное зеркало до тех пор, пока его энергия не станет достаточной для выхода в виде потока когерентного монохроматического света. Этот свет фокусируется на рабочей области зеркалами или волоконной оптикой, которые направляют луч через линзу, которая его усиливает.
В самой узкой точке диаметр лазерного луча обычно составляет менее 0,0125 дюйма (0,32 мм), но возможна ширина пропила до 0,004 дюйма (0,10 мм) в зависимости от толщины материала.
Если процесс лазерной резки необходимо начать в любом месте, кроме края материала, используется процесс прокалывания, при котором импульсный лазер высокой мощности проделывает отверстие в материале. Например, для прожигания листа нержавеющей стали толщиной 0,5 дюйма (13 мм) требуется 5–15 секунд.
Лазерная резка использует мощный лазер, который направляется через оптику и числовое программное управление (ЧПУ) для направления луча или материала. Обычно в процессе используется система управления движением для следования за ЧПУ или G-кодом рисунка, который должен быть вырезан на материале. Сфокусированный лазерный луч сжигает, плавится, испаряется или сдувается струей газа, оставляя высококачественную обработанную поверхность.
Лазерный луч создается путем стимуляции лазерных материалов посредством электрических разрядов или ламп внутри закрытого контейнера. Лазерный материал усиливается путем внутреннего отражения через частичное зеркало до тех пор, пока его энергия не станет достаточной для выхода в виде потока когерентного монохроматического света. Этот свет фокусируется на рабочей области зеркалами или волоконной оптикой, которые направляют луч через линзу, которая его усиливает.
В самой узкой точке диаметр лазерного луча обычно составляет менее 0,0125 дюйма (0,32 мм), но возможна ширина пропила до 0,004 дюйма (0,10 мм) в зависимости от толщины материала.
Если процесс лазерной резки необходимо начать в любом месте, кроме края материала, используется процесс прокалывания, при котором импульсный лазер высокой мощности проделывает отверстие в материале. Например, для прожигания листа нержавеющей стали толщиной 0,5 дюйма (13 мм) требуется 5–15 секунд.
Тип лазерной резки
Этот процесс можно разбить на три основных метода: лазер CO2 (для резки, сверления и гравировки), а также неодимовый (Nd) и неодимовый иттрий-алюминиевый гранат (Nd:YAG), которые идентичны по принципу действия, при этом Nd используется для высокоэнергетического сверления с малым количеством повторений, а Nd:YAG — для сверления и гравировки с очень высокой мощностью.
Для сварки можно использовать все типы лазеров.
CO2-лазеры используют пропускание тока через газовую смесь (возбуждение постоянным током) или, что более популярно в наши дни, используют более новую технику радиочастотной энергии (возбуждение радиочастотами). Метод RF имеет внешние электроды и, таким образом, позволяет избежать проблем, связанных с эрозией электродов и осаждением материала электродов на стеклянную посуду и оптику, которые могут возникнуть при постоянном токе, где электрод находится внутри полости.
Другим фактором, который может повлиять на производительность лазера, является тип потока газа. Распространенные варианты CO2-лазера включают быстрый осевой поток, медленный осевой поток, поперечный поток и пластинчатый. Быстрый осевой поток использует смесь углекислого газа, гелия и азота, циркулируемую с высокой скоростью турбиной или нагнетателем. Лазеры с поперечным потоком используют простой нагнетатель для циркуляции газовой смеси с более низкой скоростью, в то время как пластинчатые или диффузионные резонаторы используют статическое газовое поле, которое не требует давления или стеклянной посуды.
Для охлаждения лазерного генератора и внешней оптики также используются различные методы в зависимости от размера и конфигурации системы. Отработанное тепло может передаваться непосредственно в воздух, но обычно используется охлаждающая жидкость. Вода является часто используемой охлаждающей жидкостью, часто циркулирующей через систему теплопередачи или охлаждения.
Одним из примеров лазерной обработки с водяным охлаждением является лазерная микроструйная система, которая соединяет импульсный лазерный луч с водяной струей низкого давления для направления луча таким же образом, как оптическое волокно. Вода также обеспечивает преимущество удаления мусора и охлаждения материала, в то время как другие преимущества по сравнению с «сухой» лазерной резкой включают высокую скорость резки, параллельный пропил и всенаправленную резку.
Волоконные лазеры также набирают популярность в металлорежущей промышленности. Эта технология использует твердую среду усиления, а не жидкость или газ. Лазер усиливается в стеклянном волокне, чтобы создать гораздо меньший размер пятна, чем тот, который достигается с помощью методов CO2, что делает его идеальным для резки отражающих металлов.
Преимущества лазерной резки включают в себя:
Точность: лазерная резка обеспечивает высокий уровень точности и повторяемости, что делает ее идеальной для изготовления сложных форм с жесткими допусками.
Универсальность: лазерную резку можно использовать для самых разных материалов, включая металлы, пластик, дерево и многое другое.
Скорость: Лазерная резка — быстрый и эффективный процесс, позволяющий оперативно изготавливать детали и компоненты.
Минимальные отходы материала: лазерная резка создает узкие пропилы, что обеспечивает минимальные отходы материала и более высокий коэффициент его использования.
Чистые края: лазерная резка позволяет получить чистые, гладкие края без необходимости вторичной обработки.
Бесконтактная резка: поскольку лазерный луч физически не касается материала, риск повреждения или деформации заготовки минимален.
Автоматизация: системы лазерной резки можно легко интегрировать с автоматикой и робототехникой для повышения производительности и эффективности.