Panel Bender Machines, often referred to as Automatic Panel Benders or Panel Bending Machines, are pivotal in modern metal fabrication. These advanced machines are engineered to provide unparalleled precision, efficiency, and versatility in the bending of sheet metal, catering to various industrial applications such as automotive, aerospace, and appliance manufacturing.
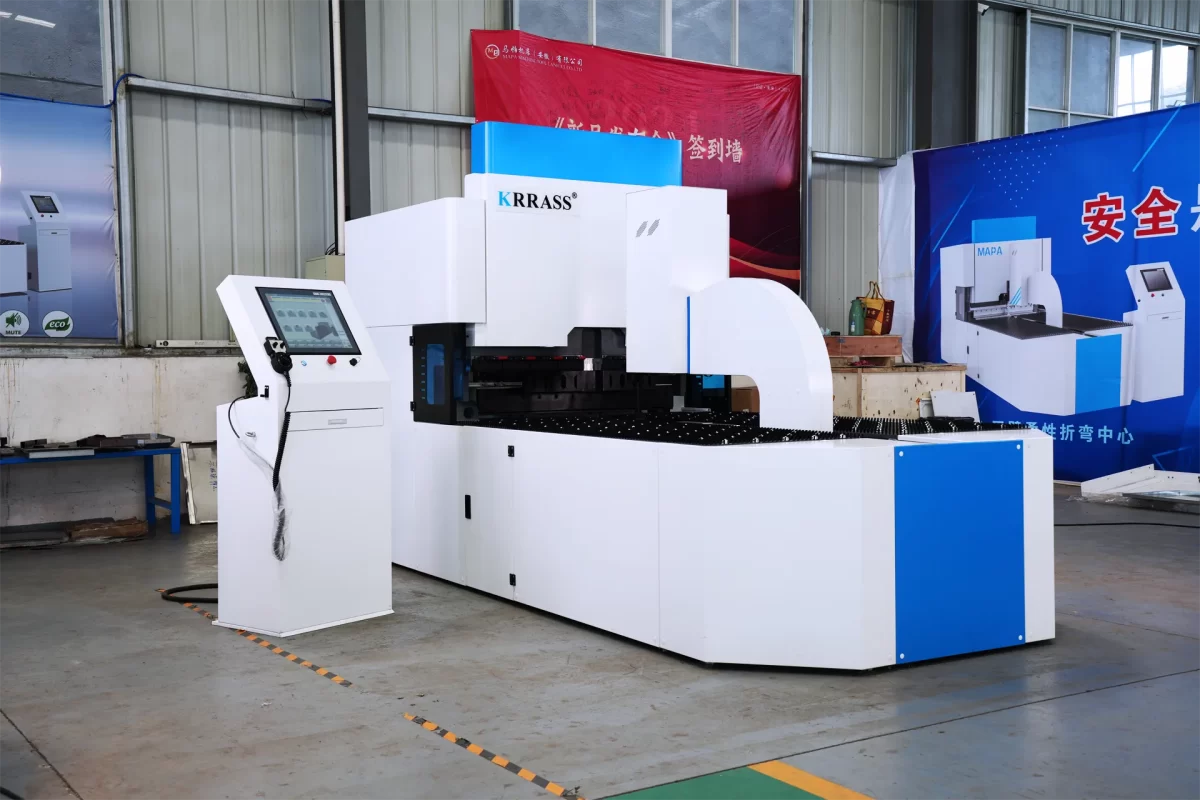
Оглавление
Key Features and Specifications
1. Precision Engineering and Versatility
Panel Bender Machines are renowned for their precise bending capabilities. They utilize advanced servo-electric technology to ensure accurate and consistent bends across various materials, including steel, aluminum, and more. The universal tooling system allows these machines to handle a wide range of materials and thicknesses without the need for frequent tool changes, significantly enhancing productivity and reducing downtime.
- Max Bending Length: 2500mm
- Max Sheet Width: 1500mm
- Max Bending Height: 170mm
- Min Sheet Thickness: 0.35mm
- Max Bending Speed: 0.5s per bend
- Bending Angle Range: ±180°
2. Automation and Efficiency
The automation capabilities of these machines are a major advantage, enabling businesses to streamline operations and improve efficiency. Features include robotic loading and unloading, automated tool changes, and real-time adjustment capabilities. This level of automation minimizes human error and maximizes production throughput.
3. Robust Construction and Durability
Panel Bender Machines are built to last, with robust construction that ensures long-term stability and precision. High-quality materials and components are used to withstand the rigors of continuous operation, maintaining consistent performance over time. The high-precision, temperature-controlled frame further enhances the machine's durability and accuracy.
4. Energy Efficiency
Modern Panel Bender Machines are designed to be energy-efficient, utilizing a full servo-electric system that minimizes electrical consumption. This not only reduces operational costs but also supports sustainable manufacturing practices by lowering the carbon footprint.
5. User-Friendly Interface
Equipped with advanced control systems, these machines offer a user-friendly interface that simplifies operation. Operators can easily program and monitor the bending process, making adjustments on-the-fly to optimize performance and ensure high-quality results.
6. Universal Tooling
The Flexible Panel Bender Machine bends the sheet metal with one universal tooling, able to bend various complex shapes.
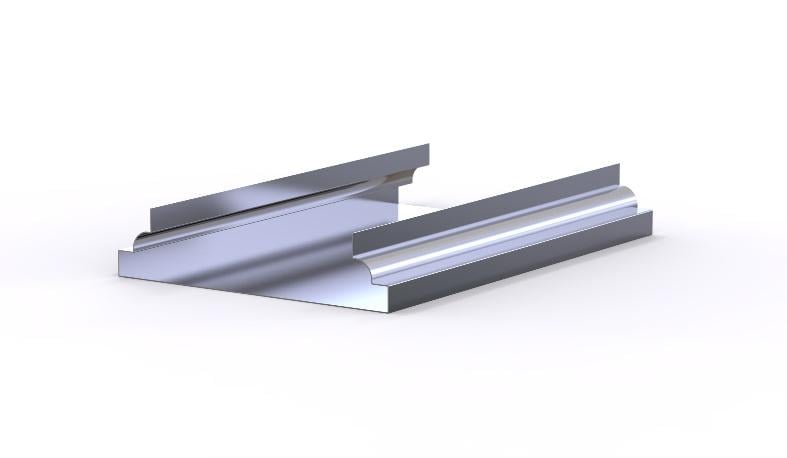

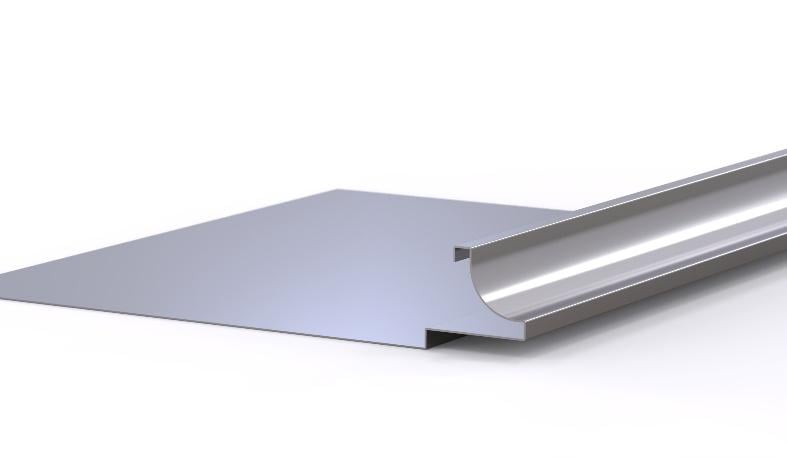
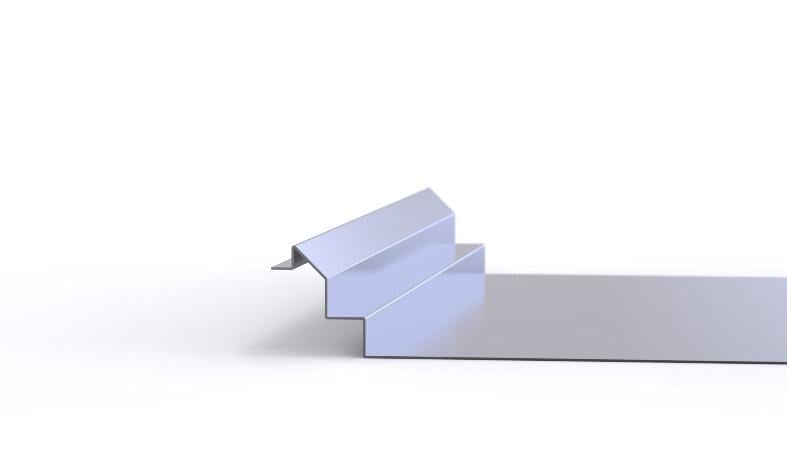
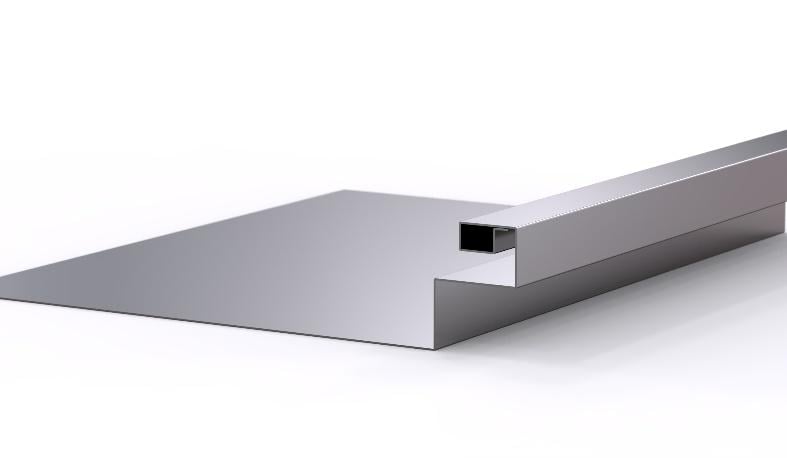
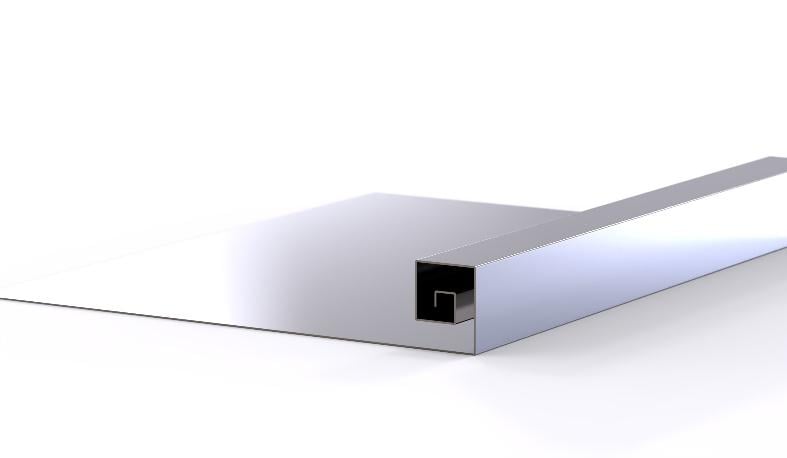
Auxiliary tool system makes the Panel Bender a highly versatile bending equipment, allowing a wide range of special bendings.
Practical Applications and Industry Use Cases
Panel Bending Machines are essential for high-precision bending tasks in various industries. Their ability to produce intricate shapes with minimal manual input makes them indispensable in high-volume production environments. Key industries that benefit from these machines include:
- Automotive Industry: Manufacturing complex components with precise bends.
- Аэрокосмическая промышленность: Fabricating parts that require stringent tolerances and reliability.
- Appliance Manufacturing: Producing parts for household appliances with consistent quality.
- Construction and Architecture: Creating customized metal panels and components for building projects.
Applications of Panel Bender
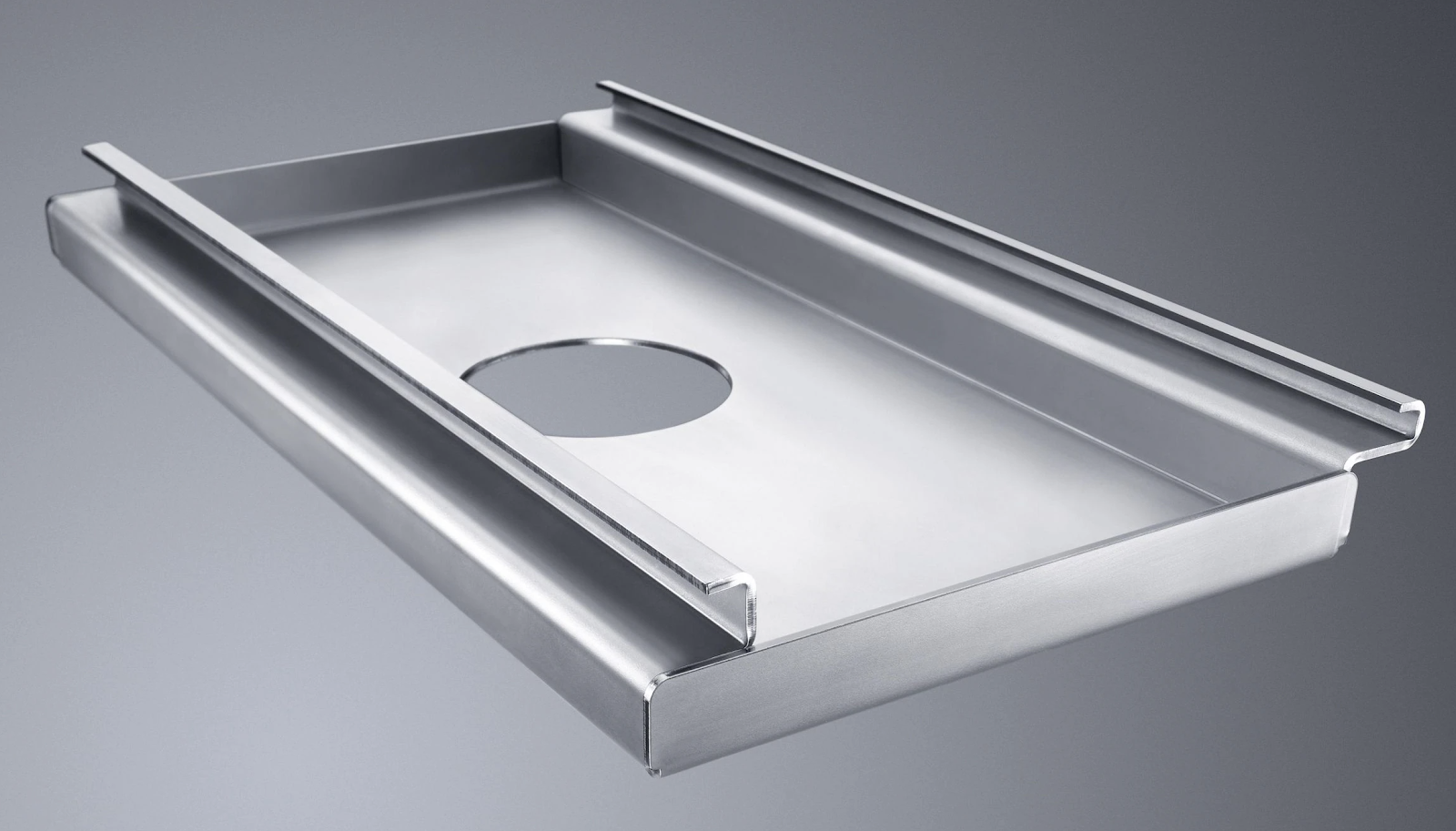
Mild steel housing cover
Maximum accuracy, even in thicker materials.
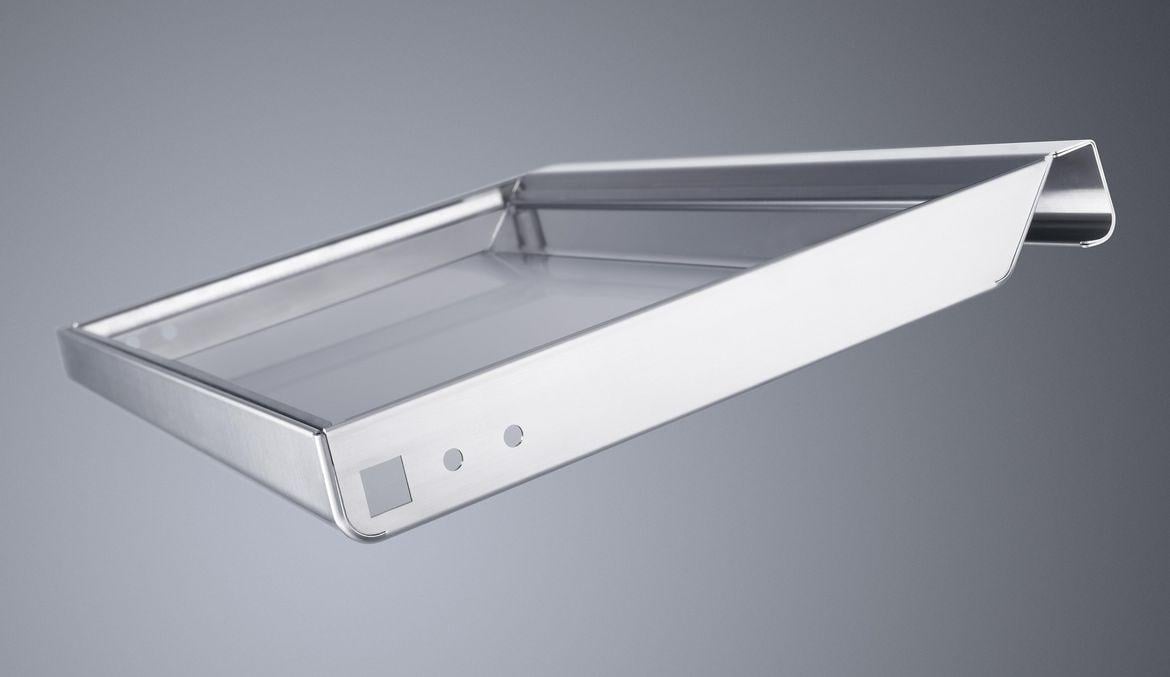
Stainless steel drawer
Radius bending with double sheet.
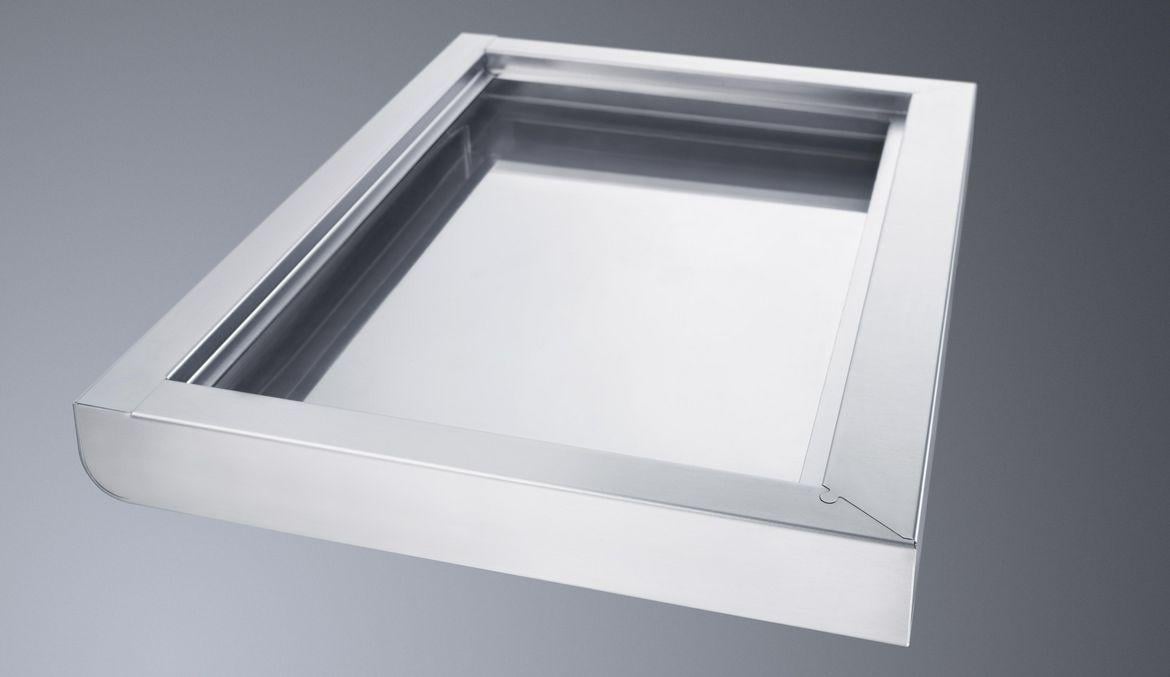
Stainless steel screen trim
Short sides combined with radius bending.
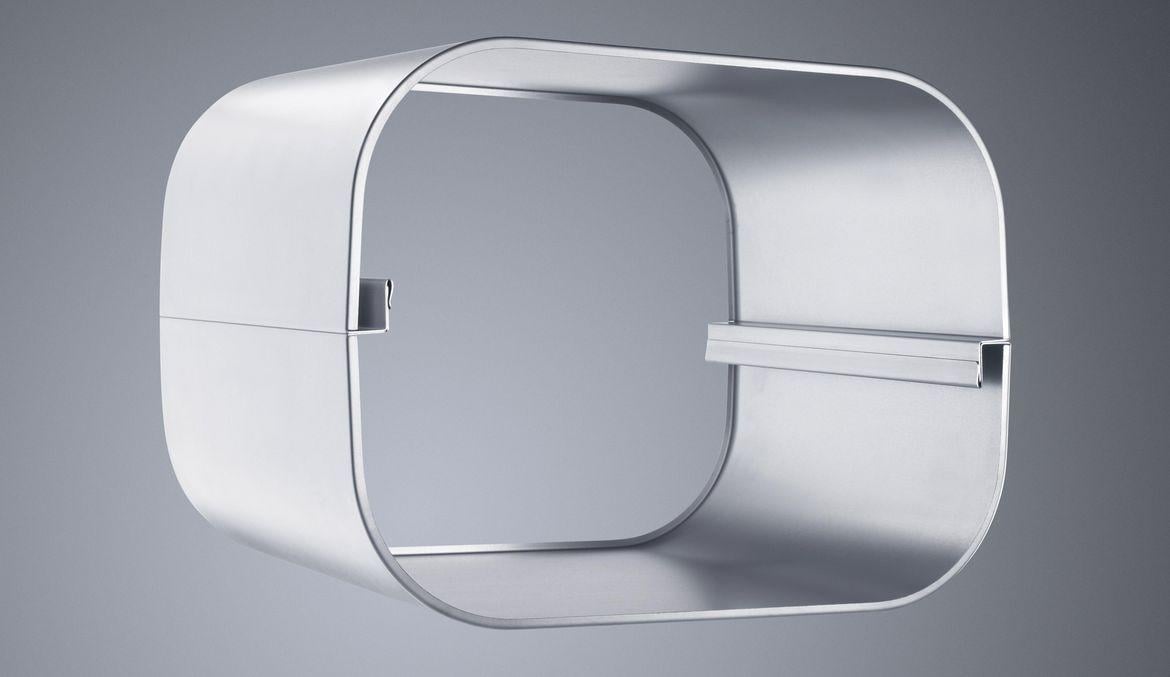
Mild steel container
Maximum accuracy during production.
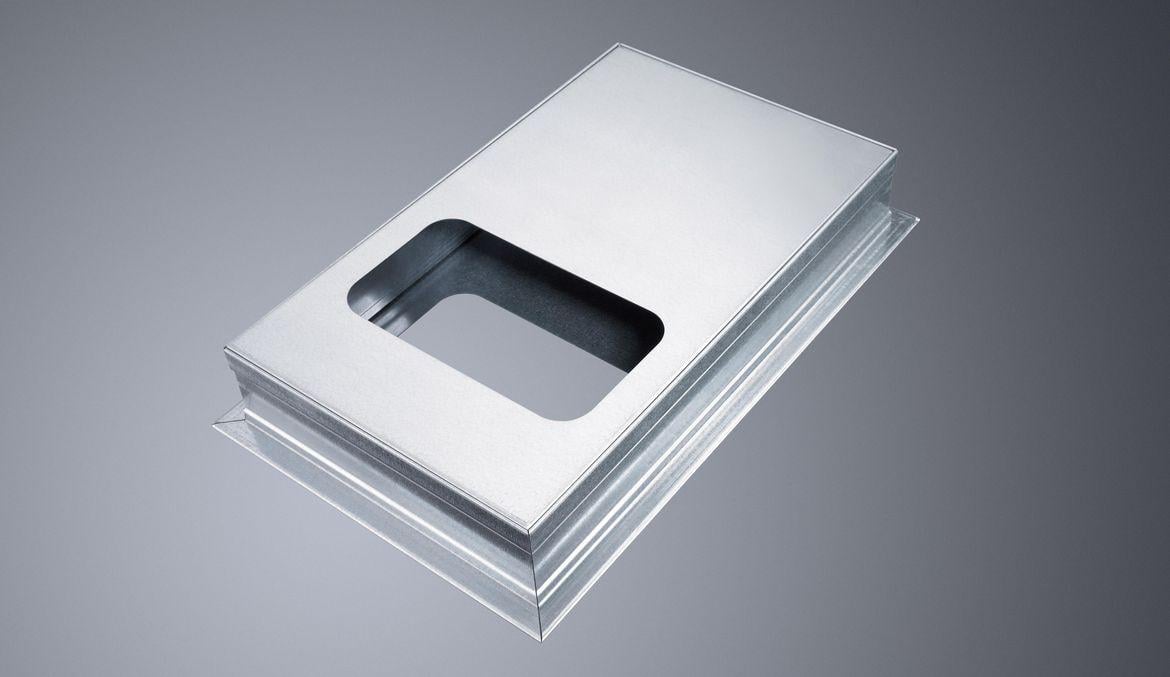
Mild steel guard plate
High repetition accuracy for a variety of bends.
Comparing Press Brakes and Panel Benders
In the metal fabrication industry, both жимовые тормоза and panel benders are tools used for bending sheet metal, but they differ in performance, efficiency, and application.
Bending Quality
Press brakes can produce high precision bends and are preferable for complex parts. They can work with different materials and thicknesses while maintaining a high-quality bend. Panel benders, on the other hand, ensure consistent bending angles, which is conducive for high volumes of identical parts.
Operational Speed
Panel benders are typically faster than press brakes due to their automated nature. They can quickly process parts without human intervention once set up. Press brakes, especially manual ones, require an operator to position and reposition the metal, resulting in a slower operation.
Versatility
Press brakes offer a higher level of versatility. Operators can use a variety of tooling to achieve different bends and angles. On the contrary, panel benders are limited to the types of bends they can execute, making them less versatile but more specialized.
Setup and Changeover Time
Setting up a press brake can be time-intensive, especially for complex parts requiring multiple tools and setups. Panel benders, equipped with automatic tool changing systems, minimize setup time, making them ideal for shorter runs with varied part designs.
Learning Curve
Operating a press brake effectively requires skilled operators with a deep understanding of the tooling and bending processes, contributing to a steeper learning curve. Panel benders have more automated processes, which simplifies their operation and requires less training.
Cost of Operation
When considering the cost of operation, press brakes generally have a lower initial investment but can incur higher labor costs over time. Panel benders, while more expensive upfront, can result in lower labor costs due to their automation and efficiency.
Advancements in Bending Technology
The bending machine industry has seen significant advancements with the integration of automation and innovative technologies in press brakes and panel benders.
Automation in Press Brakes
Modern press brakes have incorporated automated features that boost productivity and precision. For example, CNC backgauges have become standard, allowing operators to make precise bends with minimal input. Many press brakes now offer automatic tool changers which reduce setup time dramatically. These features help manufacturers to produce complex parts consistently and in less time.
Innovations in Panel Bending
Panel bending technology has progressed with the introduction of features that enhance flexibility and efficiency. Adaptive bending technology is one recent innovation, enabling machines to adjust bend angles on-the-fly for perfect results. Additionally, sophisticated software controls have been developed that allow for quick programming and simulation of bending processes, reducing the likelihood of errors and material waste. Manufacturers can also benefit from robotic panel benders that automate the entire bending cycle for increased output and improved worker safety.
Selection Considerations
To determine the most suitable machine for a metal forming task, one must evaluate certain key factors. The choice between a press brake and a panel bender can significantly impact efficiency, precision, and cost-effectiveness.
Assessing Material Thickness
- Press Brake: Ideal for a wide range of material thicknesses. Capability: Handles from thin sheets up to very thick plates.
- Panel Bender: Best suited for thinner materials. Limitation: Typically, less effective with material thickness exceeding a certain limit.
Thickness is a critical factor in choosing the appropriate equipment. The press brake's versatility allows it to work effectively with both thin and thick materials, while a panel bender's capabilities may be constrained once the material exceeds a specific thickness.
Evaluating Production Volume
- Press Brake: Flexible for low to medium production volumes. Setup Time: Longer setup times may affect efficiency in high-volume scenarios.
- Panel Bender: Highly efficient for high production volumes. Автоматизация: Capable of continuous operation with minimal intervention.
Production volume dictates the choice between the two. For lower volumes, the press brake is often sufficient; however, the panel bender shines in high-volume production environments due to its automated processes.
Analyzing Job Complexity
- Press Brake: Offers high flexibility for complex bending jobs. Универсальность: Can accomplish a variety of complex bends with appropriate tooling.
- Panel Bender: More limited when dealing with complex geometries. Design Restrictions: Best for parts with simple bends and profiles.
The complexity of the bending job is a crucial consideration. A press brake has the advantage of dealing with complex bending operations that require different angles and tool changes, while a panel bender is cost-efficient for more straightforward jobs with repeated simple bends.
Industry Perspectives
In exploring the use of press brakes versus panel benders, industry experts note significant efficiencies and evolving preferences in sheet metal fabrication.
Sheet Metal Fabrication Trends
The sheet metal fabrication industry continually adapts to new technologies and processes to enhance productivity and quality. Листогибочные прессы have long been a staple in the industry due to their versatility in handling diverse job requirements. They can be programmed to perform a wide range of bends, making them suitable for low to medium-volume jobs. Panel benders, on the other hand, cater to high-efficiency production. With the ability to automate and reduce manual intervention, these systems are rapidly becoming the go-to for high-volume, repetitive tasks. The trend also gravitates towards lean manufacturing processes, which prioritize minimal waste and shorter lead times.
- Adoption Rates: Increased adoption of panel benders in high-volume environments.
- Versatility: Press brakes remain preferred for their adaptability to custom jobs.
Case Studies: Press Brake vs Panel Bender Use
Case studies across various manufacturing sectors provide concrete examples of the decision-making process behind selecting press brakes or panel benders. For instance, a custom fixtures manufacturer noted a 30% increase in productivity after transitioning to a panel bender for their repeat orders, while a prototype development workshop continues to rely on the precision and flexibility of their press brake for varied, low-volume projects.
Case Study Example Machine Used Outcome Custom Fixtures Manufacturer Panel Bender 30% Productivity Increase Prototype Development Workshop Press Brake Maintained Diverse Production Capabilities
How to choose between a press brake and a panel bender Machine?
When choosing between a press brake and a panel bender, manufacturers should consider the specific needs of their production processes. Press brakes are versatile, making them suitable for varied metal bending tasks, and are available in a range of sizes and capacities. Panel benders, on the other hand, offer speed and consistency for high-volume or large batch processing, especially for rectangular parts.
Key Considerations:
- Production Volume: Panel benders excel in high-volume scenarios.
- Complexity of Parts: Press brakes are preferable for complex bends.
- Автоматизация: Panel benders often integrate more easily with automated systems.
- Гибкость: Press brakes provide a wider range of applications.
- Расходы: Initial investment for panel benders is typically higher.
- Setup Time: Panel benders generally have shorter setup times.
The ultimate decision should align with an organization's operational requirements, balancing factors such as the variety of parts produced, the throughput needed, and budget constraints. Each machine brings its own advantages:
- Press Brake: Cost-effective, adaptable to complex shapes, and scalable from small shops to large factories.
- Panel Bender: Efficient for repetitive tasks, less labor-intensive, and increased precision for certain part geometries.
Detailed Benefits and Advantages
1. Increased Productivity
By automating repetitive tasks, Automatic Panel Benders significantly increase productivity. The advanced automation features reduce the need for manual intervention, allowing operators to focus on more complex tasks and ensuring a faster production cycle.
2. Enhanced Precision and Consistency
The use of servo-electric technology and high-precision components ensures that each bend is consistent and accurate. This level of precision is crucial for industries where even minor deviations can lead to significant issues in the final product.
3. Cost Savings
Energy-efficient designs and reduced tool changeover times contribute to lower operational costs. The machines' ability to handle various materials and thicknesses without frequent tool changes also reduces the need for additional tooling, leading to further cost savings.
4. Flexibility and Adaptability
Panel Bender Machines can be easily integrated into existing production lines, offering flexibility and adaptability to changing production needs. The machines can handle a wide range of materials and thicknesses, making them suitable for various applications.
5. Improved Safety
Automation features such as robotic loading and unloading minimize the need for manual handling of materials, reducing the risk of workplace injuries. The user-friendly interface and real-time monitoring capabilities also enhance operational safety by allowing operators to quickly identify and address potential issues.
Заключение
Panel Bender Machines represent a significant advancement in sheet metal fabrication technology. Their precision, automation capabilities, robust construction, and energy efficiency make them an excellent investment for businesses looking to enhance their production capabilities. By integrating these machines into their operations, companies can achieve higher productivity, better quality, and reduced operational costs.
For more detailed information on specific models and features, exploring additional resources and product pages will provide comprehensive insights into the capabilities and benefits of Panel Bender Machines.