Safety is of utmost importance in CNC press brake operations to protect operators and prevent accidents. Several safety devices are commonly used to ensure safe operation:
Types of Safety Device for CNC Press Brake
Table of Contents
Machine Covering
Fixed safety devices consisting of CNC press brake MP3003CNC are the side shields to prevent manipulation of tooling on the sides and guards at the rear of the machine covering the belts and pulleys of the rear gauge.
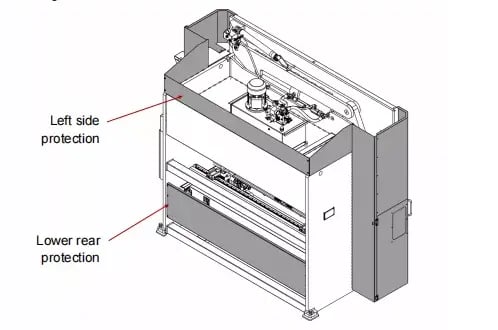
Laser Protection
The protection devices used for press brake machines are mainly set up near the tip of the upper die of the press brake to protect the area, forming a laser protection area at 2-3mm below the upper die. During the use of the press brake, the light emitter and light receiver of the bending machine protection device can move with the movement of the upper die, always keeping 2-3mm from the upper die.
If a worker’s finger enters the protective area, it will block the beam and the bending machine will immediately stop and effectively prevent finger-crushing accidents. So press brake safety devices are very important.
DSP Laser
The DSP laser protection devices used for press brakes comprehensively protects the personal safety of the press brake operator and avoids the dangers arising from the rapid movement of the slide of the machine. For the bending tooltip, a block is formed to protect the front, middle and rear areas of the tooltip. Aluminum profile bracket for easy installation, adjustable in several orientations, equipped with a scale to adjust the position of the light curtain according to the different heights of the tool.
The protective zone is fixed under the tooltip and moves in sync with the die, ensuring that any object underneath the die at high speed must first enter the DSP-generated protective zone before it touches the tooltip. As soon as an obstruction (worker’s finger) enters the DSP protection zone, the DSP signals and interrupts the downward movement of the ram.
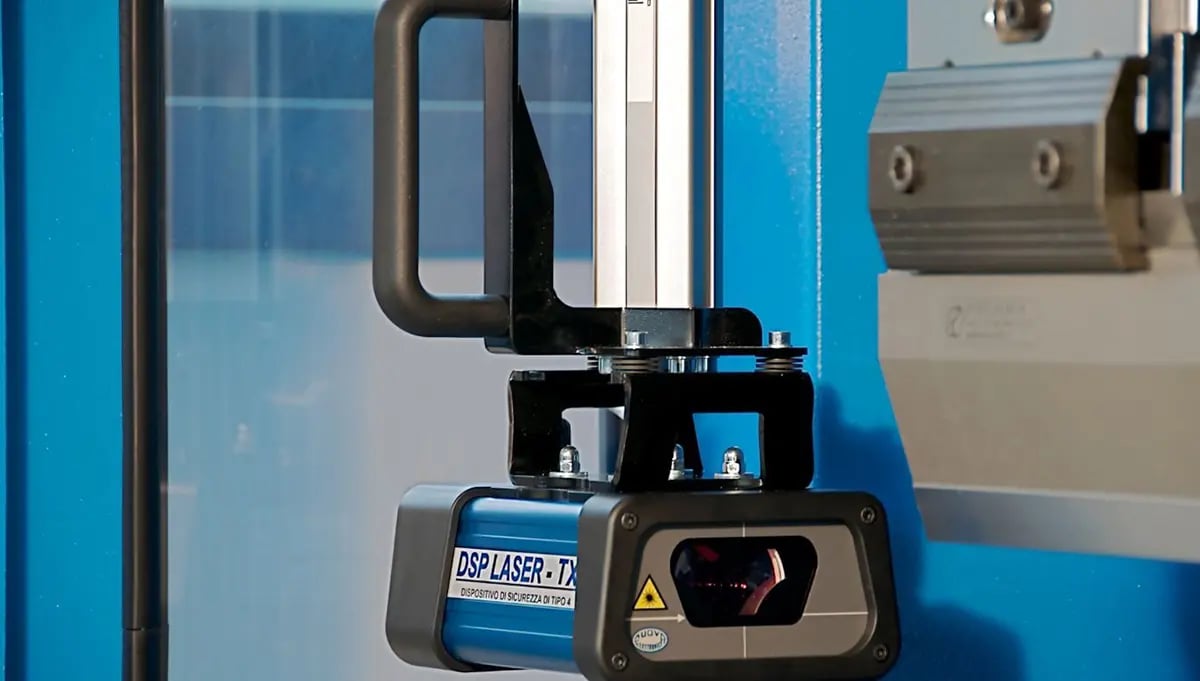
MSD Laser
The MSD laser protection devices used for press brakes prevents the operator of the press brake from dangerous detection due to the rapid movement of the upper beam of the machine, the MSD can be mounted on either the upper or lower beam table.A pair of transmitting and receiving ends form a laser beam in the area below the tooltip, thus creating a detection area by a single laser beam along the length of the bending machine.
Any opaque obstruction below the tooltip interrupts the laser beam and the MSD immediately signals and stops the upper beam via the CNC. This minimizes accidents in the production process and ensures that production is carried out in a safe and orderly manner.
Comparison: DSP has three protection options for more flexibility and MSD has One-point protection area, it will be easy to use.
Light Curtains
Light curtains are a type of presence sensing device used to protect the operator from making contact with any part of the press brake. Light curtains do not delay or limit productivity because no restraints, straps or physical barriers need to be used. Instead, light curtains use a stream of light or lasers to protect the operator. If the stream of light or lasers are broken the receiver immediately detects it and stops the machine instantly. Although the initial cost of a light curtain press brake safety devices system may be higher than using other physical barriers, the savings in manpower time and production speed more than makeup for the initial cost, while keeping your press break safety in the forefront of your mind.
Advantages:
They’re easy to install and use. You simply place a light curtain around the press brake machine and connect it to power. The only maintenance required is the occasional cleaning of dust or dirt from the sensors (which can be done with a simple wipe).
Light curtains are versatile enough for almost any type of application. Whether you’re working with large tools like press brakes or small hand tools like drills, light curtains will keep operators safe.
They offer high levels of accuracy without requiring extensive training on how best to use them.
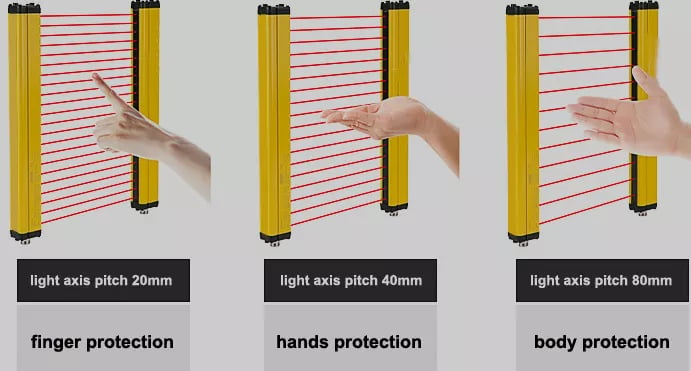
And because they require no physical contact between the operator and dangerous parts during operation (as opposed to traditional guards), there’s less chance someone will get hurt while performing their job duties.
Using and installing an automatic stroke stop system adds press brake safety to your business operations. A press brake automatic stroke stop can protect the operator and those in the surrounding area by creating two separate downward ram strokes using a ‘sequence mode.’ Each separate stroke is meant to operate at different speeds increasing press brake safety. Breaking the process down into two steps is a technique that prevents fingers, hands, or objects from getting pinched and decreasing the amount of ‘whip up.’ Using and installing an automatic stroke stop is an effective press brake safety method that is meant to prevent injury in the shop or factory.
Other Press Brake Safety Devices
A few additional press brake safety devices and methods for increasing press brake safety include, fly-off prevention dies, a two-person control device, and stepped stopper fingers. The fly-off prevention dies are intended to eliminate accidents in the workplace by using reinforcement materials that allow the die to endure greater pressure, therefore, reducing the risk of pieces breaking off. A two-person control device increase press brake safety by requiring two operators to work together decreasing the risk of operator error. And lastly, stepped stopper fingers are intended to increase press brake safety by supporting the front side of the work piece and allowing for the work piece to be steadied during operation.
Conclusion
By employing a combination of these laser protection devices and implementing comprehensive safety protocols, organizations can create safer work environments and minimize the risk of laser-related accidents and injuries.