Choosing the right sheet metal bending machine depends on several factors, including your specific bending requirements, the types of materials you'll be working with, your budget, available space, and production volume. Here are some key steps to consider when selecting a sheet metal bending machine:
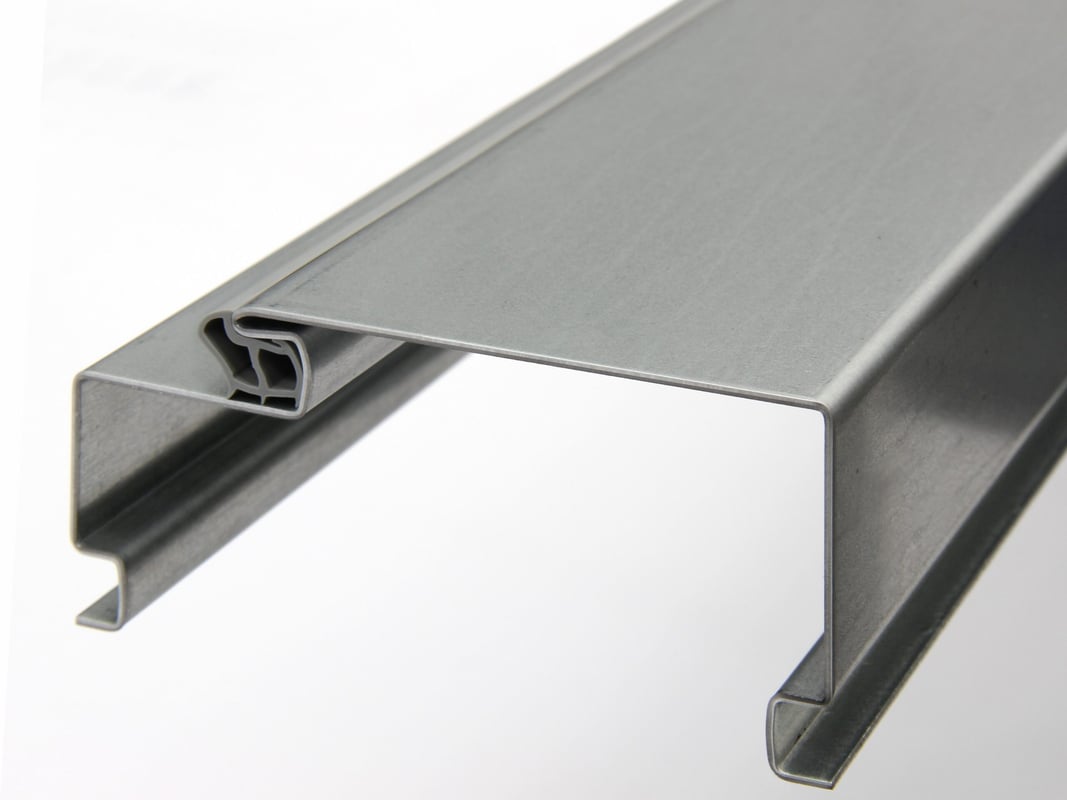
1.Understand Your Bending Needs: Determine the thickness, length, and types of materials you'll be bending. Consider the complexity and volume of bends required, as well as any special features or finishes needed.
2.Types of Bending Machines:
Press Brake: Press brakes are versatile machines suitable for a wide range of bending applications. They offer precise control over bending angles and are ideal for producing accurate bends in sheet metal.
Box and Pan Brake: These machines allow for the bending of sheet metal along multiple axes, enabling the creation of complex shapes and boxes.
Roll Bending Machine: Roll bending machines are used for cylindrical bending operations, such as rolling cylinders, cones, and spirals.
Folder: Folding machines, also known as folders, are designed for straight-line bending operations and are often used for repetitive bending tasks.
Capacity and Size: Consider the maximum bending capacity and the size of the machine relative to the size of the materials you'll be working with. Ensure that the machine's capacity can accommodate the thickness and width of your sheet metal.
3.Accuracy and Precision: Look for machines that offer precise control over bending angles and positioning. Features such as CNC (Computer Numerical Control) systems and back gauge systems can enhance accuracy and repeatability.
4.Flexibility and Versatility: Choose a machine that offers flexibility to handle a variety of bending tasks and materials. Adjustable back gauges, tooling options, and quick-change setups can increase versatility.
5.Ease of Use and Setup: Consider the ease of setup, operation, and maintenance of the machine. User-friendly controls, clear documentation, and accessibility to critical components can streamline workflow and reduce downtime.
6.Quality and Durability: Invest in a machine from a reputable manufacturer known for producing high-quality, durable equipment. Consider factors such as construction materials, build quality, and warranty coverage.
7.Cost and Budget: Determine your budget and evaluate machines based on their features, capabilities, and long-term value. Consider not only the initial purchase price but also ongoing operational costs and potential returns on investment.
8.Space and Installation Requirements: Ensure that you have adequate space for the machine and any necessary accessories or tooling. Consider factors such as power requirements, ventilation, and environmental considerations.
9.Safety Features: Prioritize machines with robust safety features to protect operators from hazards such as crushing, shearing, and flying debris. Safety guards, emergency stop buttons, and compliance with relevant safety standards are essential considerations.
By carefully considering these factors and conducting thorough research, you can choose a sheet metal bending machine that meets your specific needs and helps optimize your production processes. Additionally, consulting with industry experts or equipment suppliers can provide valuable insights and assistance in selecting the right machine for your application.