In the world of metalworking, the sheet metal press brake stands as a pivotal machine, essential for bending and shaping metal sheets into precise forms and components. From simple bends to complex shapes, the versatility and precision offered by press brakes have made them indispensable in industries ranging from automotive to aerospace. As technology advances, the capabilities of sheet metal press brakes continue to evolve, offering increased accuracy, efficiency, and automation. Understanding the intricacies of these machines, from their types and applications to their operational techniques, is crucial for anyone involved in the metal fabrication industry.
Table of Contents
Introduction to Sheet Metal Press Brake
A sheet metal press brake is a machine tool used in the metalworking industry for bending sheet and plate material, most commonly sheet metal. This equipment plays a crucial role in shaping metal into predetermined angles and forms, facilitating the creation of a wide variety of parts and components essential in numerous industries.
The importance of the sheet metal press brake in the metalworking industry cannot be overstated. It is indispensable for its ability to provide precision and consistency in bending operations, which are fundamental for manufacturing parts used in automotive, aerospace, construction, and electronics sectors, among others. The precision and versatility of press brakes allow manufacturers to produce complex shapes and designs with high accuracy, ensuring the quality and functionality of the final products.
The basic components of a sheet metal press brake include a ram, die, and punch. The ram is the part of the machine that moves up and down, driven by hydraulic or mechanical power. The die is the stationary bottom part where the metal sheet is placed, and the punch is the top part that presses down on the sheet to form it into the desired shape. Modern press brakes often incorporate computer numerical control (CNC) systems to enhance precision and repeatability, making them even more effective and efficient for industrial use.
Components of Sheet Metal Press Brakes
Bed
It is a fixed, flat surface used for the press brake to lie the workpiece. It supports and ensures the bending process is correct and aligned.
Ram
Ram is on the upper part of the press brake, which can be moved downward to exert bending force on the workpiece. It is connected to the punch and directly touches and helps form the metal.
Die
The die is a tooling and part with a specific shape used in the press brake and designed for shaping and forming the material. It is usually installed on the bottom beam.
Punch
The punch is also the tool and part with specific shapes used in the bending process for making materials to form. It is usually installed on the upper beam.
Back gauge
The back gauge is the mechanism and CNC controller installed on the rear of the press brake bending area. It is composed of the fingers and stops and is designed to position the bending material precisely, which can ensure a consistent and accurate bending operation.
Back gauge origin
The back gauge origin is the reference point measured on the back gauge system. It ensures the starting location of the back gauge during the bending operation.
CNC system
CNC is the abbreviation of the computer numerical control. It refers to a control system utilizing computer programs to control the machine movement automatically, which includes back gauge, ram, and other axes.
Upper beam
The upper beam is a movable beam or punch of the press brake, which can exert pressure on the material to perform bending. It fixes the punch and exerts the pressure via vertical movement.
Lower beam
The lower beam plays a vital role in press brake fixing, which can offer support for die or bottom tools. When the upper beam or punch moves vertically to exert bending operations, it will keep stable.
X-axis
The X-axis refers to a horizontal axis that can control the back gauge moving along the press brake length. The operator controls the back-and-forth movement of the back gauge, thus ensuring the flange length.
Y-axis
The y-axis is a vertical axis that can control the movement of the press brake punch or upper beam. The ram's vertical movement is called the Y axis. If the press brake is equipped with two independent cylinders, the CNC press brake can directly control each side of the cylinder. The left side of the ram is Y1, and the right side of the ram is Y2.
Z axis
The z-axis refers to the horizontal axis that moves or stops along the left and right locations. The Z-axis is used to measure the location and movement of the back gauge.
R axis
The R axis is used to control the back gauge finger's vertical movement or stop. It can bend complex shapes or achieve multiple bends. The back gauge vertical movement is the R axis, which can be controlled on some CNC press brakes. R1 and R2 refer to the up and down movement of the left and right back gauges.
Sheet support arms
These sheet support arms are extended parts installed on the front of the machine, which are used to support the workpiece during bending. Sometimes, they can measure the workpiece.
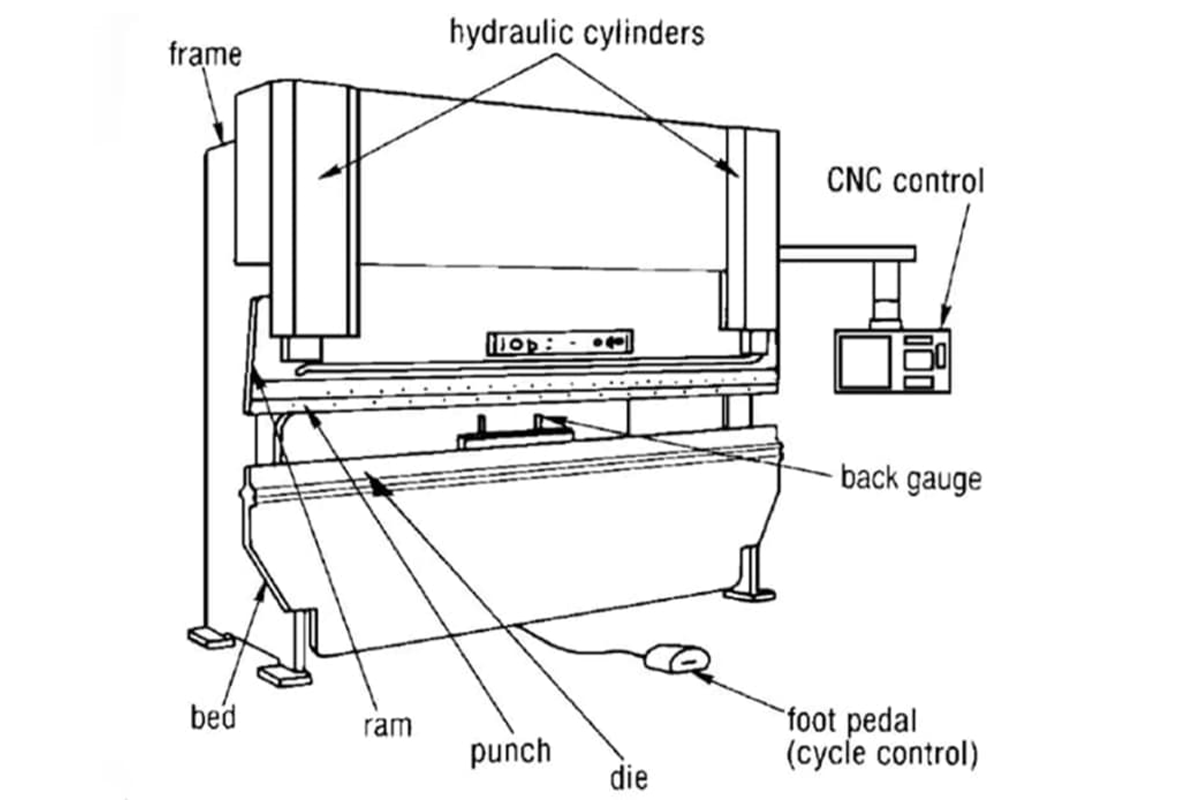
Understanding Basic Terminology of Press Brake Machine
Bend Allowance
Bend allowance refers to the deformation or elongation of material necessary to achieve a specific bending angle. It is calculated based on factors such as material thickness, bend radius, and material properties.
Bend Deduction
Bend deduction is the difference between the total flat layout dimensions and the actual length of the bent part. It represents the amount of material consumed during the bending process.
Bottom Dead Center
The bottom dead center is the lowest position the punch or upper beam reaches during its downward stroke in the bending process.
Braking Capacity
Braking capacity refers to the maximum force or tonnage that a press brake can exert when bending a specific material within its operational limits.
Clutch
A clutch is a mechanical component in a press brake that connects or disconnects the power transmission from the motor to the punch. It controls the movement and stopping of the ram during the bending operation.
Bottom Bending
Bottom bending is a technique where the upper beam applies pressure to form the material into the complete shape of the die. Unlike air bending, bottom bending keeps the punch and die in closer proximity, resulting in more surface contact with the metal. This method requires more tonnage but produces bends that closely match the shape of the punch and die.
Air Bending
Air bending is a technique where the material is bent using only three contact points. Unlike other methods, the material does not touch the bottom of the die, allowing for a more flexible and varied bending angle. The angle is controlled by the depth to which the punch descends into the die, rather than the exact shape of the workpiece.
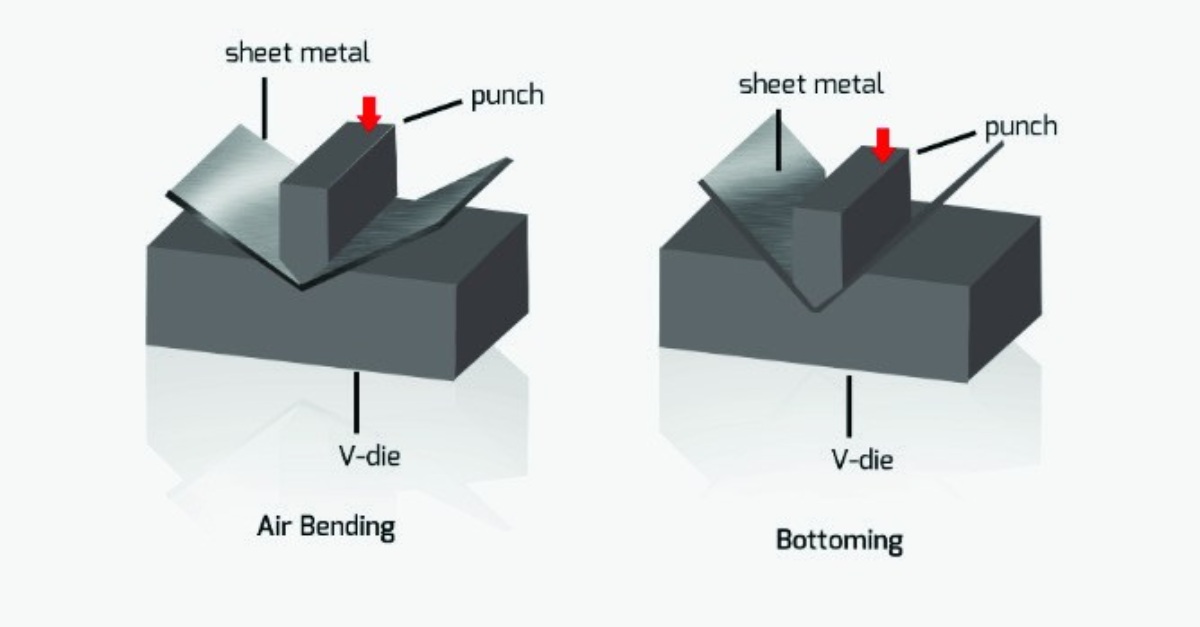
Coining
Coining is a high-precision bending method that presses the material fully into the die to achieve accurate angles and shapes. Originating from the process used to mint coins, this technique uses extremely high tonnage to ensure that the material conforms exactly to the angle of the die.
Springback
Springback is the tendency of material to return to its original shape after being bent. Once the bending force is removed, the material slightly straightens or deforms, which can affect the final angle of the bend.
Daylight
Daylight is the distance between the upper and lower beams of the press brake when it is fully open, with no material or tools inside. This measurement determines the maximum height of material and tooling that the press brake can accommodate, typically ranging from 12 to 24 inches.
History and Evolution
Origins of Press Brake Machines
The earliest iterations of press brake machines were rudimentary, hammer-like tools employed to manually bend metal into desired shapes. These early methods relied heavily on the weight of the tool and gravity to manipulate the metal, which was held in place during the process. This manual technique, however, was limited in both accuracy and speed and posed significant safety risks due to the manual labor involved.
Hydraulic Press Brakes
The early 1900s saw the development of hydraulic press brakes, which revolutionized the bending process. These machines used open- and closed-loop hydraulic systems to apply pressure, allowing for more precise manipulation of the material. Hydraulic press brakes offered significantly improved accuracy and could perform multiple operations quickly and safely, marking a significant advancement over earlier manual methods.
Computer Numeric Control (CNC)
In the 1970s, the advent of computer numeric control (CNC) technology brought about a new era for press brakes. CNC press brakes employed powerful motors to drive a system of arms and levers, precisely guiding the material into the desired shape. These machines provided unparalleled accuracy and could handle complex shapes, setting a new standard in the industry. CNC technology allowed operators to input designs that the machine could replicate with high precision, significantly enhancing productivity and consistency.
Servo Motors
As technology advanced, servo motor-driven press brakes gained popularity. These machines use powerful servo motors connected to a network of electro-mechanical systems to drive the press brake arms. Unlike traditional CNC machines, which require the user to input a design before each bend, servo-controlled press brakes allow for the programmatic input of desired shapes, resulting in more efficient production runs and greater flexibility in manufacturing processes.
Robotics
The integration of robotics into the manufacturing industry has also influenced press brake technology. Robotic press brakes can automatically move and manipulate the material, leading to faster operations and higher accuracy. The use of robotics enhances safety as well, since there is no need for workers to be near the machine during the bending process, reducing the risk of injury.
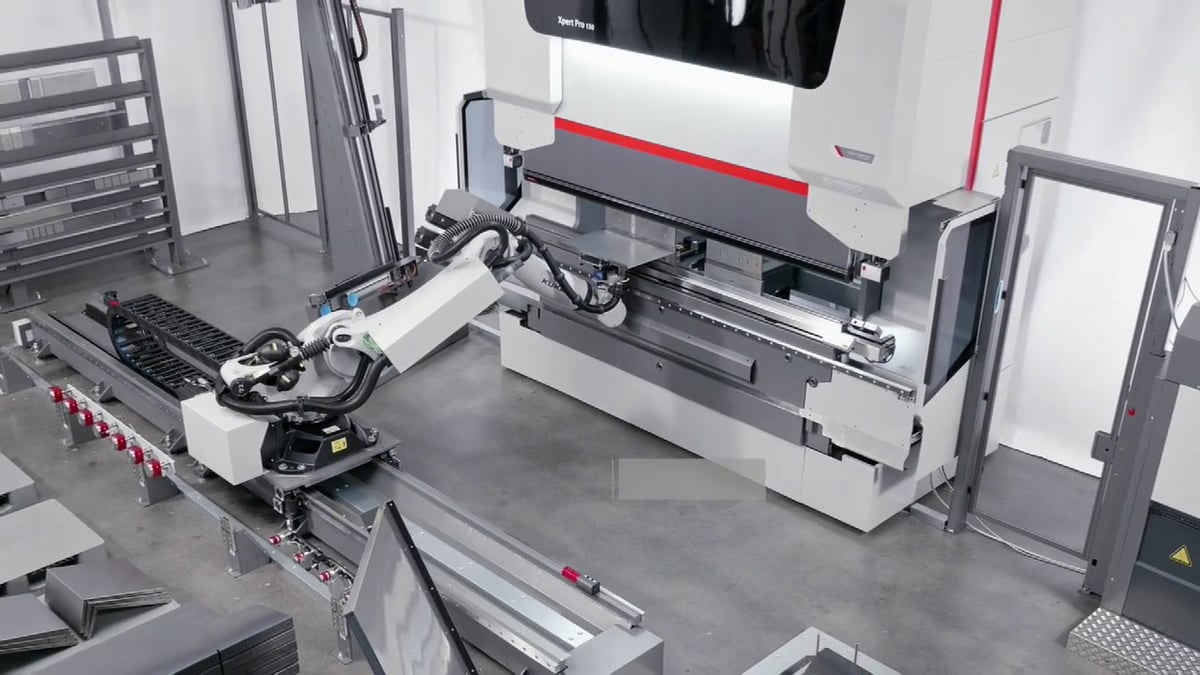
The Future of Press Brake Machines
Looking ahead, press brake machines are expected to continue evolving, particularly through further integration of robotics and advanced materials such as aluminum. Control systems based on Arduino and Raspberry Pi are anticipated to become more prevalent, offering new possibilities for customization and efficiency. Additionally, the focus will be on developing press brakes with higher capacity and durability. Automation will remain a key driver of innovation, with manufacturers striving to create machines capable of accurately and consistently producing complex shapes, thereby meeting the increasing demands of modern manufacturing.
Types of Sheet Metal Press Brakes
Mechanical Press Brakes
Mechanical press brakes are one of the earliest types of press brakes used in metalworking. They operate through a flywheel, which stores energy and releases it to drive the ram downward in a controlled manner. This type of press brake is known for its speed and efficiency, making it suitable for high-volume production runs. However, mechanical press brakes require more maintenance and are generally less precise than their hydraulic and CNC counterparts.
Hydraulic Press Brakes
Hydraulic press brakes use hydraulic cylinders to move the ram. They can be operated either by a single set of cylinders (known as a single-acting hydraulic press) or by two sets of cylinders (a double-acting hydraulic press). The hydraulic system allows for a controlled and powerful pressing force, making these machines highly accurate and versatile. They are capable of handling a wide range of materials and thicknesses, providing consistent pressure and precise control over the bending process. Hydraulic press brakes are also known for their safety features and ease of use.
CNC (Computer Numerical Control) Press Brakes
CNC press brakes represent the pinnacle of modern press brake technology. They incorporate computer numeric control to automate and enhance the bending process. Operators can program the desired shapes and angles into the CNC system, which then controls the movement of the ram and back gauge with high precision. CNC press brakes offer exceptional accuracy, repeatability, and the ability to handle complex bends and intricate shapes. They are highly efficient for both small batch and large-scale production, reducing setup times and minimizing human error.
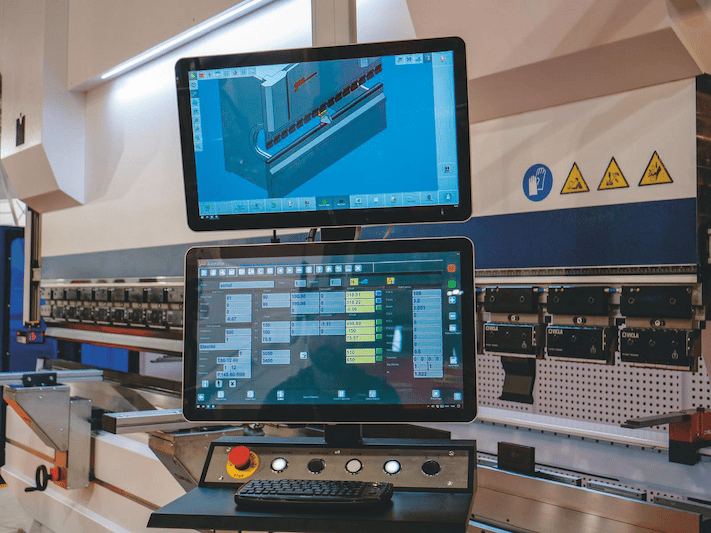
Comparison and Contrast of Different Types
Accuracy and Precision:
- Mechanical Press Brakes: Less precise due to reliance on mechanical components and manual adjustments.
- Hydraulic Press Brakes: Highly accurate with consistent pressure and control over the bending process.
- CNC Press Brakes: Extremely precise with computerized control, capable of complex and repeatable bends.
Speed and Efficiency:
- Mechanical Press Brakes: Very fast and suitable for high-volume production but require frequent maintenance.
- Hydraulic Press Brakes: Slower than mechanical presses but offer consistent and reliable performance.
- CNC Press Brakes: High efficiency with quick setup times and automation, suitable for both small and large production runs.
Versatility and Capability:
- Mechanical Press Brakes: Limited in versatility, best for simpler bends and thicker materials.
- Hydraulic Press Brakes: Very versatile, capable of handling a wide range of materials and thicknesses.
- CNC Press Brakes: Most versatile, capable of performing complex bends on various materials with ease.
Ease of Use and Maintenance:
- Mechanical Press Brakes: Require more manual adjustments and regular maintenance.
- Hydraulic Press Brakes: Easier to use with built-in safety features and lower maintenance compared to mechanical presses.
- CNC Press Brakes: User-friendly with computerized controls, minimal manual intervention, and lower maintenance due to automation.
Cost:
- Mechanical Press Brakes: Generally less expensive initially but may incur higher maintenance costs over time.
- Hydraulic Press Brakes: Moderately priced with a balance of performance and cost.
- CNC Press Brakes: Higher initial cost due to advanced technology but offer long-term savings through efficiency and reduced labor costs.
Applications of Sheet Metal Press Brakes
In the realm of metalworking and manufacturing, press brakes stand as indispensable tools with the power to transform raw materials into precision-crafted components. With their ability to bend and shape sheet metal and various materials, press brakes have found a multitude of applications across diverse industries. This article delves into the wide-ranging applications of press brakes, highlighting their significance and impact in shaping modern production processes.
Sheet Metal Bending
Sheet metal bending is perhaps the most well-known application of press brakes. These machines excel at producing crisp, accurate bends in sheet metal, enabling the creation of components used in everything from household appliances to industrial machinery. Press brakes make it possible to achieve a variety of bend angles and geometries, contributing to the structural integrity and aesthetic appeal of the final products.
Forming and Embossing
Beyond basic bending, press brakes enable intricate forming and embossing operations. They can shape sheet metal into complex three-dimensional forms, enhancing the visual and functional aspects of products. From automotive body panels to decorative architectural elements, press brakes play a vital role in producing components that demand both precision and artistry.
Coining and Coining Dies
In industries where precision is paramount, such as minting coins and producing fine jewelry, press brakes are employed in coining and stamping processes. Coined components require intricate detail and high accuracy, making press brakes an ideal choice for achieving these qualities. Specialized coining dies are used to imprint designs or text onto the material with exceptional precision.
Airplane Wing Bending
The aerospace industry relies heavily on components with precise dimensions and tolerances. Press brakes are employed to shape materials used in aircraft construction, such as aluminum and titanium alloys. These materials require careful bending to achieve the aerodynamic and structural specifications necessary for airplane wings, fuselages, and other critical components.
Automotive Component Manufacturing
Press brakes play a pivotal role in the production of automotive components, from simple brackets to complex structural elements. The ability to accurately bend and shape materials is essential for creating parts that ensure vehicle safety, performance, and aesthetics. The automotive industry’s demand for high-quality components in large quantities has driven the evolution of press brake technology to accommodate mass production.
Technical Specifications of Bending Machine
Key Specifications to Consider When Choosing a Press Brake
Tonnage
- Tonnage refers to the maximum force the press brake can exert during the bending process. It determines the thickness and type of material that can be bent. Higher tonnage machines are required for thicker and harder materials. Calculating the correct tonnage is crucial to avoid damaging the machine or producing inaccurate bends.
Bending Length
- Bending length is the maximum length of material that can be bent in one pass. It determines the size of the sheet metal that can be processed. Larger bending lengths are needed for bigger workpieces, such as large panels in the automotive or aerospace industries.
Accuracy and Precision
- The accuracy of a press brake is the degree to which the machine can achieve the desired bend angle and dimensions. Precision is critical for applications requiring tight tolerances, such as in the aerospace and electronics industries. CNC press brakes offer the highest accuracy due to their computerized control systems.
Stroke Length
- Stroke length is the distance the ram can travel during a bending cycle. It affects the depth of bends and the ability to form deeper shapes. Longer stroke lengths allow for more versatility in bending operations.
Daylight
- Daylight refers to the maximum open height between the upper and lower beams. It determines the maximum height of the workpiece and tooling that can be accommodated. More daylight allows for greater flexibility in tooling and the ability to work with larger parts.
Back Gauge
- The back gauge is used to position the workpiece accurately and ensure consistent bends. The range and precision of the back gauge are important for repeatability and accuracy in production.
Speed
- The speed of the press brake, including the approach, bending, and return speeds, affects production efficiency. Faster machines can complete more cycles per hour, increasing throughput.
Tooling Compatibility
- The type and compatibility of tooling with the press brake are essential. Different tools are needed for various bending operations, and the machine should be able to accommodate a range of tools to enhance versatility.
Control System
- Modern press brakes are equipped with CNC control systems that provide programmable control over the bending process. The complexity and user-friendliness of the control system can significantly impact the ease of use and efficiency.
Different Materials Can Be Processed By Press Brake
Mild Steel
- Mild steel is commonly used in many industries due to its ductility and ease of forming. Press brakes can efficiently bend mild steel into various shapes and angles.
Stainless Steel
- Stainless steel requires higher tonnage due to its hardness and strength. It is often used in applications where corrosion resistance and strength are critical, such as in food processing and medical equipment.
Aluminum
- Aluminum is lightweight and relatively soft, requiring less tonnage compared to steel. It is widely used in the aerospace, automotive, and construction industries due to its excellent strength-to-weight ratio.
Brass and Copper
- Brass and copper are softer metals that are easy to bend but require careful handling to avoid surface damage. These materials are often used in decorative applications, plumbing, and electrical components.
Titanium
- Titanium is a strong and lightweight metal used in high-performance applications, such as aerospace and medical devices. Bending titanium requires high tonnage and precise control to avoid cracking or damaging the material.
High-Strength Alloys
- High-strength alloys, including advanced high-strength steels (AHSS) and other specialized metals, require press brakes with higher tonnage and advanced features to handle their increased strength and hardness.
How To Operate A Press Brake
Understanding Press Brake Forming
To operate a press brake efficiently, it's essential to grasp the principles of press brake forming. This process involves using a punch and die set at a specific angle to bend or cut metal into various shapes and sizes.
At the core of brake forming is force, often measured in tonnage. Tonnage indicates the amount of pressure the punch can exert on the metal during a bend. The rule is simple: the thicker the material, the higher the tonnage required.
In addition to tonnage, bending length is another critical factor. Bending length refers to the longest part of the metal to be bent. For instance, if a machine can handle up to 14 feet of metal bending, any sheet longer than that would be too large for that machine.
Different fabrication jobs require machines with varying tonnages and bending lengths, depending on the size and thickness of the material being worked on. These specifications are crucial because they determine the load limit of the press brake, often given in tons per inch.
Using incorrect tonnage or bending length can lead to tool damage or even tool destruction.
Understanding these principles ensures:
- Proper selection of press brake based on tonnage and bending length requirements.
- Preventing damage to tools and materials.
- Maintaining efficiency in the fabrication process.
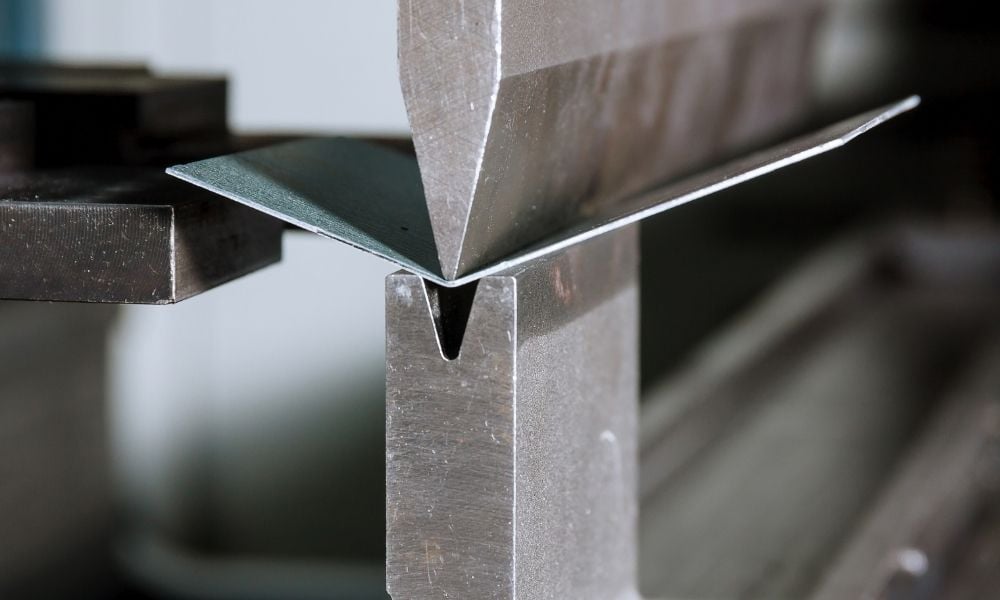
How To Run A Press Brake
Once you've understood the fundamentals of the press brake, here's how to skillfully operate the machine:
Power On:
- Start by turning on the power switch and the key switch located on the control panel.
- Then, activate the oil pump to ensure proper lubrication.
Stroke Adjustment:
- Before bending, test and adjust the stroke to match the thickness of the plate.
- The plate thickness should differ when the upper die bends it down to the bottom to avoid damage to the mold and machine.
- Stroke adjustment can be done quickly using electric controls or manually by hand.
Select Bending Notch:
- Choose a bending notch typically 8 times the thickness of the plate.
- For example, for a 4mm sheet, select a notch around 32.
Positioning:
- Place the metal sheet on the workbench.
- Use a backgauge or other positioning tools to ensure even and correct bending.
Backgauge Adjustment:
- Similar to stroke adjustment, backgauge can be quickly adjusted with electric controls or finely adjusted manually.
Initiate Bending:
- Once everything is set, press the foot switch to start the bend.
- Unlike a shearing machine, the press brake stops when you release the foot pedal.
Monitor the Bend:
- Keep a close watch on the metal sheet to ensure even and accurate bending.
- Avoid placing hands or any body parts near the work area during operation.
Shutdown:
- Close the press brake after completing the job.
- Turn off the power and clean up the work area.
- Ensure all tools and supplies are returned to their proper places.
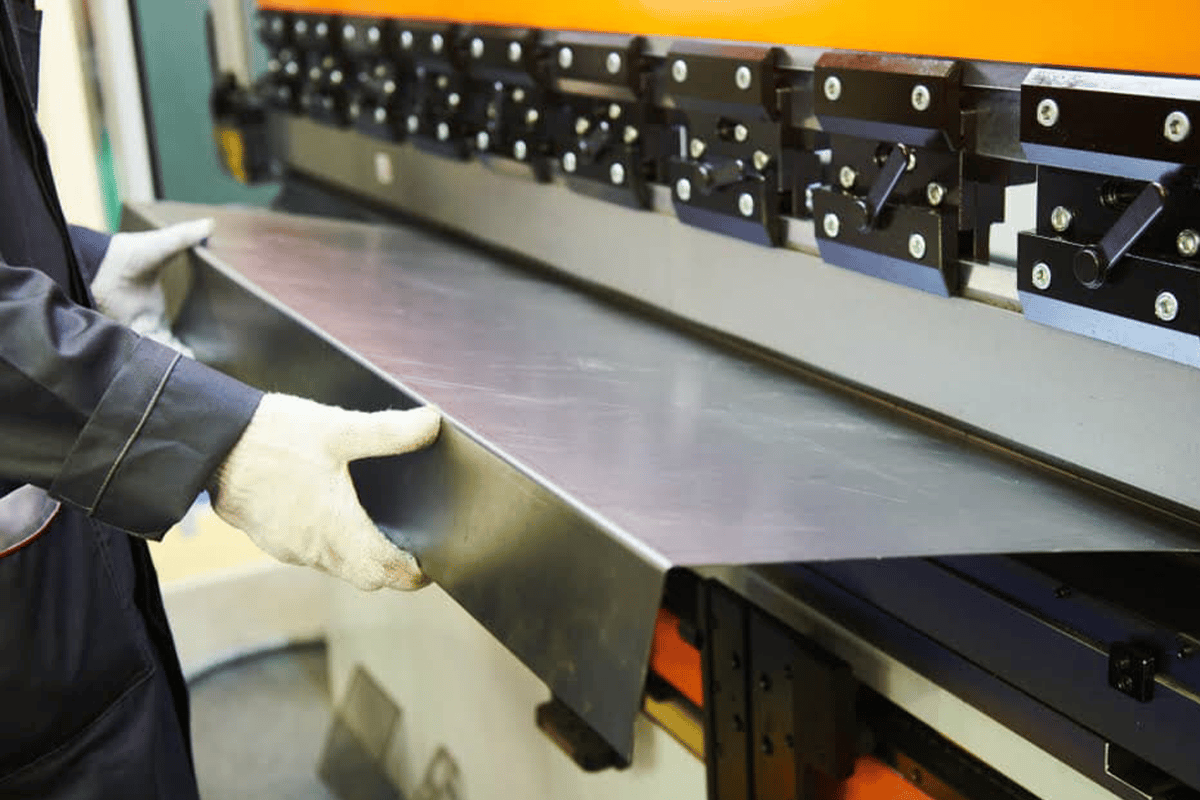
For installation of press brake, pls click here to read.
Safety Tips
Safety is paramount when operating a press brake to prevent accidents. Here are essential safety tips to follow:
Follow Safe Procedures and Wear Proper Gear:
- Always follow safe working procedures and wear appropriate safety gear such as protective goggles, gloves, and safety shoes when necessary.
Check Equipment Before Operation:
- Ensure the motor, switch, circuitry, and grounding are normal and secure before turning on the machine.
- Verify that all working buttons and parts are in their correct positions.
Inspect Molds and Positioning Devices:
- Ensure upper and lower molds are securely fitted and meet processing requirements.
- Verify that each positioning device meets the necessary standards.
Run Back-to-Origin Program:
- Initiate the back-to-origin program if the upper slide plate and positioning axes are not at their starting points.
Pre-Operation Check:
- Allow the machine to run by itself for one to two minutes after turning it on.
- The upper slide plate should move two to three times in a full stroke. Stop immediately if any strange sounds or faults occur and rectify the issue before resuming operation.
Assign Responsibility:
- Designate one person to oversee the work.
- Ensure the operator monitors feeding and pressing personnel closely to ensure safety before initiating bending.
Secure the Sheet:
- Ensure the sheet is properly pressed down before bending to prevent it from lifting and causing injury.
Stop Operation for Maintenance:
- Stop operation and turn off power when performing maintenance or when plate material is being pressed.
Safety Around Lower Die:
- Avoid touching the lower die when changing the alternative notch.
- Never stand behind the machine while it's in operation.
Avoid Overloading:
- Do not fold extremely thick iron plates, quenched steel plates, high-grade alloy steel, square steel, or plates larger than the machine's capacity to prevent damage.
Check Alignment and Pressure:
- Regularly check alignment between upper and lower dies.
- Ensure pressure gauge readings are correct.
Immediate Shutdown for Issues:
- Stop operation immediately if any issues arise, investigate the cause, and rectify it promptly.
Shutdown Procedure:
- Place a wooden block under both oil cylinders before turning off the machine.
- Lower the upper sliding plate onto the wooden block.
- Exit the control system program before turning off the power.
How To Choose Controller For Press Brakes
The right press brake controller depends on your industry and the complexity of your product. For simple products, opt for a straightforward controller to avoid unnecessary complexity and maintain cost-effectiveness. For more complex products, an advanced controller system is essential to ensure maximum efficiency in production.
Modern press brake controllers utilize the latest technologies to offer efficient and streamlined operation, enhanced functionality, and high productivity and performance levels. They also come with optional features that provide additional benefits, ensuring you get the best performance from your press brake.
Some Common Used Cotrollers Types
DA-52S
- Dutch Delem da-52s CNC system
- Fast navigation
- 6.4 “LCD true color TFT displayMaximum4-axis control (Y1, Y2 and two additional axes)
- Table deflection compensation control
- Mold/material/product library when the USB interface Advanced Y-axis control algorithm, can control the closed-loop, also can control the open loop valve
- Panel mounted structure, optional 6.4-inch LCDtrue-color TFT display Maximum 4-axis control(Y1, Y2, and two additional axes)
DA-53T
- “shortcut” touch navigation
- 10.1″high-resolution true-color TFT display
- Maximum 4 axis control (Y1, Y2+2 auxiliary axes) deflection compensation control with mold/material/product library
- Support servo or variable frequency control advanced Y-axis control algorithm can control both closed-loop valve and open-loop valve. Networkdouble machine linkage (optional)
- USB peripheral interface
- Profile-53tl offline programming software
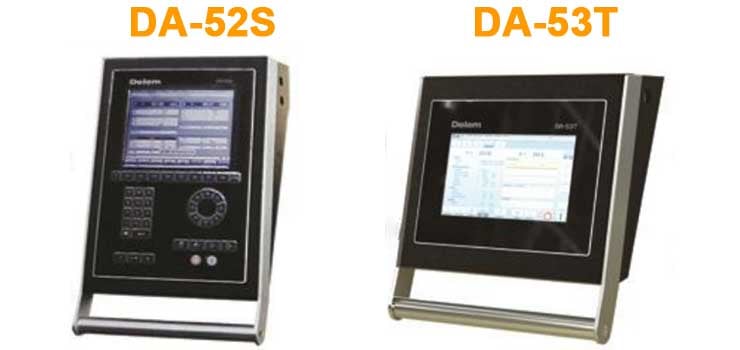
DA-58T
- 15″ high-resolution TFT true color display
- Bending process calculation, disturbance compensation control
- The advanced Y-axis control algorithm can control the closed-loop valve.
- Can also control the ring valve.
- USB port, USB flash drive.USB data
- Storage and recovery DA58T provides 2D touch graphic programming
- Includes automatic calculation of bending process and collision detection.
DA-66T
- Colour LCD display, 17”TFT, high brightness,1280x1024pixels,16 bit colour.
- Full touch screen control (IR-touch).
- Bend sequence calculation, Crowning control. Product and tools memory 256MB.3D graphics celera-on.
- Emergency switch. USB flash memory drive.
- The DA-66T offers 2D programming that includes automatic bend sequence calculation and collision detection. Full 3D machine set-up with multiple tool stations giving true feedback on the product feasibility and handling.
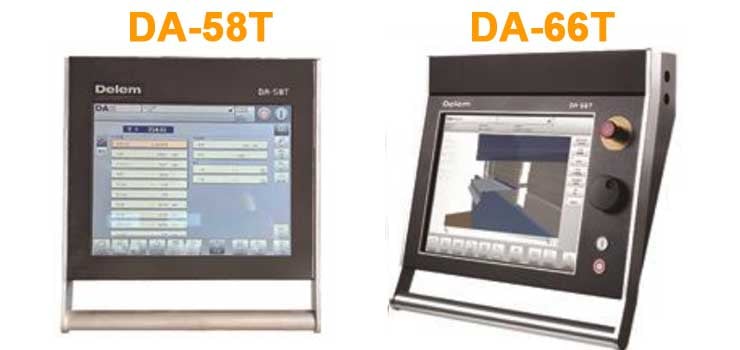
CybTouch ct8
- Large screen, high definition, and contrast touchscreen system.
- Convenient interface, clear display, and large icon keys.
- EasyBend pages are easy to bend.
- Perfect programming can improve the efficiency of batch multi-step bending. online help and pop-up prompt make the software interface very friendly.
- Support multiple languages.
- Use PC or laptop to upgrade and transmit data through wireless software.
CybTouch 12 PS
CybTouch 12 PS CNC systemCybTouch 12 PS system for our foldBending machine provides a simple and direct application: when operationAuthor A is doing bending work while the other operator B wants operator A to pause when before the bending work, help it to carry out a simple single bending process. In this case, operator A only needs to switch the page into an easy bending page, help after help B completes the bending, you can return to the original bending page face, continue the bending.
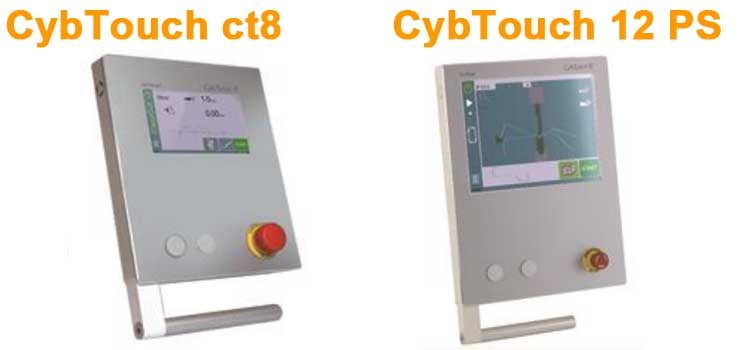
ESA630
- High-definition 10-inch TFT widescreen touch when the built-in PLC
- 2d graphics editing
- expand the length calculation
- graphic up and down mode, support multilateral mode, flexible mode
- round die, gooseneck die, and other molds
- graphic programming automation, manual optimization
- support for analog bending
- support double machine linkage function
- standard 4+1 axis, not extensible
- support graphics or numerical arc bending
ESA640
- 15 ’’touch screen panel (resolution wsvGA 1366×768).
- Standard 4 axis, Up to 6 axis control.
- FPGA integrated logics, surface mounting.fiber optic.
- Cpu Via Nano X2E 1,2 GHz with 2Gb of RAM.
- Silicon hard disk(flash disk) for more than 30.000part programs. Interactive 2d graphic editor for workpieces and tools data entry.
- 2D graphic display of machine frame, workpiece, and tools.
- 2 serial ports rs -232,2 USB port for memory stick, 1 ethernet port,2 can open port, Fiber optic interface, Local area network.
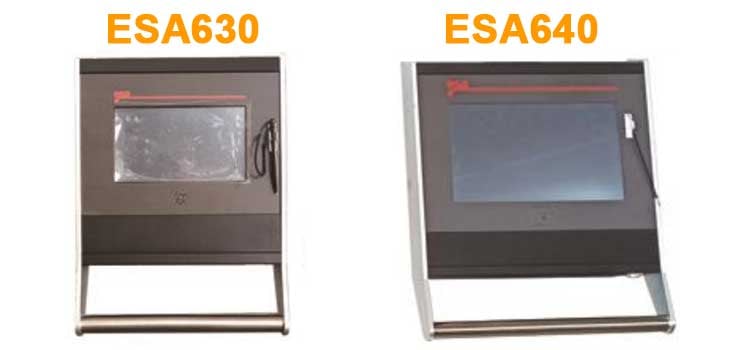
Basic Principles To Choose Right Controller
1. Assess Your Needs:
- Product Complexity:
- Simple Products: For straightforward bending tasks, choose a basic controller that is easy to manage and cost-effective.
- Complex Products: For intricate bending operations, opt for an advanced controller that offers extensive programmability and high precision.
2. Controller Types:
- Manual Controllers:
- Best for small-scale operations with less complexity.
- Require manual input for each operation.
- NC (Numerical Control) Controllers:
- Suitable for moderate complexity tasks.
- Provide basic programmability and control.
- CNC (Computer Numerical Control) Controllers:
- Ideal for complex bending operations and high-volume production.
- Offer full automation, multi-axis control, and advanced features like 3D visualization.
3. User Interface and Ease of Use:
- Intuitive Interface:
- Look for controllers with user-friendly interfaces, such as touchscreens.
- Ensure ease of navigation and quick adjustments.
- Training and Support:
- Consider the availability of training resources and customer support.
4. Programmability:
- Program Storage:
- Ability to store multiple bending programs for quick recall.
- Features like automatic bend sequencing and angle calculation.
- Offline Programming:
- Capability to program bends offline to minimize machine downtime.
5. Axis Control:
- Number of Axes:
- Basic controllers typically manage the Y-axis (ram movement) and X-axis (backgauge).
- Advanced controllers can handle multiple axes (Y1, Y2, X, R, Z1, Z2, etc.) for complex tasks.
6. Compatibility:
- Machine Integration:
- Ensure the controller is compatible with your specific press brake model.
- Check for integration with existing machinery and tooling.
7. Software Features:
- Advanced Capabilities:
- Features like 3D bending simulation, collision detection, and automatic tool selection.
- Regular software updates and support.
8. Precision and Accuracy:
- High Precision:
- Essential for tasks requiring tight tolerances.
- Check specifications for precision and repeatability.
9. Safety Features:
- Enhanced Safety:
- Look for controllers with built-in safety features to protect operators and machinery.
10. Budget Considerations:
- Cost-Effectiveness:
- Balance the features and capabilities with your budget.
- Advanced controllers may have higher upfront costs but can offer significant productivity gains.
11. Future Proofing:
- Scalability:
- Choose a controller that can accommodate future needs and advancements in technology.
- Ensure upgradeability and support for new features.
12. Popular Controller Brands:
- Delem: Known for user-friendly interfaces and advanced features.
- Cybelec: Offers high precision and extensive programmability.
- ESA: Provides robust solutions for various press brake configurations.
- Siemens: Known for integration with other industrial systems and high reliability.
How To Choose Best Sheet Metal Press Brake
Selecting the best sheet metal press brake involves a careful evaluation of your specific needs, including material type, bending length, production volume, and precision requirements. Consider the types of press brakes available, their controller systems, safety features, and maintenance requirements. Balancing your budget with the machine’s capabilities and long-term benefits will help you make an informed decision that enhances productivity and ensures high-quality results.
When it comes to reliable and high-performance press brakes, KRRASS Machinery stands out as a leading manufacturer. KRRASS offers a wide range of press brakes designed to meet various industrial needs, combining advanced technology with robust construction. Their machines are known for precision, efficiency, and user-friendly interfaces, making them an excellent choice for businesses aiming to improve their metal fabrication processes. Additionally, KRRASS provides exceptional customer support and maintenance services, ensuring your investment delivers maximum value over time.
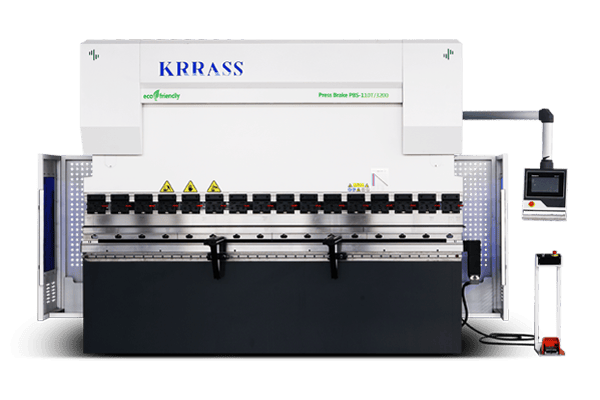