When purchasing a sheet metal press brake, customers often encounter various series of press brakes at different price points. The structure of the press brake is a key factor that distinguishes between different bending machine series. This article aims to provide a brief overview of the variances between manual and hydraulic press brake structures.
Manual Sheet Metal Press Brake
The manual plate bending machine cannot bend super thick materials and super hard materials to maintain the durability of the rigidity and macro precision of the whole machine. The manual bending brake machine adjusts the guide rail pressure plate bolts in time and maintains a good gap to obtain the ideal bending effect. The manual press brake machine should be lubricated with oil in time, and 30# mechanical oil must be used, and butter must not be injected to prevent the oil circuit from being blocked. Manual bending machines have been widely welcomed by users before 2000s, but now most customers use hydraulic press brake. The manual bending machine produced by experienced factory are made of high-quality die steel and can be well-made and tightly coordinated. The manual bending brake machine is easy to use, safe and reliable. Manual press brake toolings are blunt, and there are burrs in the cutting, and the new cutting edge should be turned over in time.
Scope Of Application Of Manual Bending Machine
Manual mechanical bending machine is used for bending of sheet metal, such as iron plate, aluminum plate, copper plate, stainless steel plate. Small pieces are more economical and cost-effective, and the manual bending machine can also be used for cutting plastic boards and cardboards.
Product Features Of Manual Bending Machine
Manual bending machine is efficient and energy-saving, light and durable. Manual mechanical bending brake machine is an ideal production equipment for limited budget workshop. The technology of this manual bending machine is mature, and the biggest advantage of manual press brake is movable adjustable upper die, adjustable die and adjustable press panel bending design.
Hydraulic Sheet Metal Press Brake Structure And Features
The hydraulic press brake machine includes a bracket, a worktable and a clamping plate. The worktable is placed on the bracket. The worktable is composed of a base and a pressure plate. The base is connected to the clamping plate by a hinge. The base is composed of a seat shell, a coil and a cover plate. The coil It is placed in the recess of the seat shell, and the top of the recess is covered with a cover plate. When in use, the coil is energized by the wire, and after the electricity is energized, the pressure plate is gravitationalized, so as to realize the clamping of the thin plate between the pressure plate and the base. Due to the use of electromagnetic force clamping, the pressing plate can be made into various workpiece requirements, and the workpiece with side walls can be processed.
Hydraulic Press Brake Machine Structure and Features:
- Adopt all-steel welded structure with sufficient strength and rigidity.
- Hydraulic upper transmission, the oil cylinders at both ends of the machine tool are placed on the slider to directly drive the sliding work.
- The slider synchronization mechanism adopts torsion shaft forced synchronization.
- The mechanical stopper structure is adopted, which is stable and reliable.
- The stroke of the slider can be adjusted quickly and manually, and the counter is displayed.
- Wedge-type deflection compensation mechanism to ensure high bending accuracy.
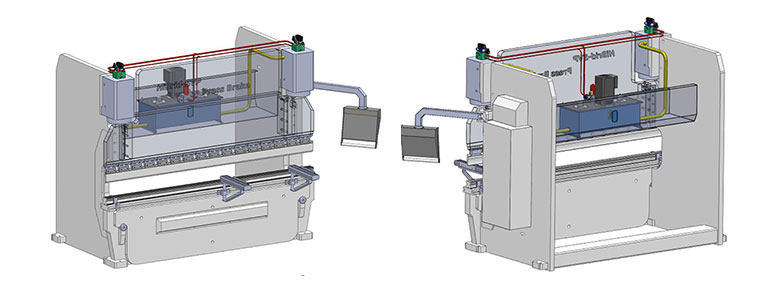
Conclusion
In conclusion, understanding the structure of sheet metal press brakes is essential for selecting the right machine for your fabrication needs. Whether it's a manual or hydraulic press brake, each type offers unique advantages and capabilities. By considering factors such as bending complexity, production volume, and budget, you can make an informed decision to optimize your sheet metal bending operations. With the right press brake structure in place, you can achieve precise bends, improve efficiency, and enhance the overall productivity of your sheet metal fabrication shop.