Sheet metal fabrication refers to a variety of processes used to assemble or manufacture parts from raw sheet metal. Depending on the material and project specifications, one or more sheet metal processes can be utilized to achieve the desired result. Clients have options such as metal cutting, welding, bending, machining, punching, and stamping to create their products. In this guide, we’ll explore each sheet metal process in detail, helping you identify the most suitable method(s) for your specific application.
Overview of Sheet Metal Fabrication
Sheet metal fabrication is essential for various manufacturing processes, ranging from the manufacturing of toys to large-scale airplane parts. Despite its popularity, it is important to know how this manufacturing process works. Here’s a detailed overview of sheet metal fabrication.
What is Sheet Metal Process?
Sheet metal process fabrication is the process of turning flat sheets of steel or aluminium into metal structures or products, by cutting, punching, folding and assembling. Sheet metal can be cut, bent or stretched into nearly any shape, which is generally done by cutting and burning the metal.
Special tools, such as band saws and chops saws, can also be used in the sheet metal fabrication process. These ensure even cutting throughout the process. Cutting torches are capable of cutting large sections of sheet metal with minimal effort.
Sheet metal fabrications use press brakes, which ease the process of sheet metal fabrication, by helping to create sharp bends and angles within the metal. There are a variety of different press brakes, which have different functions and are used for different purposes.
One of the other main factors in sheet metal fabrication is welding. Once all the components are formed, they are then assembled and tack welded into position. Many welding techniques can be used in sheet metal fabrication in order to prevent warping or any other abnormalities. These techniques include covering the metal with sand during the cooling process, special straightening process, welding in a staggered manner and using a stout fixture.
Straightening defected metal can be achieved by using with an oxy-acetylene torch. Heat is applied to the metal in a slow manner to remove any abnormalities.
The metal is usually finished by being sandblasted, primed and painted. This then ensures the metal looks fantastic and then is ready to be sent to the client.
If you have an upcoming project or want more details about we can do for you, don’t hesitate to get in touch.
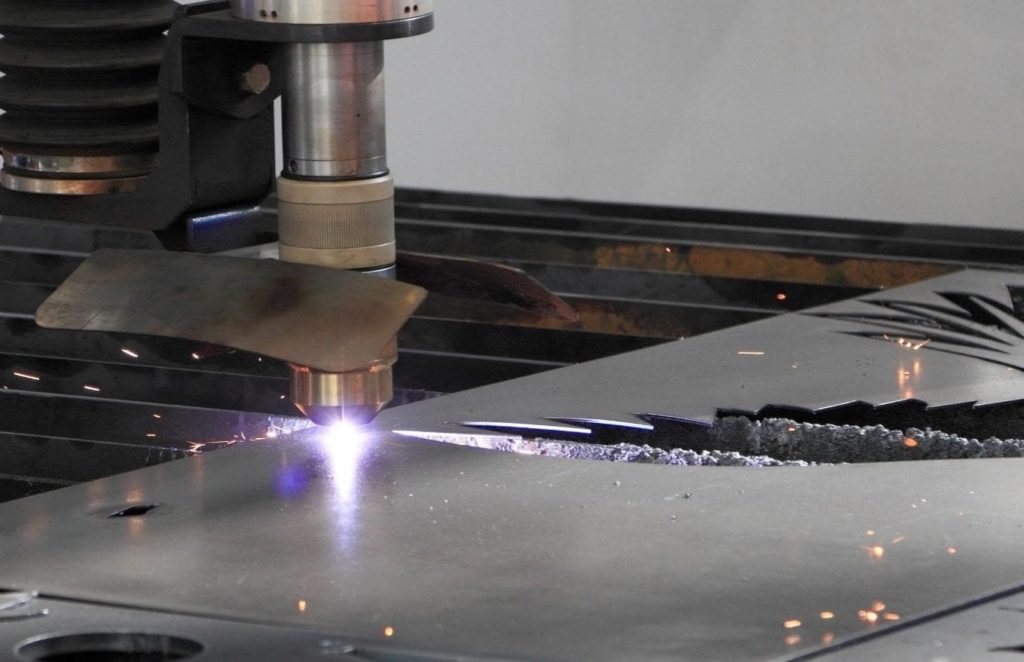
Sheet Metal Cutting Techniques
Cutting techniques are to separate sheet metal material by applying high force to cause the cutting edges to fail. They break into two groups, cutting without shear: laser cutting, plasma cutting, waterjet cutting, and cutting with shear: shearing, blanking, punching, and sawing. This section will discuss each technique in detail.
Laser Cutting
Laser cutting is a thermal cutting process that involves melting metals in localized areas using focused laser beams.
It involves two simultaneously running sub-processes. The first process involves focusing a high-powered laser beam on the sheet metal material. The laser beam is absorbed onto the material, causing it to vaporize. The second process occurs at the same time, where a cutting nozzle provides the process or blowing gas for laser cutting. This gas is typically nitrogen or oxygen, and it helps protect the processing head from vapors and splashes. It is also important for the removal of excess materials from the kerf.
Laser cutters can cut a wide range of metals, ranging from stainless steel to mild steel and non-ferrous metals. However, more reflective metals such as aluminum may be more challenging to cut. In such cases, fiber lasers are usually the better option. The thickness of the metal can range between 20mm to 40mm, with the maximum thickness depending on the laser’s power.
The laser cutting process is best suited to industrial applications. It is highly flexible, time-efficient, and can give a high degree of precision. However, the process has a high energy and gas consumption, translating to high investment costs and strict safety requirements.
Plasma Cutting
It is a thermal cutting process involving the cutting of metal with ionized gas (plasma). As the process takes place, there is a supply of substantial heat on the metal, and it melts away gradually. The final result is a rough cut with large burrs and an oxidized zone around the cut area.
It is important to note that the plasma cutting tool will only work effectively on electrically conductive metals. It is one of the best methods for cutting medium-thickness aluminum and stainless steel, copper, brass, and other conductive materials. You can use this cutting process for thicker pieces of sheet metal (up to 50mm) where there are no strict requirements for surface finish.
Plasma cutting ensures quicker cutting, high precision, and repeatability than many other cutting processes. It also guarantees automation, ensuring the effective cutting of high-strength metals with lower heat input. A downside to this process is that there is relatively high power consumption and possible noise development with dry cutting.
Waterjet Cutting
The waterjet cutting process involves using a high-pressure stream of water to cut metal sheets. The pressure is typically around 60,000 psi, supplying a velocity of about 610m/s to cut through almost any kind of metal sheet.
Waterjet cutting is versatile and can cut hard and soft materials with abrasives and pressurized water. To be specific, pure waterjet cutting is best for cutting soft metals like fabrics, rubber, or metal foils. Abrasive waterjet cutting is best suited for hard materials like carbon steel, stainless steel, aluminum, and copper.
Waterjet cutting is a great alternative to the laser cutting process. It gives extremely good surface finishes without burrs or heat distortions. However, high pressures could cause some bending near the cut area, so there is a need for proper support for the component.
Shearing
Shearing is a metal fabrication process that cuts straight lines on flat metal materials by applying a shearing force, causing the materials to separate at that point of cutting. It is ideal for high-volume applications and for cutting soft materials like aluminum, mild steel, and brass that don’t require clean finishes.
If there is a need to get straight edges on metal sheets with rough or uneven edges, shearing is one of the best options. It is cost-effective for high-output operations when you need to produce thousands of parts within a short time. However, the shearing action creates burrs and deformation on the material. As such, it may not be a great choice for applications requiring a clean end finish.
Blanking
Blanking removes a piece of sheet metal from a larger piece of the stock material with the use of blanking punch and die. The die holds the sheet metal during the process while the punch delivers a “blanking force” through the metal. The material removed is the desired component, while the material that remains on the die is the blank stock left.
Sheet metal blanking produces economic custom components and it ensures excellent accuracy, dimensional control, and repeatability. However, it is slightly slower and incurs higher tooling costs than the traditional punching operation.
Punching
Punching also creates holes in the sheet metal using shear force. However, in this case, the material removed from the hole is the scrap material, while the material left on the die is the final component. Punching helps to create cutouts and holes of various sizes and shapes.
This process is faster than blanking, producing clean and precise parts within a short time. There is also no risk of thermal changes to the workpiece because there is no heat involved. However, preparing for punching can be time-consuming since punching knives and dies need to be precisely matched.
Sawing
Sawing works by progressively cutting metal materials with a sawtooth tool to make a series of small cuts in the metal. Each saw tooth uses friction and shear force to separate a small material chip from the material body.
Metal band saws have several fines, and marginally bent teeth ideal for cutting aluminum, brass, copper, and other non-ferrous metals. Horizontal band saws are configured to cut longer bar stock to meet sizing requirements. On the other hand, vertical band saws help complete more complex cuttings requiring precise contours in the metal part.
Band saws have the ability to create accurate straight cuts. They also come with advanced features such as dual-bearing, blade-tracking adjustments, and blade-guided rollers. These features further ensure consistently precise cutting. Band saws generate smaller kerfs than many other cutting processes, substantially reducing waste. Therefore, it is a great option for lowering fabrication costs. However, it is difficult to maintain the required contact between the surface of flat workpieces and the cutting tool. This may cause material instability and cutting inconsistencies.
Sheet Metal Forming Techniques
Sheet metal forming involves reshaping metal materials while they are still in their solid states. This section will cover the most important forming processes for sheet metal. These processes are varied in their applications for making custom fabricated parts.
Bending
Bending is the process that deforms metal with force and bends the metal at the desired angle to form the required shape. It is carried out with press brakes and rolling machines. A press brake uses a punch and a die to bend sheet metal. There are different kinds of rolling machines, and they can roll sheet metal into various shapes within specific ranges.
There are various sheet metal bending methods, and the most common ones include:
- V-bending. Here, the bending punch supplies the force to bend metal materials (placed over the V-die) at desired angles. This method bends steel plates without changing their position.
- Roll bending. This method bends metal sheets into curved shapes or rolls. It uses a press brake, a hydraulic press, and three rollers to create the desired bend. It is preferred for components like tubes, cones, and other hollow-shaped materials.
- U-bending. This bending process is similar to v-bending. The only differences are that it uses a U-die and the final components are U-shaped.
- Rotary bending. This method bends metals into sharp corners. It is a great choice for bending angles greater than 90 degrees.
- Wipe bending. It uses a wipe die to determine the inner radius of the sheet metal’s bend.
Generally, bending is ideal for metals that are malleable but not brittle. They include mild and spring steel, aluminum 5052, and copper. Materials like aluminum 6061, brass, bronze, and titanium are more difficult to bend.
Bending is cost-effective when used for low to medium-volume productions, giving parts with excellent mechanical properties. However, there is a high possibility of springback affecting the resulting bend angle.
Hemming
Hemming involves rolling over a sheet metal edge onto itself to create an area with two layers. It often occurs in two stages. The first stage involves bending the sheet metal and bottoming it out into a V-die. The second stage involves the removal of the material and its placement into a flattening die. This process flattens the hem to give the desired shape.
Hemming is effective for reinforcing part edges and improving parts’ appearance. The accuracy of the process helps to get components with superior surface qualities. However, material deformation occurs during this process, leading to dimensional variations.
Rolling
Sheet metal rolling is the process in which a metal piece passes through a pair of rollers to reduce the material’s thickness or get a uniform thickness. The rollers are constantly spinning to create compressive forces that plastically deform the workpiece. If the rollers are directly perpendicular to the piece of sheet metal, flattening occurs.
There are two major rolling processes – hot rolling and cold rolling. Hot rolling occurs above the material’s recrystallization temperature, while cold rolling usually occurs at room temperature. The common applications of rolled sheet metal are found in pipes and tubes, stampings, discs, wheels and wheel rims, etc.
Rolling is a fast process with high efficiency, making it suitable for mass production. The process can be designed to create parts with tight tolerances and complex cross-section profiles. But metal rolling requires high initial investment, so it’s more suitable for mass production.
Stamping
Sheet metal stamping is a cold-forming technique that uses stamping presses and dies to transform raw materials into various shapes. This process is compatible with a wide range of sheet metal materials, including stainless steel, low- and high-carbon steel, aluminum, brass, copper, etc.
Stamping can generally be a combination of complex cutting and forming techniques to obtain complex components with shorter operations. It encompasses bending, punching, embossing, and flanging to create an extensive range of products.
Metal stamping is cost-effective. The process is fast, requires lesser tools and reduced labor time, and it’s relatively cheap to maintain the stamping dies, which contributes to an overall drop in expenses. Automating metal stamping is also easy. Therefore, proper programming of metal stamping machines will ensure consistent delivery of high-quality precision parts and repeatability. But the disadvantage of stamping is the increased cost of presses. If there is a need to alter the design during production, it may be difficult to change dies.
Curling
Sheet metal curling is the process of adding circular, hollow rolls to sheet metal edges. Most curling processes occur in three stages; the first two stages create the curves for the curl, while the third stage closes up the curl.
Curls help to remove sharp untreated edges from a workpiece to make it safer for handing. A curled edge also provides strength to the edge. Curling can also lead to burrs and material deformations, so care must be taken during the process.
Metal Spinning
Spinning involves forming metal discs into rotationally symmetrical hollows. During the process, the material is placed between the tailstock of the machine and a shaped spinning mandrel. Upon rotation, the spinning roller helps shape the sheet into the shape of the mandrel.
Metal spinning is ideal for mild metal plates, including stainless steel, copper, brass, aluminum, etc. Metal spinning can produce several hollow parts of various shapes without compromising their quality. Other sheet metal forming processes like bending and punching can be incorporated into a spinning cycle, making it highly flexible for both small batch and large volume production. Size and shape limitations are the major downside to this process. It produces only parts with concentric, symmetric shapes.
Sheet Metal Welding Techniques
Welding is a process that joins two pieces of metal sheets together using heat, pressure or both. It is a high heat process that melts the base metal, typically adding filler material.
There are various welding techniques available for sheet metal fabrication, which function to join metal together through a melting process and the addition of a filler. These welding techniques include the following:
- Stick Welding or Shielded Metal Arc Welding (SMAW). This welding process produces an electric current with an electrode stick to form an arc when it contacts the metal. The electric arc produces temperatures over 6300°F to melt metals. It is a process suitable for high-speed welding, and it can work on both AC and DC power sources. However, care must be taken when welding thin metals because the superior temperatures produced by this process may damage the material.
- Metal Inert Gas (MIG) Welding. This is also referred to as Gas Metal Arc Welding (GMAW), and it works with shielding gas and a continuous wire electrode. The melted wire electrode facilitates the easy joining of the metal parts while the shielding gas protects the weld pool from interacting with the atmosphere. MIG welding creates high-quality welds with excellent weld speed. It can also be fully automated to avoid weld splatter. However, this welding technique is not suitable for thick metals and outside welding.
- Tungsten Inert Gas (TIG) Welding. This welding is a process of creating a short arc for welding heavier metals. with a tungsten electrode. There is also an inert shielding gas to protect the weld area and electrode from atmospheric contamination. A big advantage of this welding process is that it works adequately for non-ferrous metals such as aluminum, copper, titanium, etc. There is a high degree of weld control with this process, helping it create very clean and strong welds. Therefore, it is a suitable method for automotive and aerospace constructions. However, TIG welding requires a highly skilled professional because it is more challenging.
Sheet Metal Fabrication Tolerance
Sheet metal fabrication tolerances refer to the acceptable deviations for features of sheet metal parts required for accurate and consistent installation and integration.
For sheet metal parts, ISO 2768-mk is usually used to ensure proper control of the elements of geometry and size. The following will show you 7 tolerance standards range of linear and angular dimensions, flatness & straightness, cylindricity, and circularity.
Table 1 – Linear Dimensions
Permissible deviations in mm for ranges in nominal lengths | f (fine) | Tolerance Class Designation (Description) | v (very coarse) | |
m (medium) | c (coarse) | |||
0.5 up to 3 | ±0.05 | ±0.1 | ±0.2 | – |
over 3 up to 6 | ±0.05 | ±0.1 | ±0.3 | ±0.5 |
over 6 up to 30 | ±0.1 | ±0.2 | ±0.5 | ±1.0 |
over 30 up to 120 | ±0.15 | ±0.3 | ±0.8 | ±1.5 |
over 120 up to 400 | ±0.2 | ±0.5 | ±1.2 | ±2.5 |
over 400 up to 1000 | ±0.3 | ±0.8 | ±2.0 | ±4.0 |
over 1000 up to 2000 | ±0.5 | ±1.2 | ±3.0 | ±6.0 |
over 2000 up to 4000 | – | ±2.0 | ±4.0 | ±8.0 |
Table 2 – External Radius and Chamfer Heights
Permissible deviations in mm for ranges in nominal lengths | f (fine) | Tolerance Class Designation (Description) | v (very coarse) | |
m (medium) | c (coarse) | |||
0.5 up to 3 | ±0.2 | ±0.2 | ±0.4 | ±0.4 |
over 3 up to 6 | ±0.5 | ±0.5 | ±1.0 | ±1.0 |
over 6 | ±1.0 | ±1.0 | ±2.0 | ±2.0 |
Table 3 – Angular Dimensions
Permissible deviations in mm for ranges in nominal lengths | f (fine) | Tolerance Class Designation (Description) | v (very coarse) | |
m (medium) | c (coarse) | |||
up to 10 | ±1º | ±1º | ±1º30′ | ±3º |
over 10 up to 50 | ±0º30′ | ±0º30′ | ±1º | ±2º |
over 50 up to 120 | ±0º20′ | ±0º20′ | ±0º30′ | ±1º |
over 120 up to 400 | ±0º10′ | ±0º10′ | ±0º15′ | ±0º30′ |
over 400 | ±0º5′ | ±0º5′ | ±0º10′ | ±0º20′ |
Table 4 – Straightness and Flatness
Ranges in nominal lengths in mm | Tolerance class | |||
H | K | L | ||
up to 10 | 0.02 | 0.05 | 0.1 | |
over 10 up to 30 | 0.05 | 0.1 | 0.2 | |
over 30 up to 100 | 0.1 | 0.2 | 0.4 | |
over 100 up to 300 | 0.2 | 0.4 | 0.8 | |
over 300 up to 1000 | 0.3 | 0.6 | 1.2 | |
over 1000 up to 3000 | 0.4 | 0.8 | 1.6 |
Table 5 – Perpendicularity
Ranges in nominal lengths in mm | Tolerance class | |||
H | K | L | ||
up to 100 | 0.2 | 0.4 | 0.6 | |
over 100 up to 300 | 0.3 | 0.6 | 1.0 | |
over 300 up to 1000 | 0.4 | 0.8 | 1.5 | |
over 1000 up to 3000 | 0.5 | 1.0 | 2.0 |
Table 6 – Symmetry (Position for ISO G&T Standard not-ASME or ANSI GD&T)
Ranges in nominal lengths in mm | Tolerance class | |||
H | K | L | ||
up to 100 | 0.5 | 0.6 | 0.6 | |
over 100 up to 300 | 0.5 | 0.6 | 1.0 | |
over 300 up to 1000 | 0.5 | 0.8 | 1.5 | |
over 1000 up to 3000 | 0.5 | 1.0 | 2.0 |
Applications of Sheet Metal Fabrication
Whether for structural purposes, decorative elements, or functional components within other products, many different industries rely on sheet metal fabrication.
Let’s take a closer look at its variety of common use cases.
Kiosks, vending machines & enclosures
Vending machines and kiosks bring in significant revenue for many customer-facing companies – for example, gyms and leisure centres. This is why care needs to be taken in their construction.
There are a large number of individual components needed to go into building these types of machines, which is why they require the application of sheet metal fabrication.
Construction & Security
The construction and security sectors use the application of sheet metal fabrication for products such as security doors, guard rails, security grills and bespoke security enclosures.
Retail
Creating appealing visual merchandise, as well as product displays, in the retail sector requires sheet metal fabrication.
Sheet metal fabrication can help create a wide range of retail display units for different retail clients, retail spaces and shop displays. For example, bar displays, retail display cubes, portable displays and point-of-sale stands. These products need to be eye-catching and highly functional.
Science, medical & food
Particularly the scientific, medical and food industries utilise sheet metal fabrication to create products found in commercial and industrial kitchens such as worktop surfaces, storage units, and sinks.
Stainless steel tends to be the material of choice for many applications in the food production and preparation industries.
Transportation
The transportation sector uses thousands of different products made using metal fabrication. For example, emergency vehicles rely on sheet metal fabrication for the construction of products such as glove-box enclosures, side steps, door-handle mounts, and steel surrounds for tail-lift doors.
Sheet metal fabrication is an excellent method for creating parts both large and small that can go into vehicle construction. On top of that, safety rails on building sites, ladder hatch trap doors, and stair-safe products are constructed through sheet metal fabrication.
Major Types of Sheet Metal
- Aluminium: Used for automotive parts, electrical devices, and cooking vessels. Offering numerous benefits including a good strength-to-weight ratio, and high conductivity.
- Aluminised steel: This metal combines the high strength of carbon steel with aluminium’s superior corrosion resistance. Sheets of aluminised steel are used for products intended for high-temperature environments, such as kitchen appliances.
- Carbon steel: Carbon steel is used in the industrial and consumer markets for a range of products. It is a steel alloy that contains carbon, resulting in the material increasing in hardness and strength when it undergoes heat treatment.
- Copper: Examples of products made from copper are sinks, roofs, rain gutters, and doors. Copper features higher electrical and thermal conductivity in comparison to aluminium but can be more expensive.
- Galvanised steel: Sheets of galvanised steel tend to be used for making automobile bodies, water pipes, fences, roofs, and staircases. It is made by coating steel with zinc through a hot dipping process, helping to make it more corrosion-resistant.
- High-strength steel: Military armour plates tend to be made from sheets of high-strength steel. The material is produced by alloying steel with a range of elements such as carbon, manganese, and copper. This helps to improve its hardness.
- Stainless steel: Used for kitchen vessels, storage tanks for chemicals and food processing machinery. Stainless steel offers superior corrosion resistance, fire and heat resistance, strength-to-weight ratio, and manufacturability.
- Titanium: Typical products made from titanium include aviation parts, medical equipment, and construction elements. It is primarily used for its high strength-to-weight ratio and corrosion resistance. It is also recyclable.
Conclusion
Sheet metal fabrication provides several key advantages, with the three main benefits being its strength, versatility, and ease of maintenance. Metal parts created through various sheet metal processes are highly durable and, with proper care, can last for many years, making them ideal for long-term projects. The versatility of sheet metal allows it to be used in a wide range of applications, from small to large-scale projects, making it a valuable resource for both businesses and individuals. Additionally, metal fabrications are easy to maintain, as they resist rust, corrosion, fire, and heat, making sheet metal processes particularly suitable for industrial and commercial environments.