What is Sheet Metal Roller
A Sheet Metal Roller is a kind of general equipment that can roll and bend metal sheets into a cylinder, arc, or another shape workpiece. According to the principle of three-point rounding, the continuous plastic deformation of sheet metal is produced by using the relative position change and rotation movement of the workpiece to obtain the workpiece with a predetermined shape.
The products are widely used in boiler, shipbuilding, petroleum, woodworking, metal structure, and other machinery manufacturing industries. As a special machine, plate bending machine plays an important role in basic industrial processing.
All steel forming for cylindrical, almost all with the rolling machine roll. It has applications in the automobile, the military industry, and so on.
According to different requirements, it can roll out steel columns that meet the requirements, which is a very practical instrument.
Working Principle
The upper roller of the symmetrical plate rolling machine is at the symmetrical position of the two lower rollers through the hydraulic oil in the hydraulic cylinder to act on the piston for vertical lifting movement, and the final gear of the main reducer drives the gears of the two lower rollers to mesh for rotating motion, which is the rolling motion Provide torque. The flat plastic metal plate of the plate rolling machine passes between the three working rolls of the plate rolling machine.
With the help of the pressing of the upper roller and the rotation of the lower roller, the metal plate is continuously bent through multiple passes, resulting in permanent plastic deformation. Roll into the required cylinder, cone, or part of them. The disadvantage of this hydraulic three-roller bending machine is that the end of the plate needs to be pre-bent with the help of other equipment.
This rolling machine is suitable for large rolling machines with a thickness of more than 50mm. A row of fixed idlers is added under the two lower rollers to shorten the span of the two lower rollers, thereby improving the precision of the rolled workpiece and the overall performance of the machine.
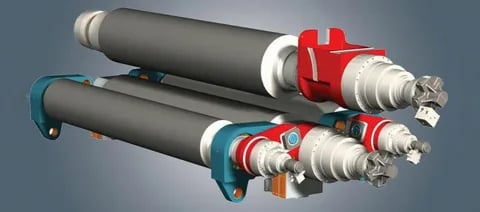
Classification
A sheet metal roller is a machine that will roll different kinds of sheet metal into a round or conical shape. It can be also called a “roll bending machine”, “plate bending machine” or “rolling machine”.
There are different kinds of technology to roll the metal plate:
Four-roller machines have a top roll, the pinching roll, and two side rolls.
The flat metal plate is placed in the machine on either side and "pre-bent" on the same side. The side rolls do the work of bending. The pinching roll holds the plate.
Three-roller machines (variable pitch aka variable geometry) have one pressing top roll and two pressing side rolls.
The three-roll variable pitch works by having all three rolls able to move and tilt. The top roll moves in the vertical plane and the side rolls move on the horizontal plane. When rolling, the top roll presses the metal plate between the two side rolls. The advantage of having the variable three roll is the ability to roll many thicknesses and diameters of cylinders.
For example; The side-rolls are what produce the mechanical advantage. With the side rolls all the way open, one has the maximum mechanical advantage. With the side rolls all the way in, you have the least mechanical advantage. So, a machine has the capability of rolling 2-inch-thick material with the maximum mechanical advantage, but a job is only 1/2 inch thick. Reduce the mechanical advantage and one has a machine that can roll from 1/2 to 2 inches thick.
Sheet Metal Rollers can be powered and controlled in multiple ways. Older plate mills are driven by electric motors and newer ones are directed by programs that are loaded into the CNC controller. When thinking about plate roll acquisition, industrial machinery companies like Provetco Technology will ask about the working length of the roller, the maximum thickness of the material, top roll diameter size as well as the minimum thickness of the material. Furthermore, the material yield is another critical component to disclose to machinery companies when looking for a plate roller.
Summary
Sheet Metal Roller plays a crucial role in the metal fabrication industry, enabling the production of complex and precise curved metal components for a wide range of applications across various industries.