The significance of small CNC press brakes extends beyond their technical capabilities. They represent a critical advancement in metalworking, offering unmatched accuracy and repeatability, which are crucial for maintaining quality standards in finished products. By automating the bending process and reducing human error, these machines enhance production efficiency and minimize material waste. Additionally, their space-saving design makes them ideal for small to medium-sized workshops, where maximizing every square foot is vital
This guide aims to provide an in-depth understanding of small CNC press brakes, exploring their key features, top brands, and factors to consider when making a purchase. Whether you are looking to upgrade your workshop's capabilities or invest in your first CNC press brake, this comprehensive guide will help you make an informed decisison.
What Is CNC Press Brake
A CNC (Computer Numerical Control) Press Brake is a sophisticated and automated machine designed for bending metal sheets. By using computer programming, it precisely controls various aspects of the bending process, including the bend's angle, depth, and length. The CNC system interprets these instructions to accurately position the bending tools. This high level of automation results in rapid and precise bending, minimizing human error and boosting productivity. CNC Press Brakes are versatile and flexible, capable of performing complex bending tasks and integrating seamlessly with other manufacturing processes.
What Tons That CNC Press Brake Have
CNC press brakes come in a wide range of tonnage capacities, depending on the manufacturer and the specific model. The tonnage of a CNC press brake refers to the maximum amount of force the machine can apply to the metal sheet being bent. Common tonnages for CNC press brakes range from:
- 30 to 100 tons: Suitable for light to moderate bending tasks and smaller sheet sizes.
- 100 to 300 tons: Ideal for medium to heavy-duty applications, handling larger sheets and more complex bends.
- 300 to 500 tons: Used for heavy-duty bending operations, capable of handling very large sheets and significant bending requirements.
- 500 tons and above: Designed for extremely heavy-duty tasks, accommodating large sheets and very thick materials.
When selecting a CNC press brake, it's important to choose one with sufficient tonnage to meet your specific bending needs, considering factors such as sheet size, material thickness, and complexity of the bends.
How to Define "Small CNC Press Brake"
A "small CNC press brake" is typically defined by its compact size and lower tonnage capacity compared to larger models.
A small CNC press brake is characterized by its compact size and lower tonnage capacity, typically ranging from 30 to 100 tons. This makes it well-suited for lighter and smaller-scale bending tasks. The working length of a small CNC press brake is generally between 1 to 3 meters (approximately 3 to 10 feet), allowing it to handle smaller sheet sizes efficiently. Its compact footprint makes it ideal for workshops with limited space.
Designed to handle thinner materials and smaller sheets, small CNC press brakes are often used for prototyping, small batch production, and in environments where space is at a premium. Additionally, they are more affordable than larger models, making them a cost-effective option for smaller shops or businesses with budget constraints.
Features of Small CNC Press Brake
Small press brakes are designed to be user-friendly and efficient, allowing for quick setup and completion of bending tasks. They typically have a smaller footprint, making them easier to fit into smaller workspaces. Despite their compact size, small press brakes still offer exceptional bending capabilities and are capable of achieving precise and consistent results.
These machines are equipped with various features that enhance their functionality and ease of use. They often come with adjustable backstops, allowing for precise positioning of the sheet metal. Some small press brakes also have digital displays and programmable controls, enabling operators to input specific bending angles and dimensions for increased accuracy. Additionally, many small press brakes are equipped with safety features, such as emergency stop buttons and guards, ensuring the well-being of the operators.
Overall, small press brakes are an essential tool for professionals in the metal fabrication industry. They offer precision, efficiency, and user-friendly features, making them a popular choice for bending tasks in smaller workshops. With their compact size and versatile capabilities, small press brakes contribute to maximizing productivity and delivering consistent results in the metal bending process.
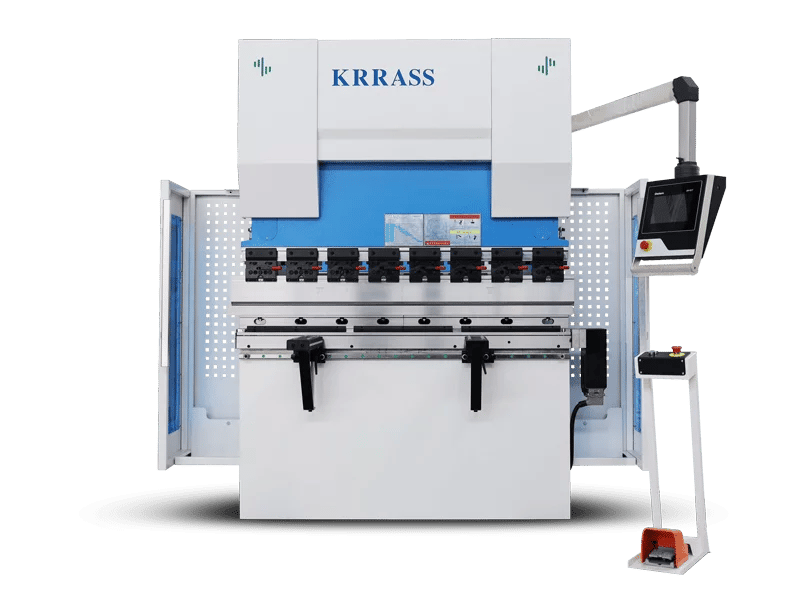
Benefits of Using Small CNC Press Brake
Space Efficiency:
The compact design of small CNC press brakes allows them to fit into tight workshop spaces, making them ideal for environments with limited floor area. This efficient use of space helps maximize productivity and enables versatile placement near other machinery or in dedicated workstations, facilitating a streamlined workflow. Their smaller size ensures that valuable workshop space is utilized effectively, enhancing overall operational efficiency.
Cost-Effective:
Small CNC press brakes are generally more affordable than larger models, presenting an attractive option for startups or small businesses with limited budgets. The lower initial investment is complemented by reduced operating costs, including lower energy consumption and maintenance needs. This combination of affordability and cost-efficiency makes these machines a practical choice for those looking to optimize their financial resources while still achieving high-performance bending capabilities.
Precision and Automation:
Small CNC press brakes leverage advanced CNC technology to deliver high precision and automation in the bending process. This ensures that bends are executed with exacting accuracy, including precise control over angle, depth, and length. By reducing human error and ensuring consistent results, these machines enhance product quality and reliability, making them indispensable for applications where precision is paramount.
Versatility:
Despite their smaller size, small CNC press brakes offer impressive versatility, accommodating a wide range of tasks from prototyping to small-batch production. They are capable of handling various materials and thicknesses, providing flexibility in manufacturing. This adaptability makes them suitable for diverse applications and allows businesses to tackle both routine and specialized bending operations with ease.
Quick Setup and Turnaround:
Small CNC press brakes are designed for quick setup and fast adjustments, which facilitate rapid turnaround times between jobs. This efficiency is particularly beneficial for handling small production runs or custom orders, allowing businesses to meet tight deadlines and improve overall productivity. The ability to swiftly adapt to different tasks and settings supports a more agile and responsive manufacturing process.
Lower Operational Costs:
The lower power consumption and reduced wear and tear associated with small CNC press brakes contribute to their lower operational costs. This includes savings on energy bills and less frequent maintenance, which together help to minimize long-term expenses. These cost savings enhance the overall value proposition of the machine, making it an economically viable option for cost-conscious businesses.
Flexibility in Production:
Small CNC press brakes provide significant flexibility for handling custom jobs and varying production needs. Their ability to adapt to different bending tasks and materials makes them a valuable asset in dynamic manufacturing environments. This adaptability supports a range of applications, from specialized tasks to custom projects, ensuring that businesses can efficiently address diverse production requirements.
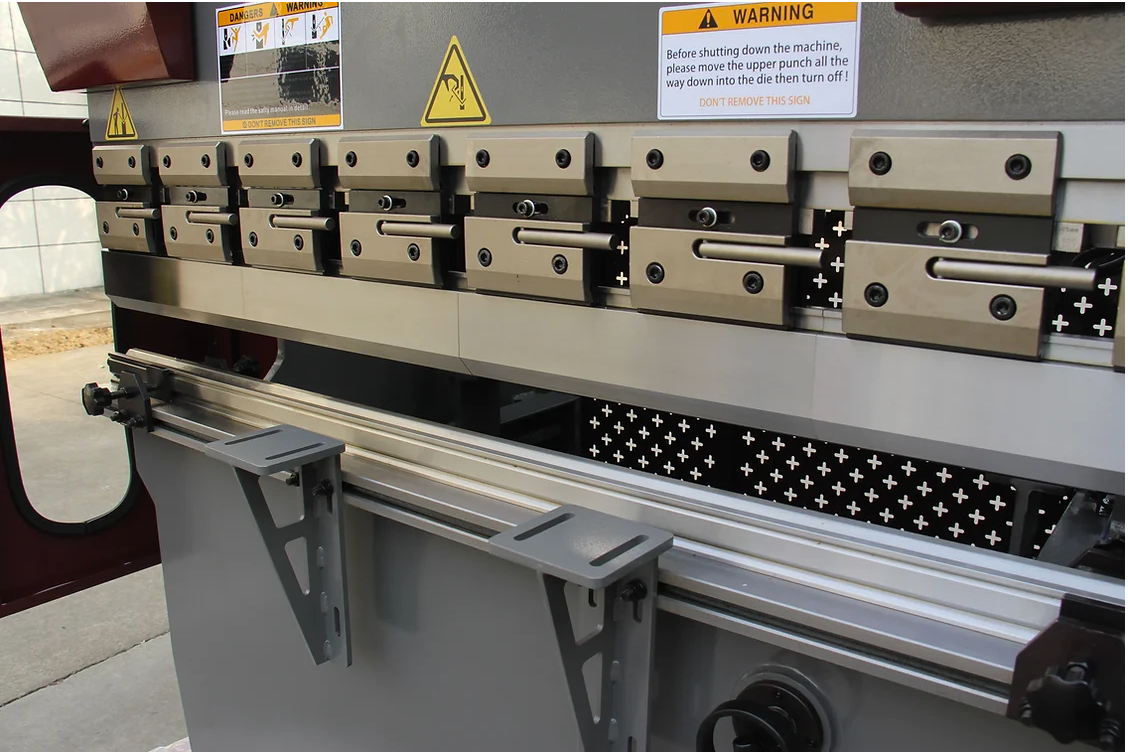
Where A Small CNC Press Brake Fit
A small CNC press brake is particularly well-suited for various environments due to its compact size and versatile capabilities. In small workshops, its limited footprint is ideal for maximizing space, while still providing high-performance bending. This makes it an excellent choice for environments with restricted floor area. Similarly, in prototyping facilities, the machine’s precision and ability to handle custom bending tasks support rapid adjustments and quick production, which is crucial for iterative design processes and prototype creation.
For small-batch production, a small CNC press brake offers cost-effective solutions by handling short production runs with high accuracy, making it more economical than larger machines. Educational institutions benefit from its compact design and hands-on capabilities, allowing students to gain experience with CNC technology in limited spaces. Custom fabrication shops and maintenance and repair shops also find value in its versatility, as it can accommodate various materials and tasks, from custom projects to small repairs.
Startups and small businesses appreciate its affordability and lower operational costs, providing an accessible entry point for CNC bending. Finally, for in-house manufacturing, it offers on-demand production and greater control over the manufacturing process, allowing companies to adapt quickly to production needs.
TOP 5 Small Press Brake Manufacturers
1. AMADA
Brand: Japan, Founded in 1946
AMADA press brake manufacturer is a large international company in sheet metal processing machinery. They provide sheet metal machinery, Amada press brake, cutting machines, grinding machines, stamping presses, and precision welding machines.
Amada is a Japanese company founded in 1946 with a long history. Amada’s products have a comprehensive and reasonable mechanical structure, providing users with the best quality guarantee.
2. Trumpf
Brand: German, Founded in 1923
Germany Trumpf is an innovative high-tech company, divided into three parts: Machine tools(Trumpf press brake, shear), laser technology, and electronics. It is one of the best manufacturers of sheet metal fabrication machinery, industrial lasers, and industrial application electronic products in the world.
TRUMPF is guiding the technological development trend with continuous innovation, establishing new technical standards, and is committed to developing and updating more products for the majority of users.
3. Accurpress
Brand: Canada, Established in 1973
Accupress is a professional manufacturer of CNC machine tools, established in Canada in 1973. It mainly manufactures Accurpress press brakes, shearing machines, tooling, and other peripheral products.
Accupress specializes in large-tonnage, tandem press brake, and robot automation. Accupress is known for its high manufacturing quality and advanced technology.
4. Bystronic
Brand: Italy, Established in 1964
Bystronic is a world-famous provider of sheet metal processing solutions, established in Switzerland in 1964.
The company focuses on the automation of the complete material and data flow of the cutting and bending process chain.
Bystronic mainly provides laser cutting machines, press brakes, automation systems, and related software.
5. Durma
Brand: Turkey, Established in 1956
Durmazlar Machinery was established by Ali Durmaz in 1956. Durma press brake manufacturer is a world-renowned metal sheet processing base.
Durma’s products include Durma CNC press brakes, turret presses, punching machines, all-solid-state fiber lasers, shears, ironworkers, plate rolls, angle rolls, and saws.
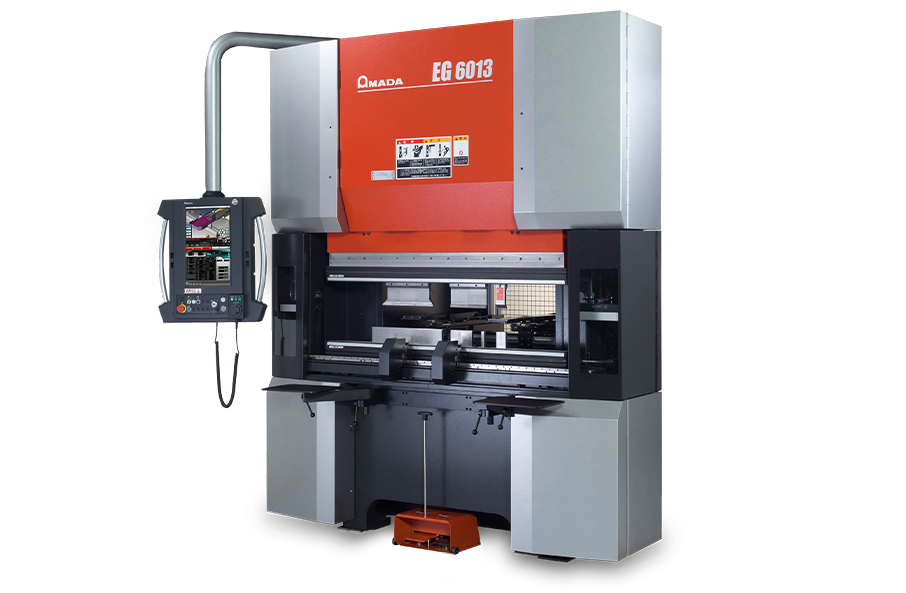
Factors to Consider When Choosing A Small Press Brake
When it comes to selecting a small press brake for your metal bending needs, there are a few key factors to consider. By carefully considering these factors, you can ensure that you choose the right machine for your workshop. Here are some important points to keep in mind:
- Size and Capacity: The first thing you need to determine is the size and capacity of the press brake that will best suit your needs. Consider the maximum length and thickness of the materials you will be working with, and choose a machine that can handle them efficiently. It’s important to strike a balance between the machine’s size and the size of the materials you typically work with.
- Features and Controls: Pay attention to the features and controls offered by the small press brake. Look for adjustable backstops, programmable controls, and other features that will enhance your precision and accuracy in bending tasks. These features can greatly improve your efficiency and productivity in the metal fabrication process.
- User-Friendliness: A small press brake should be easy to use, even for those with limited experience. Look for a machine that offers intuitive controls and clear instructions. A user-friendly press brake will save you time and frustration in the long run.
- Durability and Reliability: You want a small press brake that is built to last. Look for a machine made from high-quality materials that can withstand the demands of daily use. Additionally, consider the reputation and track record of the manufacturer to ensure that you are investing in a reliable product.
- Price and Value: Finally, consider the price and value of the small press brake. While you want to stay within your budget, it’s important to remember that quality and performance should not be compromised. Look for a machine that offers a good balance between price and value, and consider the long-term benefits it will bring to your workshop.
Larger CNC Press vs Small Press Brake, How to Choose
Every shop is unique, and understanding your specific needs is key to selecting the right equipment. A small CNC press brake can be an excellent choice if your operations involve tasks such as:
- Bending Small or Complex Parts: Ideal for handling intricate or smaller parts that require precise bends. This versatility also extends to accommodating some larger parts when needed.
- Reducing Waste and Eliminating Rejections: By ensuring accurate bending, a small CNC press brake minimizes material waste and reduces the likelihood of rejections, enhancing overall efficiency and cost-effectiveness.
- Producing a Variety of Materials and Parts: Capable of working with a wide range of materials and producing diverse parts, a small CNC press brake with a single set of punches and dies can streamline your operations and reduce the need for multiple tools.
- Saving on Bending Die Costs: With the ability to perform various bending tasks using fewer dies, you can lower the costs associated with purchasing and maintaining bending tools, making it a more economical choice.
- Creating Complex Shapes: Excellent for producing complex geometries such as S-shaped, U-shaped, and polygonal parts, providing flexibility for various design and manufacturing requirements.
- Maintaining Simple Setup and Tooling: Designed for easy setup and quick tooling changes, a small CNC press brake allows for efficient switching between different applications, supporting a wide range of bending tasks.
- Facilitating Easy Movement: When flexibility in machine placement is necessary, the compact size of a small CNC press brake allows it to be easily moved by forklift, accommodating changes in workshop layout or production needs.
Incorporating a small CNC press brake into your shop can enhance your ability to perform diverse bending tasks with precision, efficiency, and cost-effectiveness, making it a valuable addition to your manufacturing capabilities.
Maintenance of A Small CNC Press Brake
When it comes to using and maintaining a small press brake, there are a few key tips that can help ensure its longevity and optimal performance. Here are some important considerations to keep in mind:
- Read the Manual: Before operating the press brake, it’s crucial to thoroughly read the user manual. This will provide valuable information on safety precautions, operating procedures, and maintenance guidelines specific to your machine.
- Practice Safe Operation: Always prioritize safety when using a press brake. Wear appropriate protective gear, such as gloves and safety glasses, and ensure that the machine is properly grounded. Familiarize yourself with the emergency stop button and other safety features, and never exceed the machine’s maximum capacity.
- Regular Maintenance: A well-maintained press brake will not only extend its lifespan but also improve its performance. Regularly inspect and clean the machine, paying attention to the tooling, hydraulic system, and electrical components. Lubricate moving parts according to the manufacturer’s recommendations and promptly address any issues or abnormalities.
- Tooling Maintenance: The tooling on a press brake is subjected to significant wear and tear during use. Regularly check the condition of the tooling and replace any worn-out or damaged parts. Properly storing and organizing tooling is also essential to ensure their longevity and easy accessibility.
- Calibration and Alignment: Periodically check the calibration and alignment of the press brake to ensure accurate bending results. Use precision measuring tools to verify the parallelism of the ram and bed, as well as the angles of the bends. If any discrepancies are found, consult the user manual or contact a professional for assistance.
Remember, proper usage and maintenance of a small press brake are vital for optimal performance and longevity. By following these tips, you can ensure that your machine operates safely and efficiently, allowing you to achieve precise and consistent bending results.
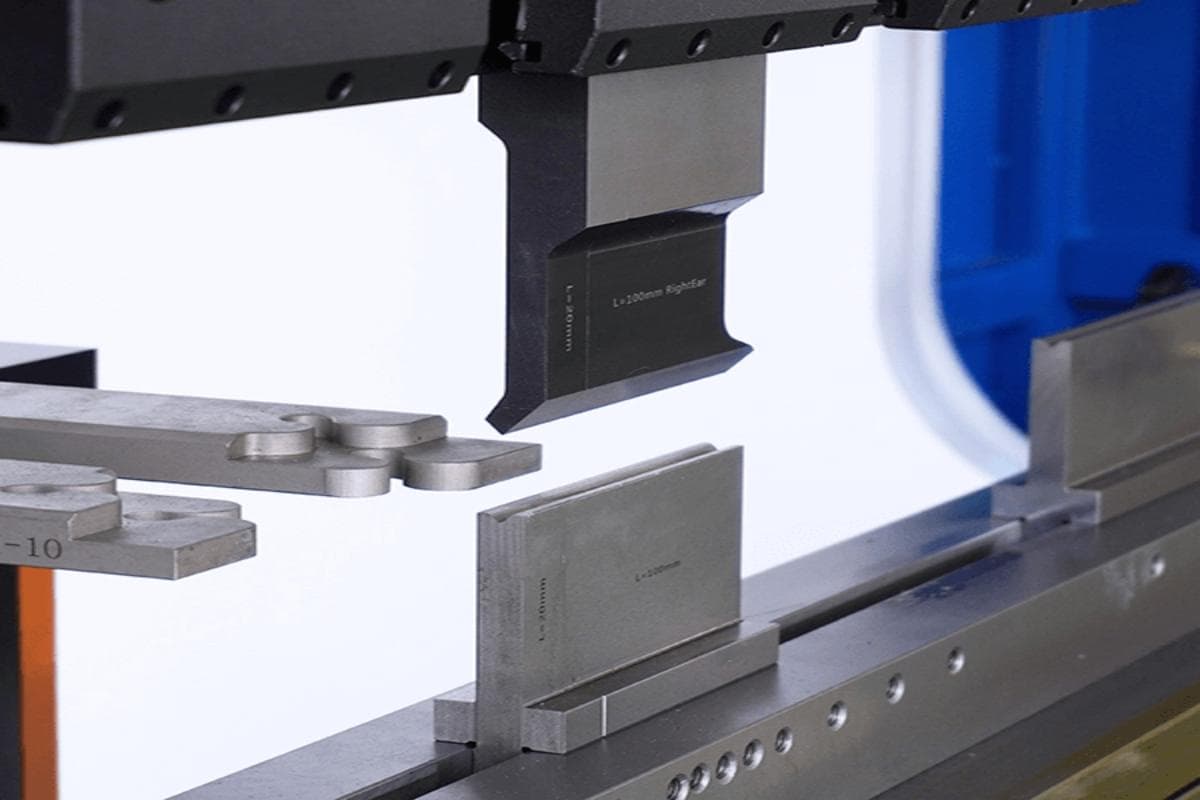
Summary
Choosing the right small CNC press brake is crucial for achieving efficient and accurate metal bending. By evaluating factors such as size, capacity, features, controls, user-friendliness, durability, reliability, and price, you can make an informed decision that aligns with your specific requirements. KRRASS offers a range of small CNC press brakes designed to provide exceptional performance and versatility, making them ideal for both small-scale workshops and larger manufacturing environments.