Table of Contents
A steel plate roller machine, also referred to as a roll bending machine, plate bending machine, or rolling machine, is a versatile tool used to shape sheet metal into round or conical forms. There are various technologies employed in rolling metal plates:
- Four-roller machines feature a top roll, a pinching roll, and two side rolls. The metal plate is positioned between the side rolls and pre-bent on the same side. The side rolls perform the bending action while the pinching roll holds the plate in place.
- Three-roller machines, also known as variable pitch or variable geometry machines, consist of one pressing top roll and two pressing side rolls. In this configuration, all three rolls are capable of movement and tilting. During the rolling process, the top roll presses the metal plate between the two side rolls. The variable three-roll setup offers the flexibility to roll various thicknesses and diameters of cylinders.
For instance, the adjustment of the side rolls determines the mechanical advantage. By opening the side rolls completely, maximum mechanical advantage is achieved, whereas closing them results in the least mechanical advantage. This versatility allows the machine to handle a range of material thicknesses.
Plate rollers can be powered and controlled through different methods. Traditional plate mills are driven by electric motors, while modern ones are controlled by programs loaded into CNC (Computer Numerical Control) controllers. When considering the acquisition of a plate roll, industrial machinery companies like Provetco Technology inquire about factors such as the working length of the roller, maximum material thickness, top roll diameter, and minimum material thickness. Additionally, disclosing the material yield is crucial for machinery companies to provide suitable recommendations for a plate roller.
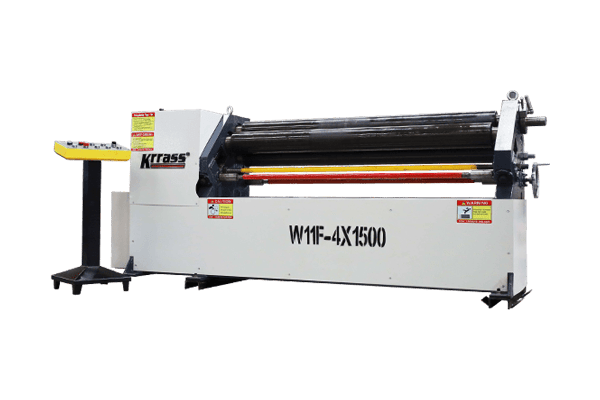
Advantages of Steel Plate Roller Machine For Metal Fabrication
There are several advantages to using plate rolling for metal forming. First, it is a cost-effective way to bend metal into complex shapes. Since the process is done with a machine, it is much faster and more efficient than manual forming. Additionally, plate rolling can be used to form thicker plates than other methods, such as press brakes. However, this will depend on the size and capabilities of the roller. This makes it ideal for heavier applications, such as shipbuilding and aerospace.
The amount of force can be adjusted to the specific needs of the application, which allows for the creation of parts with different levels of thickness and strength, alongside complex and intricate curved shapes. This can be especially useful for applications that require parts with complex designs, such as pressure vessels and tanks. Usually, materials such as steel, stainless steel and aluminium are used with the machine as they are malleable under force and not structurally brittle. However, the process can form and shape metals such as copper and titanium.
Given the mechanical nature of plate rolling operations, it is a reliable process that produces consistent results. The process is done in a controlled environment, which ensures that each part is consistent and meets the exact specifications. This can be beneficial for applications that require parts with a high degree of accuracy and is more reliable than traditional manual methods.
Safety Consideration When Use Plate Rolls
When operating plate rolling machines, safety practices are paramount. Operators must prioritize wearing proper safety gear, including gloves and eye protection. Regular inspection of the machine and its components is essential to verify optimal functionality. It's crucial for operators to understand the machine's limitations and refrain from attempting to roll plates exceeding its capacity. If your machine requires maintenance or inspection, KRRASS Machinery offers comprehensive services for a variety of sheet metal fabrication machines, including plate rolls.
Tips and Techniques for plate rolling
To get the best results when plate rolling, there are several tips and tricks to follow. First, the plate should be placed on the rollers in the correct orientation. This ensures that the plate is bent in the right direction. Additionally, the operator should use a lubricant to reduce friction and make the process easier. Finally, the rollers should be set at the correct speed and pressure to ensure that the plate is bent properly.
Plate rolling is a complex process, but it is an efficient and cost-effective way to create precision parts for industrial applications. The reliability and diverse functionality make it an essential asset to many sheet metal fabrication factories.
Choose Your Metal Roll Solution For Your Shop
Is your warehouse in need of a steel plate roller machine? Or does your current plate roll require maintenance or repair? Look no further than KRRASS Machinery for all your industrial sheet metal machinery needs, including plate rolls. Explore our range of CNC machines or hydraulic roll plates to find the perfect fit for your operations. Whether you require cutting, bending, notching, or more, KRRASS has a wide selection of new and second-hand machinery available for purchase today. Additionally, we offer maintenance and repair services to keep your industrial machinery running smoothly.