Shearing machines are essential tools in the metal fabrication industry, designed to cut metal sheets with precision and efficiency. There are several types of shearing machines available, each suited for different applications and material requirements. From hydraulic and mechanical systems to advanced CNC-controlled models, choosing the right type depends on factors like material thickness, production volume, and desired precision. In this guide, we will explore the various types of shearing machines, their features, and the specific industries they serve, helping you make an informed choice to enhance your production efficiency.
What Is Shearing Machine
A shearing machine is a machine used in metal fabrication industry for cutting metal plates into various desired shapes and sizes.
The components of a shearing machine are blades, pulleys, baffles, and an electric control system. The machine's die, used to cut various materials, can be found in different shapes, commonly two blades: straight blades and round blades.
Shearing operations are widely used in various industries, such as automotive and aerospace manufacturing, machinery production, household appliance production, and construction.
The effectiveness of a sheet metal shearing machine is determined by several factors such as its shearing capacity, accuracy, speed, and reliability.
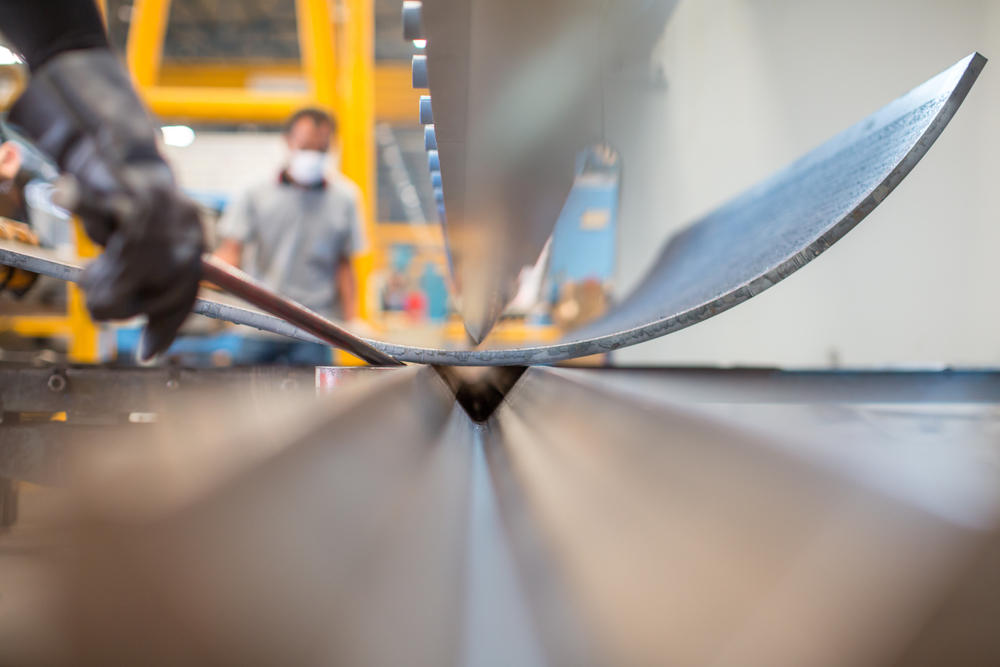
Guillotine Shearing Machine
The guillotine shearing machine is known for its high precision and ability to handle high-capacity jobs. It operates with a straight blade that moves vertically to cut through metal sheets, ensuring clean and accurate cuts. This design is ideal for large-scale operations requiring consistent and precise cutting over long periods. Guillotine shearing machines are commonly used in industries where high-speed production and tight tolerances are essential, such as automotive and aerospace manufacturing. Their robust design allows them to handle a wide range of materials and thicknesses, making them versatile for various metal fabrication needs.
Swing Beam Shearing Machine
The swing beam shearing machine operates with a blade that moves in an arc, which differs from the straight downward motion of the guillotine shear. This design reduces cutting force, making the machine more efficient and suitable for medium-duty applications. The swing beam shearing machine's cutting style also allows for easier maintenance and longer blade life, as the force is distributed more evenly. While it may not achieve the same level of precision as a guillotine shear, it offers a balance of efficiency and durability, making it ideal for industries that prioritize speed and reduced operating costs over extreme accuracy.
Key Technical Parameters of Shearing Machines
Parameter | Description |
Shearing Thickness | Maximum thickness of sheet metal that can be cut (typically 6-40mm) |
Shearing Length | Effective length of the worktable, determining maximum width of sheet (typically 1-6m) |
Shearing Angle | Angle between upper and lower blades (typically 1-3°; smaller for thin sheets, larger for thick) |
Blade Clearance | Distance between lower and upper blades (8-12% of sheet thickness; affects burr formation and shearing force) |
Shearing Speed | Speed of the shearing stroke (typically 8-20 strokes per minute; affects efficiency and vibration) |
Holding Force | Force applied by hydraulic hold-down cylinders to clamp the sheet (e.g., 13 tons for 2500mm length) |
Backgauge Stroke | Length of backgauge movement for precise positioning (e.g., 1000mm or more) |
Backgauge Accuracy | Precision of backgauge positioning (e.g., ±0.2mm or better) |
Blade Material | Typically high-carbon, high-chromium steel (e.g., HCHCr/D2) with hardness of 55 HRC or higher |
The term “rake” refers to the angular configuration of blades. Both rake and clearance are functions of the type and thickness of the material to be cut.
There are many manufacturers of shearing machines in China, and each manufacturer, according to the basic parameter standards set by the country, combined with their own factory’s product structure characteristics and market needs, has also developed their own factory’s series of parameter tables. Due to fierce competition, there are also quite a variety of product developments and specifications.
The development situation of the main technical parameters of shearing machines produced domestically and abroad is described as follows:
1. Shearable plate thickness
Around the 1960s, shearing machines capable of cutting plate thicknesses up to 60mm were produced abroad, and China also produced shearing machines with a cutting thickness of 50mm.
With the development of science and technology, the cutting process of plates has also been continuously improved. In recent years, shearing machines capable of cutting thicknesses up to 40mm have become rare. Considering the utilization rate and economy of the equipment, the maximum cutting thickness of shearing machines produced by most countries is 25mm or 32mm.
2. Shearable plate width
With the development of heavy trucks, trailers, large buses, and large aircraft, the demand for increasing shearing width continues to grow. Shearing machines with a cutting width of up to 9000mm, 10000mm have been produced abroad. Shearing machines with a cutting width of 6000mm have been relatively commonly produced.
3. Throat depth
With the continuous improvement of product quality, the requirements for the shearing quality and production efficiency of sheet metal are also increasing. The process of shearing long strips on shearing machines can no longer compete with other cutting technologies, so the method of using deep-throat shearing machines to shear long strips is rarely seen.
In addition, the throat depth significantly affects the weight of the machine, so currently, both domestic and foreign produced shearing machines tend to adopt a smaller throat depth, especially in large-scale shearing machines, it is more obvious. To accommodate users’ special requirements, in the series, except for a few specifications that have an enlarged throat, generally, a shallow throat is adopted, and a deep throat is handled through special orders.
4. Shearing angle
In order to reduce the bending and twisting of the sheared sheet, a smaller shearing angle is generally adopted, which may increase the shearing force somewhat, and also have some impact on the strength and stiffness of the stressed components, but it improves the shearing quality.
5. Number of strokes
The number of strokes is directly related to production efficiency. With the development of production, the emergence of various loading and unloading devices requires the machine to have a higher number of strokes. For mechanical transmission small shearing machines, it generally reaches more than 50 times per minute. Hydraulic transmission shearing machines also consider the hydraulic system and control aspects to enable them to automatically and quickly adjust the stroke length according to the width of the sheared plate, in order to increase the number of strokes.
Since the output of sheet metal occupies a large proportion in the steel production of each country, and many industrial sectors use sheet metal, therefore, in every industrially developed country, there are many factories that produce shearing machines according to their own series of parameter standards.
The main technical parameters of some CNC shearing machines are shown in Table 2.
Table 2 Main technical parameters of CNC shearing machines
Name | QS11K-4×2500 | QS-11K-6×2500 | QC12K-4×2500 | QC12K-6×2500 | QC12K-6×3200 | |
Cuttable thickness/mm | 4 | 6 | 4 | 6 | 6 | |
Cuttable width/mm | 2500 | 2500 | 2500 | 2500 | 3200 | |
Shearing angle | 1°18′ | 1°30′ | 1°30′ | 1°30′ | 1°30′ | |
Backgauge stroke/mm | 750 | 750 | 600 | 600 | 600 | |
Stroke frequency/(times/min) | 60 | 60 | 22 | 22 | 17 | |
Main motor power/kW | 5.5 | 7.5 | 5.5 | 7.5 | 7.5 | |
Transmission type | Mechanical underdrive clutch type | Hydraulic swing beam type | ||||
Number of CNC axes | 1 | |||||
Rear stopper adjustment maximum speed/(m/min) | 5 | |||||
Rear stopper adjustment positioning accuracy/mm | ± 0.10 | |||||
Machine dimensions/mm | Long | 3590 | 3670 | 3080 | 3130 | 3840 |
Width | 3200 | 1830 | 1440 | 1530 | 1675 | |
Height | 1560 | 1610 | 1550 | 1600 | 1620 | |
Machine weight/t | 5.5 | 6 | 4 | 5 | 6.6 |
Note: The strength of the sheared plate α b ≤450MPa.
Main Types of Shearing Machine
1. Manual Sheet Metal Shearing Machine
Manual sheet metal shears are equipment that can perform cutting of plates by manually moving the blade up and down. These shears are powered by hand, easy to operate and suitable for cutting small plates, but their cutting accuracy is low and cannot meet the requirements of large plates.
2. Mechanical Shearing Machines
The mechanical shearing machine operates using a power device consisting of a motor, flywheel, worm shaft, and clutch. It has faster cutting speeds and more strokes per minute compared to the hydraulic shearing machine.
The flywheel of the mechanical shearing machine stores energy, allowing a motor with lower horsepower to be used. Based on the operation mode, mechanical shearing machines can be further divided into up-moving and down-moving types.
3. Hydraulic Shearing Machines
The hydraulic shearing machine is powered by a hydraulic cylinder and motor. The motor drives the hydraulic cylinder, applying hydraulic oil pressure to the piston, providing power to the upper blade's piston.
The hydraulic shearing machine has a longer stroke and can handle different load capacities. Materials cut using a hydraulic shearing machine have a smooth surface with minimal markings. These machines are known for their large shearing force, stable operation, and good controllability.
The hydraulic shearing machine can be categorized into two types: the swing beam shearing machine and the guillotine shearing machine.
Comparison of Mechanical and Hydraulic Shearing Machines
Feature | Mechanical Shearing | Hydraulic Shearing |
Transmission | Mechanical (crank linkage, gear) | Hydraulic (hydraulic cylinders) |
Cutting Speed | Faster in full-cycle mode | Slower, but can operate continuously |
Capacity | Limited to thinner materials (up to 1/4" plate) | Can cut thicker materials (3/8" to 1" plate) |
Precision | Lower accuracy and adjustability | Higher accuracy and precise adjustments |
Noise | Loud during operation, but quieter overall | Constant noise from hydraulic system |
Maintenance | Simpler mechanisms, easier to maintain | More complex, but designed for easy operation and maintenance |
Safety | Can be stopped mid-cycle, but more hazards | Automatic reverse, light curtains, overload protection |
Cooling | Not required | Hydraulics run hot and require cooling |
Environmental Impact | No hydraulic waste (oil, filters) | Produces hydraulic waste |
Shock Resistance | More shock resistant due to robust construction | Less shock resistant due to hydraulic cylinders |
4. Pneumatic Shearing Machines
The pneumatic shearing machine refers to the equipment that uses a pneumatic system to control the up-and-down movement of the blade for plate cutting.
The pneumatic plate shearing machine offers high shearing speed and accuracy, as its blade movement can be adjusted through air pressure. It is commonly used for cutting special plates, such as those with high hardness and strength.
Thanks to its high cutting speed and accuracy, the pneumatic shearing machine is ideal for high-speed and high-precision cutting.
There are two main types of shearing machines for cutting plates: linear and circular. The linear shearing machine is powered by hydraulic devices and can handle thicker metal plates.
The circular plate shearing machine is powered by a motor and can cut circular metal plates. Each type of shearing machine has its own advantages and is suitable for different cutting needs.
Users can select the most suitable type of shearing machine based on their needs and the properties of the material.
For instance, manual shearing machines are ideal for cutting small plates, while large plates may require a guillotine shearing machine or a pneumatic shearing machine.
Types of Metal Shear Machines
There are several types of metal shear machines, each designed for specific applications. The most common types of metal shear machines include:
– Guillotine shears: These shears are used for straight-line cutting of metal sheets. They are available in various sizes and thicknesses, making them suitable for a wide range of applications.
– Rotary shears: Rotary shears use a rotating blade to cut metal sheets. They are ideal for cutting curved shapes and intricate designs.
– Slitting shears: These shears are used for cutting metal coils into narrow strips. They are designed for high-volume production applications.
– Nibbling shears: Nibbling shears are used for cutting complex shapes and contours in metal sheets. They use a small, rapidly moving punch to remove metal in small bites.
Key Considerations When Choosing a Shearing Machine
Material Type and Thickness
The type of material you work with—whether it's steel, aluminum, or other metals—plays a crucial role in selecting a shearing machine. Thicker or harder materials require more powerful machines, such as hydraulic shearing machines, while thinner materials can be handled by lighter models like mechanical or guillotine shears. It's important to match the machine’s cutting capacity with the material thickness to avoid damage or inefficient cuts.
Production Volume and Speed
If your operation involves high production volumes, speed becomes a critical factor. Hydraulic and CNC shearing machines are ideal for high-speed, continuous production. On the other hand, if your workload is smaller or more specialized, a mechanical shearing machine may be sufficient. Evaluating your production demands will ensure the machine meets your output requirements without compromising on efficiency.
Precision and Automation Requirements
For industries requiring high precision and intricate cuts, CNC shearing machines offer unparalleled accuracy and automation. Automated settings reduce human error and improve consistency, making CNC machines perfect for large-scale, precision-heavy applications. However, for simpler jobs where high precision isn’t a priority, manual or semi-automatic machines may offer a more cost-effective solution. Balancing precision needs with budget constraints is key when selecting the right shearing machine.
Conclusion
In conclusion, understanding the different types of shearing machines is crucial for making the right choice in your metal fabrication operations. Whether you need the high precision of a guillotine shearing machine, the efficiency of a swing beam design, or the automation of a CNC shear, each type offers unique advantages suited to specific tasks and materials. By considering factors such as material type, production volume, and precision requirements, you can select the best option to enhance your production capabilities. This ultimate guide to types of shearing machines ensures you are well-equipped to make an informed decision for your business needs.