In today’s fast-evolving world of metal fabrication, the handheld laser welding machine has become a game-changer. Known for its portability, precision, and ease of use, this versatile tool is increasingly replacing traditional welding methods. Whether you’re looking to streamline operations in automotive, aerospace, or general metalworking industries, a handheld laser welding machine offers a unique combination of speed and accuracy that significantly reduces production downtime. In this guide, we’ll walk you through everything you need to know to select the best handheld laser welding machine for your specific needs, ensuring that you make a smart and cost-effective investment.
Table of Contents
What Is Handheld Laser Welding Machine
The handheld laser welding machine is a new generation of laser welding equipment. It belongs to non-contact welding. It does not require pressure during the operation. , which melts the material inside, and then cools and crystallizes to form a weld.
The handheld fiber laser welding machine fills the gap of handheld welding in the laser equipment industry, subverts the working mode of the traditional laser welding machine, and replaces the previous fixed optical path with the handheld type. possible.
Hand-held welding is mainly aimed at laser welding of long-distance and large workpieces. It overcomes the limitation of the travel space of the worktable. The heat-affected area during welding is small, and it will not cause work deformation, blackening, and traces on the back. The welding depth is large, and the welding is Firm and fully melted, it can not only realize thermal conduction welding but also continuous deep penetration welding, spot welding, butt welding, stitch welding, sealing welding, seam welding, etc.
This process subverts the working mode of the traditional laser welding machine. It has the advantages of simple operation, beautiful welding seam, fast welding speed, and no consumables. It can be welded perfectly on thin stainless steel plates, iron plates, galvanized plates, and other metal materials It replaces traditional argon arc welding, stainless steel plate, iron plate, aluminum plate, and other metal materials welding.
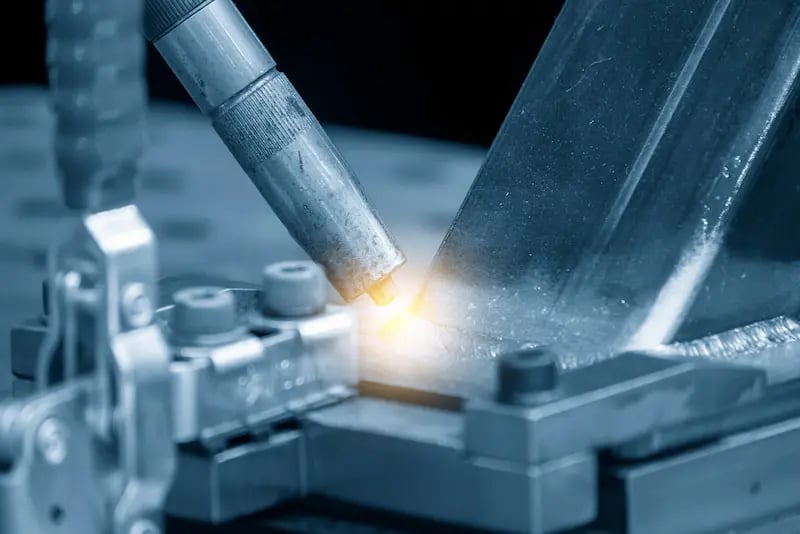
Principle of a Handheld Laser Welding Machine
1. High voltage drives the xenon lamp to emit light, the YGA crystals installed together are illuminated by the laser, resonantly resonate through the total reflection and semi-reflection diaphragm, and then input to the optical fiber through the beam splitter and optical gate, and finally focus the laser to a point
2. The power density on the focal plane can reach 10 5 -1013 w/cm2. The hand-held laser welding machine uses the characteristics of the excellent directionality and high power density of the laser beam to work.
3. The laser beam is concentrated in a small area, and in a very short period of time, a local heat source area with high energy concentration is formed at the welded part, so that the welded object is melted and a firm welding spot and seam are formed.
Laser welding can be realized by the continuous or pulsed laser beam. The principle of laser welding can be divided into heat conduction welding and laser deep penetration welding. When the power density is less than 104~105 W/cm2, it is thermal conduction welding. At this time, the penetration depth is shallow and the welding speed is slow; when the power density is greater than 105~107 W/cm2, the metal surface is concave into “holes” under the action of heat, forming deep penetration welding, with The welding speed is fast and the aspect ratio is large.
Application Field of Handheld Laser Welding Machine
Mainly for the fixed position of large and medium-sized sheet metal, cabinet, chassis, aluminum alloy door, and window frame, stainless steel washbasin, and other large workpieces such as inner right angle, outer right angle, plane weld welding, small heat affected area during welding, small deformation, and welding depth Large and solidly welded. Widely used in kitchen and bathroom industry, home appliance industry, advertising industry, mold industry, stainless steel product industry, stainless steel engineering industry, door and window industry, handicraft industry, household products industry, furniture industry, auto parts industry, etc.
Advantages of Handheld Laser Welding Machines
Extensive Welding Range: The handheld welding head comes equipped with a 5m-10m optical fiber, overcoming the spatial limitations of a fixed workbench. This allows for greater flexibility, making it ideal for outdoor or long-distance welding tasks.
Ease of Use and Flexibility: The handheld laser welder is fitted with moving pulleys, making it comfortable to operate and easy to adjust on the go. Unlike fixed-point stations, it offers flexibility, making it suitable for a wide variety of working environments and conditions.
Versatile Welding Techniques: Handheld laser welding can be used for a variety of welding methods and angles, such as stitch welding, butt welding, vertical welding, flat fillet welding, inner fillet welding, and outer fillet welding. It can handle complex welds and large, irregularly shaped workpieces. Additionally, it can seamlessly switch between welding and cutting, simply by changing the copper nozzle, making it a versatile tool.
Superior Welding Quality: Handheld laser welding utilizes hot-melt welding, offering a higher energy density compared to traditional methods. This results in deeper penetration, full melting, and stronger, more reliable welds. In fact, the strength of the weld often matches or exceeds that of the base material itself, a result that ordinary welding machines can't easily achieve.
No Need for Post-Weld Grinding: Traditional welding often requires grinding to smooth the weld points. In contrast, handheld laser welding delivers continuous, smooth welds without fish scales, scars, or imperfections. The reduced need for post-weld grinding simplifies the process and improves efficiency.
Consumable-Free Welding: Unlike traditional welding, which typically involves welding wire and other consumables, handheld laser welding requires no additional materials. This reduces production costs while maintaining high-quality results.
Multiple Safety Features: The handheld laser welding machine is equipped with several safety alarms. The welding tip only activates when the metal surface is touched, and the laser locks automatically once the workpiece is removed. Additionally, the touch switch includes a body temperature sensor, ensuring the safety of the operator during use.
Labor Cost Savings: Compared to arc welding, handheld laser welding can reduce processing costs by around 30%. The machine is easy to operate and requires minimal training, allowing even less-experienced workers to achieve high-quality results quickly and efficiently.
How Does a Handheld Laser Welder Work?
Handheld laser welding machines uses generated laser beam to melt and join two materials. The laser source can be fiber or solid-state, and it determines the welding speed and rate.
These machines are versatile and compatible with different material types and of different complexity in terms of design. They can melt and join thin and thick materials with accuracy making them suitable for welding small parts that require minimal distortion because the heat source is focused on a particular area.
Handheld Laser Welding Vs Traditional Welding
Cost and Ease of Use
Handheld laser welding machines come with a relatively high investment. Additionally, the servicing and maintenance fees are also considerably more compared to the traditional methods.
Regarding ease of use, traditional methods require technical expertise, which can increase operating costs. Furthermore, handheld laser welders have easier to use. Some models even feature automation which increases operational use.
Speed and Production Efficiency
With a faster heating and cooling rate, handheld laser welders are better than traditional methods. As a result, they are more efficient and productive in terms of small-scale welding. However, in large-scale welding, traditional methods are more suitable due to the higher long life compared to laser welders.
Heat Affected Zone (HAZ)
The area around the weld joint that experiences an appreciable temperature increase also differentiates the different welding processes. The HAZ is smaller because laser welding is a contactless process that uses a focused laser beam.
On the other hand, the heat from most traditional welding techniques affects the surrounding material extensively. This can change the microstructure of the metals through recrystallization, phase transformations and precipitation. Furthermore, the area of the heat-affected zone differs among conventional welding methods. The HAZ mig welding produces comparatively larger because it has a high heat input.
Precision and Control
The control level in laser welders depends on the level of automation. Nevertheless, the operator has total control. This is better than traditional welding techniques, which have lesser precision, no automation, and require high control and focus.
Furthermore, the accuracy and precision of the final weld made with traditional methods may be lower. However, using a highly skilled operator can overcome this shortcoming. By overseeing the process, the consistency of the final weld may be similar to laser welds.
Material Compatibility
Laser welding has wide material compatibility, although it is more suitable for thin parts. The smaller heat-affected zone they produce makes them the method of choice for delicate and heat-sensitive materials.
On the other hand, the material compatibility of traditional techniques depends on the method used. Most are strictly for joining metals and may be less effective for non-metallic materials. However, traditional welding techniques are better for very thick parts because of their high heat input.
Applications
Though one uses different welding methods for manufacturing and repair operations, their application in industries differs. Handheld laser welders are more suitable for small-scale welding and materials with thin, delicate, or complex designs.
However, traditional methods, especially MiG welding, are more suitable for chassis and frames. Furthermore, arc welding has limited use in the electronics industry because it can damage electric components irreversibly.
Handheld laser welding machines are becoming popular in several part manufacturing industry. They have some advantages and disadvantages over traditional welding techniques. Hence, they have variable applications. This article compared both welding systems, to inform you on choosing the right one for your project. If you have any questions, please contact us concerning the different welding methods.
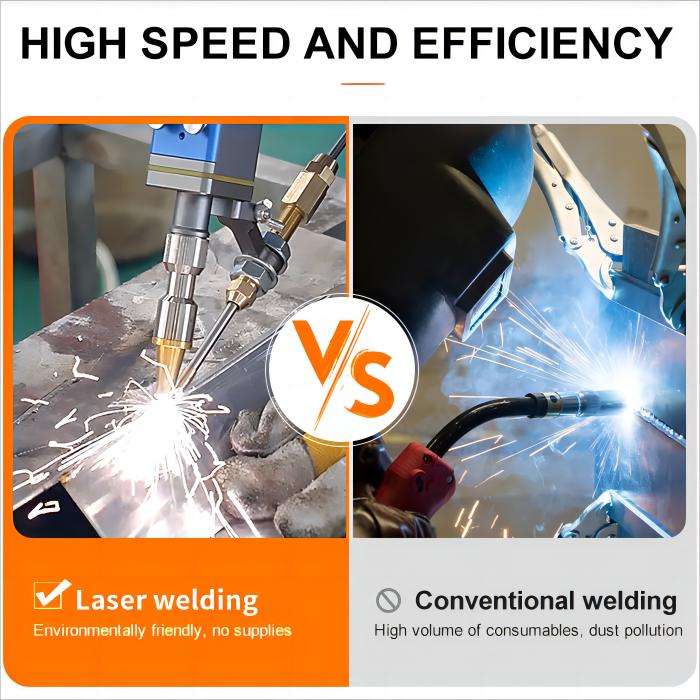
Handheld Laser Welding Machine Buying Guide
If you’re buying a laser welding machine for the first time, it’s worth knowing some getting started tips. When choosing a laser welding machine, the following aspects can be considered.
How to Select the Right Laser Type
Your laser welding machine can be equipped with either pulsed or continuous wave (CW) lasers, and the choice depends largely on the material thickness you’re working with. Pulsed lasers are ideal for thin and delicate metals, as they minimize the risk of deformation or melting. These lasers are commonly used for applications like welding sheet metal, razor blades, gold jewelry chains, and similar materials.
On the other hand, CW lasers are more suitable for welding thicker metal workpieces and perform especially well with refractory metals. However, using a CW laser on thinner parts can cause damage, so it's essential to match the laser type to the material's thickness.
How to Choose the Right Power for a Laser Welding Machine
The laser generator is the core component of any laser welding machine, and the power level directly impacts the welding depth. For instance, if a welding depth of 0.5mm to 3mm is required, a 1000W laser welding machine should suffice. However, if you're performing penetration or spot welding, a 1000W machine will be suitable. For continuous welding applications, it's advisable to opt for a higher-powered machine, such as a 1500W or 2000W model, to ensure better performance.
If you're uncertain about the power requirement for your specific application, it’s a good idea to consult experts. FORSUN CNC offers guidance to help you select the most appropriate laser welding machine for your needs.
How to Select the Configuration of a Laser Welding Machine
The configuration of a laser welding machine varies depending on its intended application. For example, mold welding, jewelry welding, and fiber transmission laser welding machines each have different configurations tailored to their specific uses, which results in varying prices. When purchasing a laser welding machine, it’s important to choose a configuration that suits your product type, processing techniques, and specific requirements.
How to Choose the Best Laser Welding Machine Supplier
First and foremost, it’s crucial to ensure that you’re working with a reputable laser equipment manufacturer, as this guarantees the quality of the machine. Additionally, the after-sales service offered by the supplier plays a significant role. FORSUN CNC, for example, provides free technical support and training to customers, helping you quickly become proficient in operating your laser welding machine. This level of support ensures you can rely on expert guidance whenever technical questions arise during operation.
Maintenance and Best Practices
1. Tips on Maintaining a Handheld Laser Welding Machine
- Regular Cleaning of the Optical Components: Dust and debris can accumulate on the optical lenses and mirrors, impacting the laser's efficiency. Regularly clean these components with a soft, lint-free cloth and appropriate cleaning solutions to prevent contamination.
- Monitor the Cooling System: Most handheld laser welding machines are equipped with water or air cooling systems. Ensure that the coolant levels are maintained and that the system is functioning properly to avoid overheating, which can damage the laser generator.
- Inspect Cables and Connectors: Regularly check the optical fiber cables and electrical connectors for wear, tear, or loose connections. Replace any damaged components to prevent power loss or inconsistent laser performance.
- Lubricate Moving Parts: Any mechanical parts, such as pulleys or guide rails, should be lubricated according to the manufacturer’s instructions to ensure smooth operation and avoid unnecessary wear.
- Software and Firmware Updates: Keep the machine’s software and firmware up to date, as manufacturers often release updates that can enhance performance, fix bugs, or add new features.
2. Common Mistakes to Avoid
- Neglecting Regular Maintenance: Skipping regular maintenance can lead to reduced machine efficiency and shorter lifespan. It's essential to follow the maintenance schedule provided by the manufacturer to ensure optimal performance.
- Overpowering Thin Materials: Using too much laser power on thin materials can lead to deformation, warping, or even complete destruction of the part. Make sure to adjust the power settings according to the thickness and type of material being welded.
- Incorrect Focus Settings: Failing to properly adjust the focal length of the laser can result in poor-quality welds. Ensure that the laser is correctly focused on the workpiece to achieve the best results.
- Improper Cooling System Use: Neglecting to monitor the cooling system can cause the laser welding machine to overheat. Always check that the cooling system is working properly and that coolant levels are adequate before each operation.
- Not Wearing Proper Safety Gear: Laser welding can be dangerous if proper safety precautions are not taken. Always wear protective eyewear, gloves, and other safety gear to avoid injury from laser exposure or hot materials.
By following these maintenance tips and avoiding common mistakes, you can extend the life of your handheld laser welding machine and maintain high-quality welding performance.
Conclusion
Choosing the best handheld laser welding machine requires careful consideration of factors such as laser type, power, configuration, and the reputation of the manufacturer. Leading brands like KRRASS, IPG, and Raycus offer a variety of models catering to different welding needs, from thin and delicate materials to thick, heavy-duty metals. By selecting a machine that matches your specific welding requirements and budget, you can achieve high-quality results while optimizing efficiency and cost. Whether you’re looking for precision, versatility, or value for money, a well-chosen handheld laser welding machine will be a valuable asset to your operations.