In the contemporary manufacturing and fabrication landscape, achieving precision and efficiency is non-negotiable. Selecting the appropriate cutting technology plays a pivotal role in determining the quality and cost-effectiveness of your production capabilities. Among the array of options available, CNC Fiber Laser cutting and Water Jet cutting emerge as prominent contenders, each offering distinct advantages and capabilities. In this blog post, we'll conduct a comparative analysis of these technologies to empower you with the insights necessary for making an informed decision tailored to your specific requirements.
Table of Contents
Differences Between Water Jets And Fiber Lasers
Understanding the differences between water jets and fiber lasers is essential for making informed decisions in manufacturing and cutting applications. Water jets rely on a high-pressure stream of water sometimes mixed with abrasive particles to erode and cut materials, making them remarkably versatile and ideal for heat-sensitive substances. On the other hand, CNC fiber lasers employ a high-powered laser beam to melt or vaporize materials with exceptional precision, especially suited for metals. The choice between these technologies hinges on a variety of factors, including material type, thickness, precision requirements, speed, heat sensitivity, environmental considerations, and maintenance costs. Careful evaluation of these factors help ensure that the selected cutting method aligns with the needs of your production.
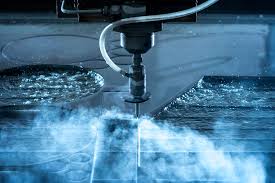
Advantages of Water Jet Cutting:
Versatility: Water jet cutting machines can cut through a wide range of materials, including metals, plastics, composites, stone, glass, ceramics, and even food products. Water jets are suitable for materials that are sensitive to heat.
Precision: Water jet cutting machines are known for their high precision, allowing for intricate designs and tight tolerances. It can produce accurate cuts with minimal material wastage.
No Heat-Affected Zone (HAZ): Since water jet cutting does not generate heat, there is no heat-affected zone. This is particularly valuable when working with materials that can be affected by heat exposure.
Reduced Material Waste: The narrow kerf width of water jet cutting results in minimal material wastage, which can lead to cost savings over time.
Low Noise Level: Water jet cutting generates relatively low noise levels, making it more operator-friendly compared to some other cutting methods.
No Need for Secondary Processing: Water jet cutting often produces finished edges, reducing the need for secondary finishing operations like deburring.
Disadvantages of Water Jet Cutting:
Slower Cutting Speed: Water jet cutting is generally slower compared to some other cutting methods, such as laser cutting or plasma cutting. This can affect overall production rates and costs.
Operating Costs: The high-pressure pumps and abrasive materials used in water jet cutting result in higher operating costs, including maintenance and consumables.
Abrasive Water Jets: When abrasive particles are added to the water jet for tougher materials, it causes wear and tear on the cutting head and equipment over time.
Complex Setup: Setting up and programming water jet cutting machines can be complex, requiring skilled operators and precise calibration for optimal results.
Water Disposal: Dealing with wastewater generated in the cutting process may require special handling and disposal procedures, which adds to operational costs.
In summary, water jet cutting offers precision and versatility, making it an excellent choice for various applications, especially when heat-sensitive materials or intricate designs are involved. However, it may have limitations in terms of cutting speed and operational costs. Careful consideration of the specific application and materials is necessary to determine if water jet cutting is the right choice for your production needs.
Advantages And Disadvantages Of Fiber Lasers
Fiber lasers have gained popularity in various industries for their precision and efficiency. However, like any technology, they come with their own set of advantages and disadvantages. Here’s a breakdown of the key pros and cons of fiber lasers:
Advantages of Fiber Lasers:
High Precision: Fiber lasers offer exceptional precision, making them suitable for cutting, engraving, and marking applications that require intricate designs and tight tolerances.
Speed: Fiber lasers are known for their high cutting and marking speeds. They can significantly improve production rates compared to some other cutting methods.
Versatility in Metal Cutting: Fiber lasers excel at cutting various metals, including steel, aluminum, and copper. They are widely accepted as the best option in metalworking industries.
Minimal Heat-Affected Zone (HAZ): Fiber lasers generate minimal heat during the cutting process, resulting in a small heat-affected zone. This is important for materials that may warp or deform due to heat exposure.
Energy Efficiency: Fiber lasers are energy-efficient, consuming less power compared to some other laser types. This leads to cost savings over time.
Longevity: Fiber laser sources have a long operational lifespan, providing consistent performance over an extended period.
Low Maintenance: Fiber lasers typically require minimal maintenance, resulting in less downtime and reduced operational costs compared to other cutting methods.
Disadvantages of Fiber Lasers:
Initial Cost: The upfront cost of purchasing and setting up a fiber laser system can be relatively high. This can be a barrier to entry for smaller businesses. However, with our wide variety of financing options found here, Moore Machine Tools offers affordable options to suite your needs.
Material Limitations: While fiber lasers are excellent for cutting metals, they may not be as versatile as other cutting methods when it comes to working with non-metal materials like ceramics, glass, or plastics.
Limited Thickness for Some Metals: Fiber lasers may have limitations in cutting extremely thick metal materials.
Environmental Concerns: Fiber lasers may produce harmful fumes and by-products when used on certain materials, necessitating exhaust and filtration systems for safe operation.
To summarize, fiber lasers offer high precision, speed, and efficiency, making them a preferred choice for a wide range of applications, particularly in metalworking industries. However, they may have limitations in terms of material versatility and upfront costs. Careful consideration of the specific application and material requirements is essential to determine if fiber lasers are the right choice for you.
Comparing Water Jets And Fiber Lasers
1. Cutting Mechanism:
Water Jet Cutting: Utilizes a high-pressure stream of water mixed with abrasive particles or pure water to erode and cut materials. It is versatile and ideal for materials sensitive to heat.
Fiber Laser Cutting: Employs a high-powered laser beam to melt or vaporize the material being cut. It is exceptionally precise and suitable for metals and other materials.
2. Material Compatibility:
Water Jet Cutting: Compatible with a wide range of materials, including metals, stone, glass, ceramics, plastics, and composites. Ideal for heat-sensitive materials.
Fiber Laser Cutting: Primarily used for metals like steel, aluminum, copper, and some non-metal materials. Less versatile when it comes to non-metal materials.
3. Thickness of Materials:
Water Jet Cutting: Suitable for a broad range of material thicknesses, from thin to several inches, making it ideal for thick materials.
Fiber Laser Cutting: Well-suited for thin to medium-thickness materials, but may have limitations with extremely thick materials.
4. Precision and Tolerance:
Water Jet Cutting: Offers high precision but may have slightly larger tolerances compared to fiber lasers. Well-suited for intricate designs and tight tolerances.
Fiber Laser Cutting: Known for exceptional precision, capable of achieving very tight tolerances. Ideal for intricate and detailed work.
5. Speed:
Water Jet Cutting: Generally slower compared to fiber laser cutting, which can affect production rates for some applications.
Fiber Laser Cutting: Known for its high cutting speed and efficiency, making it ideal for applications where speed is crucial.
6. Heat-Affected Zone (HAZ):
Water Jet Cutting: Generates no heat, resulting in no heat-affected zone. Suitable for materials sensitive to heat.
Fiber Laser Cutting: While it generates heat, the HAZ is minimal compared to other heat-based cutting methods.
7. Noise Level:
Water Jet Cutting: Generates relatively low noise levels, making it more operator-friendly.
Fiber Laser Cutting: Can be noisier due to the laser beam’s operation, requiring hearing protection in some cases.
Main Factors In Choosing Water Jets Or Fiber Lasers
Choosing between water jet cutting and fiber laser cutting requires a careful evaluation of several factors to ensure that the selected method aligns with your specific application and production requirements. Here are the key factors to consider when making this decision:
1. Material Type:
Consider the types of materials you will be cutting or machining. Water jet cutting is versatile and can handle a wide range of materials, including metals, stone, glass, ceramics, plastics, and composites. Fiber laser cutting is primarily suited for metals (e.g., steel, aluminum, copper) but may not be as versatile for non-metal materials.
2. Material Thickness:
The thickness of the materials you work with is crucial. Water jet cutting is suitable for thin to thick materials, including those several inches thick. Fiber laser cutting is ideal for thin to medium-thickness materials, but may have limitations with extremely thick materials.
3. Precision and Tolerances:
Consider the level of precision and tight tolerances required for you. Fiber laser cutting is known for exceptional precision and is ideal for applications demanding intricate designs and fine details. Water jet cutting is precise but may have slightly larger tolerances.
4. Speed and Production Efficiency:
Evaluate the speed and efficiency requirements for your production needs. Fiber laser cutting is faster and more efficient than water jet cutting, making it suitable for applications where speed is crucial.
5. Heat Sensitivity:
Determine if the materials you work with are sensitive to heat. Water jet cutting generates no heat and is suitable for heat-sensitive materials. Fiber laser cutting, while producing minimal heat, may still have a heat-affected zone, which can be a concern for some materials.
6. Edge Quality:
Assess the desired edge quality for your cut parts. Fiber laser cutting typically provides high-quality edge finishes with minimal to no burrs. Water jet cutting also offers good edge quality, but the results can vary depending on the material and cutting parameters.
7. Noise Level:
Consider the noise levels generated by each method, as this can affect the working environment. Water jet cutting generates relatively low noise levels, while fiber laser cutting can be noisier due to the laser beam operation, potentially requiring hearing protection in some cases.
8. Initial Investment:
Evaluate the upfront investment required for each technology, including the cost of purchasing and setting up the equipment. Water jet cutting systems may have a lower initial cost compared to fiber laser systems.
9. Specific Application Requirements:
Your choice should ultimately align with your specific application and production requirements. Factors like the desired cut quality, material versatility, and part volumes play a significant role in determining the most suitable technology.
By carefully considering these factors, you can make an informed decision between water jet cutting and fiber laser cutting, ensuring that the chosen method meets your unique needs and constraints.
Conclusion
In conclusion, the choice between water jets and fiber lasers in cutting and machining applications ultimately depends on your unique requirements. Water jets offer versatility, minimal heat generation, and precision. Fiber lasers, on the other hand, provide exceptional speed, higher precision, and edge quality. Each technology has its own set of advantages and limitations, and it’s crucial to carefully consider factors such as material type, thickness, precision needs, and speed. We suggest reaching out to a trusted team of industrial machine specialists to help guide you on which machine would better work for your specific production needs.