Table of Contents
What Is An Ironworker Machine
An ironworker machine is a multi-functional machine that can perform a variety of diverse and vital tasks. They’re typically hydraulic or mechanical, with hydraulic machines being more common in modern applications.
One of the main reasons why you need an ironworker is that it enables you to perform multiple tasks with a single machine. This saves time, reduces costs, and increases your overall productivity.
These machines are also highly versatile, and they’re designed to be durable and long-lasting. This means that they can withstand heavy use and are less likely to require repairs or replacement, while delivering many years of reliable performance.
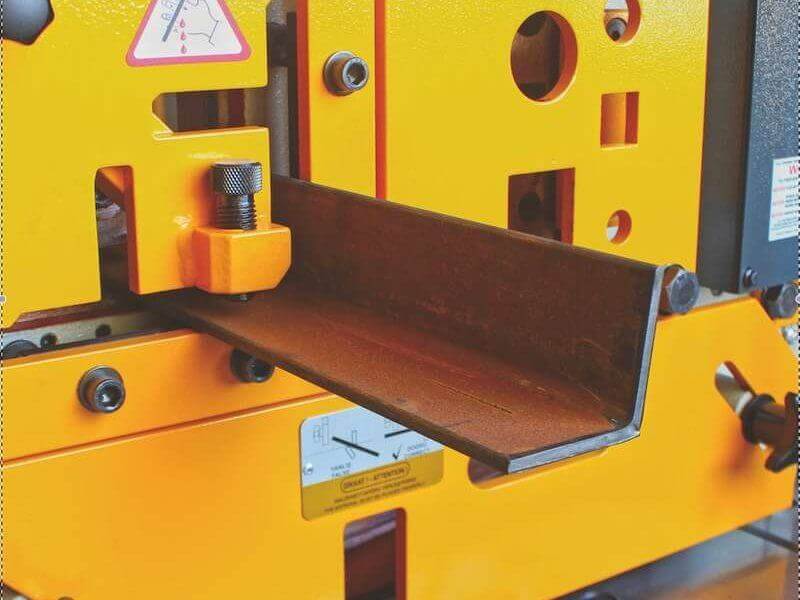
What Does An Ironworker Do
An ironworker machine is a versatile piece of equipment used in metalworking and fabrication. It performs a variety of tasks, making it an essential tool in many industrial settings. Here's what an ironworker machine can do:
Cutting: Ironworker machines are capable of cutting various types of metal, including steel, stainless steel, aluminum, and copper. They can perform straight cuts, angle cuts, and notch cuts, allowing for precise and clean cutting of metal sheets, plates, and structural components.
Punching: Ironworkers have punching capabilities, allowing them to create holes of different shapes and sizes in metal materials. This is useful for creating openings for fasteners, electrical wiring, and ventilation in fabricated metal products.
Shearing: Shearing is another important function of ironworker machines. They can shear metal sheets and plates to desired lengths and widths, producing straight and accurate cuts with minimal distortion.
Notching: Ironworkers can perform notching operations, which involve cutting V-shaped or rectangular notches into metal components. Notches are commonly used for creating joints, connections, and other features in metal structures.
Bending: Some ironworker machines come equipped with bending attachments or accessories, allowing them to bend metal bars, rods, and profiles into various shapes and angles. This capability adds versatility to the machine, enabling it to perform a wider range of metalworking tasks.
Angle Cutting: Ironworkers are capable of cutting metal angles at precise angles, such as 45-degree or 90-degree cuts. This functionality is essential for fabricating structural components and framework used in construction and manufacturing.
Bar Shearing: Ironworker machines can shear round bars, square bars, and flat bars to specific lengths, making them suitable for producing metal components used in construction, machinery, and infrastructure projects.
Ironworker machines offer a comprehensive solution for metal fabrication tasks, combining cutting, punching, shearing, notching, and bending capabilities in a single machine. They are widely used in industries such as construction, manufacturing, metalworking, and fabrication, where efficiency, accuracy, and versatility are essential for producing high-quality metal products.
How to Choose Best Ironworker Machine for Your Shop
Choosing the best ironworker machine for your shop involves considering several factors to ensure that it meets your specific needs and requirements. Here's a step-by-step guide to help you make an informed decision:
Assess Your Needs:
Begin by assessing the types of metalworking tasks you regularly perform in your shop. Determine the maximum thickness and width of the metal materials you typically work with, as well as the types of cuts, punches, bends, and notches you require.
Consider Capacity:
Look for an ironworker machine with the capacity to handle the size and thickness of metal materials you work with. Consider factors such as the maximum cutting and shearing capacities, punching force, and bending capabilities of the machine.
Evaluate Features:
Evaluate the features and capabilities of different ironworker models available in the market. Consider factors such as the number of workstations (e.g., punching, shearing, bending), the range of tooling options available, the speed and efficiency of operation, and any additional features that may enhance productivity and versatility.
Check Tooling Compatibility:
Ensure that the ironworker machine you choose is compatible with a wide range of tooling options, including punches, dies, blades, and bending attachments. This allows you to perform a variety of metalworking tasks without the need for additional equipment.
Consider Space and Layout:
Evaluate the available space in your shop and determine the optimal location for the ironworker machine. Consider factors such as floor space, ceiling height, access to power sources, and the layout of other equipment and workstations in your shop.
Assess Durability and Reliability:
Choose an ironworker machine from a reputable manufacturer known for producing high-quality, durable, and reliable equipment. Consider factors such as the construction materials, design features, warranty coverage, and customer reviews to assess the durability and reliability of the machine.
Think About Safety:
Prioritize safety features when choosing an ironworker machine for your shop. Look for features such as safety guards, emergency stop buttons, overload protection, and safety interlocks to minimize the risk of accidents and injuries during operation.
Consider Cost and Budget:
Finally, consider your budget and the overall cost of purchasing, installing, and maintaining the ironworker machine. Compare prices from different suppliers, taking into account factors such as the initial purchase price, shipping and installation costs, ongoing maintenance expenses, and any financing options available.
By carefully evaluating your needs, considering key features, assessing space and layout requirements, prioritizing safety, and staying within your budget, you can choose the best ironworker machine for your shop that meets your metalworking needs and helps improve productivity and efficiency.
Conclusion
Overall, ironworker machines are essential tools in metal fabrication and manufacturing industries, providing versatility, efficiency, and precision in performing a wide range of metalworking tasks.