A brake press machine is a versatile and essential tool in metal fabrication, used to bend and shape sheet metal into precise forms. By applying a significant amount of force through its ram, the brake press machine ensures accurate and consistent bends, making it invaluable in industries such as automotive, aerospace, construction, and manufacturing. Whether creating simple bends or complex shapes, this machine enhances production efficiency and quality, making it a cornerstone of modern metalworking processes.
Table of Contents
What Does a Brake Press Machine Do?
A press brake is a piece of manufacturing equipment that is used to bend sheet metal. It is typically narrow and long so that large pieces of sheet metal can be bent by it. Press brakes perform these bends by clamping the sheet or plate between the movable punch and the stationary die. The bends are all predetermined, and the punch and die are designed for specific lengths and shapes. A metal may be bent several times by a press brake until the desired form has been achieved.
Why Is It Called a Press Brake?
Why is a press brake called a ‘press brake’ to begin with? In the 14th century a “brake” was defined as a tool for crushing and pounding; over time that term became synonymous with machine.
“Press” comes from the word “presse,” which was used as a noun meaning “to crush or to crowd”; the term evolved to mean a machine or tool that applies force by squeezing. In modern times, press is added to brake as a modifier to describe what actuates the machine, what tools are used to form the workpiece or what types of bends the machine produces.
How Does the Bending Process Work?
Bending sheet metal requires a significant amount of force, measured in tonnage. This force is delivered through various methods as the punch is lowered onto the sheet metal. There are several types of press brake technology used to achieve this:
- Hydraulic (e.g., CNC press brakes)
- Pneumatic
- Electric power
- Mechanical
The method of force application often determines the name of the press brake, such as hydraulic press brake or servo electric press brake.
Press brakes vary in the amount of force they can provide, known as tonnage, which measures the tons of force the press brake can deliver. Higher tonnage allows for bending thicker metal. Hydraulic presses are typically used for achieving very high force levels, while pneumatic and servo electric presses deliver lesser amounts of force.
Different types of press brakes also offer varying speeds and accuracies. Servo electric press brakes generally provide the highest degree of accuracy. Pneumatic and servo electric press brakes are typically faster than hydraulic and mechanical brakes, saving valuable time during the bending process.
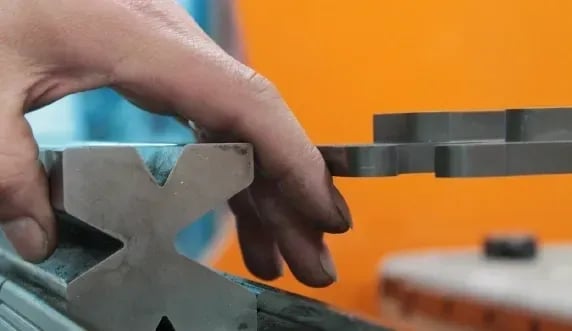
Additional Considerations
Press brake Machine can make a variety of different bends on many different types of metals. When preparing to bend, it is important to consider the metal type being bent, the die, the punch, and the bending force.
Understanding the metal type is important because each metal has differing physical properties. For instance, a high carbon steel will generally be less bendable by a press brake than many aluminum alloys because of the differences in ductility and strength. Metals typically have a recommended minimum bend radius or distance that they can be bent to without being damaged.
The die and the punch used on the press brake both have a large impact on the bending results. They are a set designed in such a way that when the sheet metal is clamped between them it bends into the pre-determined shapes and angles. The die is a hollow material that the metal is placed on top of prior to bending. It is a very hard and strong substance that is near in form to the desired shape of the metal being bent.
The punch is a solid material that is lowered down onto the metal. Since the pressing action of the punch onto the metal and the die are what causes the metal to bend, both shapes must be accurately suited to the bending job.
The correct metal shape following a press brake operation is dependent on the size and shape of the punches and dies. Dies and punches are typically designed in such a way that they can be interchanged easily to accommodate a wide array of jobs.
Common Brake Press Machine Applications
Since brake press machines can be equipped with a wide range of punches and dies, they are versatile tools suitable for almost any sheet or plate metal shaping applications. The most common applications include:
- Automotive panels
- Airframes
- Metal artwork
- Furniture
- Metal containers
- Various other sheet metal forming applications
Brake press machines are particularly useful for producing multiple identical pieces for further processing. Their ability to handle diverse bending tasks makes them indispensable in numerous industries.
Top 4 Benefits of a Press Brake Machine in Metal Fabrication
1. Less Waste
Unlike other fabrication techniques, the press brake notably generates less material waste. This can be attributed to the machine’s ability to curve, cut, or bend sheet metal into accurate pieces, maximising the raw material used.
Most press brake machines are computer numerically controlled (CNC), which means they are fully automated, and all of their components are designed to follow an effective procedure. Because of this, there is less waste produced. This allows operators to perform press brake operations efficiently and quickly. It also reduces the manufacturing lead time and cost burden on customers. There is also a decreased need for post-processing of the fabricated metal parts.
2. In-House Manufacturing
A press brake machine enables whole or partial in-house manufacturing for metal fabricators, particularly if sheet metal bending is concerned. Since having their own machine enables companies to manufacture their own materials, they can eliminate the need for offshoring, which is expensive and unsustainable at times.
Companies that do their own metal works in Perth can see how cost-effective it is to own a press brake machine in the long run. You don’t need to spend too much on training your team. Additionally, you can focus on in-house development for your long-term growth.
3. Creation of Complex Designs
The fabrication of sheet metal is essential for almost every industry. For example, construction companies need fabrications to create rafters, beams, and other structural materials for their projects. The food and beverage industry also needs metal fabrications to make equipment essential to food service, such as conveyor belts, weighing scales, mixers, and more.
The evolution of the press brake machine over the years is noteworthy. From being equipment used to bend metals into shape, it can now create more complex designs. Nowadays, press brakes come with customisable parts, which allows fabricators to perform various tasks, including burring, coining, and bends, to name a few.
4. Automated Operations
Depending on the requirements, a press brake machine can be operated manually. It can also be semi-automated or fully automated. Regardless of how it is run, this equipment is essential in improving the accuracy of parts and decreasing labour expenses.
Thanks to automation, tasks that used to be completed manually can now be performed more quickly and efficiently. The fabrication abilities of press brakes make this possible. If your company wan
Choosing the Best Press Brake Machine for Your Application
When investing in a press brake, the most important factors to consider are the bending length and tonnage. Understanding your application and proper planning will help you make the right decision.
Tonnage
The press brake’s bending force, or tonnage, determines the amount of pressure that can be applied by the punch during a bend. Higher tonnage allows for bending thicker and harder metals, while lower tonnage is more suitable for thinner metals.
Bending Length
The bending length of a press brake is the maximum length of a metal sheet that can be bent. For example, a 4-foot bending length press brake won’t be able to bend a 6-foot piece of sheet metal. You should select a press brake with a bending length slightly larger than the longest sheets you plan to bend. Keep in mind that there are two length factors to consider: the overall bed length and the bed length between the frames.
Hydraulic Press Brakes
One of the most common types of press brakes is hydraulic. Hydraulic press brakes can reduce job setup time and increase efficiency, especially when paired with CNC controls. CNC hydraulic press brakes come in various tonnages and sizes, determined by the thickness and size of the metal you are bending.
Other Types of Press Brakes
Other design types include mechanical and pneumatic press brakes, with the primary difference being the trigger mechanisms. Each type has its own advantages depending on the specific requirements of your application.
By considering these factors, you can choose the best press brake to meet your production needs, ensuring efficiency and precision in your metalworking processes.
Why Tonnage and Length Are Important
Tonnage and length are crucial because a press brake has a concentrated load limit in the center of the press calculated in tons per inch. Using the incorrect tonnage may damage the press ram, the die or the working part and, in the worst cases, even ruin the machine. Additionally, some tooling types have specific tonnage limits, including straight punches, particularly when paired with V-shaped dies.
Figuring out the press brake’s load limit can be done with some fairly basic math. You multiply the number of inches between the side columns by .6 and divide the result by the tonnage.
If you had 10.6 feet between the columns on a 350-ton press brake, for example. You would take the number of inches — 10.6 x 12 = 127.2 inches — and multiply that number by .6, which is 76.32. From there, divide that number by the tonnage — 350/76.32 = 4.58. In that case, the press brake’s load limit would be 4.58 tons per inch.
If you need to bend a 5-foot sheet on that press, you should use a press power of 275 because 60 inches x 4.58 tons per inch = 275.
This scenario changes for different types of machines and different types of metal. There are also other equations to use for determining press power.
These kinds of calculations are typically available in a chart on the machine or in the operations manual. However, a press brake operator should be aware of the material they are bending and calculate the proper press power. This will avoid using too little or too much force and prevent damage to the machine.
Is a Brake Press Machine a Press Brake?
Yes, a brake press machine is indeed a press brake. Both terms refer to the same type of machinery used in metalworking for bending and shaping sheet metal. These machines apply significant force through a punch and die system to create precise bends and folds in metal sheets, making them essential tools in various industries such as automotive, aerospace, construction, and manufacturing. The terms "brake press" and "press brake" are often used interchangeably, but they denote the same equipment and functionality.
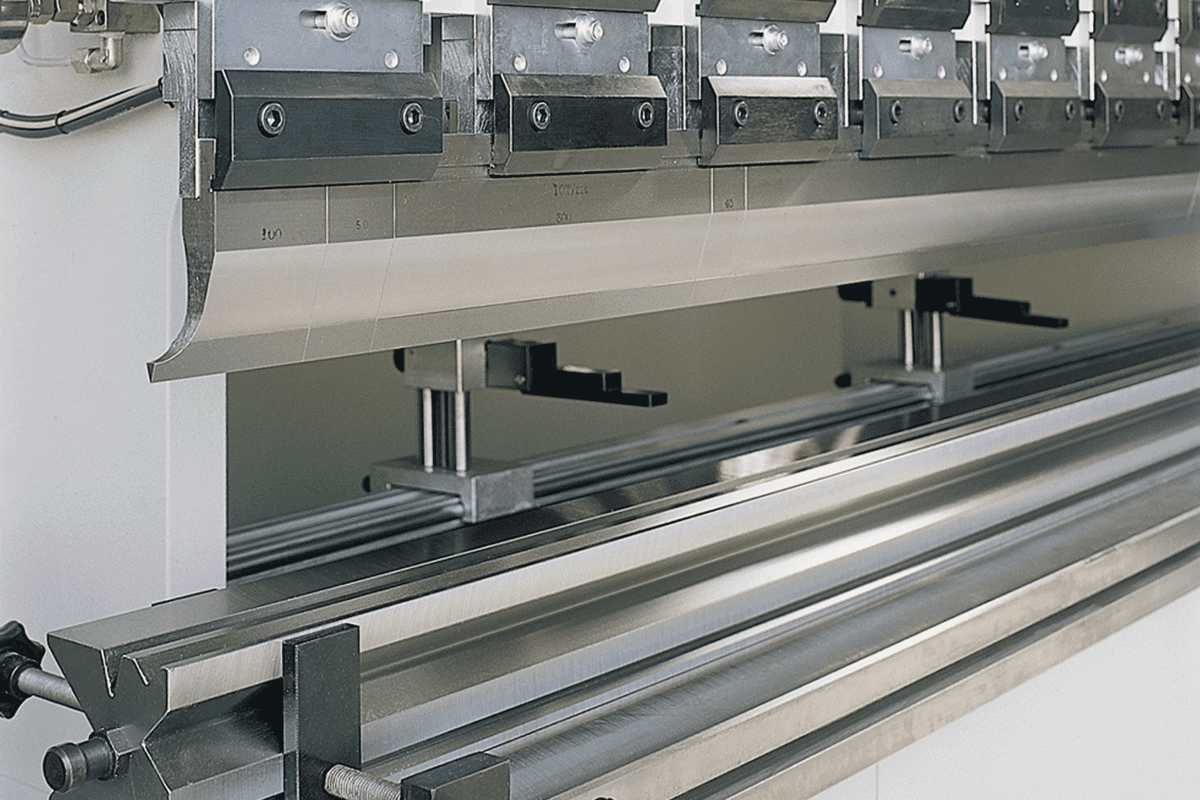
Types of Brake Press Brake and Comparison
Power source | Describe |
Mechanical | By synchronously driving the slider movement through the oil cylinders on the two side pillars, the stroke and tonnage can be stopped and adjusted during the bending process. |
Hydraulic type | By synchronously driving the slider movement through the oil cylinders on the two side pillars, the stroke and tonnage can be stopped and adjusted during the bending process |
Pneumatic | Using compressed air to drive slider movement |
Servo motor type | Precise control of slider movement using servo motors |
Conclusion
When exploring the press brake world, it is pivotal to choose a mature and advanced supplier. KRRASS is such a reliable partner.
We specialize in offering high-quality press brakes, shearing machines, and laser-cutting machines. Our products are well-designed and perform excellently to meet your various sheet metal processing needs.
We cordially invite you to visit our product page to learn more about our press brake range and technical advantages.
Whether you need effective solutions for improving production efficiency or enhancing product quality through advanced technology, KRRASS offers you professional support.