A hydraulic press brake is a machine tool used in metalworking to bend sheet metal and plate material. It utilizes hydraulic force to apply pressure on a workpiece, causing it to bend at a predetermined angle. Press brakes are commonly used in various industries, including manufacturing, construction, automotive, and aerospace, for forming components such as brackets, enclosures, panels, and structural elements.
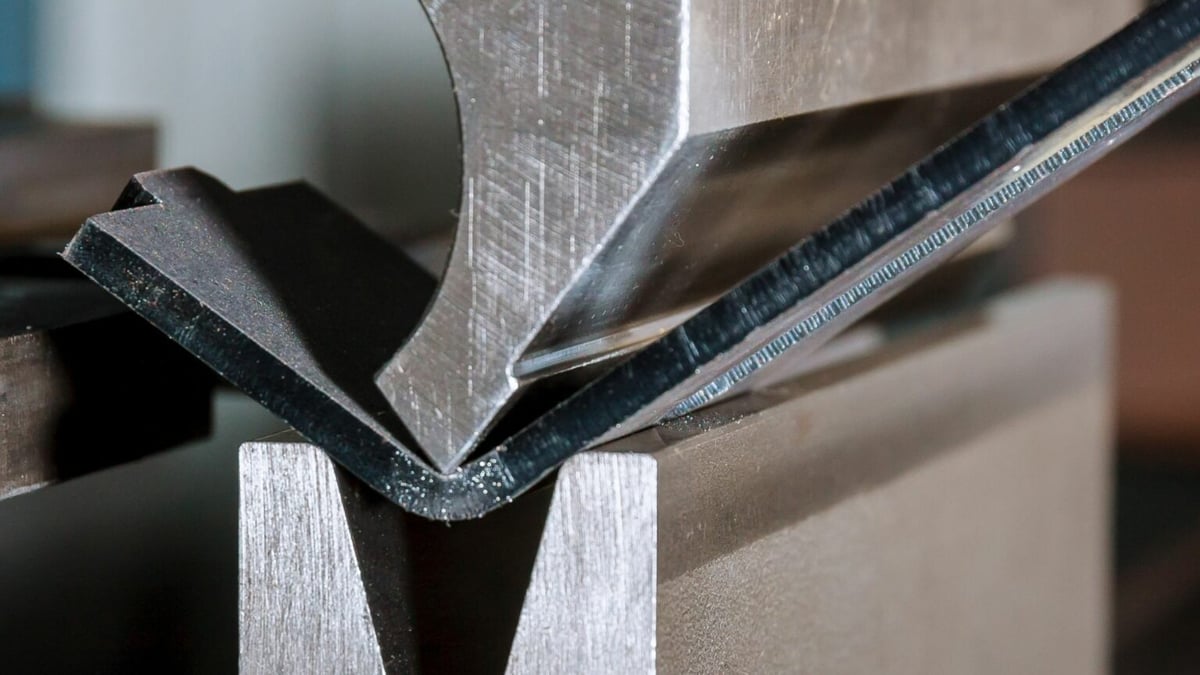
Here's an overview of the key components and operation of a hydraulic press brake:
1.Frame: The frame provides the structural support for the press brake and houses the other components. It is typically made of heavy-duty steel to withstand the forces involved in bending metal.
2.Hydraulic System: The hydraulic system of the press brake generates the force needed to bend the metal. It consists of a hydraulic pump, hydraulic fluid reservoir, valves, cylinders, and associated components. The hydraulic system allows for precise control over the bending process, including pressure, speed, and positioning.
3.Ram and Bed: The ram and bed are the primary components responsible for applying force to the workpiece. The ram, also known as the upper beam or slide, moves vertically downward to press the metal against the bed, which remains stationary during bending.
4.Tooling: Press brakes use specialized tooling, such as punches and dies, to shape the metal during bending. The punch applies force to the workpiece, while the die provides a matching surface against which the metal is formed. Tooling comes in various sizes and configurations to accommodate different bending requirements.
5.Back Gauge: Many press brakes are equipped with a back gauge system to accurately position the workpiece for bending. The back gauge consists of adjustable fingers or stops that can be positioned along the bed to ensure consistent bending dimensions and angles.
6.Control System: Modern press brakes often feature computerized control systems, such as CNC (Computer Numerical Control), to automate and streamline the bending process. These systems allow operators to program bending sequences, angles, and dimensions, increasing productivity and accuracy.
7.Safety Features: Press brakes are equipped with various safety features to protect operators and prevent accidents. These may include safety guards, light curtains, two-hand controls, emergency stop buttons, and interlocking mechanisms to ensure safe operation.
Hydraulic press brakes offer several advantages over mechanical or pneumatic alternatives, including greater bending force, precision control, versatility, and ease of operation. They are capable of bending a wide range of materials and thicknesses, making them indispensable tools in modern metal fabrication and manufacturing processes.
What are the Advantages of a Hydraulic Press Brake?
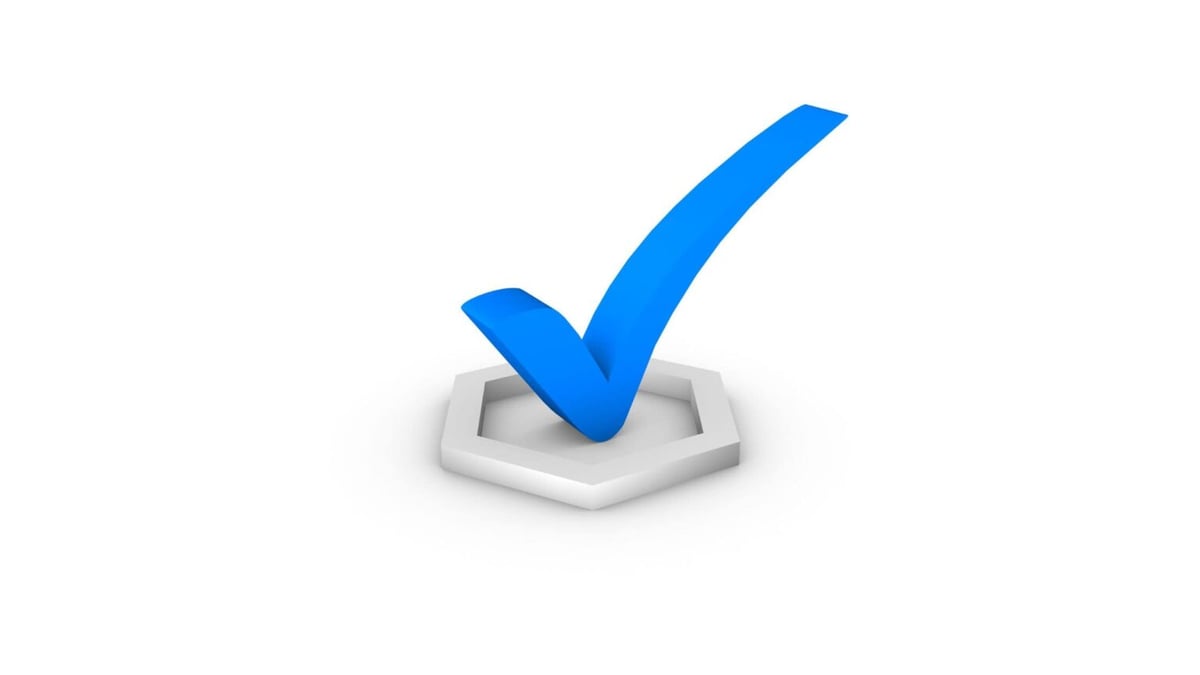
1.Hydraulic press brakes offer several advantages over other types of bending machines, such as mechanical press brakes or pneumatic brakes. Here are some of the key advantages of hydraulic press brakes:
2.High Bending Force: Hydraulic press brakes can generate significant bending force, making them suitable for bending thick and high-strength materials. The hydraulic system allows for precise control over the bending force, ensuring consistent and accurate results across a wide range of materials and thicknesses.
3.Versatility: Hydraulic press brakes are versatile machines capable of performing a variety of bending operations, including straight bends, box bends, U-bends, and more complex shapes. They can accommodate a wide range of tooling configurations and bending applications, making them suitable for diverse industries and manufacturing processes.
4.Precision and Accuracy: Hydraulic press brakes offer precise control over bending angles, dimensions, and positioning. Advanced control systems, such as CNC (Computer Numerical Control), enable operators to program complex bending sequences and parameters with high accuracy and repeatability. This results in consistent part quality and reduced scrap rates.
5.Ease of Operation: Hydraulic press brakes are relatively easy to operate, especially with the integration of modern control systems. Operators can set up and adjust bending parameters quickly and intuitively, reducing downtime and increasing productivity. Additionally, hydraulic press brakes typically have smoother and quieter operation compared to mechanical alternatives.
6.Safety: Hydraulic press brakes are equipped with various safety features to protect operators and prevent accidents. These may include safety guards, light curtains, two-hand controls, emergency stop buttons, and interlocking mechanisms. Additionally, the hydraulic system provides gradual and controlled bending motion, reducing the risk of sudden or unexpected movements.
7.Energy Efficiency: Hydraulic press brakes are generally more energy-efficient than mechanical alternatives, as they only consume power when actively bending material. Hydraulic systems can also be designed for energy recovery, where energy is stored and reused during the bending process, further reducing energy consumption and operating costs.
8.Durability and Reliability: Hydraulic press brakes are known for their durability and reliability, with heavy-duty construction and robust components designed for long-term performance in demanding industrial environments. With proper maintenance, hydraulic press brakes can provide years of trouble-free operation, contributing to overall equipment uptime and efficiency.
Overall, hydraulic press brakes are versatile, precise, and reliable machines that offer significant advantages for a wide range of metal bending applications. Whether bending thin sheet metal or thick plate material, hydraulic press brakes provide the bending force, control, and efficiency required for modern manufacturing processes.
Where are Hydraulic Press Brakes Used?
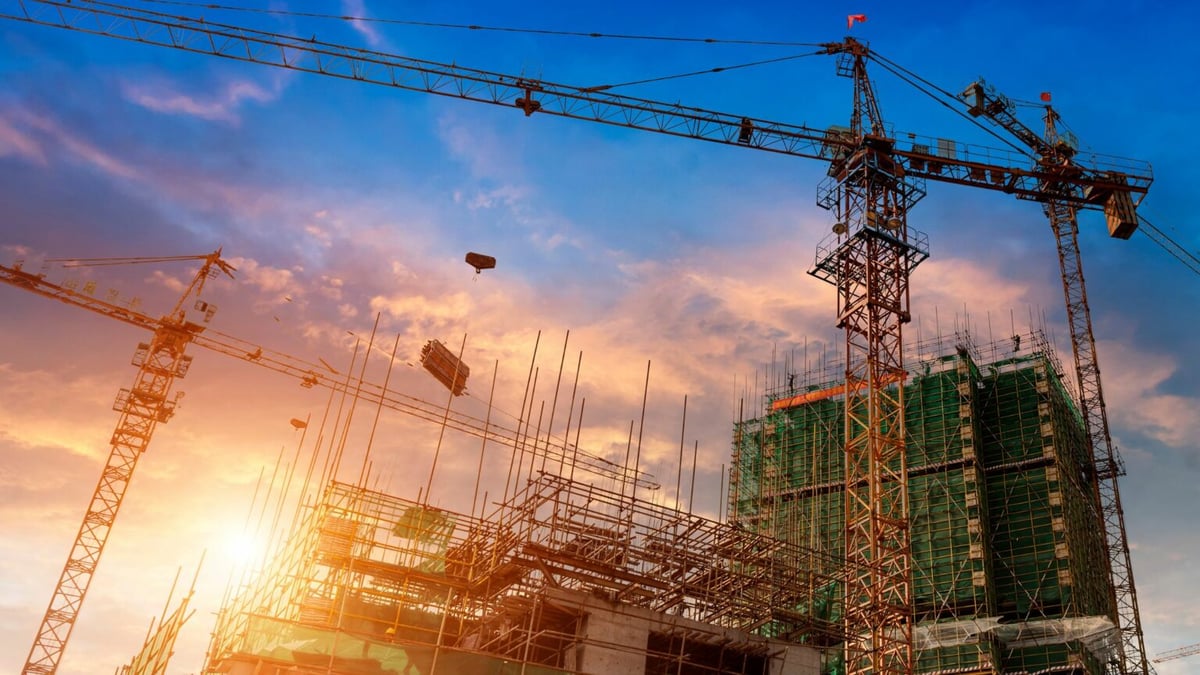
Hydraulic press brakes are used in various industries and applications where bending and forming of sheet metal or plate material is required. Some common industries and applications where hydraulic press brakes are used include:
1.Metal Fabrication: Hydraulic press brakes are widely used in metal fabrication shops and manufacturing facilities for bending and forming sheet metal and plate material to create components and products used in various industries.
2.Automotive Manufacturing: Hydraulic press brakes play a crucial role in the automotive industry for bending and forming sheet metal components used in vehicle bodies, chassis, frames, panels, brackets, and other parts.
3.Aerospace and Aviation: Hydraulic press brakes are used in the aerospace and aviation industries for fabricating components used in aircraft structures, wings, fuselages, landing gear, engine housings, and other aerospace applications.
4.Construction: Hydraulic press brakes are used in the construction industry for bending and forming sheet metal components used in architectural and structural applications, such as building facades, roofing, cladding, and structural support elements.
5.Appliances and Household Goods: Hydraulic press brakes are used in the manufacturing of appliances and household goods, such as refrigerators, ovens, washing machines, dryers, sinks, cabinets, and other consumer products that require sheet metal components.
6.Electronics and Electrical Equipment: Hydraulic press brakes are used in the production of electronics and electrical equipment, including enclosures, cabinets, panels, racks, and other components requiring precision bending and forming of sheet metal.
7.Industrial Machinery: Hydraulic press brakes are used in the manufacturing of industrial machinery and equipment, including machine frames, guards, enclosures, housings, platforms, and other structural components.
8.Shipbuilding and Marine Industry: Hydraulic press brakes are used in the shipbuilding and marine industry for fabricating components used in ship construction, such as hulls, decks, bulkheads, superstructures, and other marine applications.
9.Energy and Power Generation: Hydraulic press brakes are used in the energy and power generation industry for fabricating components used in power plants, renewable energy installations, transmission infrastructure, and other energy-related applications.
10.Custom Fabrication and Job Shops: Hydraulic press brakes are used in custom fabrication shops and job shops for bending and forming sheet metal components for a wide range of applications across various industries, including prototypes, one-off parts, and custom projects.
Overall, hydraulic press brakes are versatile machines used in numerous industries and applications where precise bending and forming of sheet metal or plate material are required to produce high-quality components and products.