An electric press brake is a type of machine used for bending sheet metal into various shapes and angles. It utilizes an electric motor to power the bending process, as opposed to hydraulic or mechanical systems found in traditional press brakes.
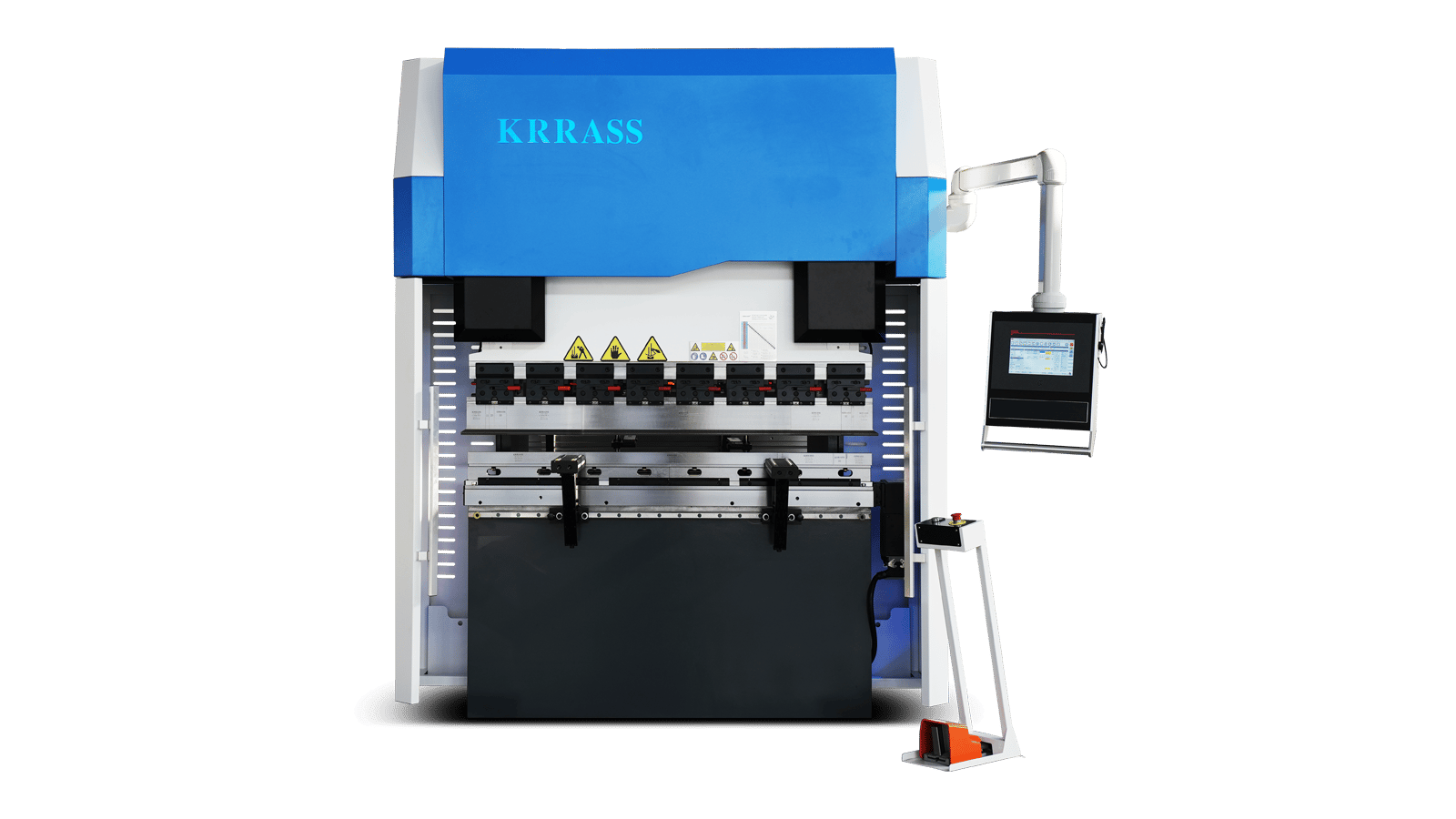
Here's how an electric press brake typically works:
1.Material Placement: The sheet metal to be bent is placed onto the machine's work area, usually between a pair of clamping tools to hold it securely in place.
2.Programming: The operator inputs the desired bending parameters such as angle, bend length, and material thickness into the machine's control system. Some modern electric press brakes feature CNC (Computer Numerical Control) systems, allowing for precise and automated bending sequences.
3.Bending Process: The electric motor drives a ram or beam, which applies force onto a tooling set (often a punch and die set) that presses against the sheet metal. The force exerted by the ram causes the sheet metal to bend to the specified angle.
4.Precision Control: Electric press brakes offer precise control over the bending process, allowing for accurate and repeatable bends. This precision is essential for achieving consistent results, especially in applications requiring tight tolerances.
5.Safety Features: Like other press brakes, electric press brakes are equipped with safety features such as light curtains, interlocks, and emergency stop buttons to ensure operator safety during operation.
6.Electric press brakes offer several advantages over hydraulic or mechanical press brakes, including:
7.Energy efficiency: Electric press brakes consume less energy compared to hydraulic systems, especially during idle periods.
Lower maintenance requirements: Electric press brakes typically have fewer moving parts than hydraulic systems, resulting in reduced maintenance needs and downtime.
8.Cleaner operation: Electric press brakes do not require hydraulic fluid, reducing the risk of oil leaks and environmental contamination.
Electric press brake uses
Electric press brakes are used for bending sheet metal in a wide range of industries and applications where precision, efficiency, and versatility are essential. Here are some common uses of electric press brakes:
1.Metal Fabrication: Electric press brakes are widely used in metal fabrication shops to bend sheet metal into various shapes and forms for products such as enclosures, brackets, panels, frames, and components for machinery and equipment.
2.Automotive Industry: In the automotive industry, electric press brakes are used for manufacturing components such as body panels, chassis parts, brackets, and reinforcements. The precise bending capabilities of electric press brakes ensure consistent quality in mass production.
3.Aerospace and Aviation: Electric press brakes are used in the aerospace and aviation sectors to fabricate components for aircraft structures, including panels, ribs, brackets, and ductwork. The ability to achieve tight tolerances and complex bends is critical in this industry to meet stringent safety and performance requirements.
4.Appliance Manufacturing: Electric press brakes play a significant role in producing components for household appliances such as refrigerators, ovens, washing machines, and HVAC systems. They are used to bend sheet metal for housing, cabinets, shelves, and other structural elements.
5.Electronics and Electrical Enclosures: Electric press brakes are used to fabricate enclosures and cabinets for electrical and electronic equipment, including control panels, junction boxes, switchgear, and server racks. These enclosures often require precise bending to accommodate components and ensure proper functionality.
6.Architectural Metalwork: In architectural and construction applications, electric press brakes are used to fabricate metal components for building facades, structural elements, interior fittings, and decorative features. They are employed to create custom shapes, angles, and profiles to meet design specifications.
7.Prototyping and Custom Fabrication: Electric press brakes are valuable tools for prototyping and custom fabrication projects across various industries. They enable manufacturers and fabricators to quickly produce prototypes, one-off parts, and small-batch production runs with minimal setup time and cost.
Overall, the use of electric press brakes has revolutionized sheet metal bending processes by offering precision, efficiency, and flexibility in a wide range of manufacturing applications. Their ability to produce high-quality bends with consistent accuracy makes them indispensable tools in modern metalworking operations.
Worries about electric press brake
While electric press brakes offer numerous benefits, there are also some potential concerns and considerations associated with their use. Here are a few worries that individuals or businesses might have regarding electric press brakes:
1.Initial Cost: One concern is the initial cost of purchasing an electric press brake, which can be higher compared to hydraulic or mechanical press brakes. However, it's essential to consider the long-term cost savings from energy efficiency, reduced maintenance, and increased productivity.
2.Complexity of Operation: Electric press brakes with advanced CNC systems may require specialized training for operators to program and operate effectively. Some operators might worry about the complexity of learning to use these systems, especially if they are accustomed to traditional hydraulic press brakes.
3.Reliability and Downtime: Like any machinery, electric press brakes are susceptible to breakdowns and downtime, which can disrupt production schedules and impact business operations. Businesses might worry about the reliability of electric press brakes and the potential costs associated with maintenance and repairs.
4.Compatibility with Existing Workflows: Integrating a new electric press brake into existing manufacturing workflows and processes can be a concern for businesses. They may worry about compatibility with existing tooling, software systems, and production methods, as well as the need for additional training and adaptation.
5.Risk of Electrical Issues: Electric press brakes rely on electrical components and systems, which can be vulnerable to issues such as power surges, electrical faults, or component failures. Businesses might worry about the risk of electrical problems causing downtime or safety hazards in the workplace.
6.Limited Tonnage and Capacity: Some electric press brakes may have limitations in terms of tonnage and capacity compared to larger hydraulic press brakes. Businesses with heavy-duty bending requirements might worry about whether electric press brakes can meet their needs effectively.
7.Environmental Impact: While electric press brakes offer energy efficiency benefits compared to hydraulic systems, concerns about their overall environmental impact may still arise. Businesses might worry about the environmental footprint associated with manufacturing and operating electric press brakes, including energy consumption and waste generation.
Addressing these worries often involves thorough research, consultation with manufacturers and suppliers, proper training for operators, and proactive maintenance and management practices. Despite these concerns, many businesses find that the benefits of electric press brakes outweigh the potential drawbacks, leading to increased productivity, efficiency, and quality in their metalworking operations.