A hydraulic press brake is a machine tool used in metal fabrication to bend sheet metal into various shapes and angles. It employs hydraulic cylinders to apply force to a bending punch, which presses the sheet metal against a die, causing it to bend. Hydraulic press brakes are widely used in industries such as manufacturing, automotive, aerospace, construction, and more due to their versatility, efficiency, and precision.
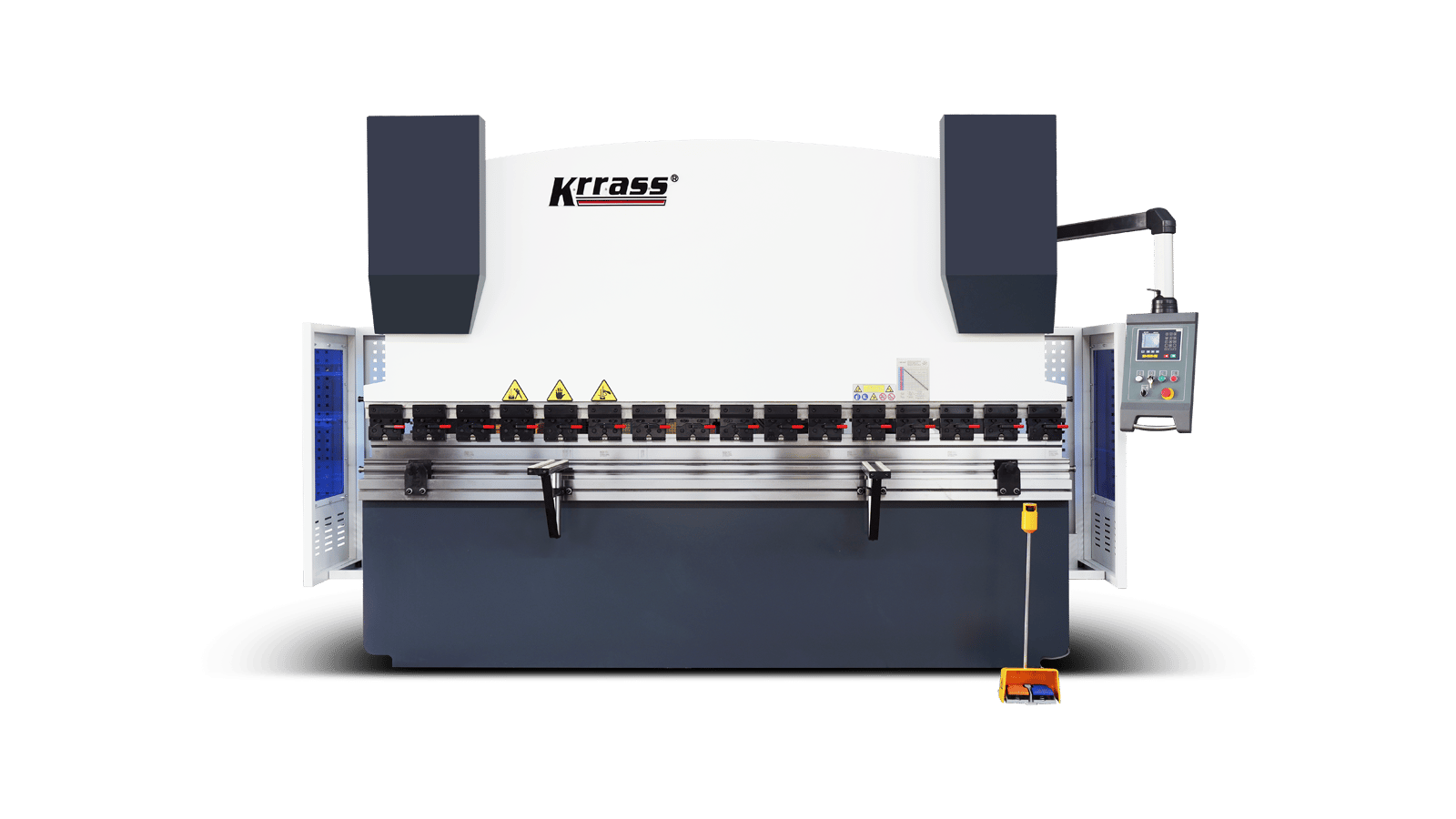
Here's how a hydraulic press brake typically works:
1.Material Placement: The sheet metal to be bent is positioned between the punch and die, which are mounted on the upper and lower beams of the press brake, respectively. The sheet metal is aligned with the desired bend line.
2.Bending Process: When the operator initiates the bending cycle, hydraulic fluid is pumped into cylinders located on either side of the press brake. The hydraulic cylinders exert force on a ram or beam connected to the upper beam of the press brake. This force causes the bending punch to descend and apply pressure to the sheet metal against the stationary die.
3.Bend Angle Control: The operator controls the bending process by adjusting parameters such as the depth of the bend, bending speed, and backgauge position. Hydraulic press brakes may feature manual, semi-automatic, or fully automatic control systems to facilitate precise bending operations.
4.Release and Removal: Once the desired bend angle is achieved, the hydraulic pressure is released, and the bending punch retracts, allowing the operator to remove the bent sheet metal from the press brake.
Hydraulic press brakes offer several advantages over other types of press brakes, including:
1.High Force: Hydraulic systems can generate high bending forces, making them suitable for bending thick and high-strength materials.
Versatility: Hydraulic press brakes can perform a wide range of bending operations, including air bending, bottoming, coining, and more.
2.Accuracy: Hydraulic press brakes provide precise control over the bending process, allowing for consistent and repeatable bend angles.
Safety: Hydraulic press brakes are equipped with safety features such as light curtains, interlocks, and emergency stop buttons to ensure operator safety during operation.
3.Reliability: Hydraulic systems are known for their reliability and durability, with minimal maintenance requirements compared to other types of press brakes.
The use of hydraulic press brake
Hydraulic press brakes are extensively used in metalworking industries for bending sheet metal into various shapes and forms. Their versatility, precision, and efficiency make them indispensable in a wide range of applications. Here are some common uses of hydraulic press brakes:
1.Metal Fabrication: Hydraulic press brakes are central to metal fabrication shops where they are used to bend sheet metal into components for various products. This includes bending sheets for enclosures, cabinets, frames, brackets, and other structural elements used in machinery, equipment, and infrastructure.
2.Automotive Industry: In automotive manufacturing, hydraulic press brakes are used for producing components such as body panels, chassis parts, brackets, and reinforcements. They enable the bending of sheet metal with precise angles and dimensions required for vehicle assembly.
3.Aerospace and Aviation: Hydraulic press brakes play a crucial role in the aerospace industry for fabricating components used in aircraft structures. This includes bending sheet metal for panels, ribs, brackets, and other structural elements that require strict adherence to tight tolerances and specifications.
4.Construction and Architectural Metalwork: Hydraulic press brakes are used in the construction industry for fabricating metal components used in building structures and architectural features. They can bend sheet metal for facade panels, roofing elements, beams, columns, and decorative elements with precise shapes and angles.
5.Appliance Manufacturing: Hydraulic press brakes are employed in the production of household appliances such as refrigerators, ovens, washing machines, and HVAC systems. They are used to bend sheet metal for appliance enclosures, cabinets, shelves, and other structural parts.
6.Electronics and Electrical Enclosures: In the electronics industry, hydraulic press brakes are used to manufacture enclosures and cabinets for electrical and electronic equipment. These enclosures house control panels, circuitry, and other components, requiring precise bending to ensure proper fit and functionality.
7.General Manufacturing and Prototyping: Hydraulic press brakes are used in various manufacturing processes for bending sheet metal components used in diverse products and industries. They are also valuable for prototyping and custom fabrication, allowing for quick and accurate bending of one-off parts and small production runs.
Worries about hydraulic press brake
While hydraulic press brakes offer numerous advantages, there are also some potential concerns and considerations associated with their use. Here are a few worries that individuals or businesses might have regarding hydraulic press brakes:
1.Maintenance Requirements: Hydraulic press brakes require regular maintenance to ensure optimal performance and prevent downtime. Concerns may arise regarding the cost and frequency of maintenance, as well as the availability of skilled technicians to perform maintenance tasks.
2.Fluid Leaks: Hydraulic press brakes utilize hydraulic fluid to generate force, and concerns may arise regarding the potential for fluid leaks. Fluid leaks can not only lead to contamination of the workpiece but also pose safety hazards for operators and contribute to environmental pollution.
3.Energy Consumption: Hydraulic press brakes can consume a significant amount of energy, especially during operation. Businesses may worry about the environmental impact and operating costs associated with energy consumption, particularly in regions with high electricity prices or stringent environmental regulations.
4.Noise and Vibrations: Hydraulic press brakes can generate noise and vibrations during operation, which may be a concern for operators' comfort and safety. Excessive noise and vibrations can also affect the surrounding workspace and potentially impact the quality of the bent components.
5.Limited Speed and Accuracy: While hydraulic press brakes offer high force capabilities, they may have limitations in terms of bending speed and accuracy compared to other types of press brakes, such as electric press brakes. Concerns may arise regarding productivity and the ability to meet tight production schedules and quality requirements.
6.Potential for Overloading: Hydraulic press brakes can be susceptible to overloading if operators exceed the machine's maximum capacity or apply excessive force during bending operations. Overloading can lead to equipment damage, costly repairs, and safety risks for operators.
7.Complexity of Operation: Hydraulic press brakes may have complex control systems and operating procedures, especially for advanced models with programmable features. Concerns may arise regarding the training and skill level required for operators to effectively program and operate hydraulic press brakes, as well as the potential for human error during operation.
Disadvantages of hydraulic press brake
While hydraulic press brakes offer numerous advantages for bending sheet metal, they also come with certain disadvantages. Here are some common disadvantages associated with hydraulic press brakes:
1.Energy Consumption: Hydraulic press brakes require significant energy to operate, especially during the bending process. The continuous use of hydraulic pumps and motors can lead to higher electricity costs compared to other types of press brakes.
2.Maintenance Requirements: Hydraulic press brakes have complex hydraulic systems that require regular maintenance to ensure optimal performance. This includes monitoring hydraulic fluid levels, inspecting hoses and seals for leaks, and maintaining hydraulic cylinders and valves. Neglecting maintenance can lead to costly repairs and downtime.
3.Fluid Leaks: Hydraulic press brakes utilize hydraulic fluid to generate force, and there is a risk of fluid leaks from hoses, fittings, or seals. Fluid leaks not only pose safety hazards for operators but can also contaminate the workpiece and surrounding environment.
4.Noise and Vibrations: Hydraulic press brakes can produce noise and vibrations during operation, which may be a concern for operators' comfort and safety. Excessive noise and vibrations can also affect the surrounding workspace and potentially impact the quality of the bent components.
5.Limited Bending Speed: Compared to other types of press brakes, such as electric press brakes, hydraulic press brakes may have slower bending speeds. This can impact productivity, especially in high-volume manufacturing environments where rapid bending cycles are required.
6.Accuracy and Repeatability: While hydraulic press brakes offer high force capabilities, they may have limitations in terms of bending accuracy and repeatability, particularly over long production runs. Variations in hydraulic pressure, wear and tear on components, and other factors can affect bend angles and dimensions.
7.Environmental Concerns: Hydraulic press brakes rely on hydraulic fluid, which can pose environmental risks if not properly managed. Spills or leaks of hydraulic fluid can contaminate soil, water sources, and ecosystems, leading to environmental damage and regulatory penalties.
8.Initial Cost and Installation: Hydraulic press brakes tend to have higher initial costs compared to mechanical or pneumatic press brakes. Additionally, installation and setup may require specialized knowledge and infrastructure, such as hydraulic power units and piping systems.
Despite these disadvantages, hydraulic press brakes remain widely used in metal fabrication due to their versatility, reliability, and ability to handle a wide range of bending applications. By addressing maintenance needs, implementing proper safety measures, and investing in energy-efficient technologies, businesses can mitigate many of the drawbacks associated with hydraulic press brakes.